Spacecraft use consumables like propellant and coolant to perform key functions such as maneuvering and maintaining critical equipment. Consumables, by their very nature, eventually run out. The technology to replenish these crucial supplies in space does not currently exist. NASA’s Robotic Refueling Mission 3 (RRM3) will help change that paradigm, advancing satellite servicing capabilities and enabling long duration, deep space exploration.
Robotic Refueling : Phase 3
RRM3 builds on the first two phases of International Space Station technology demonstrations that tested tools, technologies, and techniques to refuel and repair satellites in orbit.
RRM3 will extend these demonstrations to include technologies needed to store and transfer super-cold cryogenic fluids. The mission launched to space station in December 2018. It will have a projected two-year life on station, though NASA intends to accomplish RRM3’s objectives within the first year. On April 8, RRM3 experienced an issue that necessitated the venting of the cryogenic fluid contained within the module, but the mission is still projected to carry out the tool operations associated with transferring cryogenic fuel in space, demonstrating the cutting edge technologies needed to make it possible.
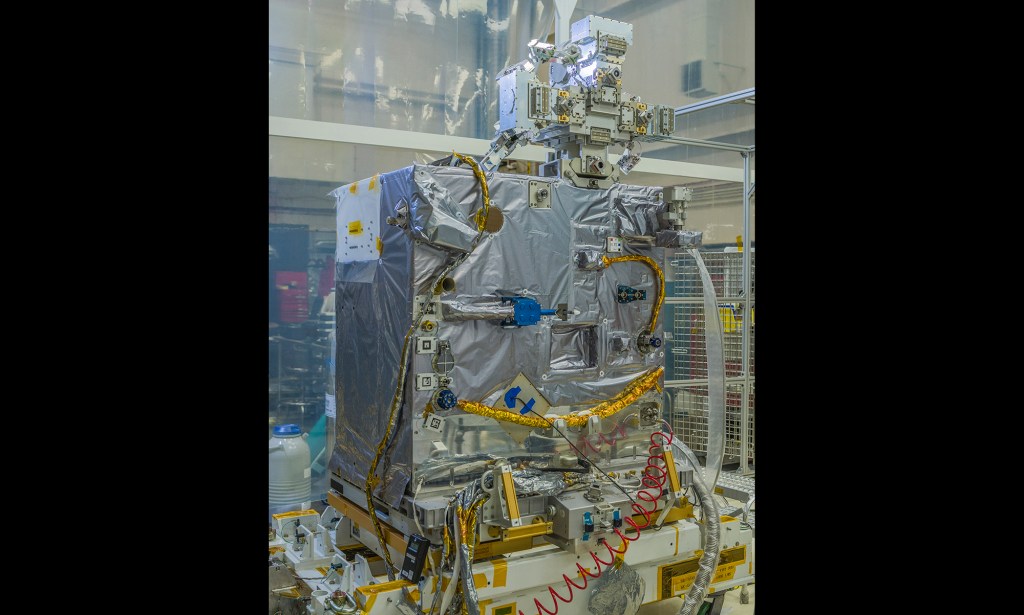
What Are Cryogenic Fluids?
Cryogenic fluid is an important consumable for spaceflight.
As a propellant, cryogenic fluids such as liquid methane and liquid hydrogen are useful for exploration missions because they produce enough thrust, or what is essentially acceleration, to launch a rocket from Earth or another planet. Without a powerful enough propellant, a planetary body’s gravitational pull would prevent a rocket from successfully escaping the body’s orbit.
Liquid oxygen, another cryogenic fluid, is also used to maintain life support systems for astronauts, since it is a more efficient way to transport and store oxygen than in its gaseous form.
As a coolant, it keeps spacecraft operational, and the ability to replenish it could extend their lifespan by years.
RRM3 is testing the tools and technologies needed to store, transfer and replenish cryogenic fluid so the technology is ‘ready for primetime’ when needed.
Enabling Human Exploration throughout the Solar System
The ability to resupply propellant and coolant enables longer journeys than a single tank of propellant would allow. The capabilities NASA will develop through RRM3 can be applied to future human exploration missions.
RRM3 Primary Objectives
1. Demonstrate Techniques necessary to perform cryogenic liquid methane transfer in micro-gravity
2. Maintain cryogen fluid mass long term (<3 months) via zero boil-off
What’s in and on the Module?
- Fluid transfer system (including tanks and lines)
- Cryogenic fluid (liquid methane)
- Cryogen interface (cooperative and non-cooperative)
- Compact Thermal Imager (CTI)
- Innovative vision systems
- Cryocoolers
- Tools and adapters
- Multi-Function Tool 2 (MFT2)
MFT2 Adapters:
Cryogen Coupler Adapter (CCA) - Cryogen Servicing Tool (CST)
- Visual Inspection Poseable Invertebrate Robot 2 (VIPIR2)
- Multi-Function Tool 2 (MFT2)
Compact Thermal Imager
The Compact Thermal Imager (CTI) is an advanced, highly compact thermal camera that has been mounted in a corner of the RRM3 payload and from that position will image and videotape Earth’s surface below. RRM3’s hitchhiker companion will image and measure fires, ice sheets, glaciers, and snow surface temperatures. CTI will also measure the transfer of water from soil and plants into the atmosphere — important measurements for understanding plant growth. Many of the conditions that Earth scientists study, including these, are easily detected in the infrared or thermal wavelength bands.
CTI’s enabling technology is a relatively new photodetector technology known as Strained-Layer Superlattice, or SLS. In addition to being very small, measuring nearly 16 inches long and six inches tall, SLS consumes little power, operates at liquid-nitrogen temperatures, is easily fabricated in a high-technology environment, and is inexpensive. The demonstration’s goal is to raise SLS’s technology-readiness level to nine — or TRL-9 — meaning that it has flown in space and has demonstrated that it operates well under the extreme environmental conditions found in space.
RRM3 Secondary Objectives
1. Demonstrate and validate the Compact Thermal Imager – An instrument that utilizes available room on RRM3 to observe Earth to detect smoke and fires, as well as measure crop transevaporation.
2. Complete Machine Vision Tasks – In-space assessment of fiducials (decals) with unique patterns that enhance machine vision algorithms and aid in autonomous rendezvous and tool positioning.
Tool Descriptions
A suite of three primary tools, designed to be used by space station’s Dextre arm, will be employed to conduct mission objectives. These second generation tools were designed based on operational lessons learned from RRM Phase 1 and 2, and and unique RRM3 mission requirements. The three tools are:
Visual Inspection Poseable Invertebrate Robot 2 (VIPIR2)
A robotic inspection camera used to visually verify entry and positioning of the Cryogen (flexible line) Transfer Hose (CTH) into the receiver tank.
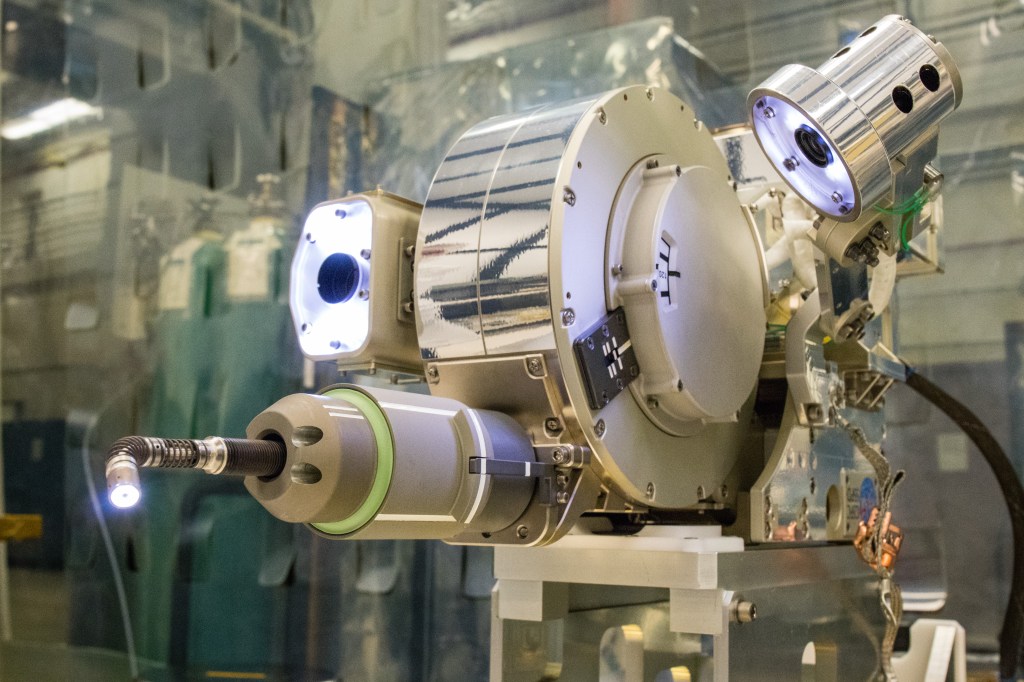
Cryogenic Servicing Tool (CST)
A robotic tool with adjustable rollers used to grab a flexible cryogen transfer hose and install it into a fuel port.
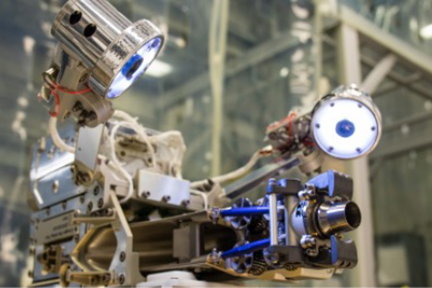
Multi-Function Tool 2 (MFT2)
A dual rotary drive tool used to connect custom hose adapters to robot-friendly fill ports.
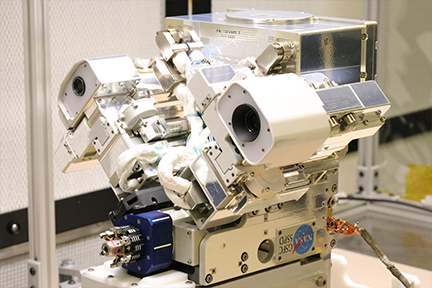
Cryogen Storage and Replenishment Demonstration
RRM3 will demonstrate the tool operations needed to robotically transfer cryogenic fluid, which is critical for propulsion and life support systems in space. The previous phase of the Robotic Refueling Mission (RRM2) demonstrated many preparation tasks leading up to cryogen replenishment such as removing caps/valves, and installing coolant line adapters. RRM3 robotic operations will focus on the final step of connecting, sealing and managing the hoses needed to enable cryogenic fuel transfer on-orbit. Since launch in December 2018, RRM3 demonstrated the first ever long-term storage of cryogenic fluid with zero boil off, having successfully stored cryogenic fluid for four months on station prior to the April venting operation.
Contained within the RRM3 module is a source tank, representing a supply on a servicing spacecraft and a receiver tank, representing a spacecraft with a depleted cryogenic tank.
During RRM3 mission operations, the space station’s Dextre robotic arm will carry out tasks using a suite of three primary tools, and without using a cryogenic fluid. The task sequence begins with the multi-function tool 2, which operates smaller specialized tools to prepare for the transfer of liquid methane from the source tank to the fluid transfer. Next, the cryogen servicing tool uses a hose to connect the source tank to the receiver tank. To monitor the process, the Visual Inspection Poseable Invertebrate Robot 2 (VIPIR2) utilizes a state-of-the-art robotic camera to make sure tools are properly positioned.
Storing cryogens in space can be difficult because their extremely low boiling points cause them to boil off over time if the temperature cannot be maintained. Conventional cryogen storage tanks on the ground use passive cooling systems and intentionally vent their contents to the atmosphere to limit tank pressure during warmup. This greatly reduces the life of the stored cryogen.
A critical part of RRM3 is the demonstration of zero boil off storage of its 42 liter liquid methane supply through the use of active cooling. By using cryocoolers and advanced multilayer insulation to balance temperatures, RRM3 successfully stored liquid methane for four months with zero boil off, demonstrating a system which will dramatically lower fluid loss and eliminate the need for oversized tanks and extra propellant.
Featured News

Astronauts Assemble Tools to Test Space Tech

NASA to Launch New Refueling Mission, Helping Spacecraft Live Longer and Journey…
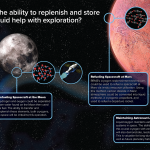
Robotic Refueling Mission 3 Completes Crucial Series of Tests
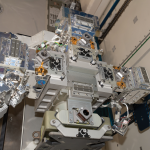
Space Station Enables Tests of Technology to Capture, Refuel, Repair Orbiting Satellites