Quick Facts
Year Built: 1930
Historic Eligibility: Former National Historic Landmark
Important Tests: Brewster F2A-2 Buffalo, gust testing, drag cleanup of almost all U.S. WWII aircraft, propulsion noise, dirigibles, submarines, VTOL and V/STOL, British P.1127 Fighter, delta wing, swept wing, blended wing, parachutes, ground-based structures, Project Mercury, Lunar Landing Test Vehicle, Space Shuttle.
History
The 30- by 60-Foot Tunnel, Building 643 in the NASA East Area, was NASA’s oldest operating wind tunnel until its closing in October 1995. Originally known as the Full-Scale Tunnel, it operated for more than 64 years. It was the largest wind tunnel in the world until 1945, and in 1985 was named a National Historic Landmark. Throughout its history, it was the site of historically significant research, used to test everything from World War II aircraft, to submarines, to the Mercury capsule, to concepts for supersonic transport.
Full-Scale Tunnel
The Variable Density Tunnel (VDT) of the National Advisory Committee for Aeronautics (NACA), put into operation in the 1920s, was recognized as a breakthrough accomplishment in wind-tunnel testing technology. By using higher than atmospheric pressure in its airstream, the VDT provided aerodynamic conditions more representative of those experienced in flight. However, the relatively small size of its test section required the use of relatively small aircraft models and severely limited testing of full-scale airplane components. Powered models could not be accommodated, and the aerodynamic effects of real aircraft construction such as rivets, fabric, and other component details were difficult or impossible to simulate.
Of even more concern, however, was the recognition that significant aerodynamic turbulence was present in the VDT’s air flow due to the geometrical shape of the tunnel. As the concern over results from the VDT began to grow, several research leaders at Langley began to advocate for a new wind tunnel, one capable of conducting tests of full-scale aircraft.
In February of 1929, the NACA authorized construction of the Full-Scale Tunnel (FST) at Langley. Design work started immediately, led by Smith J. DeFrance and included Abraham Silverstein, Clinton H. Dearborn and Harry J. Goett. Three of these NACA researchers later became directors of other NACA/NASA field centers: DeFrance (Ames); Silverstein (Lewis); and Goett (Goddard).
The timing of the Full-Scale Tunnel project was fortunate. The initial appropriation of $900,000 was made before the onset of the Great Depression, and by the time work began in the spring of 1930, labor and material costs had fallen, and there was a large pool of unemployed engineers who needed work.
Since the FST was to be the first wind tunnel constructed with an elliptic throat and two drive propellers mounted side-by-side, the designers requested that a 1/15-scale model of the FST be constructed for studies of the flow circuit, and guidance in the shaping of the tunnel lines and airflow turning. The request was approved, but it was noted that the NACA did not have sufficient shop space for construction of the model tunnel. Instead, management suggested that the model be built outdoors with a protective roof. Construction of the model tunnel, using a lumber framework and a tarpaulin-covered roof, began in 1929 in a vacant area between two NACA power plant buildings behind the NACA administration building.
A highly successful test program provided vital information which informed the design and construction of the FST. Once the FST was finished, the model tunnel was moved into it where it was subsequently used for years as a small-scale test facility, including valuable studies of the propeller-whirl flutter instability that caused fatal accidents of two Electra turboprop transports in the 1950s. The model tunnel was subsequently given to Portugal in the late 1950s by NASA Headquarters for use in its scientific programs as part of good will within the Advisory Group for Aerospace Research and Development (AGARD) cooperative program.
In the 1970s, Langley conducted a major inspection and rehab of the FST, uncovering alarming fatigue cracks and evidence of major vibratory issues within the mounting structures of both drive motors. The non-symmetric airflow in the tunnel (both propellers rotated in the same direction) was identified as a major factor causing the problem, and Langley requested that NASA Headquarters attempt to have the model tunnel returned to Langley for additional studies of altering the flow properties in the FST. However, return of the tunnel was resisted, and even though the issue discussed at levels as high as Secretary of State Henry Kissinger, the tunnel remained in Portugal.
NASA proceeded to have a second model tunnel constructed under contract in Canada. The new model tunnel was located in the hangar annex of the FST and used to evaluate many structural modifications to mitigate the flow-induced structural problems. Several modifications to the FST came from the model investigation, including large guide vanes located around the periphery of the inlet of the tunnel exit cone.
Work on the FST proceeded rapidly, and it was completed and ready for operation in May 1931. It was dedicated on May 27, 1931, during the Sixth Annual Aircraft Engineering Conference. The largest wind tunnel in the world at that time, the FST had a unique design, with the building’s steel framework visible on the exterior of the building. The enormous facility measured 434 feet in length, 222 feet in width and 97 feet in height, immediately becoming a recognizable landmark at Langley.
The semi-elliptical test section measured 30-feet high by 60-feet wide with an open jet test section (no walls immediately adjacent to the test section), allowing the installation of aircraft with wingspans up to 40 feet. The tunnel was powered by two 35-feet 5-inch diameter propellers, each driven by a 4,000-horsepower electric motor that could circulate air through the test section at speeds between 25 and 118 mph.
The air circuit was of the double-return type, in which the airflow from the propellers was split right and left into two streams, doubling back between the test section and the building’s walls then reuniting before entering the throat of the test section. Extensive tuning of airfoil-shaped turning vanes in the tunnel circuit resulted in satisfactory flow properties in the test section. In addition to testing full-scale aircraft, the FST had considerably lower turbulence than the VDT.
Full-scale aircraft were mounted to a six-component strut support system which used linkages connected to dial-type force scales to measure air loads on the test article. Early calibrations were conducted with aircraft that also underwent flight tests permitting correlation with FST results. After successful initial operations, the tunnel became a national asset for testing and its contributions to aeronautics and space research continued for 78 years.
Early testing in the FST focused on the aerodynamic effects of aircraft geometry, and construction methods on aerodynamic drag and engine cooling. Results of exploratory testing indicated unexpectedly high penalties in performance from seemingly negligible aircraft protrusions and construction methods.
Aware of the value of such tests, in 1938 the Navy sent its Brewster F2A-2 Buffalo to Langley for analysis of the aircraft’s aerodynamic performance, which had a disappointing top speed of only 250 mph. After analyzing a number of drag-producing items such as the landing gear, exhaust stacks and gun installations, recommended design modifications were made and subsequently adopted, resulting in a 31 mph increase to the aircraft’s top speed.
The tests were such a success that both the Navy and the Army quickly began sending a steady stream of military aircraft to Langley for “drag cleanup” tests. In the next 18 months, 18 different aircraft were tested and improved in the FST. During WWII, the FST operated around the clock and seven days a week, conducting not only drag cleanup tests but also engine cooling methods, stability and control, and assessments of unexpected operational problems. Early versions of virtually every high-performance fighter aircraft were evaluated in the FST, allowing for countless design improvements that gave American pilots a critical edge in combat.
Following WWII, the FST was used in the 1950s to explore emerging new concepts such as wing sweep, delta wings, and boundary-layer control for improved low-speed performance. A remarkable variety of other subjects were also tested in the FST, including dirigibles, submarines, radar antennae, gliding parachutes, inflatable airplanes and even another wind tunnel complex.
Although the performance of jet aircraft in the postwar period outpaced its relatively low speed capabilities, the FST remained an important test facility for NACA and its successor, the National Aeronautics and Space Administration. After the creation of NASA in 1958, changes in the tunnel’s backlog of tests and transfer of key NACA personnel to the new NASA Space Task Group provided an opportunity for a new type of testing – remote-controlled free-flying models. These tests had previously been conducted in Langley’s 12-Foot Free-Flight Tunnel to determine the flight characteristics of radical aircraft designs. The FST’s huge test section provided much more room to maneuver the models and could support the testing of larger models with more realism.
The influx of free-flight models brought a decade of intense research on unconventional vertical takeoff and landing (VTOL) aircraft. Numerous types of civil and military VTOL designs were tested, including the British experimental aircraft, the P.1127, which helped lead the British to the first vertical and/or short take-off landing jet fighter bomber, the Hawker Siddeley Harrier.
In the 1960s, new types of aerospace projects were conducted to evaluate the low-speed characteristics of a parawing/capsule combination, advanced supersonic transports, lifting body configurations for spacecraft, and breakthrough concepts such as variable sweep. The tunnel was also used to test the tubular Lunar Landing Training Vehicle, assisting in an investigation into the cause of an accident during astronaut training in late 1968.
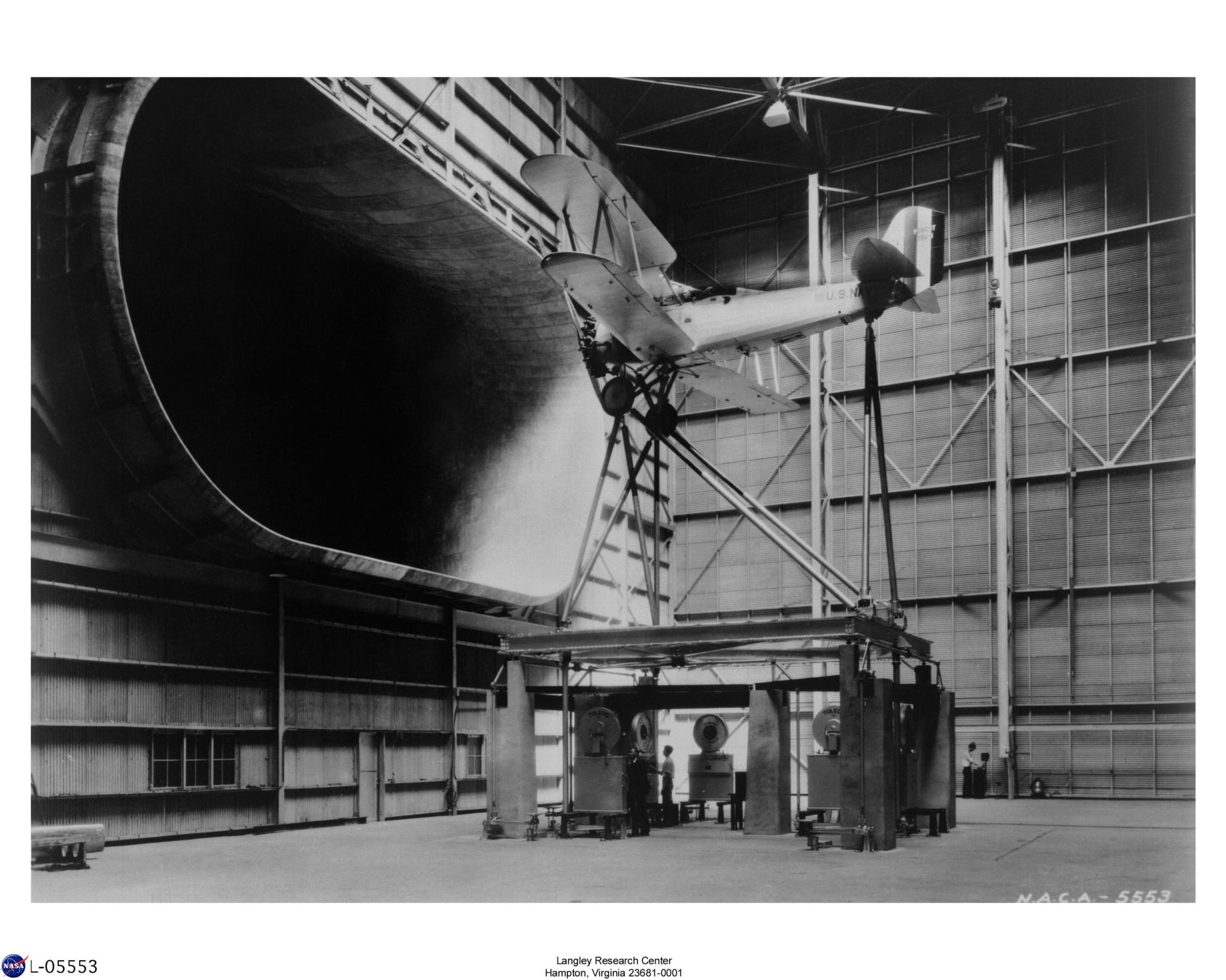
In 1969, the FST began a research program on high-angle-of-attack behavior of fighter aircraft using free-flight models. The program began an integral part of the development process for all new military high-performance aircraft for more than 25 years. An upgrade to the FST in 1977 (and later in 1984) improved the operation of the electric fan motors and allowed the facility to continue testing aircraft designs whose technology and performance could not have been envisioned in the biplane era in which it was built.
The historical significance of the FST and its many contributions to aerospace technology were recognized when it was designated a National Historic Landmark in 1985.
When NASA finally decommissioned the FST in October 1995, Langley’s oldest operating wind tunnel gained a new lease on life – it was transferred to Old Dominion University (ODU) under the terms of an innovative privatization program. ODU began operations at the FST in October 1996, providing engineering research facilities for graduate students and private customers in the field of aircraft and automotive transportation.
First Langley Gust Tunnel
Although NASA Langley’s Building 643 is normally associated with the Full-Scale Tunnel operations, it has also been the site of other significant research projects. For example, in the 1930s and 1940s the facility was the site for an innovative NACA testing technique to acquire data for the structural design of aircraft.
A daunting engineering design challenge in aviation is the development and validation of methods to predict air loads experienced during flight in gusts and turbulence. This capability is extremely important, not only from a safety-of-flight perspective, but also to prevent an overdesign of aircraft structures which would result in unnecessarily large weight penalties. Early research in the 1920s and 1930s at the NACA Langley laboratory had included theoretical studies of loads generated in specific gust fields, but flight data to substantiate the predictions were extremely difficult to obtain at that time.
To experimentally investigate gust loads under controlled conditions, in 1937 the NACA designed and constructed a pilot gust tunnel within Building 643 but outside the tunnel flow circuit, under and to the right of the FST’s exit cone structure.
The pilot gust-tunnel testing technique consisted of launching dynamically scaled, free-flight airplane models through gusts of known shapes and intensities. During the flight, measurements were made of the accelerations and reactions of the models due to the gusts. The test facility consisted of a gust generator, a catapult for launching the models, and two screens used to decelerate and catch the airplane model at the end of the flight.
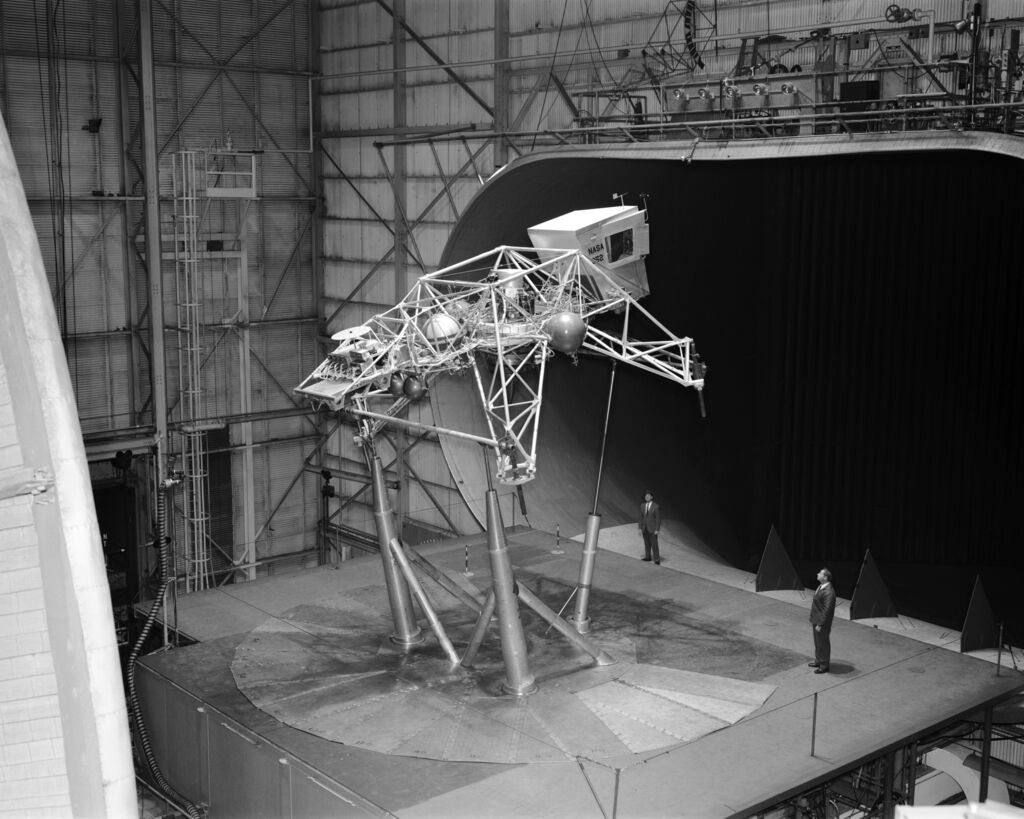
The gust generator was a large squirrel-cage blower which supplied air to an expanding rectangular channel discharging a current of air upward. The vertical jet of air was 6-feet wide by 8-feet long and its air speed profile was shaped by a combination of screen meshes designed to produce the desired gust shape. After the catapulted airplane model completed its flight through the vertical-gust field, it impacted a barrier of vertical rubber strands which decelerated the model. After deceleration, the model’s barbed hook-shaped nose engaged a burlap screen which stopped the model and held it until it could be removed by the tunnel operator. The propelling catapult was powered by a dropping weight, and the maximum model flight speed was adjustable by changing the amount of weight. The facility was capable of testing scaled airplane models having a wingspan of about 3 feet at speeds up to about 50 mph.
This first gust-tunnel facility operated in Building 643 for almost a decade. The tunnel produced very valuable information on gust loads as affected by primary aircraft design variables, and results from the facility were used to justify reducing the structural design criteria that had led to overdesign of wing structures for certain types of aircraft configurations.
In 1945, the pilot gust tunnel was replaced by a new gust tunnel in a new building, Building 1218, located in Langley’s West Area. Similar in operational concept, the new tunnel could test models with wingspans up to 6 feet and at speeds up to 100 mph. The blower from the pilot tunnel was retained and briefly used at Building 643 for studies of flow through helicopter blades in hovering flight.
Propulsion Noise Laboratory
Another important historical research operation in Building 643 was a sound laboratory used in studies of the generation and suppression of propeller noise. The sound lab was in the front right of the building, near the staff offices. The lab combined experimental and theoretical analysis of propulsion noise, and was involved in research on how to suppress noise generated by propeller-driven aircraft. Noise generators were used to simulate various levels and tones of noise during typical studies, and virtually all testing was done outside the FST test section or wind-tunnel operation.
The most famous project conducted by the sound lab group was the highly successful modification of a propeller-driven military liaison-type aircraft (Stinson L-5) in the late 1940s. During that time the rapid post-war expansion of interest in personal-owner aircraft stimulated the NACA to develop methods to reduce airplane noise. In the opinion of regulatory agencies, the threat of excessive noise from propeller aircraft was one of the most significant threats to the growth of civil aviation. Theories had been developed for the prediction of propeller noise in the late 1930s, but the NACA focused on an effort to reduce noise from all sources—propeller, engine, and exhaust system. A coordinated effort among several Langley organizations to demonstrate the ability of technology to reduce the noise of a typical personal-owner aircraft was conceived and included the sound lab contingent from the FST.
A five-bladed propeller was chosen for the experiment to reduce the required tip speed of the propeller blades, thereby reducing propeller-generated noise. Existing muffler design methods for aircraft were inadequate, forcing the FST staff to conduct experiments to arrive at a suitable muffler for the experiment. With propeller, engine, and muffler modifications, the noise pressure levels of the airplane were reduced an astounding 90 percent.
The modified airplane was demonstrated as a “quiet airplane” at the Sixteenth Annual Inspection at Langley in May 1947. Many in attendance heard the airplane as it flew over the assembled crowd at an altitude of a few hundred feet during a break at the inspection. Following the demonstration, additional flights generated detailed engineering data on noise levels for the basic and modified airplane.
Procedures Trainer for Project Mercury
Yet another research activity in Building 643 produced critical contributions during the late 1950s and early 1960s, the early days of America’s space program. As the U.S. raced to meet the Russian challenge of Sputnik, leading Langley managers and researchers realized how ignorant they were of space and rocket technologies. The massive education process included developing basic understandings of celestial flight, meeting the challenges of designing a rocket/capsule configuration that would be reliable and safe, and developing technical and political means to communicate, track, and recover astronauts after space missions.
When Langley’s Christopher C. Kraft was assigned the incredibly difficult job of organizing and directing the flight operations for the nation’s first manned space flights (Project Mercury, late 1950s), he quickly recognized the special challenges facing his team within the NASA Space Task Group. Kraft conceived the idea for flight procedures trainers that could be tied into a central command center and provide realistic training for routine and emergency operations for astronauts, controllers, and the tracking station personnel. Under NASA contracts to McDonnell, two Mercury procedures trainers were built by the Link Trainer Company, which was famous for building airplane trainers for pilots in WWII. One of the procedures trainers was installed at the Cape, the second in Building 643 at Langley.
A special enclosed room was built beneath the exit cone flooring of the FST, under the tunnel air circuit, to house Mercury Procedures Trainer No. 1. It consisted of a complete mockup of the Mercury capsule with operating instruments and controls interconnected to an analog computer. The trainer provided practice in sequence monitoring and familiarization with the cockpit systems. External reference through the capsule’s periscope was simulated by means of a cathode-ray tube display. Provision was included for pressurizing the astronaut’s suit and for simulating heat and noise. Also included in the same room, for the equally essential training of the personnel who would man the 17 Mercury tracking stations across the world, were three ground-control consoles – one for a doctor, one for a spacecraft communicator and one for a systems monitor – which comprised the minimum equipment at any one of the tracking stations.
By simulating the entire mission, the fledgling team could interact during the dozens of daily training sessions that were needed to prepare for manned missions. Virtually all the original seven astronauts used the Langley procedures trainer. With the use of the trainers, the STG team built up the procedural elements during Mercury-Redstone and Mercury-Atlas missions that would become the backbone of future NASA manned space activities. The Mercury astronauts who flew the suborbital missions claimed that the most useful pre-flight training for normal and abnormal conditions was obtained in the trainer at Langley.
On July 23, 1962, Mercury Procedures Trainer No. 1, re-designated the Mercury Simulator, was moved from Building 643 at Langley to a Manned Spacecraft Center building at Ellington Air Force Base in Houston. The room that had been occupied by the trainer then became a model preparation room for tests in the FST.
Facility Closure and Demolition
The FST performed its last test on September 4, 2009. NASA made the difficult decision to close and demolish the facility several years prior, citing deterioration of the structural integrity of the tunnel, lack of funding for repair and maintenance, and no current or future mission need for its testing capabilities. It was demolished in 2010 and its National Historic Landmark designation was removed in August 2014.
Search the NASA Technical Reports Server for additional examples of the historic research conducted in this facility. Examples include:
- The NACA full-scale wind tunnel – NASA Technical Reports Server (NTRS)
- Sound-Level Measurements of a Light Airplane Modified to Reduce Noise Reaching the Ground – NASA Technical Reports Server (NTRS)
- Calculation of tunnel-induced upwash velocities for swept and yawed wings
- An analytical study of the steady vertical descent in autorotation of single-rotor helicopters
- An Analytical Treatment of Aircraft Propeller Precession Instability
- Propeller-rotor whirl flutter – A state-of- the-art review
- Wind tunnel investigation of a 14 foot vertical axis windmill
Related Materials
Langley Memorial Aero
1987 Floorplan
Memorandum Report for Army Air Corps: Drag Analysis of the Lockheed YP-38 Airplane (1942)
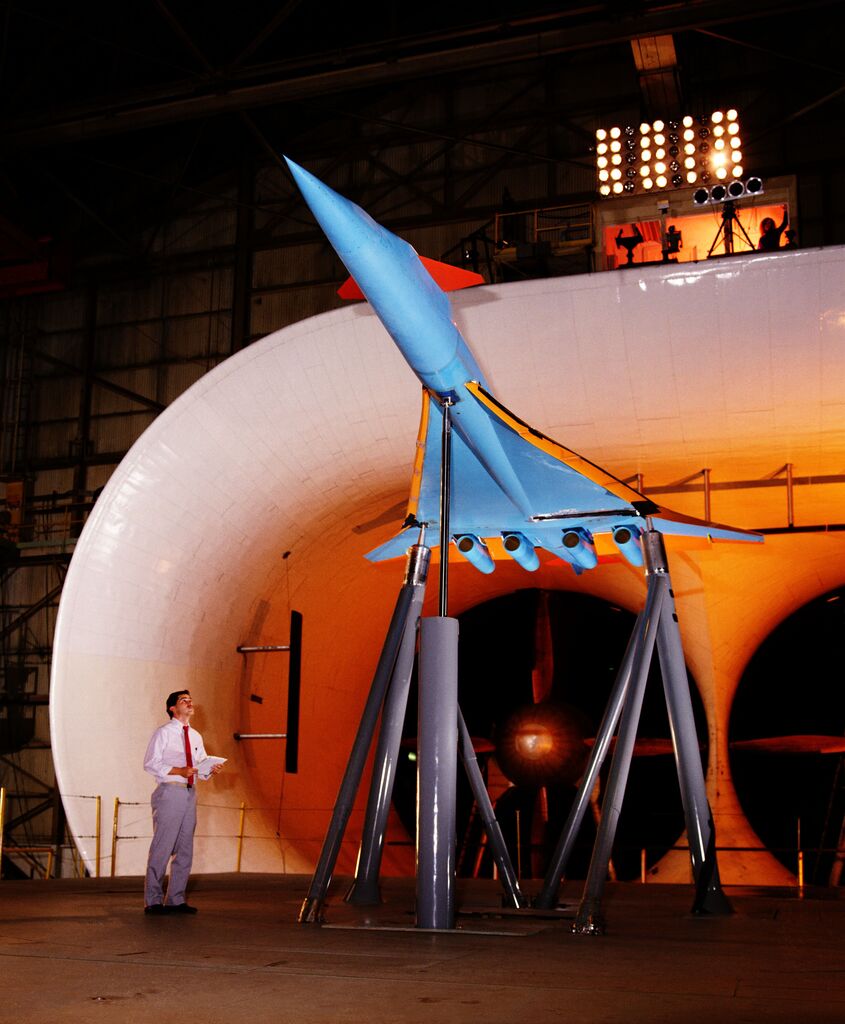