From Earth orbit to the Moon and Mars, explore the world of human spaceflight with NASA each week on the official podcast of the Johnson Space Center in Houston, Texas. Listen to in-depth conversations with the astronauts, scientists and engineers who make it possible.
On episode 326, NASA experts discuss VIPER’s vacuum chamber testing in preparation for a south pole lunar landing from inside of NASA Johnson’s Chamber A. This episode was recorded on December 8, 2023.
Transcript
Host (Gary Jordan): Houston, we have a podcast! Welcome to the official podcast of the NASA Johnson Space Center, Episode 326, “Podcast in a Vacuum Chamber.” I’m Gary Jordan. I’ll be your host today on this podcast, we bring in the experts, scientists, engineers, and astronauts, all to let you know what’s going on in the world of human spaceflight and more. How do you know if a system is truly ready for space when you build a spacecraft that’s not just tightening that last bolt and strapping that system on top of a rocket? No spacecraft systems go through rigorous testing. Rockets fire their engines on the ground. Spacecraft are slammed with acoustics and vibrations. Capsules are dropped into water, and oftentimes a fully assembled vehicle is put in a special chamber to prepare for the stress of extreme temperature and vacuum. Now, this Thermal Vacuum testing is often essential to verify a spacecraft readiness for flight, but just why do we use this test and what does it mean?
On this episode, we’re chatting with Jonathan Homan, System Test Branch chief in the engineering directorate here at the Johnson Space Center. We had him on the podcast back in 2018 to discuss the Vacuum Chamber testing for the James Webb Space Telescope that was done here in Houston at the time. We brought him into the studio as we normally do. But on this episode, we got the unique privilege to record the interview inside a vacuum chamber. Of course, not while in vacuum, but the location allowed us to have a very interesting conversation while immersed in this unique and somewhat magical environment. Chamber A is preparing to receive the VIPER rover that will land on the lunar South Pole this year. So we also chat with test director for VIPER’s Chamber A testing, Steven Del Papa. With that, I’m very excited to chat with Jonathan Homan and Steven Del Papa in what is probably the coolest location we’ve ever recorded a podcast. Let’s get into it. Enjoy.
[Music]
Host: Jonathan Homan, thank you so much for coming on Houston We Have a Podcast today.
Jonathan Homan: Thank you. It’s definitely an honor to have you here, Gary and your team, and to show you guys our amazing facility here at the Johnson Space Center. And like I said, I think it’s just an incredible asset for the agency.
Host: Jonathan, the honor’s all mine. This is—you went out of your way. We’re like, “Hey, you want to come to our studio?” You’re like, “No, Gary, why don’t you come to our fantastic facility so we can record in chamber A.” I mean, I’ve be honest, Jonathan, I am just in awe. This is just a spectacular facility. I feel kind of out of place like I’m supposed to be like a spacecraft or something, you know, it’s just a massive facility. I wonder—I am just in awe just sitting here and recognizing its scale and value—but I wonder if you get a chance to do this. Just come into and just really take a moment. I’m sure you’re working hard and you have a lot of engineering, but just to take a moment to appreciate just the scale of this facility is unbelievable.
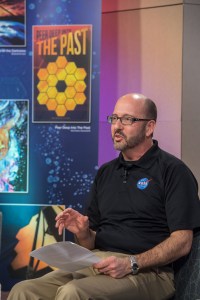
Jonathan Homan: No, I appreciate you saying that because I do feel that way. But again, like I said, I think I’ve been very busy, but I was also very fortunate. This facility is near and dear to me for my career. So I started early on, probably in the nineties, kind of supporting a lot of space station development and that some of this was being tested here. So I did get to spend quite a bit of time in this chamber, and it is crazy how unique and the amazing amount of engineering and technology that went into designing this, especially originally for Apollo, and to see how it’s been used and how we have used it to support NASA’s missions over the years. So I see it and I go, “Wow.” When you see the black, I also just go, I don’t know if you get this feeling, but I see this, I see the door and I see there’s a clean room out there, there’s light, and it’s almost like an escape. And in here you feel like, yes, this could be space in here. And that’s what its role is to simulate space. And you realize this is going to be really cold and harsh, and you understand why, how hard it is to design things in space and how hard it is for things to survive space-like environments and how important it is to use a facility like this to be able to test.
Host: Yeah. There are really so many ways to verify a spacecraft system, and we’ll get into a lot of the specifics here specifically with this, with this test. But really thinking about thermal vacuum testing, you talk about this is really putting a lot on the spacecraft. You design a spacecraft, you have hopes for how it will perform in space. But really, let’s talk about thermal vacuum testing for just a second. What exactly is that? What is the value that that kind of test provides to a spacecraft?
Jonathan Homan: Yeah, so most spacecraft wants to both qualify and accept. So qualify usually means we’re proving out the design at its max limits. So we’re going to take it to its thermal extremes and go with hot and cold multiple times and see if everything continues to perform. And then acceptance means, hey, here’s the final kind of flight design. And it’s kind of proving a lot of the workmanship. But another big thing that we also do with thermal vacuum testing is especially more modern days, is correlate thermal models. So we have all these instruments that we attach on thing on onto the spacecraft, be able to collect a lot of data and give it to analysts who are trying to figure out how things are going to perform out in space. And it lets them kind of correlate. So they can say, “Oh yes, our models look correct here on something where they can collect a lot of data.” And so when they’re out in space and they can’t collect a lot of data, they know that they’re accurate in the environment that they’re seeing out in space.
Host: I see you’re designing a spacecraft, you put it into a CAD or you put it into a computer simulation, you have some idea of how it’s going to perform. But really, how well does the data match your expectations in the design, in the computer animations? Let’s actually put it in a facility and just see how that compares. Because if they compare really well, you can expect very similar performance in space.
Jonathan Homan: Correct. So that’s almost always the heart of our customers who come in here are the flight missions, as well as, like you said, you put in mechanical structures. Do those things work at these extremes when they’re at the very coldest temperatures that they’re supposed to operate at? You know, when we get down there and they soak for a while, because you can’t do it in a lab. The only way to get to those temperatures is to come into an environment that allows you to create that cryogenic environment or very high-temperature environment.
Host: So let’s get into Chamber A, let’s get into exactly where we are. So thermal vacuum testing, I want to understand more about this facility because just besides being an operational and very unique and important test facility, it’s a historic landmark as well. It’s got a lot of storied history. Can you take us to the beginning?
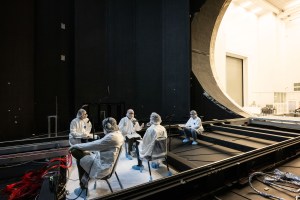
Jonathan Homan: Yes. So, you know, this chamber was designed specifically to support the Apollo program. We specifically again tested the Apollo Service and Command Module 8. So it was the capsule where the actual astronauts lived and the service command module where you had the limb and the lunar module that would land and the engines and stuff like that carried it back and forth between the Moon and Earth. And so, this was designed in 1962, or it was supposed to be brought on in 1962. And again, when I think about the engineering and what they had to do, you didn’t have a lot of computer models. So I was going to tell you a quick story of, you know, when you think about this chamber, it’s a large soda can, when you think of we’re pulling all the air out and it wants to collapse. Well, the very first time they tried to test it, it did start collapsing at about a few PSI differential. And that’s because they didn’t have the computer models to do finite element modelling. So they had to produce like small models that would simulate the size of the chamber and kind of do performance testing on them. And they weren’t able to get everything right. So they had to come back and reinforce this chamber. And so it really didn’t come online until 1964, which was perfect, still earlier than going to the Moon in 1969 with humans. So they got it right.
But some of the unique features, excuse me, on this chamber that were very specific to Apollo that were not as specific for like James Webb were the Apollo service command module. Again, same thing. They didn’t have very good thermal modelling. So they had to figure out how does this spacecraft perform as it’s going to the Moon and back and once it leaves Earth’s orbit, it’s sitting there and they decided to do a slow roll to be able to kind of make sure that one side that’s always facing the Sun isn’t burning up. So it’s constantly moving. So one part of it’s always facing the cold of space and one side’s facing the Sun. And we used to have solar simulators that would simulate the Sun’s intensity outside of our atmosphere, they had to follow spacecraft in here. And this whole floor that we were sitting on in the past used to have a rotating device to move it.
Host: Okay. Like a lazy Susan.
Jonathan Homan: Lazy Susan. Right. We used to call it like a rotisserie.
Host: Rotisserie. Yeah, yeah.
Jonathan Homan: You’d bake it on one side and then it was actually super cold on the other side. So it’s not like it was ambient-type temperatures. But it was like, yeah, it was super cold. So that was really unique. And at the time too, you got to remember, we actually had humans in the vehicle during the testing, so we had to have our systems in here to be able to rescue a human really fast. That was a real big difference and the original design of that. But because it was so successful in testing Apollo prior to sending the vehicle to the Moon, it’ one of the reasons it’s a national historic landmark.
Host: Yeah. So it was, I mean, when we are thinking about, I mean, you talk about coming online in 1964, this is a lot, this is a storied history of operations well over 50 years. So there’s a lot that this has done. But when it comes to the design, when it comes to the initial thoughts of what exactly do we need, it was done very much with Apollo in mind.
Jonathan Homan: Correct. And a lot of engineers and pens and paper, not as much, you know, computer modeling, but it’s an amazing when you look at the engineering that was done, but yes.
Host: Yeah. I mean, you talk about computer models, right? You don’t have that, so you have to do just a tiny model. Yeah, I love that. But I mean, with the Apollo in mind, I think one thing that is hard to appreciate, maybe even in pictures, we’re going to show some of the photography of this online, but the door is massive. The facility is massive. Why the scale?
Jonathan Homan: Oh yeah. The scale was, if you can think of the entire service command module was in this chamber. So this is a 40-foot diameter door. Actually, Apollo could not fit in here stacked and roll in here. But we had the rail system, this is actually these rails. The Apollo rails are gone. And these are the rails specifically for James Webb. But it’s a very similar type of concept that we used where they built up out there and they rolled in, but they actually brought the command module in, lifted it up and then brought the service module in and stacked it in the chamber. So you had something that was actually above 40 feet in this chamber.
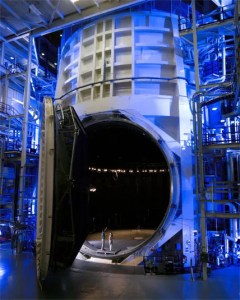
Host: There it is. So you had to bring it in. The door is not necessarily tall enough, but to get that stack, you bring everything in, stack it, put it on the rotisserie table. And now you have yourselves a really good robust test. Excellent. Wow. So when the test was actually being conducted, right? You put it on the rotisserie table, you shut the door, bring everything down to vacuum, and then you start your observations. What is the operations of a test? Let’s stay in the Apollo days here for a sec. What does the operations of a test look like in 1960s?
Jonathan Homan: I would say that the basic operations from the roles and responsibilities of different people are not that much different. So we have a control room and we have a test director that runs the operations, kind of leading the team. And then we have technicians that are all around the facility operating different equipment that helps the facility get to the space-like environment for us.
So in Apollo, a lot of the big things they had to test, because probably the most important was going to be like the thermal systems cause they have never tested a thermal system that was going to see that type of environment. But a lot of other things were happening as well cause we had humans in the chamber. So we had life support systems that had never been designed to work in space before, carrying humans, you know, you have multiple people that are watching each of their subsystems as you do an integrated system level test. So when you think like, hey, Apollo, you’re testing this capsule. It’s now like when I say a customer, that customer’s a team, a team of multiple engineers, right? Multiple, you know, maybe even scientists and stuff like that. It’s very similar. Also with James Webb, we probably had more than a hundred people come through that were supporting James Webb verifying their hardware. So the operations are very similar that.
Host: Yeah. It makes sense. You guys are in charge of making sure that everything goes smoothly because this customer is very much counting on the data from this test. So you have to just oversee that everything it gets on the rail safely. Any stacking that’s required that is done safely and we are able to execute the test. What the customer is caring about is, am I getting the data that I want? Because obviously, this is very important. Now when you’re executing a test and when you’re actually putting this chamber into operation, we talk about thermal vacuum. I guess one of the things is you have to take this giant chamber and it’s full of air. And then you have to bring that, you have to suck it all out and bring it down to vacuum and get to those conditions. What is that like?
Jonathan Homan: So in this building, we have a series of both mechanical pumps. So we’re forcibly removing the air. And that kind of helps takes us down to a certain level of pressure. Once you get to a certain level of pressure, those molecules are harder and harder to capture. So we use the next set of pumps, which are, again, we have on this chamber right now, we have turbo-molecular pumps. So they’re just really fast rotary veins that are, again, mechanically pulling anything that makes contact with them out and out of the chamber. And then the last little bit is we start freezing the molecules out. We have pumps that are outside the chamber that are super cold, and anything that comes in there will freeze and stick and no longer bounce around. And then we also have a series of cryogenic panels in this chamber that are not part of this space environment, but are specifically like cryo-pumping panels that get down to, again, about 12 or 13 degrees Kelvin. So, you know, really, really cold. That’s a few degrees above absolute zero where anything like oxygen or nitrogen, once it makes contact with those panels, they just stick and they no longer move around until we get above a temperature at which they would release.
Host: Wow. So to get that volume of air out of a facility like that, it’s almost several phases of suck out. And then you have the new system to suck out even more. Make sure there’s no particles floating around, let it stick to the sides. Really try to simulate as best as you can, the vacuum of space. Molecule free. Right. And so you had, you had an interesting analogy, right? Of like Olympic pools and bringing all of that air out. So I think you said this is like four Olympic pools, correct?
Jonathan Homan: Yeah. This is about 10 million liters, about four Olympic-sized pools. And if you think about a neighborhood pool, most Olympic pools are more than twice the size of a neighborhood pool. So they’re big pools. You could fit four Olympic pools in here, volumetrically. And when we’re done pulling all the air out, it’s less than the size of a golf ball, kind of about the size of a ping-pong ball. All those molecules would fit at this current pressure that we’re at.
Host: Wow. So, okay. When it comes to a test, and we’ll get into the modifications for James Webb here in a second, but I’m thinking like high level sort of features of what makes a good thermal vacuum test. You mentioned these radiators, right? That would simulate the heat of the Sun. And as you put the spacecraft on this rotisserie table, it would alternate between heat and extreme cold in that vacuum. Those are gone for James Webb, right?
Jonathan Homan: Correct. So, real quick, I’m going to summarize what I would say, like Apollo, we had to test humans in here. That was our number one criticality is testing the humans inside the vehicle. So we had to simulate space and make sure humans stayed safe. So there was a lot of redundant systems designed for Apollo to be able to create the cold of the lunar transit and that Sun and keep human safe. With Webb, you start thinking it’s an optical telescope. So it was contamination, long duration and stability. When I say stability, it’s two parts of that stability. One is thermal stability, because any temperature change = on a spacecraft like James Webb actually causes focus issues. And then vibration stability; when it’s out in space, it has no movement. But, you know, every little thing transmits vibrations into this chamber. And we had to come up with a system to not allow that to happen with James Webb. And we actually found as we were doing more and more testing, that little things were transmitting and we had to kind of redesign those out. So that was kind of an interesting thing with Webb.
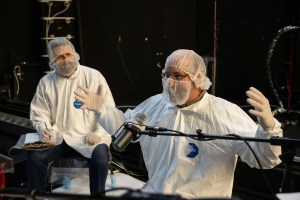
Host: Wow. Okay. You really want to isolate it like a lot. So we’ll get into James Webb here in a second. I think one thing you mentioned though, is the human-rated. So part of the design of this and Apollo, when we go back to the initial design in the sixties, is redundant systems and crew rescue abilities, things like that. Are those all still here or were those removed as well?
Jonathan Homan: They are here in Chamber B.
Host: Aha. We’ll talk about that, too. Yeah. But not for Chamber A.
Jonathan Homan: Not for Chamber A. So Chamber A, if you think about the size of this volume, we have to have the ability to rescue somebody. So that means we have to be able to push air in here really fast and bring in rescue technicians. And the size of this chamber, it became actually just way too dangerous to be able to do human testing. Now, Apollo, the good thing was they were actually in the spacecraft themselves. So they were living in there with the ability to kind of, we could repress the chamber if needed and keep them safe. Where Chamber B, they’re actually in a spacesuit, and if they have a problem, we have to be able to get to them really fast.
Host: I see. And that’s a much smaller chamber.
Jonathan Homan: It’s one-tenth of volumetric size, so it is much smaller.
Host: Makes sense. Okay. Now let’s get into, you know, your bread and butter is the project to take it from the historic landmark that it was and get it ready for James Webb. You were tasked with this. And it was quite an effort. Can you bring us to the beginning of that to say they came to you “Jonathan, hey, we want to put you in task of this incredible project to turn this into, you know, a high vacuum cryogenic optical test chamber for James Webb.” Where do you start?
Jonathan Homan: Well, one, it’s not just Jonathan. It’s a whole bunch of people that are doing it. So, thank you. Again, when you talk about sitting around, I can tell you that when James Webb came to us and I heard their requirements, I spent a lot of time just sitting in this chamber kind of looking at what do they need to do and what did Apollo do? And of course, so we had this helium shroud that we’re sitting on, and you see the walls here, these are light tight. That was not a requirement for Apollo. But it is a requirement for James Webb because, again, they’re looking for thermal stability. They don’t want any source of heat getting from behind these shrouds. So any energy that’s behind these shrouds has to hit the shrouds multiple times before it can pass in. So when we turn the lights off, it’s very black, but we’re not worried about the visible light. We’re more worried about the infrared light, heat transferring in and out. So that was a new concept for this chamber. And this was a new build for this chamber—the shroud.
The other thing too, this shroud had to act as a clean room. Apollo didn’t have these requirements. When you’re dealing with humans in space, you know, there’s a certain level of contamination control we do. But when you’re doing an optical telescope or things that have a lot of sensitivity on science instruments, contamination becomes a huge concern that you don’t want something that once it’s clean and integrated in a spacecraft, there’s any chance of something migrating. So the air flows in this chamber completely different, we flip the air. In Apollo, the air used to kind of come in through the bottom and we could pull the air out the top. Now we change it from a top-down. So it kind of flows as a laminar airflow. And it’s all super clean air. We have a multiple sets of HEPA filtration and environmental controls to make sure that the air that you’re breathing in this chamber is particulate-free and the constituents in there are really pure. So we have a lot of carbon filtration to make sure anything that’s in Houston coming from our local area is purified out. Probably the last big thing I can think of, actually two big things is the duration. When we did Apollo testing, they probably only tested for one week, sometimes maybe a little under two weeks at a time. So they run the systems really hard, get the data they needed, turn around and get ready for the next test. But a lot of systems were designed to be I would think of it like a race car. So it’s going, but you’re just going to replace the engine at the end and you know, swap parts out.
Host: Change out the tires, keep going.
Jonathan Homan: Yeah. And that was the Apollo era. James Webb we’re coming in, they needed to test for three to six months at a time. They didn’t know they needed to test for a year. And we needed to design systems that could just sit there and operate and create this environment and hold it stable for months and months and months at a time. So that was a big difference. And then the last is the one we already kind of talked about is the vibration. We had to figure out, you know, we have trucks going by outside, there’s air conditioning system in this building. You can hear the little bit of buzzing right now, even just around the chamber. And we could not have any of that vibration coming and affecting the optical performance of what we were testing.
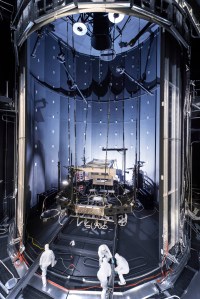
Host: Yeah. So let’s hit those one at a time. Let’s start with the shroud. So you have this problem, no optical or infrared light can enter into this. So you picked this and this is what we’re looking at now, right? When you say shroud, it’s the black panels that we’re looking at right now. So, you know, what are they made of in order to accomplish such a big task? And I feel like you had a special order them, right? This is quite unique.
Jonathan Homan: Correct. And all that. And one of the very unique things about this chamber is, again, this is our big door, 40 foot, but you can see our shroud panels are taller than 40 foot. We couldn’t just buy this and have it dropped into the chamber. We had to buy these from specialty vendors who work with us with creating like space-type equipment and then have it assembled in here. So it was kind of building a little bit of a ship-in-a-bottle type of scenario. So, you know, we had to kind of do all that and then try to maintain a certain amount of contamination control while you’re doing heavy construction.
So when you ask about the construction or the materials, the materials are all aluminum. They are a grade of aluminum that allows them go to a really cold temperature so there is some differences between, you know, what you might find in your aluminum can that you’re drinking a soft drink out of. And then we coat them all with a black paint that is highly admissive down to really cold temperatures. So, like I said, any energy that’s hitting it, it will tend to absorb that energy. Real interesting fact about those shrouds too is these shrouds probably shrink about four inches in length as we go cold. So there’s a little bit of overlap. So everything’s hanging from the ceiling. So the shroud is actually hanging from the ceiling other than the floor. The floor is supported here, but all the walls in the ceiling actually suck up a little bit as we get colder. And that’s one of the things why we don’t mount anything to the rails because the rails in the test article would move. So we actually lift things off the rails and kind of isolate them so as everything in this chamber is starting to shrink and move, the testicle we’re holding is kind of remaining stable.
Host: Okay. Yeah. A lot of considerations, right? It’s not just the light. You have to think about the contamination, there’s a lot that goes—even the paint—
Jonathan Homan: Even the paint, yeah. A really unique paint. You’re not going to go buy it at Sherwin-Williams or Home Depot. It’s special ordered, you know, it, it is a flight-type grade paint. So it’s got to be able to not off gas at really, you know, low vacuum and survive really high extreme temperature. So we can take this paint, it’s not as good of a high-temperature paint as some others, but we can take this paint to about maybe 185 degrees Fahrenheit, I think about 70-so degrees Celsius. And then of course it goes all the way down to close to absolute zero.
Host: That’s very important.
Jonathan Homan: Yeah.
Host: Yeah. For thermal vacuum, right? The extreme colds is unbelievable. Now, the air, the clean air that you talked about. I mean, it’s more than just providing clean air. You talked about changing the direction of the air as part of the project to get ready for James. What was the reason for that and the project and the work that actually went behind that?
Jonathan Homan: Yeah. That, that was one of our sub-projects of getting ready for James Webb. So what we ended up doing is there’s a massive amount of piping outside the chamber that allows the air to flow. So before it used to flow in from the bottom, and we had a way to pull it from the top. All we did is flip the direction down by the big pumps, kind of changing the direction of the piping. But these are four-foot diameter pipes. They’re really large. It’s not small stuff that we were dealing with. And then what we do again, is we’re pulling in a certain amount of Houston air. A certain amount of this is just being recirculated, but all that air comes in, it goes through, like I said, a series of pre-filters, carbon filters, and then HEPA filtration is the last thing. Then after all that, we thermally control it. So it goes through like essentially an air conditioner system where we, you know, control the humidity and control the temperature. And then we do a final kind of filtration and then push it in here. And like I said, so it’s coming in from the top. You probably can’t feel it that much right now. And then it actually kind of pulls through the floor. And then the reason why it moves hopefully slow is what you don’t want is when people are working in here around test articles, they’re generating particles. You want it to be slowly swept and go into the system. You don’t want it to be floating around. And then, like I said, you got James Webb with this large cup here. People are working around it. You don’t want something coming off somebody’s, you clean garment cause you’re going to shed particles as you move. And have those kind of redeposit on top of test hardware.
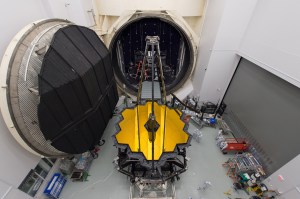
Host: Fascinating. You want it gentle to avoid spewing nasties all over the place.
Jonathan Homan: Yeah, like a little bit of a flow that’s kind of like pushing everything down.
Host: Yeah. Absolutely fascinating. Okay. So the next one was duration that you mentioned. Now, how do we get from relying on systems that only have to do, you know, a couple of days to several months? I mean, you have to have really robust systems cause one of the things you said is not just the duration, but you have to maintain it steady. You can’t have a lot of fluctuation. So what went into the improvements to get ready for Webb for duration?
Jonathan Homan: Yeah. I would say the one biggest thing that we made the modification for for duration was our cryogenic liquid nitrogen system. So this cold shroud you see is helium that creates the space-like environment and it gets really cold. But the bulk of the energy that takes you from 300 degrees Kelvin around room temperature to 15 degrees Kelvin is liquid nitrogen, but it’s closer to 100 degrees Kelvin. And then the helium kind of brings you the rest of the way down. Well, it used to be a forced flow, which means that we used mechanical pumps and a whole lot of safety systems to make the liquid nitrogen system work. We completely changed it to a thermo-siphon, which is a natural flow system. So actually, all those tanks, I don’t know if you’ve ever seen driven by our building, but we have six large liquid nitrogen tanks.
Host: Oh yeah. Hard to miss.
Jonathan Homan: Yeah, yeah. We push the liquid nitrogen up to the top above the roof of the chamber, and then gravity just feeds it down and gravity and the energy causes it to change the density and come back up. So there’s no pumps, there’s no mechanical systems anymore. So all we need is a certain amount of power to be able to move the valves and to read the instruments and run a control system. So we got a computer. So with that, all we needed was an uninterruptible power supply. And then we always have an emergency generator for a lot of our systems. But you know, when you’re running pumps, they’re energy hogs I would say, you know, they use a lot more energy. So we became much more efficient. In fact, our usage of the liquid nitrogen went down tremendously when we redesigned the chamber. But that allows us to kind of keep that full of liquid nitrogen going. And as long as there’s liquid out in those tanks, if we had a hurricane hit, which we did–
Host: Yeah. This happened just a couple months after Harvey.
Jonathan Homan: Yeah. Harvey actually hit while we were testing. But we didn’t lose power fortunately, but with that, if we had lost power, the liquid nitrogen would’ve continued to flow. So that was kind of one of our biggest design changes. And then our helium system, unfortunately, because helium is a closed loop system, helium is a rare Earth kind of molecule. So we try to keep it all enclosed. So we take helium that’s compressed again in some of our large tanks, you might see outside. It runs through a refrigerator and gets down to the cryogenic chamber temperatures, runs in here, picks up that load and goes back. And then it’s kind of just recycled over and over again where the nitrogen is not, we buy liquid nitrogen just like the hospitals and other industry do because it’s very common in air. And it’s less expensive to just use the refrigeration properties of that cryogen and to have it turn into gas and vent it back to the atmosphere than it is for us to try to have a closed loop system.
Host: Efficiency is what I’m hearing.
Jonathan Homan: Efficiency was a big thing.
Host: Improving the efficiency.
Jonathan Homan: Correct. As you improve the efficiency, you actually realize that things run longer with less energy going into it. So it’s like, hey, we kind of designed the chambers in such a way that if we walked away from it and it had an issue, it would sit there and just run for a long period of time. And the idea was to protect the test article in case there was a hurricane. But as long as we have power, we are able to maintain the conditions that it wants to see, the test article wants to see.
Host: Yeah. There’s that stability that you were talking about. Exactly. Yeah. Okay. Last one was the vibration table. So we are on it right now, yes?
Jonathan Homan: Well, nope.
Host: No?
Jonathan Homan: We’re not. So for James Webb, the vibration system’s up on the roof of this chamber.
Host: Oh fascinating.
Jonathan Homan: So as I mentioned, the shrouds are supported by the dome of the chamber. So they’re actually physically connected and supported by the dome of the chamber. Again, in Apollo, they had a top sun. So there’s a series of penetration plates that were at the top to be able to do a solar simulator. We took some of those penetration plates and put a vibration system above the chamber and ran those rods down through the helium shroud. And they all came all the way down to these rails. And we actually lifted James Webb up with all its optical equipment and all that kind of was what we’d call an optical bench. So if you can think above the chamber, you have this vibration isolation system, and then everything is kind of just floating.
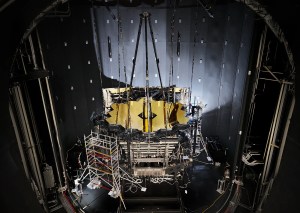
Host: Wow. So, suspended.
Jonathan Homan: Yeah. Suspended. So if you think of it, I’m trying to remove a vibration at a very high level way above where the center of gravity is. And it worked very, very well. And a big thing for us, which puts us in favor of other parts of the country is Houston is not sitting on bedrock. This chamber is just pounded into gumbo, Houston gumbo, with like huge pylons. So, you know, if a train is going, it tends not to transmit in here, but there’s still a lot of vibration from the building. And one of the things we ended up finding out, kind of an interesting thing, is we were talking to some of the folks about our instrumentation before is that’s where we started finding, we were seeing, we were picking up frequencies going into James Webb, and we realized it was coming from all these cables because as these cables become cold, they’re no longer flexible, they’re rocks. And they were sitting on the floor, and then they were going back up to James Webb and we were seeing things moving. So we ended up having to come up with a localized like little thing right here to be able to put the cables on a vibration isolation, or a vibration dampening system. So we actually let the vibrations dampen out and then go back up to the test article.
Host: There’s no forgiveness, it sounds like.
Jonathan Homan: There’s no forgiveness. And it’s one of those things where with James Webb, we finished the chamber in like 2012, but we did the flight test in 2017 into 2018. But those years in between, we did a lot of small testing because we had so much we needed to learn to be able to test the true performance of James Webb.
Host: You needed it, right? In order to prepare I mean, you thought you were ready to go and all of a sudden you realized that you have these super cold cables that are causing vibration. This thing needs vibration isolation. So you need to solve those problems. So you said you finished at 2012, several years of repairing for James Webb. Tell me about the moments leading up to, “Hey, Jonathan, James Webb is about to arrive to your facility. Are you ready?” What were some of the things that you were thinking like, “Oh boy, am I ready? Have I thought about all of these different things? Have we tested it enough?”
Jonathan Homan: From the chamber standpoint, I was very confident. And also from JSC’s standpoint, I was very confident. I felt like there was great support from all the way up, our center director was wanting to make sure everybody was on board that, hey, we’ve got at the time $8 billion worth of test hardware coming in. You know, it wasn’t the entire spacecraft because the spacecraft bus and sun-shield were still out at Northrop Grumman. But all the really challenging things were controlled by the government, you know, through the Goddard Space Flight Center and their team. So, you know, the primary mirrors, the secondary mirrors, the tertiary devices and all the science instruments being integrated, the stuff that was actually going to be capturing these amazing images we’re seeing now was going to be tested here and proven out prior to being shipped to Northrop Grumman to be integrated to the spacecraft bus, which has, you know, the parts that are facing the Earth and doing like, you know, little maneuvers and all the communication and data transfers and stuff.
Host: Okay. Now, now when it arrived here and you had to start putting it in, I don’t know if we touched on this a little bit, but we’re in a clean room right now. We’re wearing, you know, we’re wearing some pretty intense gear to make sure we don’t have any of our human particles going all over the facility yet to turn this into a clean room in order to prepare this too.
Jonathan Homan: Correct. Yeah. And we hadn’t had that level of experience of working with clean rooms until James Webb. And as you’re saying, we’re getting ready for VIPER, and this is the contamination level we need for VIPER. When we did James Webb, we actually put another layer on top of you, so it would’ve been really uncomfortable. So we had a full ESD bunny suit on top of it where you had the hoodie and everything integrated and covered so that we had even less chance of particulate. I mean, every time you come in here, it’s an effort to get gowned up and come in, you know, we try to tell people to come in prepared, bring your own water bottles, bring stuff like that. But, you know, if you have to leave naturally, it’s an effort. And one of the things that we were telling some of the gentlemen before is we’d be working down here and realize you have to work on something up above. And it’s like, I’ve got to go take everything off, go up three flights of stairs, and then again, re-get everything back on. So I can go deal with some minor issue that was 30 feet above my head. Or 40 feet above my head.
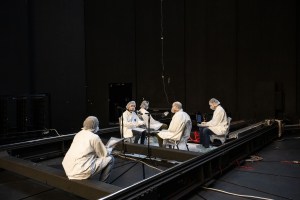
Host: But you’ve got to do it, right? Cause you’ve got to keep it absolutely pristine. So you reflect on your time when James Webb was here, you had a lot of prep, it was a big project. James Webb was here reflecting on the test, how did everything go?
Jonathan Homan: Oh, the test was great. I would say the hurricane was probably one of my most stressful times in my life. But because I was mostly concerned about the safety of the people here. Then I was about the testing that was going on. I’m going to kind of jump a little bit ahead because I know I had the privilege of being asked by some media to kind of talk about, “Oh, James Webb launched, it’s deploying. What are your concerns? What are your thoughts going into it?” And I was like, you know, we spent 45 days getting James Webb down to the temperatures it needed to be at to be able to start testing the mirrors. And then Harvey hit, and the building looked like a war hit, you know, a lot of the ceiling tiles fell in. We created a lot of like plastic barriers to try to protect all the different areas that were looking at the test article. So we ended up kind of just creating like tenting, a second layer of tenting so we could continue testing. And during that, that was the primary time where we were kind of taking the mirrors from their kind of minor launch lock position.
So they had a series of deployments they had to go through, the primary mirrors and also the secondary mirror. And then, if you know, Webb has 18 individual segments for the primary mirror, and they all were out of focus. So we had to get them into focus and also get them to be into alignment as well. So instead of 18 different mirrors all of a sudden became one large monolith. And we did that while we were dealing with rain and flooding in a building that was not conducive to work in, but we made it work and people got stuck here for a long time because a lot of, especially the JSC team, many of them live lived in areas that were completely flooded out. So we had kind of prepared for that and kind of had people being able to bring stuff in here and let them, you know, camp out. So we kind of had that camp out kind of mentality. So we kept working even though the center was closed for more than two weeks. So when they were talking about the alignment of the mirrors in space and if I had any concerns, I was like, if we did it during Harvey, and I know how successful it was, I really wasn’t concerned about it happening in space because I knew what they were going to do, and I knew how we proved it out here in this chamber.
Host: Wow. You can prepare so much, right? You’re thinking about the cables, you’re thinking about that, and all of a sudden, you know, you get hit with this unexpected challenge with Harvey, but sounds like you guys were prepared, you were concerned about the team. And I think it just shows the resilience of the team, right? Not only is everybody trying to work through this challenge of Harvey in their own homes and just, you know, life here in Houston during that time, but making sure the test not only continues, but continues pristinely. And you could say that on the back end of that test, even through all those challenges, you guys have a successful test here.
Jonathan Homan: Yes. And absolutely. And not to kind of get into too many stories, but one of our biggest concerns during Harvey was our liquid nitrogen prior to Harvey, about a day or so before, we quit getting deliveries, they shut that down and set those folks home. And we weren’t expecting that. So we were actually getting to a point where we were thinking we might have to make a decision on there, but we were able to make calls and we were helped out by one of our vendors. The Kennedy Space Center got a special contract for us, emergency, worked while our center was closed, they were able to pull in and some other vendors, and we were able to continue testing. But those were like those, like I said, the people who were working the test and the chamber and the spacecraft, James Webb never knew anything was going on. But we were having to kind of rapidly kind of work some things to keep the testing rolling.
Host: Oh, cool. Oh my goodness. Yeah. I could see what you mean by the liquid nitrogen is getting lower, lower, lower. You’ve got to fill it and otherwise you’re right, the decision would be to pull it out of the test, right?
Jonathan Homan: Correct. Yeah. Stop the test and then you know, eventually have to restart. And that would’ve been a huge delay for James Webb.
Host: It would’ve pushed back the whole timeline, but you guys kept on going. Honestly, the team did incredible when you reflect on that.
Jonathan Homan: Yeah. No, absolutely. They did a great job.
Host: Okay. So just going outside of Chamber A for just a second, I want to stress that we have this incredible facility. We’re here, we get to record in here, but just to tackle some of the other capabilities that we have, right? Because I think one thing that’s important is this is able to address, you know, certain kinds of tests, right? We’re talking about James Webb, because that was a significant test that had to go into this chamber. But when it comes to some of the other facilities you have here, we talked about Chamber B being the human-rated one. You guys have other facilities with other capabilities. What are some of the things you have around that allow for testing of spacecraft and other needs?
Jonathan Homan: Yeah, so our branch, we call ourselves a Systems Test Branch, but we specifically do kind of space simulation when it goes to thermal vacuum and thermal vacuum-type testing. So we have facilities here in Building 32, Chambers A and B. We have Building 33 that has a lot of small vacuum, thermal vacuum, and thermal chambers. And then we have facilities in Building 7 that are kind of vacuum-focused, and there’s a thermal vacuum as well. But the ones in Building 7 are definitely focused on testing with humans in that environment. So it’s a completely different level.
So I usually like to tell people, we focus on human exploration and large-scale testing, but we all kind of do the small stuff as well, which is a great kind of learning ground for people as well as there’s just more of that, and programs always need to test on the small scale. Even as we’re doing James Webb, they wanted to use our small chambers as they test things out before they integrate it into the big chamber. So, that’s a lot of what is happening currently with one of our current customers, VIPER, you know, we do a lot of small scale testing, and then it gets assembled into a larger vehicle, and then we’re going to test the large vehicle here in this chamber.
But Chamber B I’m going to talk about a little bit, because that is human-rated. So we just recently got through with testing the xEMU, the Exploration EMU, the new suit that NASA designed. Currently, there’s the xEVA’s contract, so people have that ability to look at that suit and design that. So there’s two vendors who are building new suits and providing EVA services. But we wanted to see how far the government had taken its design. And we had like, probably one of the most amazing tests just a few months ago here. And then we also did one this summer for SpaceX, where we tested a commercial suit for them. And so, you know, the unique thing about that chamber is we know how to test humans in that risky environment. And what we have outside our field building, again, is we have the liquid nitrogen tanks, and then there’s a lot of other tanks, and we compress those with air. Again, it’s very, very pure air to a high pressure so that if there is an emergency, the test directors have the ability to hit a button and start the repress of that chamber and then automatically, our technicians are trained, they know what to do, and we have a couple technicians that would go in and do the rescue.
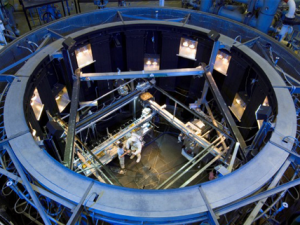
Host: So what can we expect typically for, you know, you mentioned spacesuits, right? So you mentioned Axion Space, Collins Aerospace as providers for the Extravehicular suits, you mentioned SpaceX as well. So you put a subject in a suit and you bring it down to vacuum. What sorts of tests, what sorts of things are happening that allow for you to walk away from that test and say, “Hey, I learned something.” Maybe it’s about the suit’s functionality, it’s reaction to a vacuum environment. What exactly are we learning in a test like that?
Jonathan Homan: Yeah, usually first is the modality of the suit, being able to move around in it, it’s usually proven out. You don’t need the thermal vacuum to do that. But a lot of the systems that support the life support of the human in the suit don’t really work until you’re in a thermal vacuum environment or a vacuum environment. So then all of a sudden the human becomes a metabolic load with a soul essentially, you know, they’re in there working their tail off. We try to work them really hard to see if the systems, that the suit has to provide their life support to pull that heat away, to remove the carbon dioxide, keep them alive and safe and working safely are working. So that’s a lot of what we do in there. It’s like testing the suit performance.
When I think of things like the EMU that’s on space station, and was developed for the shuttle, same thing. We did a lot of that testing, but then we did a huge series of testing with the EMU in Chamber B that was mostly hardware testing for space station. So the other big thing we can do in there is, hey, you’re going to do a spacewalk on space station, and it’s a high risk environment. We can simulate that environment and their operations in Chamber B prior to going into space. And we don’t try to do it from a what would happen in the NBL, where they’re testing out the operation so much. We’re usually looking at testing the hardware with the human. And especially like when we did space station assembly, hey, here’s two different things that need to be assembled, but the flight hardware hasn’t been done together in a flight like environment. And that’s what we were able to do. So we weren’t using the suit or the human to test the performance of the suit. We’re using the suit to keep the human alive and give them as much of a feel of what they’re going to be dealing with in space in terms of the spacesuit. So they’ve got the ability of the reach and the limitations of doing things. And now we’ve got to do high-risk EVA assembly in Chamber B. So that’s another part of it.
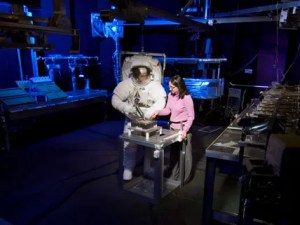
And then of course, you know, kind of a big thing is like for like SpaceX, one of the things is it’s just the way they’ve designed their suit, it’s acceptance testing. So their suits are built specifically for each crew member. So one of the things they want to do is take them in an environment and make sure that each suit that is built for their private astronaut is going to work for them. And since it’s not a fleet of suits like we have on the EMU, everyone’s a custom make so they want to do like a series of just kind of testing each suit with each crew member and just prove out the workmanship, if that makes sense.
Host: Yeah, it does. Yeah. I think about myself and if I were to go into one of those spacesuits and really test the performance and push the performance of a spacesuit systems and have to do, you know, running and really exert myself, I don’t think I would be a very good test subject. I think they wouldn’t get the data. They’d need someone a little bit more fit than me.
Jonathan, this is awesome. I’m going to take a quick pause right now and turn to Steven Del Papa, test director here in the Systems Branch, because I want to bring it back really quickly to the Chamber. A testing. Cause Jonathan, you’ve mentioned this a couple of times, we’re gearing up this facility right now to test a very important hardware, very important mission that we have coming up, VIPER. Steven, welcome to the podcast.
Steven Del Papa: Thank you for having me. I’m glad to be here.
Host: Awesome, alright, so you are in charge. Now, we talked a lot about James Webb with Jonathan. You’re in charge of the upcoming tests for VIPER. So let’s start with just introducing our audience to VIPER. What is VIPER?
Steven Del Papa: So VIPER stands for Volatiles Inspecting Polar Exploration Rover. The purpose of it is to land on the South Pole and investigate the regolith and primarily to quantifiably measure the amount of water that is at various depth and levels within the regolith. The regolith is just the lunar surface, the rocks, the dirt, and all that. So we do know that there is water ice, but we know what the distribution is. We don’t know what the quantity is or specific points, what the amount is. So this lunar rover, that’s what it’s going to measure, and that’s all part of leading up to humans living on the lunar surface. Okay, cause water is going to be one of the primary sources, not just the water itself, but it can be broken apart and used for fuel and other things. So this is kind of a precursor and part of the science that we need for humans living on the lunar surface.
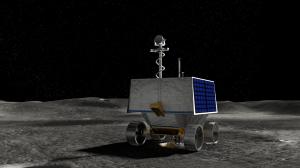
Host: Excellent. Now, this is quite challenging, or at least VIPER is going to go through quite a challenging time. We talked about James Webb going into the vacuum of space, obviously very harsh conditions. You know, talked about even for Apollo, that rotisserie roll, right? Of introducing with the heat of the Sun and the extreme cold against the Sun. But there are some areas on the Moon in the lunar South Pole that are permanently shadowed, no sun. Right? So we’re talking about areas that are, I think, colder than we’re used to when it comes to space operations. And this is VIPER. So is this test going to help with understanding VIPER’s performance for that?
Steven Del Papa: Well, this is all part as Jonathan mentioned, where we qualify the hardware. So this is the final test of qualifying the rover itself. The mantra is you want to test as you fly. So the chamber is to give you that environment. It’s different from James Webb, which is a deep space spacecraft. So it’s not going to see the thermal extremes. So VIPER, we will be taking it to the ultimate cold temperature that the chamber can provide down to 20, 15 kelvin around that range. But we’re also going to be thermally cycling it, which is also bringing it up to the expected hot temperature that you would see on the lunar surface. So it does have additional hardware to do that thermal cycling and in order to qualify and to verify that it does work in the environment.
Host: Right? Yes, of course, cause VIPER isn’t just going to drive into a permanently shattered region and stay there, right? You have to operate on the lunar surface and the southern poles and it’s going to have a little bit of sunlight, right? You have to work on that. Okay. So what are you doing as test director to prepare this chamber, Chamber A, for VIPER’s test?
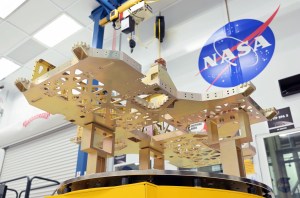
Steven Del Papa: So one of the main things that we had to do was to provide all the test support hardware. So the hardware that’s going to interface between the rover itself and the rails that it will be sitting on. We provided the hardware for producing the thermal environment when we want to go to the hot condition and reconfiguring the facility in order to meet their very specific objectives. We don’t have the harsh requirements of vibration isolation. It’s a much simpler test in a lot of regards compared to James Webb. It is a long duration. We’re looking at this point roughly about 24 days of a test. That’s including the original pump down the cooling of the chamber, going through the thermal cycling, and then the warmup at the very end.
Host: Okay. Now, it seems like the facility itself is armed with a lot of the capabilities just from the James Webb upgrades. The one that I think that’s a little different, and maybe you can clarify for me, is this warming, is that a new sort of capability that you guys have to prepare for and install?
Steven Del Papa: It is a new capability because we removed the system that originally provided heat.
Host: The Apollo one. Yeah.
Steven Del Papa: The Apollo, all the solar simulators. We would actually have to do some major modifications to bring that back. So instead a radiation enclosure was developed where we have these hanging panels that surround VIPER at certain locations, and we would heat those up and then that would subsequently radiate to the rover and bring its temperature up. So that’s how we would do the thermal cycling. So that was built very specifically in order to bring that elevated temperature capability back for this customer.
Host: Excellent. Okay. So you guys are going to be working on that. When it comes to the operations over those 24 days, what are some of the things that we can expect? You know, I guess does it start with bringing it down to those extreme cold temperatures, 15, 20 Kelvin, and then you start firing it with some heat? Or what is the duration? What does the test look like?
Steven Del Papa: So we followed the standard operation of originally of first pulling the chamber to vacuum. Now, actually, the first portion of the VIPER test is to elevate the temperature because the first phase is to do a bake out of the hardware. So under vacuum at an elevated temperature. And we hold it and we have sensors, CQCM’s, Cryogenic Quartz Crystal Microbalance. And the purpose of that is it actually measures the outgassing rate that the hardware is liberating in the vacuum environment because VIPER does have some sensitive, like optics on it. There’s an original part of the mission phase where they do elevate the temperature as part of the bake out on its transit to the lunar surface. And that’s what we’re doing in the chamber as well. So the first phase is the bake out phase.
We’re going to take it to the hot survivability condition, and then we start cooling it down, and then we go to a thermal balance condition. So Jonathan talked about thermal math modelling, and that’s the purpose of this, where it’s very critical that we hold the chamber and the environment to a stability level. So it’s a constant environment that the VIPER is exposed to. And then they put energy into their various systems and they see where that energy goes to and they measure it and they validate their math model using that portion of the test.
After that, then we start going to the cryogenic condition and fully cool down the shrouds. And then once the shrouds are full cold or cryo-stable as we call it, and then we’ll start doing the thermal cycling of powering on the radiation enclosure and cycling it that way. We will be using the radiation enclosure also for elevating it during the bake out phase as well. So it’ll be used before that, but that’s in general what the process and the various phases of the VIPER t-vac test is going to be.
Host: Excellent. And this is really, you’ve mentioned the final test, right? So VIPER’s undergoing quite a bit, but after this one it gets shipped over to the Cape for integration into the launch vehicle.
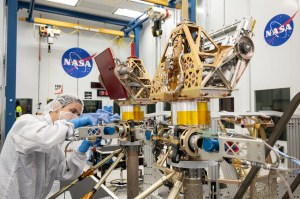
Steven Del Papa: Yes. Our Branch has supported VIPER in various ways. We’ve actually, in our Building 33 or smaller chambers, we have tested quite a bit of their component-level hardware. Going through qualification and acceptance level on the component level. But again, this test in Chamber A is kind of the final culmination of the whole vehicle itself, putting it in that space environment and then testing the systems. Okay, they have various operations that the VIPER team is going to be doing. We provide the environment that they want and they put their systems through the rigorous testing in the environment that we provide. And that’s kind of the final check to make sure everything is working before you send it off into space.
Host: So we’re in December, now, December, 2023, recording this episode. How are things going, in terms of preparing for that test?
Steven Del Papa: Things are going well. You know, we have a huge team, not just on the facility side preparing for it, but also on the VIPER team for the integration and all the engineers and technicians are doing a great job. At this point we’re looking at the late spring time, so in about four or five months is when we’re going to do the t-vac test here in Chamber A for it.
Host: Very exciting. How do you feel? You feel ready or, man, there’s a lot to do.
Steven Del Papa: We still have some work to do in front of us. I am, I don’t want to say nervous, but I am happy, you know, to be a part of the team. And to lead this wonderful team. You know, I’m very confident that we’ll get there. We do have work ahead of us, as I said. But barring any major catastrophe, that is going to be a very successful test.
Host: Very good. Well, I’m sure you have a lot to do, and I think nervous is the right emotion, right? Not because it’s just because of the responsibility. You know, that this is a very important test. This is really the final test before it goes over to Florida for that integration and gets integrated onto the Griffin Lander and of course, the launch vehicle to go to the lunar South Pole. And this is a very important mission. So Steven, thanks for what you’re doing to prepare for VIPER.
Steven Del Papa: It’s my pleasure. also said nervous kind of tongue in cheek, because that is the name of one of the instruments on the rover itself. So just an Easter egg.
Host: Oh yeah. NIRVSS. Yes, yes. That’s being tested on an upcoming, commercial lunar payload mission too. And ahead of its time with VIPER, that’s the one that’s measuring water ice, if I’m not mistaken. I believe.
Steven Del Papa: That’s one of the instruments. Another one, you know, they have a neutron detector. They have the MSOLO, which is the mass spectrometer as well. So yes, VIPER has various systems and instruments on it.
Host: And when you test it in Chamber A, it’s not only going to verify VIPER, it’s going to verify the payloads that are integrated with it?
Steven Del Papa: I would have to ask VIPER team with exactly when they’re do, but I know one of the things that will be determined real time during the test is for the MSOLO, there is a cap on that optical sensor that the really, the only time that they can determine if that cap will deploy or actually test it environment is going to be during this test. We don’t want to contaminate it. So measuring the outgassing level, using the CQCM and what that data is showing at that moment is going to feed into a real time decision for testing that very specific piece of hardware.
Host: There you go. Well, Steven, I know you got a lot of work to do to prepare for this test. We’ll let you go and we’ll head over to Jonathan for some final questions,
Jonathan, you know, we had this conversation about Chamber A, the facilities we have here, thermal, vacuum testing, really even VIPER, just the conversation with Steven. Thinking about the importance of a test like this, you know, you’ve obviously care very much about these facilities and the tests and the value of them. I wonder, from your perspective, think about thermal vacuum testing and the facilities we have to verify some of these systems. When someone asks you, “Why do we have these facilities? Why do we support these things?’ How do you respond?
Jonathan Homan: Well, when, tests go perfect, unfortunately, a lot of people who are spending the money go, “Wow, that was a lot of money for us to not learn anything.” And I’m like, “No. It was a lot of money to verify that the thing’s ready to work.” So, like with James Webb, we had probably close to 200 objectives. And they were all done successfully. But we actually had four different things that were found during that test. And one actually was one of the mirrors was not coming into focus. And we thought it was a mechanical installation problem. And we were able to kind of do an analysis and prove that it was, and be able to, post-test, quick go find out what we thought was wrong, cause we actually realized it was a bolt putting a little bit of pressure on one of the mirrors that should not have been there. So somebody screwed it in just a little too far. We were able to put that where it was supposed to be, do a really short test, and verify that was right. And it works. So that way, you know, you’re kind of proving like, hey, the design’s great, but then the assembly has a chance to have you some issues. There was also some thermal things we didn’t understand, and we realized that the thermal portions of James Webb were not from the design, but again, how we were actually testing it. So it’s again, kind of a thing to prove out.
When I talk about Chamber B and human testing. When space station was being assembled, we had a series of what they called human-rated thermal vacuum test that the EVA program office wanted to do because we had Boeing and all these vendors bringing all this hardware, some international partners, and none of it was being integrated and tested on the ground. It was going to be flown and integrated. And they were saying, “Hey, there’s a lot of high-risk stuff here. And during that test, we found out that 98% of the stuff, when we were integrating it, either had to go through a redesign or the EVA community had to come up with special tools to help the astronauts be able to do this assembly and do it successfully. And or we had to change some of our operations. If we had not done that, the potential damage it could have done for both our agency’s reputation, but also if hardware did not go together well and, you know, we lost part of the mission, it would’ve been a big disaster.
So when testing goes well, people go, “Wow, that’s a lot of money to do a test.” Cause it’s expensive, like what James Webb did. And of course, Hubble didn’t do what James Webb did. And, you know, had to have a service repair mission, which probably cost on the order of a hundred times more or maybe a thousand times more than what the actual thermal vacuum test would’ve cost, which, you know, was still expensive. But when you think about developing new hardware, flying it up there and integrating it, they spent way more than they would’ve if they had done a proper ground test. So, that’s some of just the lessons learned that I’ve seen, you know, in doing testing,
Host: The 98% is very significant to me. That’s redesigning, that’s a lot. That’s really starting from scratch almost in a sense in terms of your approach to things.
Jonathan Homan: Yeah. And a lot of it wasn’t huge redesigns. Like some of the stuff we found were, again, people designed this stuff and one vendor for Boeing built a piece of hardware, another built a second, and they were supposed to be integrated on this during a spacewalk for the space station. And we realized like the fit didn’t quite work just right. So, you know, yes. It just needed a slight modification. It wasn’t a major redesign, but it was a slight modification to be able to see that, hey, these two components go together. Even though this vendor goes, “I met my requirements and I tested it in my facility in a smaller chamber like we have at 33, and it meets its requirements.” Well, it wasn’t integrated as a system. And you think of something like space station, there’s no way to put the entire space station together and do a test. But, you know, there is so much assembly done through spacewalks and we had to really kind of reduce that risk. So that might give you a little bit of a perspective.
Host: Right and maybe I use the wrong terminology. I mean, obviously, it’s not necessarily a redesign, but ultimately you need to make sure that two things work together.
Jonathan Homan: Correct. And then some of it we realized two things work together, but you couldn’t get it together with a spacesuit as it is. So then we ended up having to get the EVA community to look at it and say, “Hey, well you know what? We actually need a special tool to help them put that together.” And that wasn’t thought of until you actually do the test.
Host: Yes. Yes. It just reveals so much. The thing that I think is apparent, I think in the spaceflight community, but maybe needs to be said out loud is there’s almost a sense of perfection that’s required when it comes to designing a spacecraft. You talked about even on James Webb, just a bolt, right? It goes down to that level, like how to make the whole thing work together. You need to fix, you know, a bolt and Hubble, it was a mirror, right? So it was some small thing, but it’s this test that really brings your system to that level of confidence and can reveal stuff that can ultimately in space make you successful.
Jonathan Homan: Correct. Yes.
Host: Excellent. Now of course, I wanted to end on this note, and you’ve stressed this a couple of times, I think I’m credit I’m crediting you, but you say, you know, “It’s not just Jonathan. It’s a whole team.” And I do want to recognize that for a second is, you’re obviously essential in a lot of the integration for James Webb and this and this facility and everything. But just to recognize, when it comes to making sure that we successfully pull off a test, the folks that are dedicated to maintaining this facility on, you know, a day-to-day basis, the folks that come in and make sure that all teams are working together on a successful test run. It’s not just a couple of people doing this.
Jonathan Homan: Oh, absolutely. And you got to talk with Steven. He’s one of our test directors. And I always like to tell people, our test directors are our tip of the spear. They kind of interface directly with our program customers and who’s going in there. And then they have a team of engineers, and then the engineers have sometimes more engineers. And then we have a team of technicians who are the actually hands-on people putting the instruments into the chamber, you know, doing the operations, the guys who run our cryogenic systems or run our vacuum systems. So, you know, there is a huge swath of people that both work to design and integrate to get the test built and then operate our facilities. And then, like I said, those same people also have to maintain these facilities. So they have to have a certain amount of knowledge and care of, wow, there’s a lot of stuff around this building and I want to make sure that it’s in pristine order, you know, so that we’re ready to keep NASA’s mission successful in our small part of doing their testing.

Host: So on that note, this is where I want to end is just thinking about that systems test and the facilities you bring to verify some of these critical things before they head off into space. One thing that you like to keep in mind and to let your team know on the value of what systems test and the Branch and the folks that are supporting bring to the spaceflight community. What is it the purpose that you are serving to ensure successful spaceflight?
Jonathan Homan: Well, you know, some of the neat thing that we get to do is we’re kind of at the tail end, so integration and test of hardware. We get to see everything almost, you know, that that’s flying out here. Currently, like I said, we’ve got VIPER coming, but we have multiple VIPER’s. The Science Mission Directorate. We’ve got NEO Surveyor coming, which is another Science Mission Directorate, and then we’ve got STMD, and of course HEO, so we get to see all kinds of hardware. We’re not in that design phase of that hardware, but before that hardware is going into space, our role is so critical that it comes through here and we verify its operation. So, you know, like I said, it’s very stressful too because usually we’re really close, like on Webb. You know, if we are delayed, we’re causing a launch delay. If we delayed VIPER, we’d be causing a launch delay. So we’re always, you know, trying to tell everyone, we always try to work with a sense of urgency, but also with that sense of we want to make sure that they’re successful and we’re doing everything the right way and safely. So that’s kind of like what I try to tell everyone and then I’m like, man, you guys, we are needed. You are needed by every mission directorate. And that’s, that’s a great place to be is to kind of feel like, hey, everybody needs our facilities. And you know, everyone plays a part in that to make NASA successful.
Host: Something they get behind and truly something that is needed for successful spaceflight. Jonathan, thank you so much. This was such a treat, not just to get to talk to you, to talk to Steven and really dive in much deeper on Chamber A and the facilities we have here than we have in the past. But you brought me to Chamber A, this is awesome. I mean, just to be in this environment and as we’re talking about the importance of this testing, to just see the scale of this and just appreciate, you know, the work that’s gone in to make it what it is and to continue the testing. This was an absolute treat. Thank you so much for having us come in.
Jonathan Homan: You’re very welcome. Again, it was our honor to have you here.
Host: Very good. Thanks Jonathan.
Jonathan Homan: You’re welcome.
[Music]
Host: Hey, thanks for sticking around. That might have been one of the coolest experiences that we had, to record an episode inside of a vacuum chamber. I really hope you got a sense of just how magical it was. In fact, you can check out our episode webpage for some of the photos that we captured during the recording session and just hopefully, you got a sense of that reverb and the scale of the environment that we were in. But seeing those photos, you can certainly appreciate it maybe just a little bit more. Special thanks to Dane Turner and Will Flato for all the work that it took to prepare with the teams. And we’ll thank all of them later to get this ready for recording.
Thanks for sticking around. I hope you learned something today. This is of course not the first time we talked with Jonathan. If you want to, you can listen to Episode 31, going way back the episode title is “The James Webb Space Telescope.” We caught Jonathan while the famous telescope was here at the Johnson Space Center for testing in Chamber A back in 2018.
You could check out nasa.gov for the latest happening on Chamber A, on VIPER, on NASA Johnson. And of course, we have many podcasts across the whole agency. You can go to nasa.gov/podcasts to listen to any of the shows we have across the agency, as well as ours in our whole episode list, which you can listen to in no particular order. On the NASA Johnson Space Center pages of social media like Facebook, X, and Instagram, you can chat with us using #AskNASA and ask a question or maybe make a suggestion for the show. Just make sure to mention it’s for us at Houston We Have a Podcast.
This episode was recorded on December 8, 2023. Thanks to Will Flato, Dane Turner, Abby Graf, Jaden Jennings, Rajeev Khalil, Sammy Garcia, and the Systems Test Branch team for their support in enabling this recording. Thanks to Robert Markowitz for photographing the recording session. And of course, thanks again to Jonathan Homan and Steven Del Papa for taking the time to come on the show and record in such a special location. Give us a rating and feedback on whatever platform you’re listening to us on, and tell us what you think of our podcast. We’ll be back next week.