
NASA’s endeavor to create a sustainable presence on the Moon and put humans on Mars can be made easier by using natural resources on the Moon to create rocket fuel to refill landers on either surface.
Future astronauts would be able to top off their fuel after landing on the Moon, just like stopping for gas on a family vacation road trip. This would allow future lunar landers to be lighter and cheaper without needing to haul fuel for the return journey at launch from Earth.
Technology developed at NASA’s Armstrong Flight Research Center in Edwards, California, could help make that possible. The technology is FOSS, Fiber Optic Sensing System, and it took temperature measurements during tests of a system designed to liquefy oxygen in the same manner it would be done on the lunar surface. During the tests, conducted at NASA’s Glenn Research Center in Cleveland, FOSS tracked the temperatures inside a tank as oxygen chilled and condensed from a gas to a liquid at minus 297 degrees Fahrenheit.
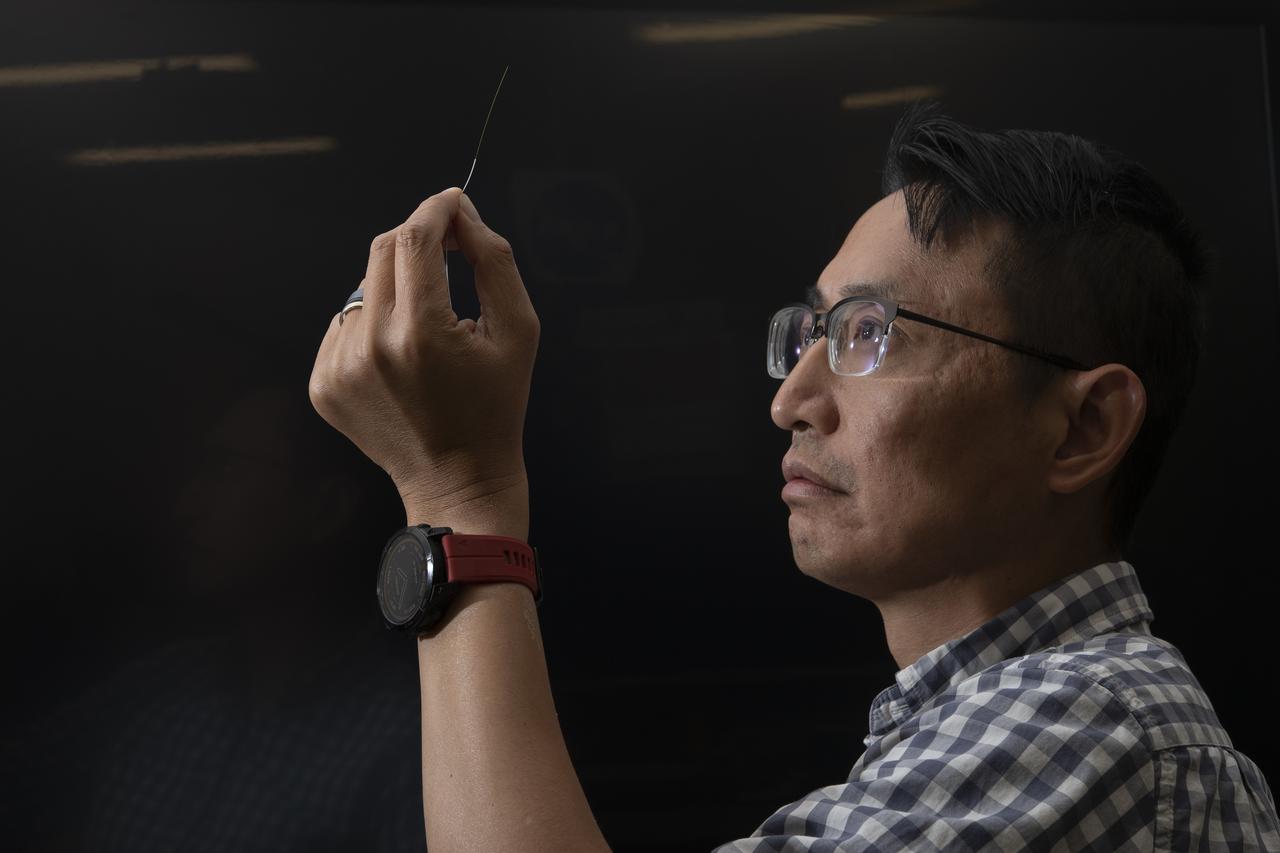
FOSS uses long strands of fiber optic wire about the thickness of a human hair to take thousands of measurements of temperature, strain, and other information critical to mission safety. In the past, collecting and transmitting such data required bulky wires and sensors. Originally developed for aircraft, NASA Armstrong’s FOSS team is adapting the technology for other uses, including space missions.
In 2018, NASA Armstrong researchers started developing a FOSS system for CryoFILL, Cryogenic Fluid In-situ Liquefaction for Landers, an effort to create a liquid oxygen manufacturing system.
“We’ve been using fiber for temperature measurement, but not in the realm of liquid oxygen testing,” said Patrick Chan, electronics engineer, and NASA Armstrong’s FOSS portfolio project manager. “We had to develop a unique sensor suitable for these extreme cold temperatures.”
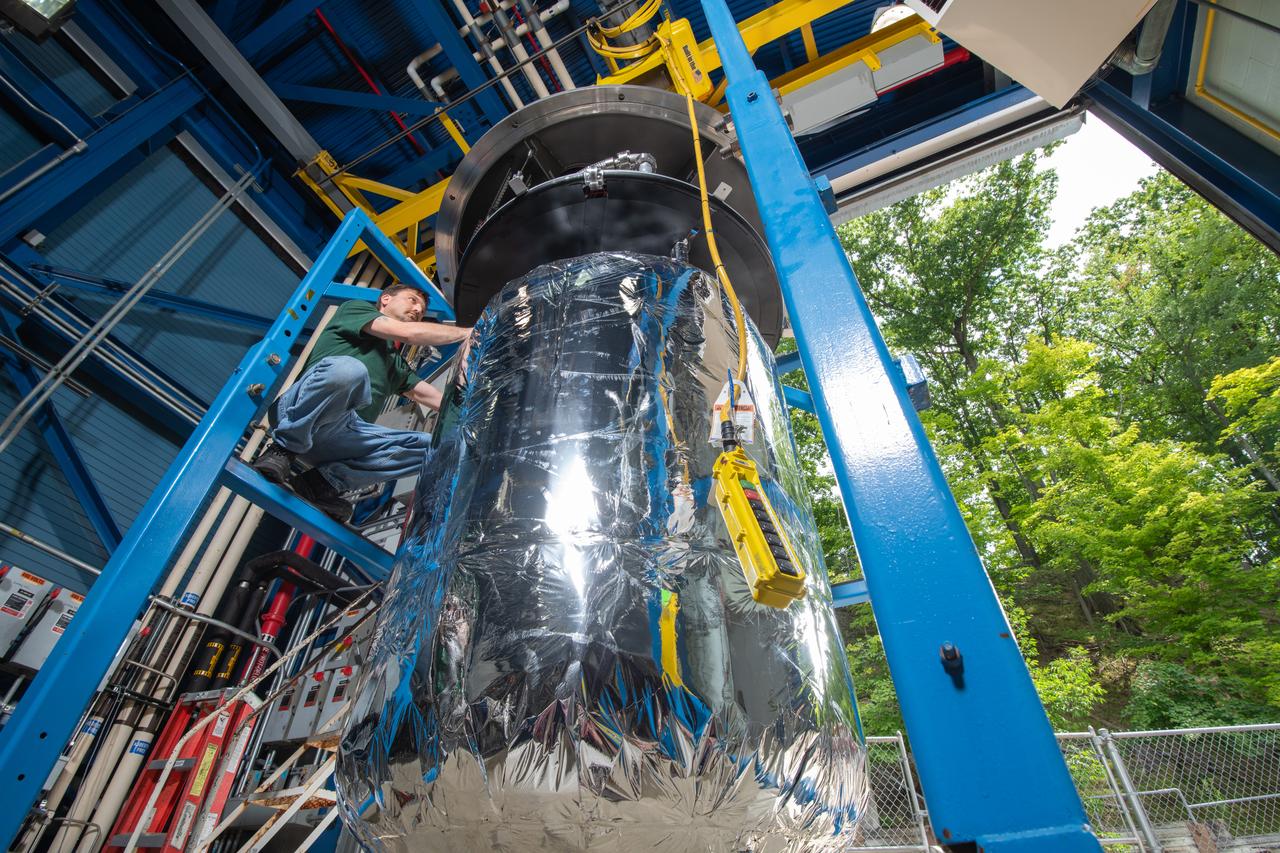
The FOSS team produced a support sleeve made of strong, waxy, nonflammable synthetic material to protect the fiber from the cold and make it safe to use in a pure oxygen atmosphere, but still allowed for the sensitivity needed to track temperatures of the liquid oxygen. The team tested the FOSS sensors using liquid nitrogen before shipping them to NASA Glenn for the test setup.
CryoFILL testing used a tank 77-inches tall with a storage capacity of up to 528 gallons. The experiments included a 140-inch FOSS strand with 330 sensors. A second temperature measuring system with silicon diodes was also used in the experiments.
More than 40 liquefaction tests were conducted over several months with researchers looking at various parameters such as flow rate and tank pressurization rates. Individual tests lasted anywhere from 24 hours to over 200 hours (about eight days).
“These are slow processes,” Chan said. “We’re talking about in terms of days, not hours. This was a tough test for fiber optics they were running the tests for days on end.”
Chan said he was impressed with the FOSS system’s performance. If the CryoFILL project moves forward with additional testing, additional optic fibers will be installed into the liquid oxygen manufacturing tank to provide more data.
CryoFILL is part of the Cryogenic Fluid Management Portfolio Project under the Technology Demonstration Missions program in NASA’s Space Technology Mission Directorate.