Why is NASA Testing Robotic Servicing Technologies?
Since 2009, advancements have been made in the robotic technologies for a notional free-flying servicer spacecraft that could access, repair and refuel satellites in geosynchronous Earth orbit, or GEO. The team is also examining ways to service satellites in low Earth orbit, or LEO. RRM is a part of this technology development campaign.
Located about 22,000 miles above Earth, GEO is home to more than 400 satellites, many of which deliver such essential services as weather reports, cell phone communications, television broadcasts, government communications and air traffic management.
LEO is the orbital highway for many satellites providing Earth observation and weather tracking. By developing robotic capabilities to repair and refuel satellites, NASA hopes to add precious years of functional life to spacecraft and expand options for operators who face unexpected emergencies, tougher economic demands and aging fleets. NASA also hopes that RRM technologies will help boost the commercial satellite-servicing industry that is rapidly gaining momentum.
How RRM Works
RRM consists of the RRM “module”— a box covered with activity boards — and four stowed RRM Tools. The International Space Station’s twin-armed Canadian “Dextre” robot acts as a skilled spacecraft refueling and servicing technician.
During operations, controllers on the ground remotely command Dextre to reach into the RRM module and pick up RRM tools. Dextre then goes to work on RRM’s components and activity boards, demonstrating such servicing tasks such as cutting and peeling back protective thermal blankets, unscrewing caps, turning valves, transferring fluid, inspection, and intermediary steps leading up to coolent replenishment.
What’s the common thread? Servicing capabilities. These new technologies, tools and techniques could eventually give satellite owners resources to diagnose problems on orbit, fix anomalies, and keep certain spacecraft instruments performing longer in space.
The RRM Module
The RRM team at NASA’s Goddard Space Flight Center broke down robotic servicing activities into distinct, testable tasks, then built the cube-shaped RRM module to contain the components, activity boards, and tools to practice them.
The module is about the size of a washing machine and weighs approximately 550 pounds, with dimensions of 33″ by 43″ by 45.” RRM includes 0.45 gallon (1.7 liters) of ethanol to demonstrate fluid transfer in orbit. Protective thermal blankets, caps, valves, simulated fuel, and other spacecraft components allow the team to practice a wide range of satellite-servicing tasks.
RRM Tools
RRM demonstrates five unique tools that were designed and manufactured by NASA’s Satellite Servicing Projects Division, the same team that developed astronaut tools for the Hubble Servicing Missions. These tools and their accompanying adapters cut and manipulate wires, unscrew caps, open and close valves, transfer fluid, practice steps leading up to coolant replenishment, and provide inspection capabilities.
Demonstrations
RRM demonstrations cover many diverse satellite-servicing activities. Click on the links for detailed descriptions of RRM tasks on orbit.
RRM Phase 1
RRM is on the International Space Station. What’s next?
Now that the RRM is securely mounted onto the International Space Station, the operations team is demonstrating robotic servicing and refueling tasks using the RRM module and the Dextre robot.
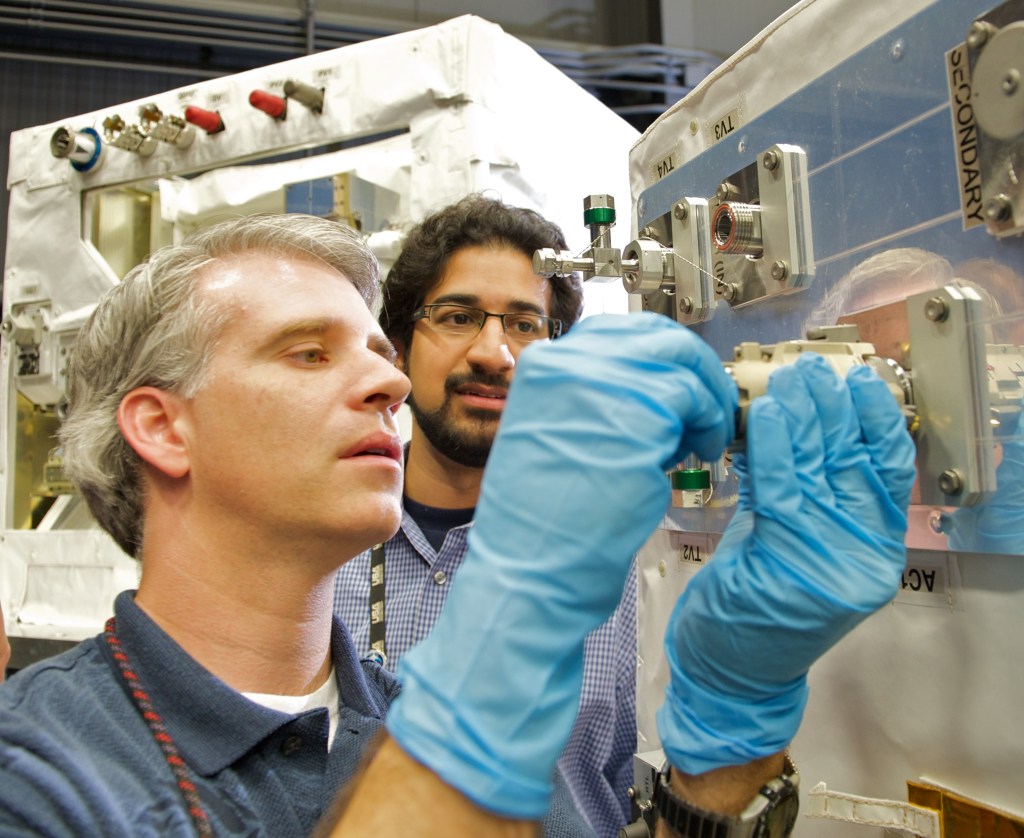
Phase 2
The Robotic Refueling Mission Tackles New Frontiers
Is there life for a NASA experiment after it’s proved its namesake task? If you’re built to be modular and upgradable, as NASA’s Robotic Refueling Mission is, then the answer is yes!
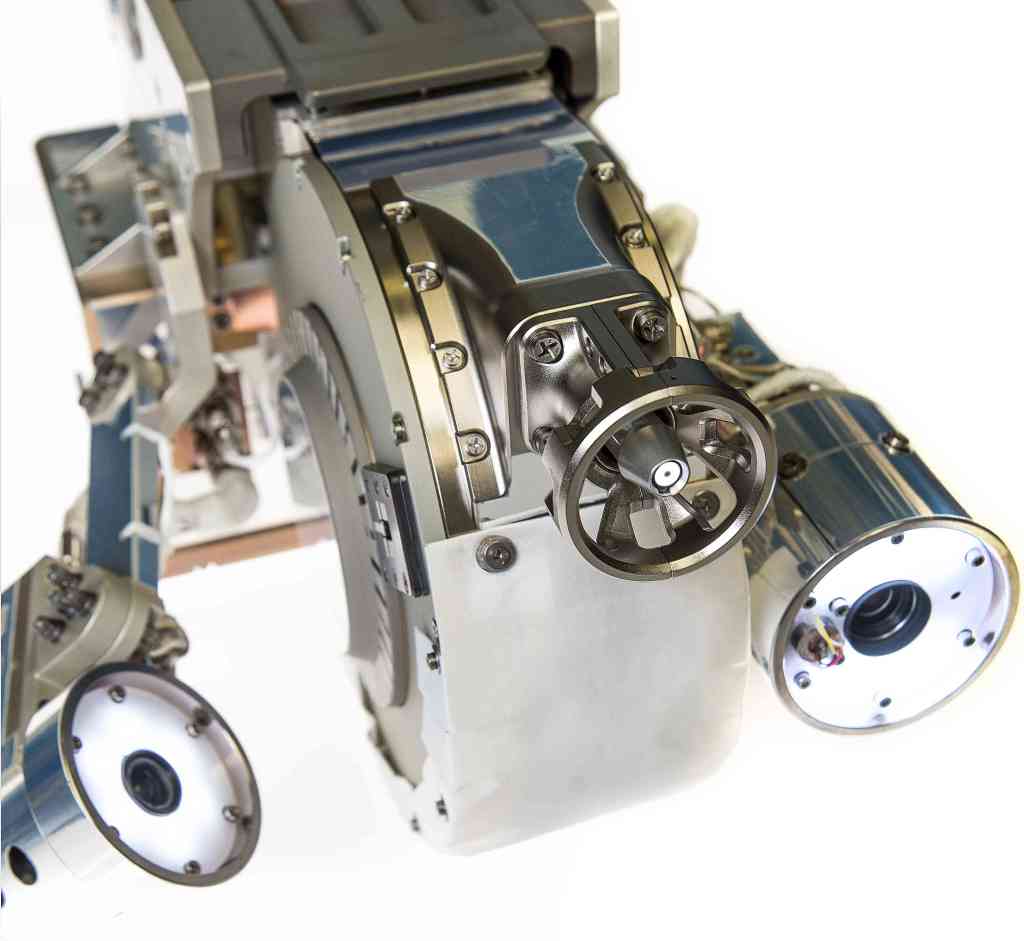
What Makes RRM Unique?
- First demo to test the robotic refueling of satellite interfaces not designed to be accessed or serviced. The Orbital Refueling System tested by astronaut Kathryn D. Sullivan during the 1984 STS-41-G shuttle flight and DARPA’s robotic Orbital Express Mission were very successful, but had different objectives.
- First use of the International Space Station’s Dextre robot for technology research and development.
- Operations are completely controlled from the ground.
- RRM tools execute activities at the end of more than 70 feet (21.34 meters) of combined Dextre and Canadarm2 robotics.
Launch and Mounting on ISS
The shuttle Atlantis carried RRM to the International Space Station on July 8, 2011 during STS-135, the last shuttle mission. Spacewalking astronauts Mike Fossum and Ron Garan then transferred RRM onto a temporary platform on Dextre on July 12, 2011. RRM is the last payload an astronaut ever removed from a shuttle cargo bay.
On September 2, 2011, Canadarm2 and the Dextre robot transferred RRM to its permanent location on space station, the ExPRESS (Expedite the Processing of Experiments to the Space Station) Logistics Carrier-4.
RRM-Phase 2 hardware was split into two deliveries. The first occurred in August 2013, and the second in August 2014.
Mission Operations
RRM operations are entirely remote controlled by flight controllers at NASA’s Goddard Space Flight Center in Greenbelt, Md., Johnson Space Center in Houston, Marshall Space Flight Center in Huntsville, Ala., and the Canadian Space Agency’s control center in St. Hubert, Quebec.
Development and Testing
Each RRM task requires a high level of robotic precision and demonstrates state-of-the-art technology, tools, and techniques. RRM maneuvers, tools and algorithms were tested and verified in the Goddard Servicing Technology Center in Greenbelt, Maryland.
Partners
RRM is a joint effort between NASA and the Canadian Space Agency (CSA).