NESC Technical Bulletins
NESC Technical Bulletins can result from NESC independent testing, analysis, and assessments. A technical bulletin captures critical engineering information or best practices in a one-page, quick-read format.
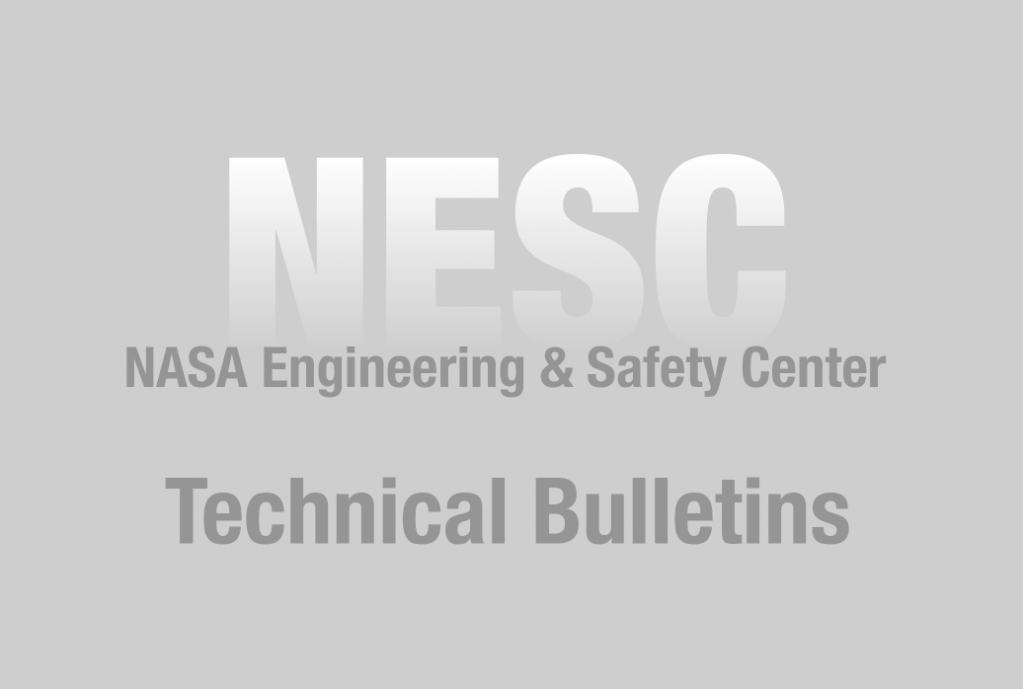
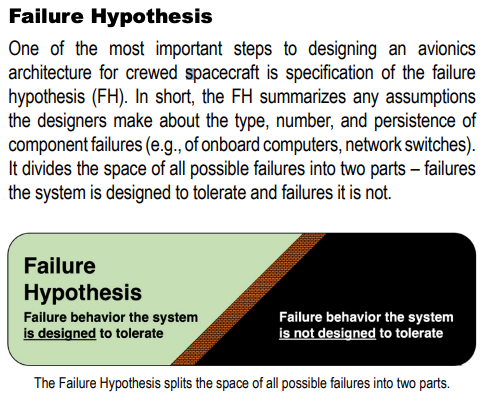
24-05: Key Considerations When Developing Avionics for Safety-Critical Systems
This bulletin describes how to show the design of an avionic system meets safety requirements for crewed missions.

24-04: 6DOF Check Cases
This bulletin focuses on Earth-based check-cases for well specified, rigid-body, six-degree-of-freedom (6DOF) aero/spacecraft models to promote consistent and accurate flight simulations across multiple Agency tools and facilities.
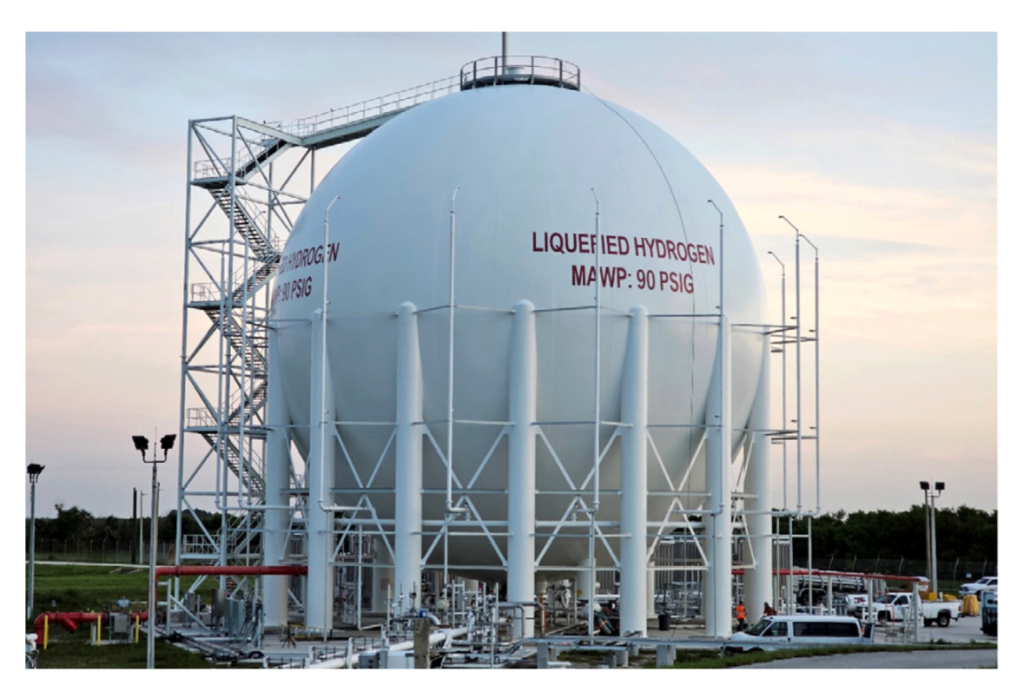
24-03: Helium Conservation by Diffusion Limited Purging of Liquid Hydrogen Tanks
This bulletin highlights an analytical model that predicts diffusion between two gases during piston purging of liquid hydrogen (LH2) tanks.
Previous Technical Bulletins
- 24-02: Considerations for Using Autonomous Flight Termination Software in Crewed Launch Vehicles
Autonomous flight termination systems (AFTS) are being progressively employed onboard launch vehicles to replace ground personnel and infrastructure needed to terminate flight or destruct the vehicle should an anomaly occur. This automation uses on-board real-time data and encoded logic to determine if the flight should be self-terminated. - 24-01: Material Compatibility of Common Aerospace Metals in MMH/MON-3
The NESC evaluated material compatibility of some common aerospace metals in monomethylhydrazine (MMH) and nitrogen tetroxide (MON-3). Previous work had identified a lack of quantitative compatibility data for nickel alloy 718, 300 series stainless steel, and titanium Ti-6Al-4V in MMH and MON-3 to support the use of zero-failure-tolerant, thin-walled pressure barriers in these propellants. - 23-07: Best Practices for Fabrication of Microelectronic Devices
Material degradation during the fabrication of microelectronic devices has plagued the space industry for many years owing to the layering of many dissimilar metals to create these devices. Often, commonly used materials and systems are overlooked as potential sources of material degradation. This technical bulletin highlights extensive research to isolate probable causes of this degradation. - 23-06: Considerations for Software Fault Prevention Tolerance
Mission or safety-critical spaceflight systems should be developed to both reduce the likelihood of software faults pre-flight and to detect/mitigate the effects of software errors should they occur in-flight. New data is available that categorizes software errors from significant historic spaceflight software incidents with implications and considerations to better develop and design software to both minimize and tolerate these most likely software failures. - 23-05: Flight Mechanics Analysis Tools Interoperability and Component Sharing
The NESC recently explored ways that increase interoperability of three mission analysis tools: Copernicus, General Mission Analysis Tool (GMAT), and Mission-Analysis Operations Navigation Toolkit Environment (Monte). These tools are used to generate a variety of products throughout all phases of a mission including: maneuver planning, trajectory optimization and design, orbit determination, performance and error analysis, trade studies and sizing. - 23-04: Fast Coupled Loads Analysis Method: Norton-Thevenin Receptance Coupling
A new method called Norton-Thevenin Receptance Coupling (NTRC) has been developed to perform coupled loads analysis (CLA). NTRC provides a tool that payload developers can use to obtain launch loads at a fraction of the cost of a CLA any time it is required in the payload design cycle. NTRC combines the frequency domain component coupling method of Receptance Coupling with the Norton and Thevenin theory used in force limiting to derive an alternate method for performing CLA. - 23-03: New Transient Finite Energy Shock Prediction Methodology
Shock prediction is one of the top loads and dynamics discipline technical challenges identified within NASA and industry programs and projects. The physics-based Transient Finite Energy (TFE) shock prediction methodology has been developed and compared favorably against test results. TFE can provide another approach to develop predictions of shock response spectra (SRS) for use in the analysis of structural margins. - 23-02: Safety Considerations when Repurposing Commercially Available Flight Termination Systems from Uncrewed to Crewed Launch Vehicles
Both uncrewed and crewed launch vehicles (LV) require Flight Termination Systems (FTS) for Range Safety to protect the public and ground assets in the event of a LV failure. Flight crew safety in this context is an added consideration for human spaceflight. The FTS is an electroexplosive system that activates destruct charges to rupture propellant tanks and shut down engines during flight termination. Commercially available FTS units have been developed for uncrewed applications and are now being repurposed to crewed applications. A consequence of using these systems is that they are designed for public and ground crew safety, though inadequate for flight crew safety. Missing are Human Space Flight (HSF) design controls for inadvertent activation during crewed ascent and protection for crew emergency abort.
- 23-01: Including Key Design Features in Safety-Critical Pyrotechnic Firing Circuits
Pyrotechnic systems often fall into a unique category in that inadvertent activation of these systems resulting from a fault and/or lack of safe margins can lead directly to loss of crew. For example, untimely activation of pyrotechnics used for a flight termination system could override an abort capability. Over the years, NASA and the military have learned lessons about safe pyrotechnic circuit design and test, many of which are codified. However, with NASA’s recent efforts to move toward a development model that leans more heavily on Commercial Partners these requirements have not always been directly levied on projects, and in some cases have been misinterpreted. This bulletin describes key safety features of pyrotechnic firing circuit design and provides rationale for inclusion of each feature. - 22-08: Contaminant Reduction in High Purity Hydrazine (HPH)
Hydrazine and its derivatives are used ubiquitously in liquid propulsion systems. In smaller thruster systems, contaminant build up has historically caused flow decay and consequently performance losses. Many of these contaminants are not controlled by the current revision of MIL-PRF-26536 [1], the HPH procurement specification, yet have been observed to be present in HPH at variable concentration and, often exceed potentially problematic levels for small thrusters. This technical bulletin outlines recent work aimed at identifying appropriate separation processes to remove specific target elemental and carbonaceous contamination in HPH. - 22-07: Helium Solubility in MMH and NTO
A test program to characterize the solution of helium in nitrogen tetroxide/mixed oxides of nitrogen (NTO)/(MON) and monomethylhydrazine (MMH) at anticipated flight-representative pressures/temperatures was completed. Updated relations for helium solubility in MMH and NTO were generated and documented. - 22-06: Treatment of Slosh Stability Margin Reductions for Human-Rated Launch Vehicles
Slosh dynamics pose a stability concern for human-rated launch vehicles during ascent. Historical perspectives on the treatment of slosh dynamics, newly developed rules of thumb, the utility of flight data, and methods for analyzing and dispositioning slosh instability risks should be considered when linear stability margins are lower than typically accepted for human-rated systems. - 22-05: Launch Vehicle Flight Control Stability Margin Reduction Considerations
Launch vehicle ascent stability analyses typically rely on a combination of frequency and time domain analyses. Frequency domain analysis uses a sequence of high-fidelity linear models with constant parameters spanning the ascent trajectory. Complementary time domain analysis is performed using high-fidelity, nonlinear 6-DOF simulations. Analyses are typically dispersed to verify robustness to parameter variations by showing the vehicle meets frequency domain stability margin requirements and time domain performance metrics. This Technical Bulletin outlines standard stability margin best practices and provides recommendations for treatment of deviations from industry-standard launch vehicle stability margins due to vehicle flexibility, slosh dynamics, aerodynamics, other offending dynamics, or coupling thereof. - 22-04: Uncertainty Quantification of Reduced Order Structural Dynamic Models
Uncertainty quantification (UQ) provides statistical bounds on prediction accuracy based on finite element model (FEM) uncertainty. An alternate method for UQ, called the Hybrid Parametric Variation (HPV) combines a parametric variation of the Hurty/Craig-Bampton (HCB) fixed-interface (FI) modal frequencies with a nonparametric variation (NPV) method. This provides a UQ method that can be traced to test data, which can be updated as additional data and improved correlated models become available. - 22-03: Treatment of Transient Pressure Events in Space Flight Pressurized Systems
Analytical and experimental evidence shows that fast-moving dynamic pressure fluctuations caused by valve actuation, fluid-system priming, fluid discharge, vibration, and flow disturbances can elicit adverse structural response and must be considered in the space flight pressure system design and verification process. - 22-02: Revisiting Filtration Standards and Definitions for Spaceflight Propulsion and Pressurant Systems
The NESC performed an assessment of existing filtration standards and guidance documents for propellant and pressurant systems. The assessment included a vendor survey to better understand concerns about filtration systems, defined a common set of filtration and contamination-related terms, and developed guidelines for system filtration design and implementation. - 22-01: Detecting Flow-Induced Vibration in Bellows
The NESC performed testing to determine if high-speed video techniques can be used to predict the onset of flow-induced vibrations (FIV) in bellows. A comprehensive test matrix was established to determine if Motion Magnification (MM) and Digital Image Correlation (DIC) can be used to determine the onset of FIV in straight and gimbaled bellows. Several of the tests were intended to determine if MM and DIC can establish the resonant frequencies of the bellows with no a priori knowledge. The results of the MM and DIC were compared with data from strain gages and microphones. Although the testing was limited to one single-ply unshielded bellows, this effort provided the proof-of-concept that MM and DIC are feasible methods for determining the onset of FIV in bellows. - 21-05: Industry Recommendations from Arecibo Observatory Zinc Spelter Socket Joint Failure Analysis
A structural analysis and forensic investigation concluded that the Arecibo Observatory M4N socket joint failure in August 2020 was primarily due to cumulative damage caused by initially low structural design margins and a high percentage of sustained load, resulting in zinc creep deformation, progressive internal socket wire damage, and eventual loss of joint capacity. Open spelter sockets of this type are used throughout industry in stay cables. Recommendations are proposed to prevent failures of similar socket joints, including verification of positive stress margins in socket joint wires for all failure modes, periodic visual inspections with pass/fail criteria for zinc extrusion that are tied to structural qualification, and revisiting codes/industry standards to capture lessons learned. - 21-04: Evaluating Appropriateness of LEFM Tools for COPV and Metal Pressure Vessel Damage Tolerance Life Verification
Human spaceflight composite overwrapped pressure vessels (COPVs) and metal pressure vessels can use linear elastic fracture mechanics (LEFM) analysis to demonstrate damage tolerance life in some cases per ANSI/AIAA-S-081 for COPVs and ANSI/AIAA-S-080 for metal pressure vessels. LEFM analysis assumptions require that the crack tip plastic zone is small relative to the crack size and is completely surrounded by elastically responding material. Test and analysis have shown that LEFM tools (e.g., NASGRO*) can provide unconservative crack growth predictions for cracks in COPV liners that violate LEFM assumptions. COPV and metal pressure vessel designers should evaluate and address the violation of LEFM plasticity assumptions before using LEFM analysis tools for damage tolerance life verification. - 21-03: Best Practices for the Elemental Profiling of High-Purity Hydrazine
Trace contaminants in high-purity hydrazine (HPH) propellant impact a wide variety of commercial, Department of Defense (DoD), and NASA missions. Depending on thruster design, elemental contaminants must be kept at extremely low levels and are verified as such by routine analysis. A number of these contaminants have recently undergone an assessment to shed light on their quantities present following changes in the HPH supply chain. A round robin analysis utilizing four separate laboratories resulted in unacceptably high variability in the quantification of these contaminants. The principal objective of this technical bulletin is to signal the availability of a new analysis methodology which yields accurate and repeatable quantification by providing best practices for both quantitation methodology and strategies for avoiding sample contamination during analysis. - 21-02: Genesis Flight Mechanics Simulation
The NASA Engineering and Safety Center (NESC) consolidated and modernized a suite of legacy flight mechanics simulations, including the Flight Analysis and Simulation Tool (FAST), resulting in Genesis, a generic, multi-vehicle, variable-degree-of-freedom flight mechanics simulation for ascent, aerocapture, entry, descent, and landing (A2EDL) trajectory design. - 21-01: Experimental and Computational Study of Cavitation in Hydrogen Peroxide
Cavitation in liquid propulsion systems can lead to performance degradation and hardware failures. The NESC sponsored an investigation to measure and model cavitation in pressurized hydrogen peroxide flow. The experimentally measured and computationally predicted cavitation lengths were compared as a function of cavitation number. The measured and predicted data exhibited close agreement over the range of pressures and temperatures studied, and no calibration of the cavitation model coefficients was needed. - 20-08: Assessment of Ketazine Derived High Purity Hydrazine for Spacecraft Propellant Systems
Hydrazine and its derivatives have dominated the class of hypergolic liquid propellants for bipropellant propulsion systems, and is used as a monopropellant in auxiliary power units and thrusters. With continued use of hydrazine in current and future spacecraft and payloads, it is necessary to understand the historical and current states of synthesis for the commodity and possible purity implications that may arise from changes in production processes for the United States stock. This technical bulletin describes these issues in detail. - 20-07: Evaluating and Mitigating Liner Strain Spikes in COPVs
Based on NESC analysis of cracks and leaks that occurred in flight Composite Overwrapped Pressure Vessels (COPVs), a failure mode due to liner strain spikes was observed through measurement and predicted by analysis. The failure mode may be present in COPVs used on NASA programs and by the aerospace industry. This technical bulletin was developed to alert manufacturers and the user community to this failure mode and contains approaches to evaluate COPVs for susceptibility to this failure mode. - 20-06: Material Compatibility Assessment of Spacecraft Oxidizer Systems
After recognition that an ignition vulnerability existed between certain materials and oxidizers used in spacecraft propulsion, the NESC researched ignition mechanisms to better understand the potential risk to NASA and industry. An assessment focused on the flammability/ignition behavior of titanium and oxidizers such as nitrogen tetroxide but revealed that other metals may also be susceptible. While the oxidizer compatibility assessment process is on-going, this technical bulletin discusses the immediate steps NASA is taking to mitigate this risk until these ignition mechanisms are fully understood and thresholds and operating envelopes can be determined. - 20-05: Determination of Autogenous Ignition Temperature for Isopropyl Alcohol and Ethanol
As part of a recent liquid rocket engine shutdown investigation, a commercial partner requested that NASA provide the autogenous ignition (or autoignition) temperature (AIT) of isopropyl alcohol (IPA). NASA provided the available data, but the data were somewhat scattered, likely due to test configuration and test technique differences. NASA Engineering and Safety Center (NESC) support was requested to experimentally determine the AIT of IPA and ethanol, both of which are extensively applied to propulsion systems. This report contains the outcome of the NESC assessment. - 20-04: Alternative O-Rings for Hypergolic Propellant Systems
The commercial company Parker-Hannifin has stopped production of O-rings using the material E0515. NASA programs such as the Multi-Purpose Crew Vehicle, the Commercial Crew Program, Mars 2020, the Europa Clipper, and the International Space Station have used O-rings made of this material to seal high pressure lines that contain liquid engine propellants and gases. As NASA reserves of the E0515 O-rings will soon be depleted, Dr. Daniel Dorney, NASA Technical Fellow for Propulsion, led an NESC assessment team that tested potential replacement candidates. This Technical Bulletin provides the results of that testing as well as recommendations for replacement O-rings that are compatible with hypergolic propellant applications. - 20-03: Navigation Filter Design Best Practices
Onboard navigation and attitude estimation systems are at the heart of almost all of NASA’s missions, either on launch vehicles, robotic science spacecraft, or on crewed human exploration vehicles. Best practices for attitude estimation systems/filters are scattered throughout open literature, however, even within NASA there has been no previous attempt to codify this knowledge into a readily available design handbook. Without such a document, it is possible for isolated practitioners to lack understanding and appreciation of many tried and true approaches to successful and robust filter design and the implied cost/benefit trades associated with them. To aid designers of current and future missions, a handbook of navigation filter best practices has been developed and is introduced here. The development of this document is also an outgrowth of a recommendation made in an NESC summary of lessons learned from the DARPA Orbital Express mission to utilize best practices for rendezvous navigation filter design. With this handbook, future designers have a reference that establishes NASA’s best practices. - 20-02: Effective and Environmentally Compliant Cleaner – Solstice Performance Fluid
Historically, NASA has used Hydrochlorofluorocarbon-225 (HCFC-225 or AK-225) solvent to clean and verify propulsion systems that use liquid and gaseous oxygen, but when the EPA implemented restrictions regarding its use, NASA began efforts to find an acceptable replacement. This Technical Bulletin highlights the cleaning capabilities and compatibility of alternative fluids, Honeywell’s Solstice® Performance Fluid (PF), PF-high purity (HP), and PF-HP spray, that may be used in a variety of cleaning applications. The bulletin is provided by Mr. Steven Gentz, NESC Chief Engineer at Marshall Space Flight Center, who through NESC assessments, supported the Agency’s initiative to identify and test alternatives to AK-225. - 20-01: Latching Safety Critical Signals in Pyrotechnic Circuits
When a shock test of safety-critical pyrotechnic circuits resulted in an inadvertent firing, it revealed a sensitivity to electrical noise in the latching circuits, which store the state-of-control signals in pyro control circuitry. This technical bulletin, developed by Dr. Robert Hodson, NASA Technical Fellow for Avionics, recommends enhancements to recent designs of these circuits that would reduce this sensitivity and the susceptibility of the circuit to unintentional firing. These best practices offer simple improvements such as qualifying data signals and adding filters to the design of these critical circuits that are vital to the safe operation of spacecraft. - 19-02: 90/95 POD Radiography Concern for COPVs and Metal Tank Welds
Inspecting all-metal tanks and composite overwrapped pressure vessels using radiography presents significant challenges, particularly when inspecting for cracks in the tank welds. Recent evaluations performed by Nondestructive Evaluation experts at Johnson Space Center found that X-rays, which must penetrate two-wall thicknesses of a welded tank, cannot guarantee detection of a crack with the same level of reliability demonstrated in the typical single-wall test. This lack of visibility into the weld cracks can mean fracture risk is not fully understood. This Technical Bulletin aims to highlight that risk and suggests methods to better understand it until further research can determine more effective techniques for evaluating damage tolerance on these tanks. - 19-01: Mitigating Risks of Single-Event Effects in Space Applications
Since most Electrical, Electronic, and Electromechanical (EEE) parts are intended for terrestrial applications, they are susceptible to a range of radiation threats in the space environment if the resulting effects are not properly characterized and mitigated. Even specially designed radiation-hardened parts may not be tolerant to all types of radiation effects. Radiation hardness is a multi-dimensional property of any part that describes intrinsic abilities to tolerate various radiation environments [1,2]. Effects to be concerned with include total ionizing dose, total non-ionizing dose, and single-event effects (SEE) – all of which depend on the mission, environment, application, and lifetime. Radiation effects concerns may be the same whether a EEE part is Commercial-Off- The-Shelf (COTS), MIL-SPEC, or some other variant, all of which are susceptible to the same radiation threats [3]. SEE consequences range from recoverable faults to catastrophic failure. Like other random faults, SEE can be mitigated with informed circuit design practices at the device, card, and/or system level. - 17-01: Development of NASA Standards for Enabling Certification of Additively Manufactured Parts
As NASA approaches certification of manned spaceflight components made from additively manufactured (AM) parts, Mr. Richard Russell, NASA’s Technical Fellow for Materials, initiated this NESC technical bulletin to underscore the need for an Agency standard that outlines the requirements for AM parts design, manufacture, and certification. The AM field is experiencing rapid growth. NASA, as well as its commercial crew partners, are using these parts in several programs such as the Orion Multi-Purpose Crew Vehicle and the Space Launch System (SLS) – programs that will by flying before industry and international standards agencies can complete the AM standards they are currently developing. Marshall Space Flight Center, took the initiative to write a Center-level standard – MSFC-STD-3716 “Standard for Additively Manufactured Spaceflight Hardware by Laser Powder Bed Fusion in Metals,” 2017, and an accompanying specification – MSFC-SPEC-3717, “Specification for Control and Qualification of Laser Powder Bed Fusion Metallurgical Processes,” 2017, encompassing the laser power bed fusion (L-PBF) process. - No. 16-02: Damage Tolerance Life Issues in COPVs with Thin Liners
While Composite Overwrapped Pressure Vessels (COPVs) with thin liners offer weight savings, they present fracture control challenges. Current methods for estimating damage tolerance life may be limited for thin-lined vessels. This Technical Bulletin explains the challenges present when COPVs with thin liners are used, why additional qualification tests may be necessary, and what steps the NESC is taking to develop a path forward for their future use. - 16-01: Buckling Knockdown Factors for Composite Cylinders
It took decades to figure out the complex buckling behavior of metallic cylindrical launch vehicle structures and the knockdown factors (KDFs) that account for the unknown variability in the geometry, loading, and material imperfections. The KDFs, established by Apollo-Era engineers, are still in use today by NASA and by industry world-wide, as captured in NASA SP-8007 Buckling of Thin-Walled Circular Cylinders from 1968. Developed with conservatisms warranted by the technology of the time, these KDFs are likely adding unnecessary weight to today’s modern aerospace structures. That was the catalyst behind Dr. Mark Hilburger’s NESC-sponsored proposal to develop and implement updated shell buckling KDFs, now in use by the Space Launch System Program.
Designers of composite cylinders, however, still turn to SP-8007, often using KDF=0.65 in their composite designs, a number for which the technical justification is unclear. As a result, Dr. Marc Schultz, working with Dr. Hilburger, is investigating KDFs for modern composite cylinders. Their work has led to the development of this Technical Bulletin, which emphasizes that composite cylinders are outside the scope of SP-8007 and why caution must be taken when using the universal KDF in composite designs. - 15-03: Best Practices for Use of Sine Vibration Testing
Sine vibration testing replicates the low-frequency launch environment. This test method is used mainly on flight articles to determine if they can survive the harsh launch environment. Testing involves accepting calculated risk, but failure to follow best practices for sine vibration testing has resulted in avoidable damage to flight hardware. Dr. Curtis Larsen, NASA Technical Fellow for Loads and Dynamics, Mr. Daniel Kaufman, NESC Discipline Deputy for Loads and Dynamics, and their Technical Discipline Team identified top risks and documented best practices to help mitigate those risks and take full advantage of what sine vibration testing has to offer. - 15-02: Best Practices for Use of Sine Burst Testing
For more than two decades, sine burst testing has provided a method of strength testing for aerospace hardware that not only minimizes potential for damage to the test item, but can be performed on a shaker table along with other tests to maximize efficiency. But with all testing comes potential risk. In this Technical Bulletin, Mr. Daniel Kaufman, NESC Discipline Deputy for Loads and Dynamics, identifies top risks such as unintended over-test or erroneous calculations, and provides best practices to help mitigate those risks and take full advantage of what sine burst testing provides. - 15-01: Preventing Incorrect Installation of Polarized Capacitors
Concerns that the incorrect installation of polarized capacitors has continued, despite lessons learned from past installation issues, Dr. Christopher Iannello, NASA Technical Fellow for Electrical Power, and Andrew Ging, an industry partner on the NESC Electrical Power Technical Discipline Team, initiated this technical bulletin to shed new light on a timeworn problem. Using an NESC assessment of an anomaly on board the International Space Station as an example, Dr. Iannello and Mr. Ging highlight the ways in which reverse installation can occur, and provide a short list of best practices — from procedure review to the correct use of symbols on schematics — to help eliminate any future issues with reverse installation. - 14-03: COPV Mechanical Model Validation
When issues surrounding the understanding of composite overwrapped pressure vessel (COPV) mechanics surfaced in two previous NESC assessments, Dr. Lorie Grimes-Ledesma of the Composite Pressure Vessel Working Group discovered that even with the availability of vendor-supplied finite element tools, there was a lack of accuracy in understanding COPV liner and composite response. And that lack of accuracy was propagating in subsequent fracture and stress rupture analysis. A look back to fundamentals in understanding autofrettage and a subsequent correlation study between finite element analysis and measured response on COPVs led to this technical bulletin’s best practices for COPV model validation. - 14-02: Aerodynamic Reaction Control System (RCS) Orientation and Jet Interaction (JI) Model Validation
A historical perspective on jet interaction prediction issues combined with NESC analysis gleaned from a Mars Science Laboratory assessment led to this technical bulletin’s guidance on the placement and orientation of reaction control system (RCS) jet thrusters on hypersonic entry vehicles. Dr. David Schuster, NASA Technical Fellow for Aerosciences, concluded that taking the proper precautions in the development of an RCS system, paired with computational fluid dynamics calculations and wind tunnel testing, yields a more accurate view of controllability and the flow characteristics behind those vehicles. - 14-01: Designing for Flight Through Periods of Instability
An NESC assessment of the Ares 1 flight control sensitivity to slosh dynamics in the Orion service module raised questions for Neil Dennehy, NASA Technical Fellow for Guidance, Navigation, and Control (GNC), about stability margins, the degree of conservatism flight control system (FCS) engineers put into designs, the linear and nonlinear analysis tools they use, and how it all related to safely flying a vehicle through brief periods of control instability. As stability is a mantra for GNC experts, Dennehy began capturing what the GNC community was learning about stability margins with respect to control instability, resulting in this technical bulletin that suggests FCS designers not limit themselves, and look beyond the frequency domain approach when designing flight control systems. - 12-02: Structural Analyses and Margins of Safety
There is an increasing reliance on modeling and simulation to verify, quantify, and certify designs of complex structures. The availability of a range of commercial modeling and simulations tools and packages with a variety of capabilities, in conjunction with increased computational resources, is allowing analysts to rapidly perform detailed analyses. However, care should be taken to understand specific tool limitations, assumptions, and boundary conditions as erroneous results can be generated without being recognized by the analysts. In addition, the reported margins of safety should be carefully interrogated to identify any false positive or negative margins and highlight any areas for structural concern. - 12-01: Simulation Framework for Rapid Entry, Descent, and Landing Analysis
The NASA Engineering and Safety Center has archived a number of key historic Entry, Descent, and Landing (EDL) simulation models and developed several new models to enhance the capability of the Agency to evaluate a wide range of EDL systems for system analysis studies, preliminary design, mission development and execution, and time-critical assessments. The simulation models developed in this activity can be used to help define the required architectures and investment strategies for future robotic and human exploration missions. - 11-01: Nickel-Hydrogen (NiH2) Common Pressure Vessel (CPV) Cell Capacity Loss and Voltage Collapse
During an investigation of anomalous voltages during a NASA scientific mission, a NASA Engineering and Safety Center (NESC) team discovered that the design of NiH 2 CPV batteries may be susceptible to a unique electrolyte bridging between the two internal cells resulting in undesired ionic current flow. This condition can lead to depletion of the capacity within one of the two cells. - 10-02 – Potential Failure of Dual Simultaneously Initiated Pyrotechnic Operated Valve
The NASA Engineering and Safety Center (NESC) Technical Bulletin No. 09-01 reported an independent investigation of four pyrovalve failures that occurred while using aluminum (Al) pyrovalve primer chamber assemblies (PCAs) during ground testing. The investigation revealed that simultaneous firing (within a few microseconds) of the NASA Standard Initiators (NSIs) was the primary reason why the booster charge failed to ignite and the pyrovalves subsequently failed to operate. A second investigation of a new stainless steel (SS) PCA design with separate flame channels was completed in 2010. The new SS configuration was found to be improved in most respects; however, no improvement was noted in the temperature delivered to ignite the booster during dual simultaneous NSI firings. Simultaneous firings should be avoided when using either the Al or the SS PCA design. - 10-01: Power MOSFET Thermal Instability
In the quest for faster switching times and lower “on resistance” the Metal-Oxide Semiconductor Field-Effect Transistor (MOSFET), produced since 1998, has achieved most intended goals. Unfortunately, lower “on resistance” and higher switching speeds in the designs now being produced allow the charge carrier dominated region to develop conditions that could lead to thermal runaway. Temperatures above 450º C on any location within the part can cause the metals to begin migrating causing a fatal short circuit. - 09-05: Self-Contained Oxygen Generator
A Self-Contained Oxygen Generator (SCOG) produces breathable oxygen (O ² ) by using chemically-reactive briquettes that begin producing O ² when mechanically ignited. Contamination with organic material of, or manufacturing defects in, the briquettes have been shown to lead to conditions that can cause an explosive failure. - 09-04: Penetrant NDE Capability
As the desired crack detection size is decreased and approaches the physical limitations of liquid penetrant inspection techniques, the approach of performing a probability of detection (POD) validation test at a single aspect ratio, and then extending the results to other aspect ratios based on equivalent area predictions may not be valid. POD testing for penetrant inspection of metallic pressure vessels and COPV liners should be performed at the bounds of the required range of crack aspect ratios. - 09-03: Battery Database/Guideline
Lithium-Ion (Li-Ion) batteries are fast becoming the battery chemistry of choice for aerospace applications requiring (rechargeable) power supplies. These batteries offer high-energy density and high-specific energy combined with excellent rate capability and cycle potential. The increased energy content and operational characteristics of this system require defined safety and handling procedures to ensure the safe implementation. Standardized approaches to defining, determining, and addressing safety, handling, and qualification for Li-Ion batteries have been developed and published as an NESC-sponsored Li-Ion Battery Guidelines Document. A data base was established cataloging cells and batteries that have been considered for aerospace applications. - 09-02: Battery Protection
Most commercial cylindrical 18650 Lithium-Ion (Li-Ion) cells have two internal protective devices: the Positive Temperature Coefficient (PTC) and the Current Interrupt Device (CID). The PTC protects the cells under external short conditions and the CID protects the cells under overcharge conditions. While proven to be effective at the single cell and small-size battery levels, these devices do not always offer protection when used in high- voltage and high-capacity battery designs. - 09-01: Pyrotechnic Valves Failure
Investigation of recent pyrovalve failures reveals timing of redundant initiator firings is crucial for reliable operation of pyrovalves. Simultaneous firing, i.e., within a very narrow time frame, was found to be the primary cause of the valve failing to operate. Testing of both single and dual initiators revealed important design characteristics affecting pyrovalve device performance. They include Primer Chamber Assembly (PCA) geometry and material properties, as well as operational effects on combustion product flow, and resulting energy transfer to the booster.
The CONAX PCA design has evolved slowly over time undergoing incremental changes to correct known issues. These piecewise changes were verified by limited test, without a full understanding of the overall system impact or effect on margins. Adequate system performance margins may be adversely affected in existing or future systems incorporating a pyrovalve actuated by simultaneous firing of dual initiators. - 07-01: Braycote Grease Storage
Braycote™ greases that are in mechanisms in controlled storage retain their tribological properties for an extended period of time. Testing on aged and separated Braycote™ grease obtained from several sources showed no detrimental effect on lubricity. Additionally, Thermal Gravimetric Analysis testing demonstrated no significant decrease in performance due to static, controlled storage. Tribological action, heat, or other forces are required to effect the performance of Braycote™ grease.