In This Week’s Star
- Marshall Engineers Test Combustion Chamber to Advance 3-D Printed Rocket Engine Design
- Major Assembly Complete on System that will Pack a Powerful Push for Orion
- Expedition 48/49 Crew Meets with Marshall Flight Controllers for Post-mission Debrief
- As 2016 Comes to a Close, Marshall Team’s CFC Goal within Reach
- Leadership Class Gets Inside View of Arsenal Agencies as Official Redstone Arsenal App is Created
- This Week in NASA History: First American-built International Space Station Module Launches — Dec. 15, 1998
Marshall Engineers Test Combustion Chamber to Advance 3-D Printed Rocket Engine Design
Recent tests of a developmental rocket engine at NASA’s Marshall Space Flight Center produced all the performance data engineers were hoping for, along with the traditional fire and roar. But this engine is anything but traditional.
Marshall engineers are designing each of the components from scratch to ultimately be made entirely by additive manufacturing, or 3-D printing, methods. The series of 12 test firings in late fall brought them a big step closer to that goal, said Andrew Hanks, test lead for the project. The fuel turbopump, fuel injector, valves and other major engine components used in the tests were 3-D printed, with the exception of the main combustion chamber.
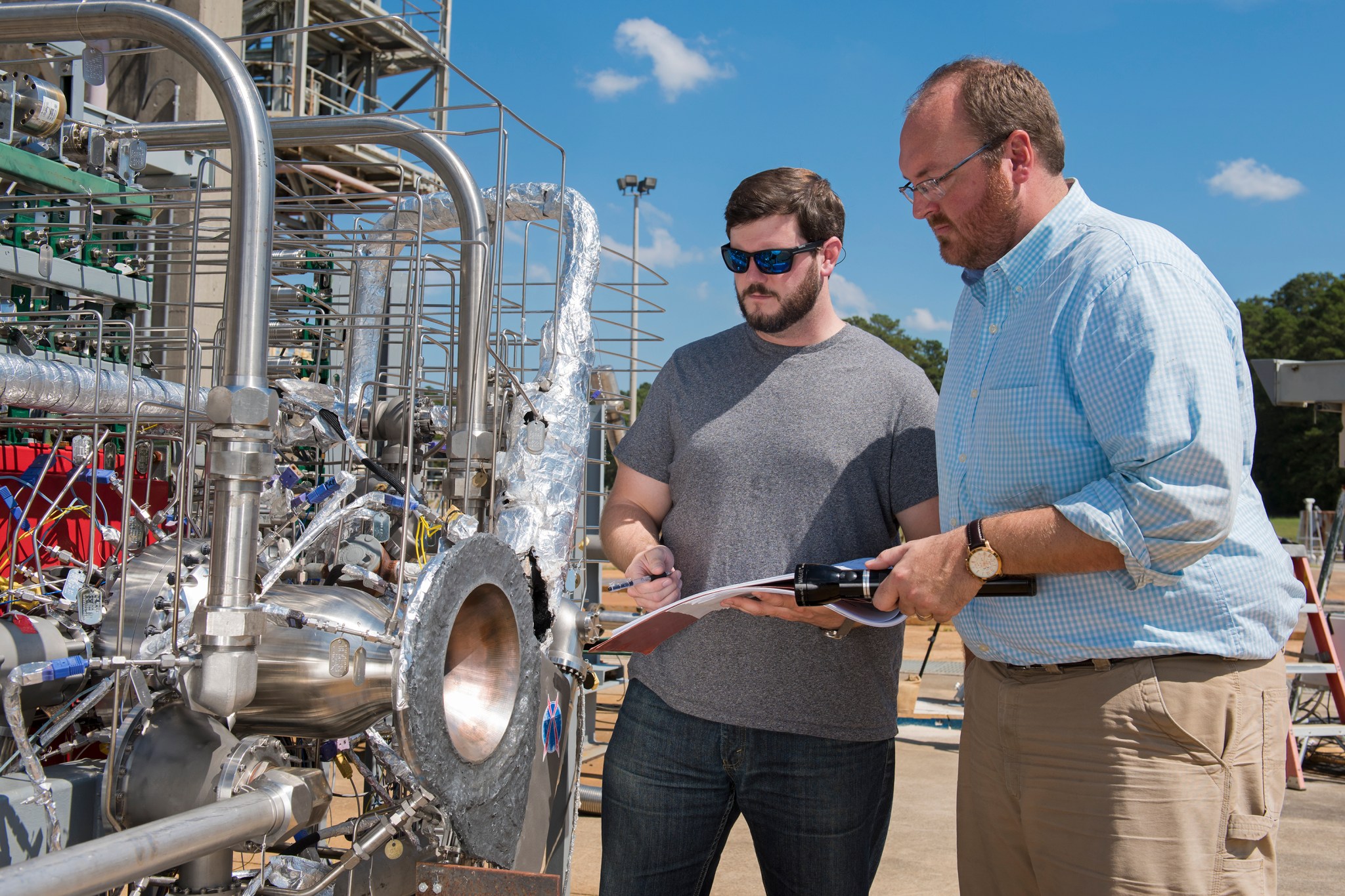
Previous testing of the engine parts used an ablative combustion chamber, which erodes during a burn, changing internal pressures and allowing only a 10-second firing time. The latest tests ran for 30 seconds, giving engineers a more realistic picture of what’s going on inside their developmental engine, which is designed to produce 35,000 pounds of thrust.
The regeneratively cooled main combustion chamber used in the tests was of the Marshall team’s new design, but was machined in a traditional way. That allowed engineers to proceed with testing nearly all the pieces of their demonstrator engine design in place.
“The addition of the main combustion chamber was important because it is a crucial part of an engine system,” said Greg Barnett, team lead for development of the chamber, which involved more than a dozen team members and five contractors. “The data from this hot-fire test series facilitates a higher fidelity estimation of the system performance, which contributes to the optimization of all other component designs.”
Having the chamber in place allowed the team to obtain better data about each of the other components, said Nick Case, the project’s lead system analyst.
“A system is not just a sum of parts put together. It’s a product of the interaction of the parts. What we’re trying to do is understand and manage those interactions,” he said. “At the same time, we must understand the performance of the individual 3-D printed pieces. That’s what this test allowed us to do.”
The project looks more like that sum of parts than any real rocket engine. The chamber, fuel turbopump, valves and other components are spread across a framework of tubing and wires in what engineers call a “breadboard” engine. They’re connected so they work together as they would if packaged for a spacecraft or flight, but the breadboard gives engineers the flexibility to easily make adjustments and changes during development, said Graham Nelson, project manager.
Using additive manufacturing allows the team to more rapidly design and build complex parts that would ordinarily take workers many, many hours to machine and assemble — in many cases designs that cannot even be built using traditional machining. Testing already shows the benefits of designing for additive manufacturing can be realized in a high-performance propulsion environment, Nelson said. The team hopes to test a nearly 100-percent 3-D printed breadboard engine system next year.
The Marshall additive manufactured demonstrator engine project team isn’t working to become an engine manufacturer, but could produce a prototype that informs and influences commercial designs, Hanks said. For more than three years they’ve been working with vendors to manufacture some of the developmental engine’s parts, which is helping to grow a vendor base capable of producing rocket engine parts for industry.
The team continues to evolve the system as new components become available and new needs arise — providing more relevant hot-fire environments at each step. The next major step will be the addition of a 3-D printed oxidizer turbopump to the setup. It is being fabricated as part of a collaborative development with the NASA Space Technology Mission Directorate’s Game Changing Development program, which is also funding the development of a 3-D printed combustion chamber.
Major Assembly Complete on System that will Pack a Powerful Push for Orion
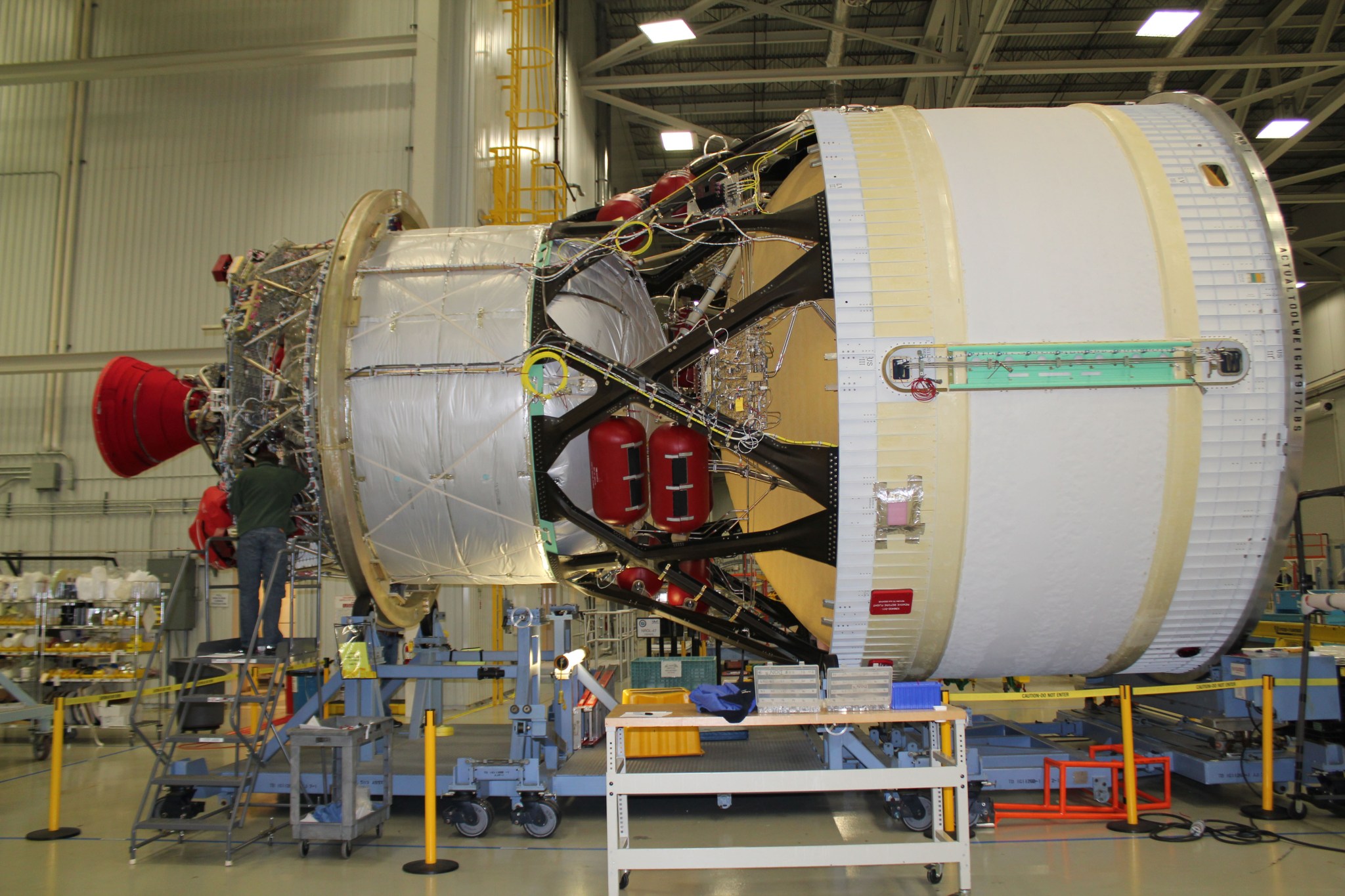
The propulsion system that will give the Orion spacecraft the in-space push needed to travel thousands of miles beyond the moon and back has completed major assembly at United Launch Alliance in Decatur, Alabama. The Boeing-designed interim cryogenic propulsion stage is a liquid oxygen/liquid hydrogen-based system that will give Orion an extra punch of power on the first, uncrewed flight of the spacecraft with NASA’s new rocket, the Space Launch System, in late 2018. The first integrated exploration mission will allow NASA to use the lunar vicinity as a proving ground to test systems farther from Earth, and demonstrate Orion can get to a stable orbit in the area of space near the moon in order to support sending humans to deep space, including the Journey to Mars. With major assembly now complete on the flight hardware, the ICPS has several more steps to go, including avionics installation at the ULA-Decatur factory; barge and road transport to the Delta Operating Center at Cape Canaveral, Florida, for avionics and system-level testing; and delivery to NASA in mid-2017. (ULA)
Expedition 48/49 Crew Meets with Marshall Flight Controllers for Post-mission Debrief
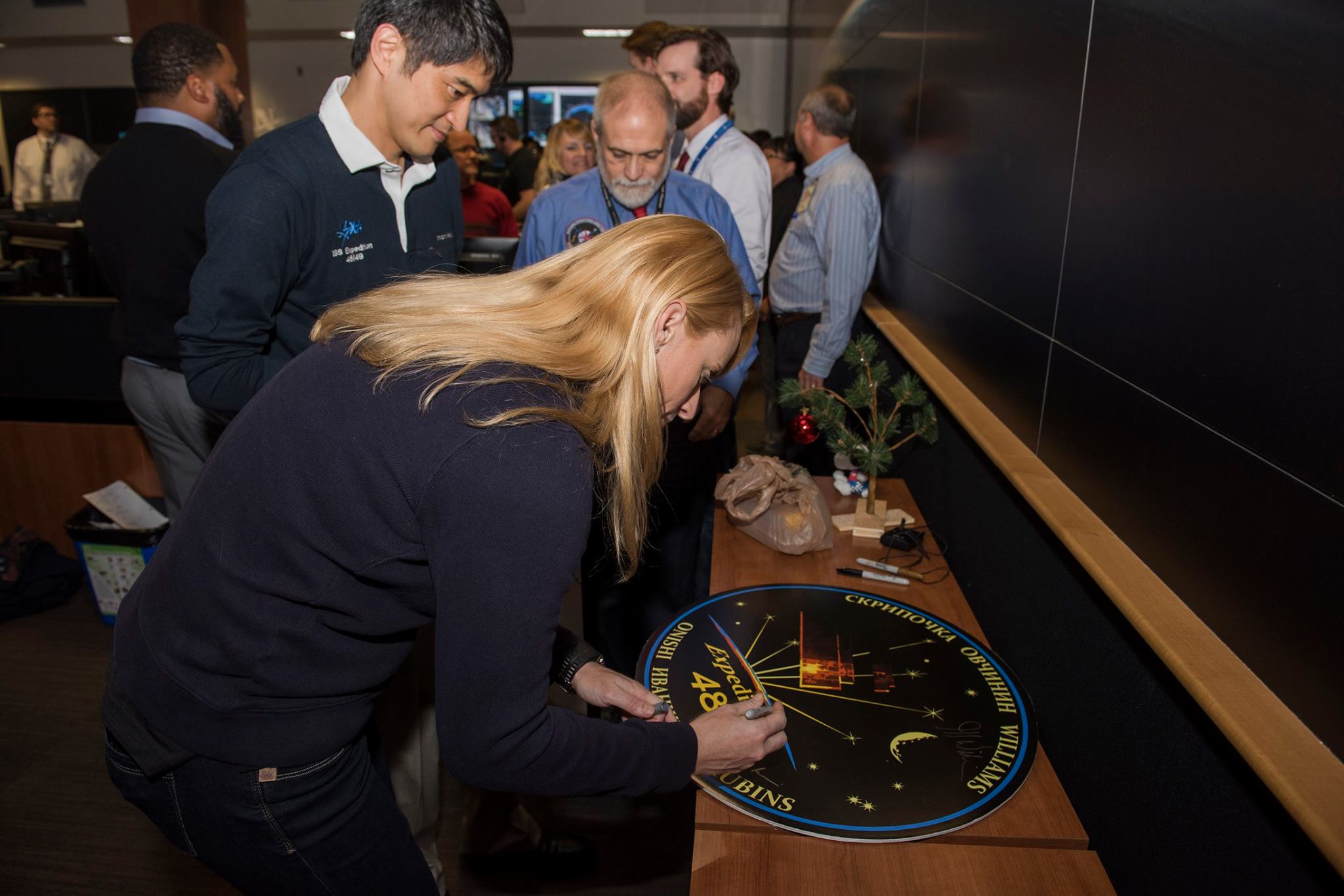
Astronauts Takuya Onishi of the Japan Aerospace Exploration Agency, left, and Kate Rubins of NASA autograph their Expedition 48/49 mission plaque while visiting the Payload Operations Integration Center — mission control for science on the International Space Station — at NASA’s Marshall Space Flight Center. Rubins and Onishi visited the POIC for a mission debrief with the Marshall flight controllers they worked closely with while living and working on the orbiting laboratory earlier this year. They also thanked the entire team for helping accomplish a successful mission. (NASA/MSFC/Charles Beason)
As 2016 Comes to a Close, Marshall Team’s CFC Goal within Reach
With NASA Marshall Space Flight Center’s annual Combined Federal Campaign charity drive coming to a close, the campaign has officially reached nearly 95 percent of the final goal. Donations reached a high last week, and organizers hope a final push could help reach the center’s goal.
The current total raised or pledged is $568,500 of the $600,000 campaign. “We need to close out the campaign very strongly in order to reach our goal,” said Rhoney Triplett, Marshall’s CFC Chairperson. “If we raise approximately $31,500 we will achieve our goal.”
CFC organizers are asking all Marshall team members to remember those less fortunate during this holiday season by visiting the CFC page on ExplorNet to learn how to help the many charities in need.
Leadership Class Gets Inside View of Arsenal Agencies as Official Redstone Arsenal App is Created
By Kenneth Kesner
As members of Team Redstone, everyone at NASA’s Marshall Space Flight Center sometimes needs up-to-date information about the arsenal traffic at the gates, directions to an Army or an agency’s building, or to know where you can grab a bite to eat on post. All that and more can now be found at the touch of a smartphone or tablet with Redstone Arsenal’s official app, “Redstone Explorer,” available from the Apple App Store and Google Play.
Redstone Explorer includes regular updates of arsenal news and announcements, with the option of pushing news alerts to devices. It also features phone numbers and links to websites about the dozens of Department of Defense commands and organizations on the arsenal, and those of the many federal agencies such as NASA and the FBI; recreational resources; maps; and links to Team Redstone social media platforms.
The app will be maintained as a one-stop-shop for official information about the arsenal, said Markeeva Morgan, Space Launch System Core Stage Avionics Hardware manager at Marshall. He is also a member of the most recent class of the Army’s Advanced Leadership Investment for Tomorrow, or AdvLIFT, program, which developed Redstone Explorer as a class project over just nine months.
“We’re pretty proud of it. We did this and we were doing our day jobs,” Morgan said, smiling. “It was challenging, but we committed to releasing a fully functional, complete app before we graduated, not just software code or a proof of concept that the next class could take on and finish.”
The LIFT program, begun in 2005, has three courses that are open competitively to civil servants in any agency at Redstone Arsenal. The Upward Leadership Investment for Tomorrow, or UPLIFT, course is for GS11 and below and equivalents; the Intermediate or iLIFT course for GS 12-13s and equivalents; and the Advanced or AdvLIFT course for GS 14-15s and equivalents.
The 2016 graduation ceremonies for LIFT on Dec. 13 recognized 64 participants from 13 organizations and agencies including Marshall, the Army Materiel Command, Redstone Test Center, Missile and Space Intelligence Center and Missile Defense Agency.
Morgan learned about LIFT when he served as a mentor to someone in an UPLIFT course. He believes the development training offered by NASA is second to none, and was intrigued by LIFT’s inter-agency approach and the opportunity to learn about values involved in leadership and teaming from the perspective of the Army and many of the federal organizations on the arsenal.
“It was fascinating to me to be in a leadership program that cross-pollinated cultures across the arsenal,” Morgan said. As the class was working to obtain the approvals needed for the Redstone Explorer app, to get Garrison Commander Col. Tom Holliday’s support, to gather the information needed by the Aviation and Missile Research, Development and Engineering Center’s Army Game Studio as it designed the app, Morgan and the others learned about their respective agencies and developed contacts that could aid mutual assistance or potential partnerships.
LIFT is helping prepare future leaders who can better serve their organizations because they have a better understanding of the workings of Team Redstone, of the needs and strengths of neighboring agencies, said Larry Mack, deputy director of the Marshall Office of Human Capital. In recent years, there have been concerted efforts to work together for the benefit of all.
“There are things that we all have in common,” he said. “We find that it’s very important for us to leverage one another as resources. If something impacts the arsenal, it will impact Marshall and the other organizations.”
For information about participating in the LIFT program, contact Mack in the Office of Human Capital at larry.k.mack@nasa.gov or 256-544-2723.
Kesner, an ASRC Federal/Analytical Services employee, supports the Office of Strategic Analysis & Communications.
This Week in NASA History: First American-built International Space Station Module Launches — Dec. 15, 1998
This week in 1998, STS-88 touched down at NASA‘s Kennedy Space Center after an 11-day mission that delivered the first American–built module to begin construction of the International Space Station. Here, astronauts Jerry Ross and James Newman work together on the final of the mission‘s three spacewalks to connect the Unity module to the Russian Zarya module. These two pieces of the space station had never been in the same hemisphere, but they were mated together perfectly. The Unity module, the first of the three connecting nodes, was built at NASA‘s Marshall Space Flight Center. The space station is a blueprint for global cooperation and scientific advancements, a destination for growing a commercial marketplace in low–Earth orbit, and a test bed for demonstrating new technologies. The orbiting laboratory is the springboard to NASA’s next great leap in exploration, including future missions to an asteroid and Mars. The NASA History Program is responsible for generating, disseminating, and preserving NASA’s remarkable history and providing a comprehensive understanding of the institutional, cultural, social, political, economic, technological, and scientific aspects of NASA’s activities in aeronautics and space. For more pictures like this one and to connect to NASA’s history, visit the History Program’s webpage. (NASA)