In This Week’s Star
- NASA Concludes Series of RS-25 Engine Tests
- New Structural Test Stand for SLS Begins Rise at Marshall
- Marshall Team Designs and Tests First NASA 3-D Printed Turbopump
- Hurricane Katrina Remembrance Ceremony Held at Michoud
- NASA, USAID Open New SERVIR Environmental Monitoring Hub in Southeast Asia
- Marshall’s Dan Irwin, SERVIR Developer, Uses Space Data — and Playgrounds — to Change the World
- Small Business Forum Held at Michoud
- Mission Success Is in Our Hands: Q&A with Carla Shackelford, System Safety Engineer
- This Week in NASA History: Von Braun Welcomes Astronauts to Marshall — Sept. 1, 1962
NASA Concludes Series of RS-25 Engine Tests
NASA has completed the first developmental test series on RS-25 engines that will power the agency’s new Space Launch System on missions deeper into space than ever before.
NASA concluded the series with a seventh hot fire test of an RS-25 developmental engine Aug. 27 on the A-1 Test Stand at the agency’s Stennis Space Center. The test ran for a full-duration 535 seconds.
“The completion of this test series is an important step in getting SLS ready for the journey to Mars,” said Steve Wofford, engines manager at NASA’s Marshall Space Flight Center, where the SLS Program is managed for the agency. “The RS-25 engine gives SLS a proven, high performance, affordable main propulsion system. It is one of the most experienced large rocket engines in the world, with more than a million seconds of ground test and flight operations time.”
The series was designed to collect valuable data on performance of the RS-25 engine, a former space shuttle main engine operating at higher thrust levels in order to provide the power needed for the SLS vehicle. Of particular interest is data that will aid in development of a new engine controller, or “brain,” to monitor engine status and communicate programmed performance needs.
“These are extremely reliable engines. We are testing them again because we want to ensure that the engine performs as required with a new engine controller, higher propellant inlet pressures and lower temperatures that are part of the SLS design. We also want to mitigate any risks on the ground before flight,” Wofford said.
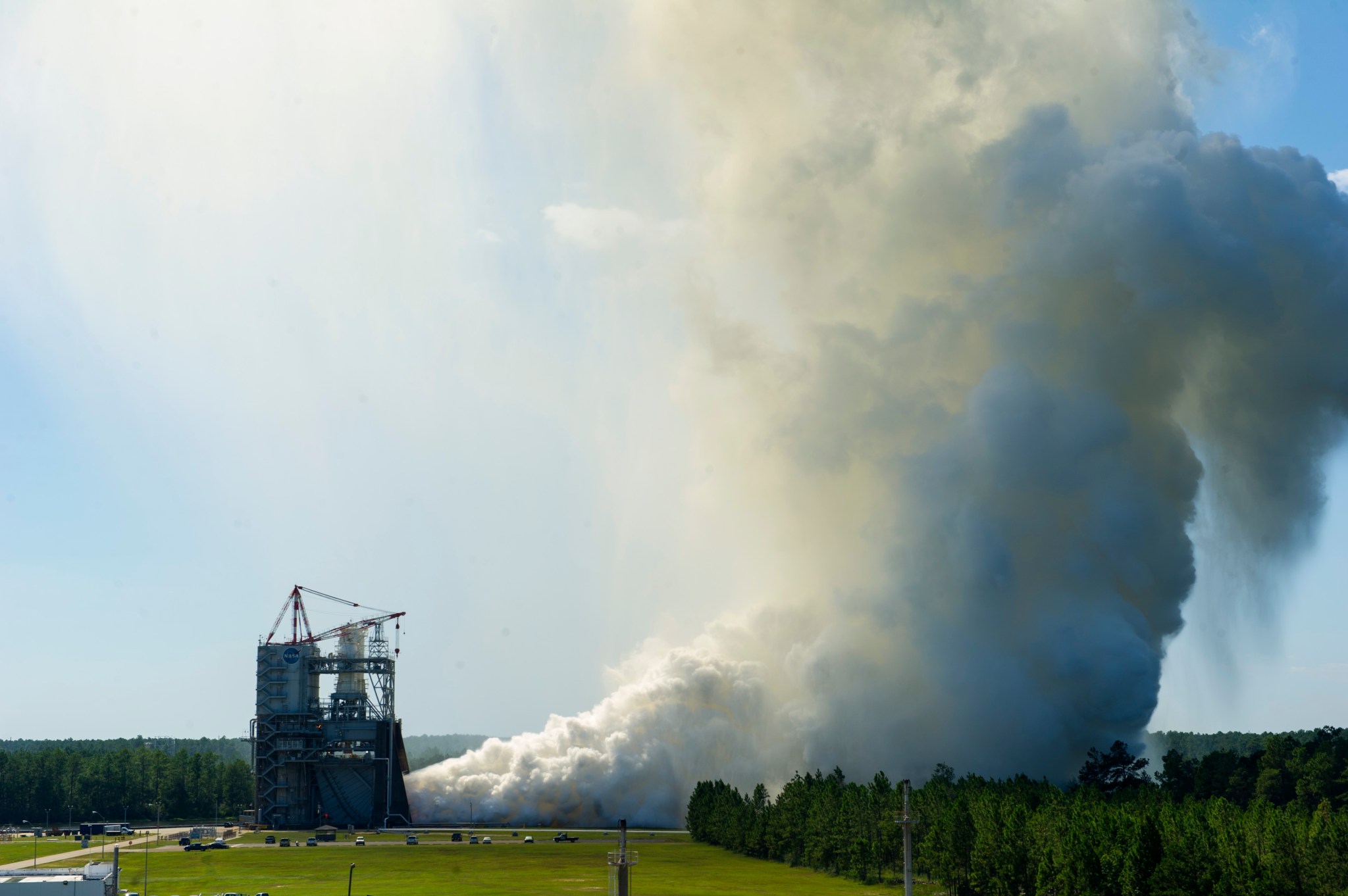
Four RS-25 engines will help power the SLS core stage during launch. Firing simultaneously at 109 percent of its operating level, the engines will provide approximately 2 million pounds of thrust and operate in conjunction with a pair of five-segment solid rocket boosters for a total of 8.4 million pounds of thrust to lift the initial 70 metric ton (77-ton) SLS off the launch pad. The SLS eventually will evolve to a 130 metric-ton (143-ton) configuration that will enable missions to such deep-space destinations as an asteroid and ultimately Mars.
This test series used the developmental engines to validate the new engine controller and the engine performance at the higher thrust level before testing the actual flight engines. The RS-25 engines that will be used on the initial SLS missions are flight engines remaining from the Space Shuttle Program. These are among the most tested engines in the world but will undergo additional testing to prove them flightworthy when operated at the higher performance levels needed for SLS.
Testing of RS-25 flight engines for those initial missions will begin at Stennis this fall. “What a great time to be at Stennis,” said Rick Gilbrech, director of Stennis. “When it comes to powering the future of the deep-space exploration program for this country, this is the front line, where we enable those missions to fly.”
The recently concluded series of developmental tests began with a Jan. 9 hot fire. Development engine testing resumed in May after scheduled work was completed on the high-pressure industrial water system that provides the thousands upon thousands of gallons of water needed during an engine test. Aerojet Rocketdyne of Sacramento, California, is the prime contractor for the RS-25 engine work.
“This was a great test series for Stennis,” said Ronnie Rigney, RS-25 project manager at Stennis. “Our teams built up a lot of history with space shuttle main engines and were able to use that expertise to meet very challenging test specifications for the RS-25. The testing done here will help ensure the engines perform as needed during actual SLS missions.”
In addition to testing RS-25 flight engines, Stennis operators will employ their collective expertise to test the SLS core stage. The B-2 Test Stand at Stennis is being renovated now to conduct tests on the SLS flight core stage prior to its first uncrewed mission. That testing will involve installing the flight stage on the stand and firing its four RS-25 engines simultaneously, just as during an actual launch.
New Structural Test Stand for SLS Begins Rise at Marshall
By Kenneth Kesner
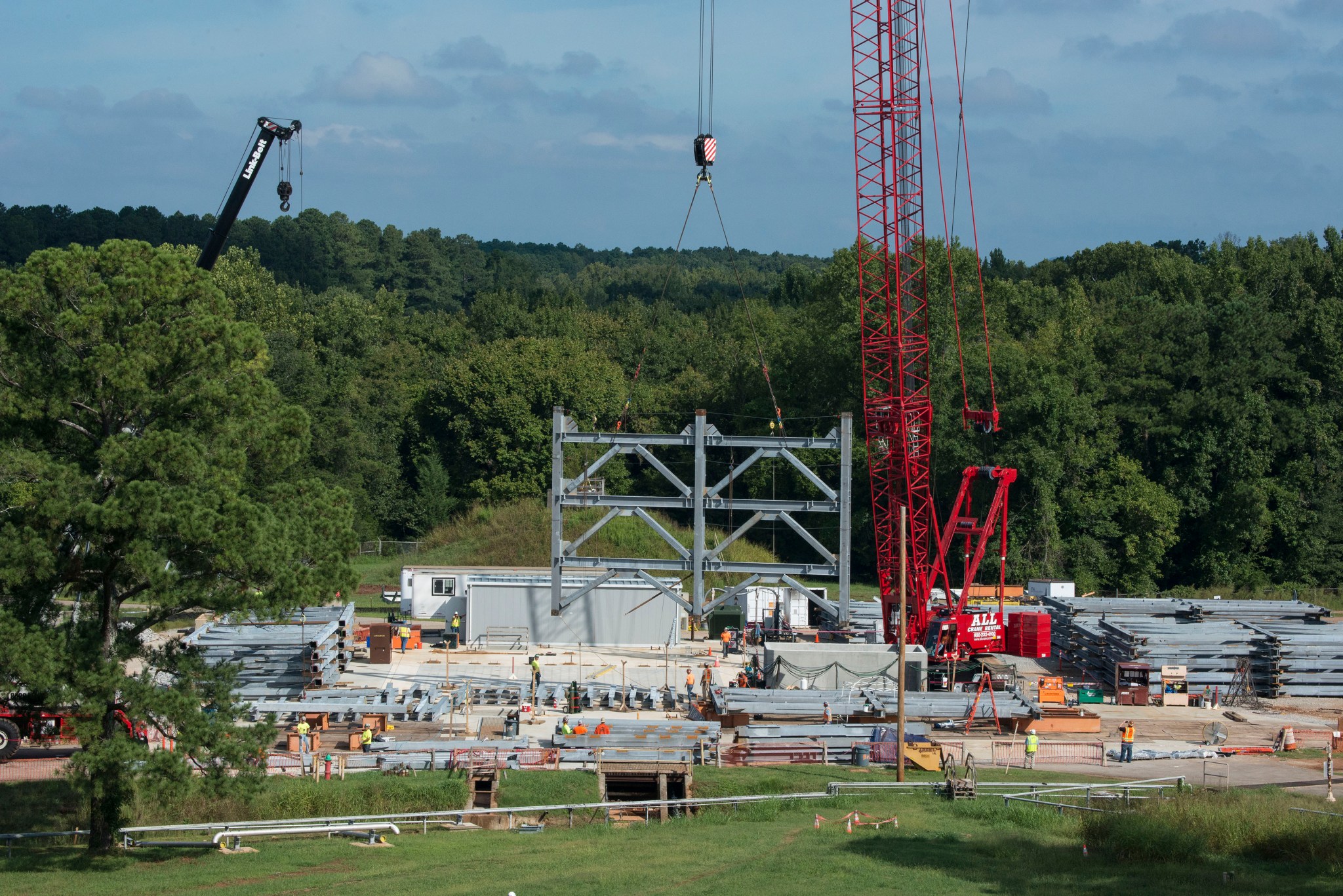
The first major steel piece of a new structural test stand for the liquid hydrogen tank of the Space Launch System’s massive core stage was welded to the foundation Aug. 31 at NASA’s Marshall Space Flight Center.
When construction is completed in the summer of 2016, the twin towers of Test Stand 4693 will rise 215 feet, or about 23 stories, adding another distinctive feature to Marshall’s skyline. The stand will subject the tank, which is 185 feet tall, to the same pressure loads and conditions it will experience at launch. The stand is being built in Marshall’s West Test Area on the foundation of the stand where the Saturn V F-1 rocket engine was tested in the 1960s.
“It seems fitting that the same ground on which NASA tested the technology that took astronauts to the moon will be used to test the tanks and hardware that will launch a new generation of explorers,” said Tim Flores, integration manager of the Stages Element in the SLS Program Office. “The stand will change the horizon at Marshall and is a visible sign of the progress on SLS and the journey to Mars.”
SLS will be the most powerful rocket ever built, able to carry astronauts in NASA’s Orion spacecraft on missions into deep space. The 213-foot-tall, 27.6-foot-diameter core stage will have the largest cryogenic fuel tanks ever used on a rocket, feeding four RS-25 engines.
Development of the first exploration-class vehicle since the Saturn V required the development of a new test stand, involving engineers and managers across the spectrum of Marshall organizations — Center Operations, the Engineering Directorate, SLS Program Office and others.
“It’s been heartening to see these teams working together on the test stand as they do on other elements of the program,” said Ricky Wilbanks, element discipline lead engineer for SLS core stage testing in Marshall’s Test Laboratory. “This stand is a critical step in the development of SLS.”
At the site of Test Stand 4693, welders work under tents to shield them from the sun, piecing together rectangular tube-steel sections into frames or “bents.” Each bent is a three-story element of the test stand. A crane then lifts the pre-assembled frames into position, stacking them so they can be welded into place. “It looks like a giant Erector set,” said Phil Hendrix, Marshall project manager for the liquid hydrogen test stand.
One side of a tower’s framework is braced, then the other side, and then they are outfitted with infrastructure such as flooring and stairs. The process greatly reduces the amount of welding and construction that must be done far above the ground.
Another open-steel framework will connect the test stand’s two towers across the top — it’s being called the “roof,” Hendrix said. A “crosshead” beneath the roof has been designed so that it can be lowered and raised between the two towers, allowing special test equipment to be more easily installed and changed. The movable crosshead will also allow the stand to accommodate future tests of different sizes of tanks and equipment in addition to the core stage liquid hydrogen tank.
“The tolerances on this project are much tighter than with typical steel construction because the crosshead has to move up and down between the two towers,” Hendrix said.
Hydraulic cylinders will push, pull and bend the tank to simulate launch stresses. Engineers will also apply pressure loads to the tank, which will be partially filled with nitrogen during tests, instead of more-volatile liquid hydrogen.
Many of the same techniques will also be used to build an 85-foot-tall, L-shaped stand for structural testing of the SLS core stage’s liquid oxygen tank and hardware, also in the West Test Area. NASA contracted for the construction of the test stands through the U.S. Army Corps of Engineers, which awarded the contract to Brasfield & Gorrie of Birmingham, Alabama.
Hendrix said it’s easy to get caught up in dealing with the day-to-day difficulties inherent in any major construction project. But seeing the test stand begin to take shape brings home again the enormity of the goal and the SLS program.
“Anything of this nature, for exploration, it’s new, it’s hard,” he said. “When you get the chance to step back and really consider the big picture, how important this is, it’s awe inspiring. When SLS launches, it’s going to be an important day for the country.”
Kesner, an ASRC Federal/Analytical Services employee, supports the Office of Strategic Analysis & Communications.
Marshall Team Designs and Tests First NASA 3-D Printed Turbopump
One of the most complex, 3-D printed rocket engine parts ever made, a turbopump, got its “heartbeat” racing at more than 90,000 revolutions per minute during a successful series of tests with liquid hydrogen propellant at NASA’s Marshall Space Flight Center.
“The Marshall engineering team’s ability to design, assemble and test rocket engine parts, as well as perform manufacturing tasks, has made it possible to build a 3-D printed liquid propulsion system in a timely and affordable manner,” said Mary Beth Koelbl, manager of Marshall’s Propulsion Systems Department.
Additive manufacturing, or 3-D printing, is a key technology for enhancing space vehicle designs and enabling affordable missions to Mars. The turbopump, a critical rocket engine component, features a turbine that spins and generates more than 2,000 horsepower — twice the horsepower of a NASCAR engine. The fuel pump design proved to be hardy with three tests reaching full power. The turbopump delivered 1,200 gallons of liquid hydrogen per minute, enough cryogenic liquid hydrogen to power an upper stage rocket engine capable of generating 35,000 pounds of thrust.
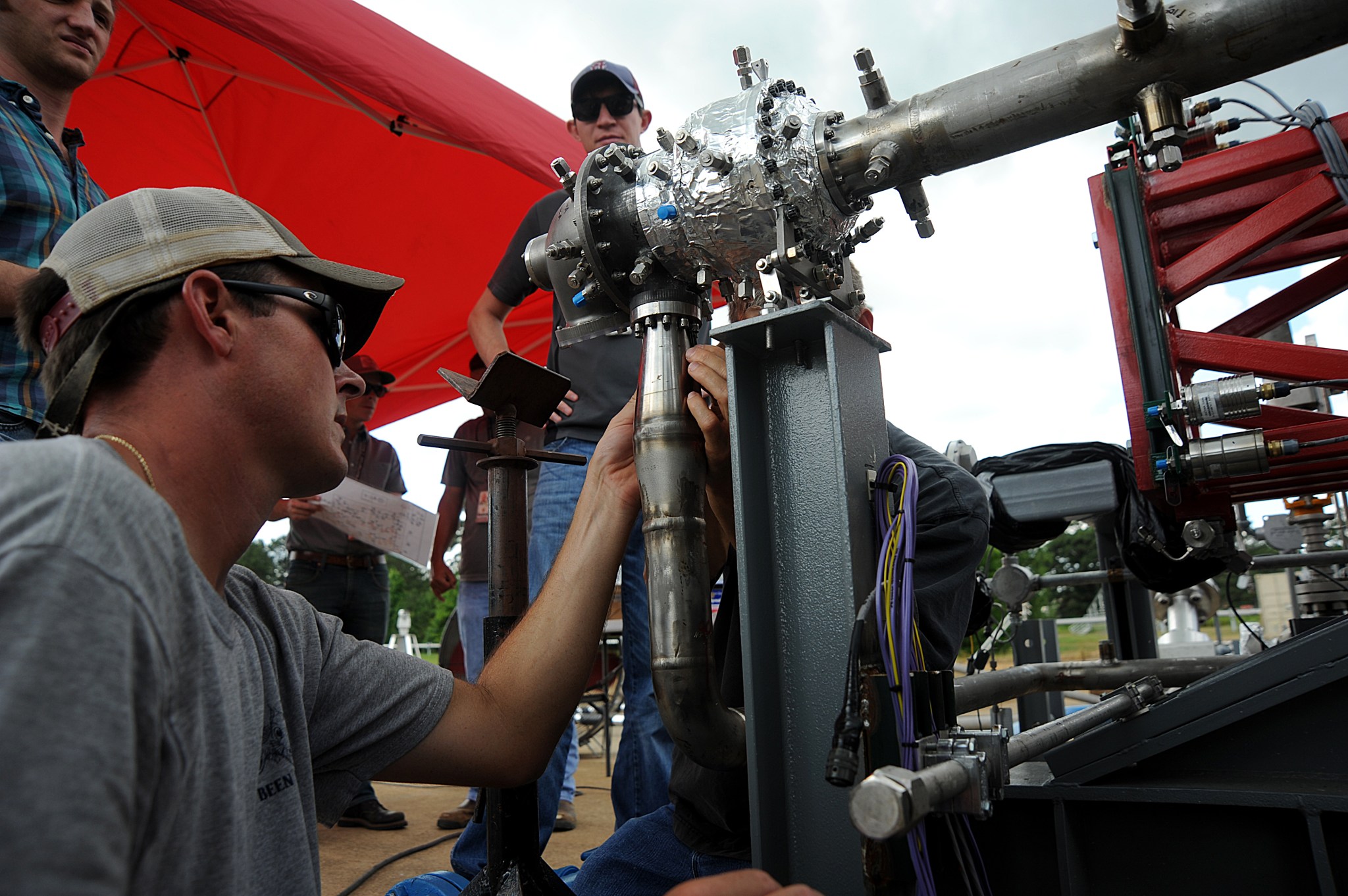
“The test series went really well,” said Marshall test conductor Ryan Wall. “We completed our three primary test objectives through 15 separate tests to ensure the hardware performed the way it was designed to operate inside a rocket engine. These tests and others have given us the confidence to move forward with testing a breadboard demonstrator engine made almost entirely of 3-D printed parts.”
The 3-D printed turbopump has 45 percent fewer parts than pumps manufactured with traditional welding and assembly techniques. Marshall engineers designed the fuel pump and its components and leveraged the expertise of four suppliers to build the parts using 3-D printing processes. To make each part, a design is entered into a 3-D printer’s computer. The printer then builds each part by layering metal powder and fusing it together with a laser — a process known as selective laser melting.
“Our team had a goal to design and test the fuel pump in two years,” said Nick Case, a propulsion engineer and systems lead for the fuel turbopump work. “If we used traditional manufacturing processes, it would have taken us double that time. Using a completely new manufacturing technique has allowed us to push the limit of what we’ve been taught in engineering. We are designing engines in a whole new way.”
During the tests, the 3-D printed turbopump was exposed to extreme environments experienced inside a rocket engine. Testing helps ensure 3-D printed parts operate successfully under harsh conditions. Test data are available to American companies working to reduce uncertainties and drive down the cost of using this new manufacturing process to build parts that meet aerospace standards.
“This development has given the next generation of engineers, like myself, real experience in designing and building rocket engine components for an engine system that operates under conditions similar to those experienced during launch and spaceflight,” said Marty Calvert, Marshall’s design lead for the turbopump.”
The Marshall team is in the process of assembling and preparing for upcoming tests of the additively manufactured demonstrator engine.
Hurricane Katrina Remembrance Ceremony Held at Michoud
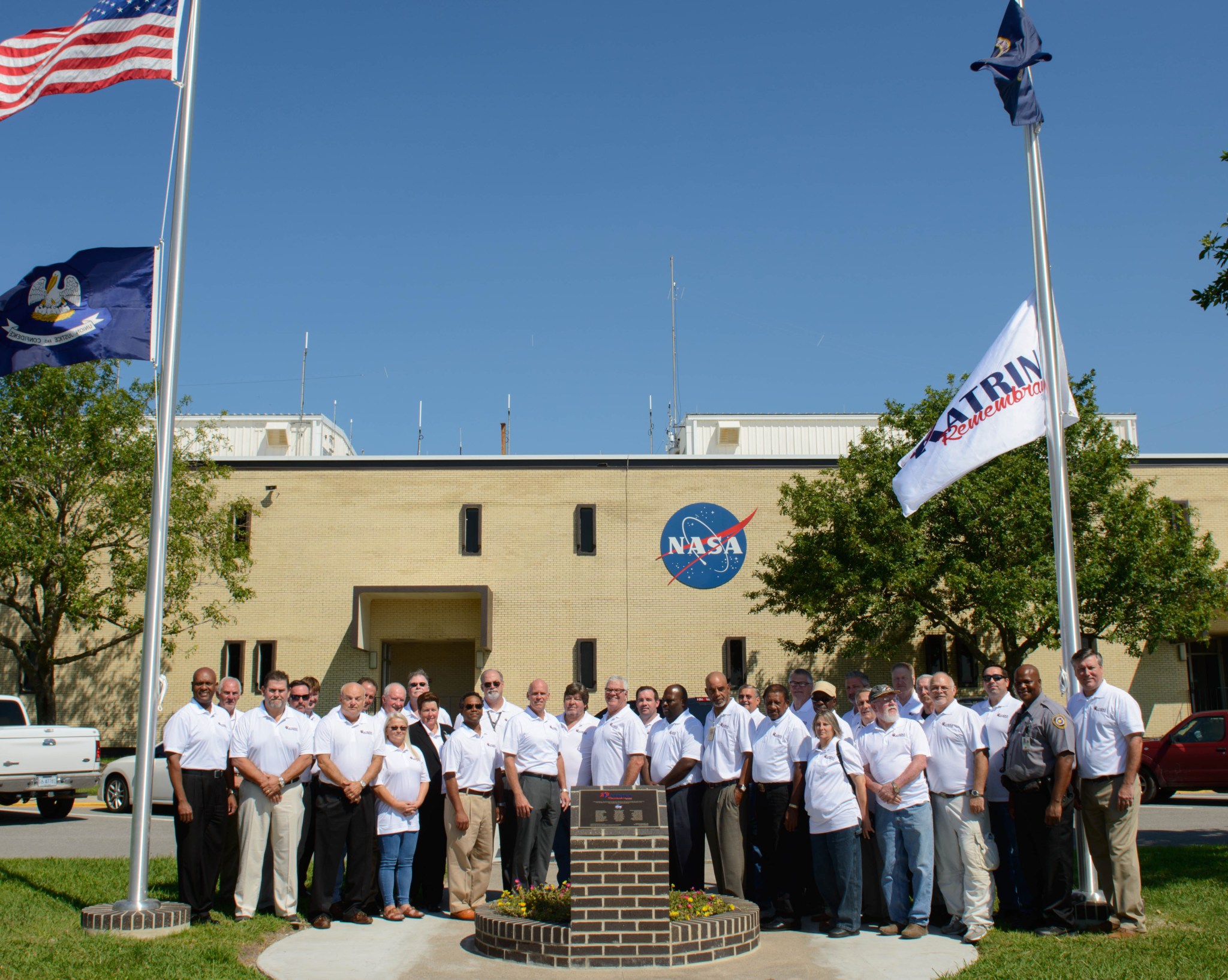
NASA, USAID Open New SERVIR Environmental Monitoring Hub in Southeast Asia
On Aug. 31, NASA and the U.S. Agency for International Development launched SERVIR-Mekong, a joint project to strengthen regional environmental monitoring in five countries in the lower Mekong region of Southeast Asia.
One of three hubs now operating in developing regions of the world, the new SERVIR facility is housed at the Asian Disaster Preparedness Center in Bangkok, Thailand, and joins a growing global community of scientists and decision-makers using publicly available data from space assets to address critical regional issues.
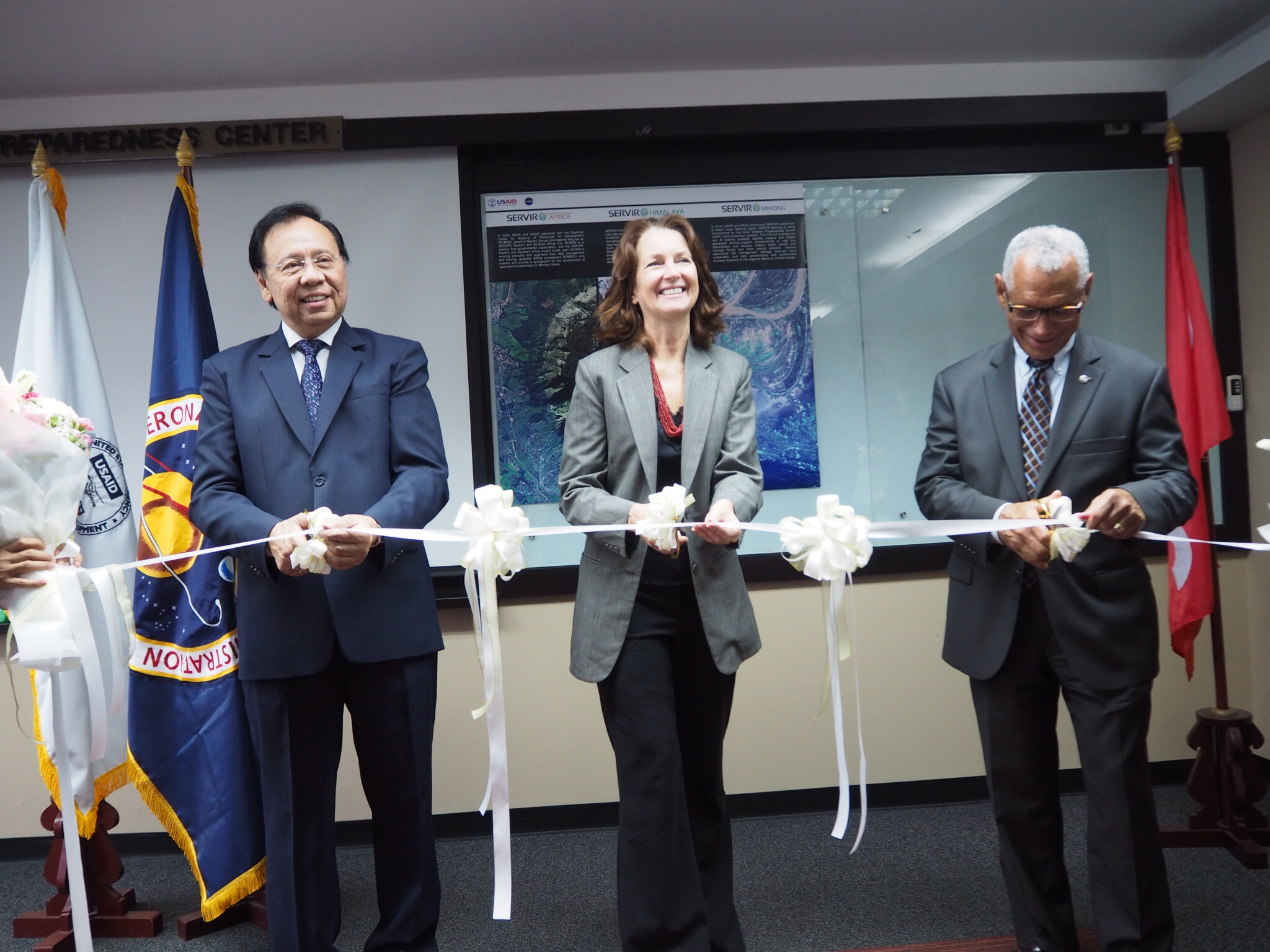
“Today, NASA demonstrates the human impact of its science mission here on Earth and our commitment to protecting the resources, the environment and most of all the millions of people living, working and raising new generations of pioneers and innovators across the region,” said NASA Administrator Charles Bolden, who took part in the facility’s official opening along with NASA Chief Scientist Ellen Stofan.
Named for a Spanish term meaning “to serve,” SERVIR was developed in 2005 by researchers at NASA’s Marshall Space Flight Center, which continues to house the SERVIR Coordination Office. Researchers draw on a continuous stream of space-based climate, weather and other Earth observation data from NASA and its partners, sharing timely information with governments and researchers — in the case of SERVIR-Mekong, in Burma, Cambodia, Laos, Thailand and Vietnam — and addressing issues such as water management, land use planning, disaster risk reduction and management of natural resources.
The SERVIR program helps governments and development stakeholders incorporate Earth observations and geospatial technologies into natural disaster response, improve food security, safeguard human health, and manage water and natural resources. Hubs in each region focus on issues and needs most critical to local populations.
“Under SERVIR-Mekong, we are tapping into the best available science and technology to help protect this region’s vital ecosystems and the benefits they provide to society,” said Beth Paige, director of USAID’s Regional Development Mission for Asia. “Already, Asian scientists, NASA scientists and others are beginning to develop tools to build resilience and contribute to tackling some of the region’s most pressing challenges.”
Partnering with NASA and USAID, as part of the SERVIR-Mekong consortium, are the Asian Disaster Preparedness Center; Deltares, headquartered in Delft, The Netherlands; the Stockholm Environment Institute in Sweden; and the Spatial Informatics Group of Pleasanton, California. SERVIR global demand support is provided by Development Alternatives Incorporated, headquartered in Bethesda, Maryland.
SERVIR was developed in coordination with the Group on Earth Observations, an alliance of more than 90 nations and organizations collaborating to build a global Earth-observing system to benefit society’s needs. NASA, USAID and their partners operate SERVIR hubs in Kathmandu, Nepal, serving the Hindu-Kush-Himalaya region, and in Nairobi, Kenya, serving Eastern and Southern Africa. The first hub, launched in Panama in 2005, served the Mesoamerican region and the Dominican Republic.
SERVIR is operated by the Earth Science Division‘s Applied Sciences Program in NASA’s Science Mission Directorate. Marshall collaborates with four other NASA field centers on SERVIR: Goddard Space Flight Center, the Jet Propulsion Laboratory, Ames Research Center and Langley Research Center.
Marshall’s Dan Irwin, SERVIR Developer, Uses Space Data — and Playgrounds — to Change the World
By Rick Smith
Ten years on, NASA researcher Daniel Irwin — developer of the joint NASA-USAID SERVIR environmental monitoring program at NASA’s Marshall Space Flight Center — remains a man of two realms. He’s committed to Earth, but his defining work relies on technology in space.
A decade ago, Irwin had just begun turning SERVIR — its name drawn from a Spanish word meaning “to serve” — into a network of scientists using Earth-observation satellites to identify impacts from climate or environmental conditions such as flooding, deforestation, wildfires, drought and other long-term hazards. This information could be shared in real time with governments and stakeholders throughout affected regions, enabling them to prepare for and limit the impact of disasters in the making, or rapidly respond to those already in progress.
Today, Irwin’s job as director of the SERVIR Coordination Office has gone global. A joint initiative of NASA, the U.S. Agency for International Development and partners around the world, SERVIR strengthens the ability of governments and organizations to use Earth observations and geospatial technologies to respond to natural disasters, protect food and water supplies, safeguard human health and protect other natural resources.
On Aug. 31, NASA, USAID and the Asian Disaster Preparedness Center in Bangkok, Thailand, officially launched the SERVIR-Mekong hub, serving five Mekong River Basin countries: Burma, Cambodia, Laos, Thailand and Vietnam. Other SERVIR hubs in the International Centre for Integrated Mountain Development in Kathmandu, Nepal, and the Regional Center for Mapping of Resources for Development in Nairobi, Kenya, support the Hindu-Kush-Himalaya region and eastern and southern Africa, respectively. The first SERVIR hub, launched in 2005, served the Mesoamerican region.
Irwin is excited to bring SERVIR to Southeast Asia. “We anticipate benefits on a scale we could only imagine 10 or 20 years ago,” he said. “That’s the result of our growing global partnership, and I could not be prouder that NASA, USAID and our incredible regional partners are pioneering this effort.”
From space to playgrounds
When he’s not focused on bettering the world one region at a time, Irwin seeks to improve lives on a much more personal scale. In 1993, when he first visited Guatemala to map local forests for a conservation organization, he fell in love with the rural village of San Andrés — and with local resident Julieta Puga, now his wife of 19 years and mother of Irwin’s two daughters.
Returning often to San Andrés over the years, Irwin was struck by the lack of resources for its 2,000 or more children. In 1999, armed with donations and a grant from a non-profit firm, he and his partners built San Andrés a library. They added a cultural center in 2001. But something was still missing. Pondering the village’s ancient, derelict playground, years in ruin, it occurred to him that an entire generation of children was growing up without a place to play.
So in 2004, Irwin raised funds again to design and build the massive Carlos Soza Manzanero Community Playground. Named for a mentor of Irwin’s who died of cancer in 2003, the playground serves more than 3,000 kids from San Andrés and nearby communities. It’s getting a complete refurbishment and expansion this year.
“I realized from that first project that this — helping communities — was what I want to do for the rest of my life,” he said. “That’s what keeps me connected, what keeps me grounded.”
Never content to rest on his laurels, he ticks off future SERVIR goals: increased hub-to-hub exchange; continued work with USAID and other partners to open new hubs, expanding the network into a truly global monitoring system; and greater cooperation with government and non-government organizations, embracing the needs and capabilities of each.
Irwin’s ready for the challenges. Ready to keep doing work he believes in. And when he can, he’ll go back to Guatemala, too, hammer in hand. Ready to keep doing work he loves.
Read his full story here.
Smith, an ASRC Federal/Analytical Services employee, supports the Office of Strategic Analysis & Communications.
Small Business Forum Held at Michoud

Mission Success Is in Our Hands: Q&A with Carla Shackelford, System Safety Engineer
Carla Shackelford, system safety engineer with Bastion Technologies, supporting the Safety & Mission Assurance Directorate at NASA’s Marshall Space Flight Center, recently talked with Marshall Public Affairs Officer Molly Porter about “Mission Success Is in Our Hands,” an initiative underway at Marshall to strengthen team members’ commitment to mission assurance and flight safety.
Years at Marshall: I have been supporting the Safety & Mission Assurance Directorate for seven years, going back to 2006. Prior to joining Marshall, I spent six years at NASA’s Johnson Space Center, plus two years with the Department of Defense.
What are the key responsibilities of your current job?
I am a subject matter expert and mentor for Space Launch System safety integration. I manage the integrated hazard analysis for SLS while mentoring the members of the team. I work with the cross program integration team within the Exploration Systems Development Division and SLS chief safety officers.
How does your work support the safety and success of NASA and Marshall missions?
The development of the SLS hazard analysis is a key step in the certification of SLS and is one of the opportunities to influence the safety of the vehicle for human spaceflight.
What does “Mission Success Is In Our Hands” mean to you?
Each one of us adds value and can influence the process. Together we can succeed.
Do you have a story or personal experience to share that can help others understand the significance of mission assurance and flight safety? What did you learn from it?
I have always worked on flight and payload development programs and I have learned over time it’s never too late to think safety. My career has taught me that incorporating safety as an integral part of the design process is critical to program success. It always benefits us to address the issues early on when safety can be incorporated into the design instead of as an afterthought. The impacts of implementing safety in the early stages of the design cycle are huge in preventing cost increases and schedule delays to any project or program and in ensuring the safety of the crew.
Leading others takes courage. Knowing the right decision is usually easy. Making the right decision is hard.
How can we work together better to achieve mission success?
We can welcome opportunities to talk with fellow colleagues to build rapport and learn from each other’s experiences.
This Week in NASA History: Von Braun Welcomes Astronauts to Marshall — Sept. 1, 1962
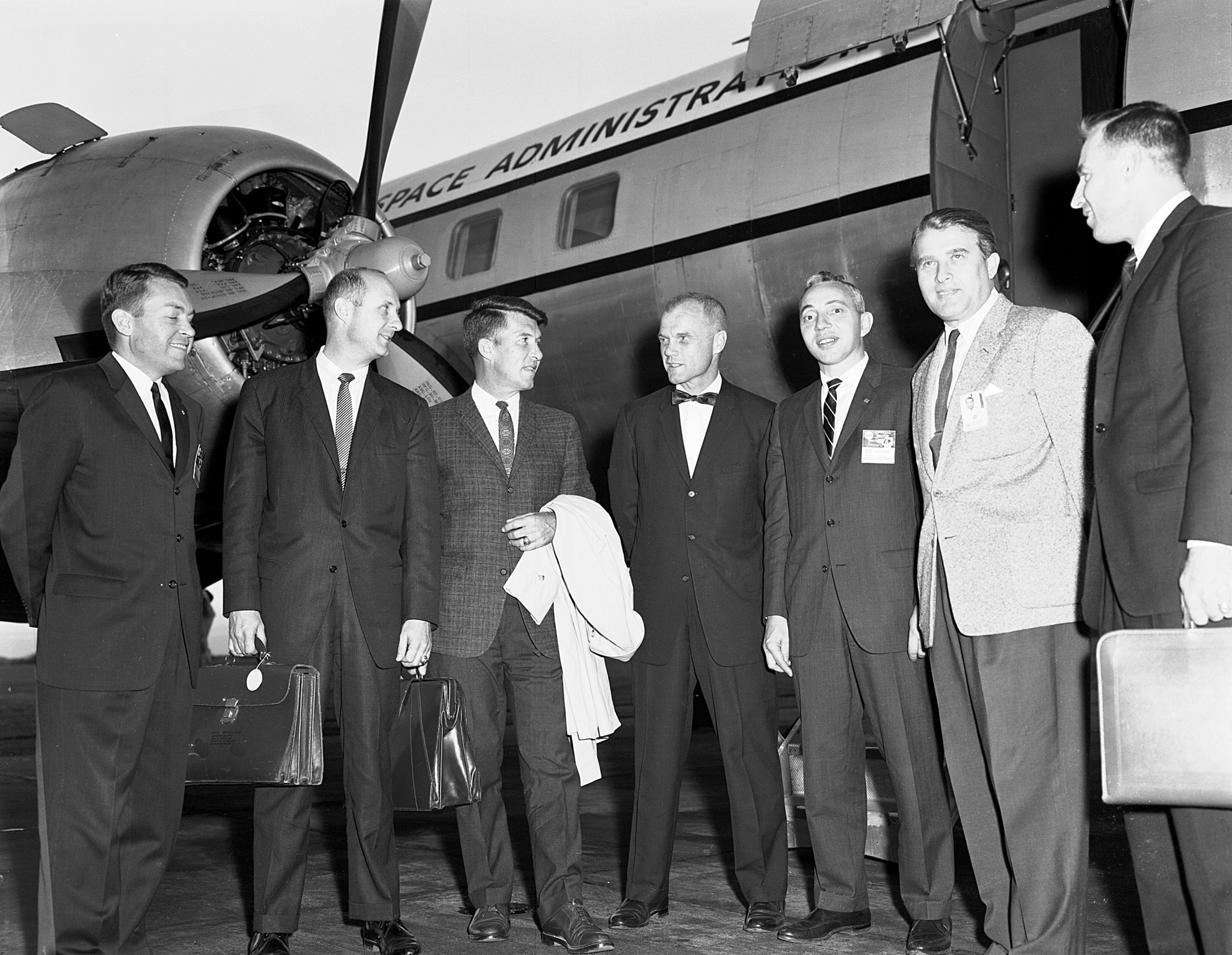
This week in 1962, NASA Marshall Space Flight Center Director Dr. Wernher von Braun met with five astronauts and Brainerd Holmes, NASA associate administrator for Manned Space Flight, at Marshall. From left are Elliot See, Tom Stafford, Wally Schirra, John Glenn, Holmes, von Braun and Jim Lovell. NASA officials and astronauts often traveled to Marshall to meet with von Braun. The NASA History Program documents and preserves NASA’s remarkable history through a variety of products — photos, press kits, press releases, mission transcripts and administrators’ speeches. For more pictures like this one and to connect to NASA’s history, visit the History Program’s Web page.