In This Week’s Star
- NASA Deep-Space Exploration Systems Look Ahead to Action-Packed 2018
- NASA Tests 3-D Printed Rocket Part to Reduce Future SLS Engine Costs
- Scientists Take Viewers to the Center of the Milky Way
- Marshall Fosters STEM Education Through CubeSat Class in Tennessee
- This Week in NASA History: STS-72 Lands – Jan. 20, 1996
- Obituaries
NASA Deep-Space Exploration Systems Look Ahead to Action-Packed 2018
By Kaitlin C. Rogers
Engineers preparing NASA’s deep-space exploration systems to support missions to the Moon, Mars and beyond are gearing up for a busy 2018. The agency aims to complete the manufacturing of all the major hardware for the first flight of NASA’s Space Launch System and NASA’s Orion spacecraft, Exploration Mission-1, by the end of the year. Planes, trains, trucks and ships will move across America and over oceans to deliver hardware for assembly and testing of components for the Orion spacecraft and the SLS rocket while teams at NASA’s Kennedy Space Center prepare the Ground Systems infrastructure.
Early in the year, engineers at Kennedy will bolt Orion’s heat shield to the crew module. The heat shield will endure temperatures as high as 5,000 degrees Fahrenheit, half as hot as the surface of the Sun, when Orion returns from its missions near the Moon. Mating the heat shield is a crucial step before the service module arrives from Europe in the middle of the year. Once the powerhouse for the spacecraft arrives, technicians will outfit it for mating with the crew module and stack the elements together, joining propulsion lines, avionics and other connections.
NASA engineers and the U.S. Navy will head out to sea off the coast of California in January to evaluate how they plan to recover Orion after the EM-1 test flight. Testing will continue with remaining qualifications of Orion’s parachutes as well as propulsion system verification for Orion’s European Service Module and evaluations of the Orion test article.
Work is already well underway and will continue for the Orion spacecraft that will carry astronauts on Exploration Mission-2. Workers are welding the primary elements of Orion’s structure at Michoud Assembly Facility and will ship the completed vessel to Kennedy by the end of 2018. At NASA’s Johnson Space Center, engineers will review the life support and crew survival systems, and astronauts and test subjects will continue evaluations of the crew interface.
SLS engineers will move at full throttle to complete rocket hardware that will roar off the launch pad. Michoud will see a surge of activity, as five major structural pieces of SLS come together to form the 212-foot-tall core stage. The four RS-25 engines that will produce two million pounds of thrust upon launch will be attached to the stage. Engineers will ship the integrated hardware on the Pegasus barge to NASA’s Stennis Space Center for the final test in 2019 before launch, called the “green run” test, when all four engines roar to life and drain the core stage tanks of more than 700,000 gallons of propellant in a mere eight minutes. The brains of the rocket, the core stage avionics and flight computers, will complete qualification and functional testing and be readied for the green run.
Solid rocket booster segments made by Orbital ATK in Utah will ride the rails to Kennedy and join booster parts, such as the aft and forward skirts. Two launch adapters made at Marshall will also arrive at Kennedy. Pegasus will take the 30-foot-tall launch vehicle stage adapter, and NASA’s Guppy cargo airplane will carry the Orion stage adapter. The Orion stage adapter not only connects the Orion vehicle to the SLS, but will also be loaded with 13 small satellites.
SLS testing will continue as the core stage structural test articles for the liquid hydrogen tank, intertank, and liquid oxygen tank arrive at Marshall and are loaded into towering test stands to be pushed and pulled to simulate flight. SLS teams will also continue to build core stage components and other rocket parts for Exploration Mission-2 and test engines in support of future missions with crew.
Workers at Kennedy will prepare NASA’s modernized spaceport in Florida for blast off of the rocket and spacecraft. In the spring, the mobile launcher will be rolled out to Launch Pad 39B ahead of a fit check that will verify all physical connections between the launcher and pad systems fit before rolling it into the Vehicle Assembly Building for testing. After testing in the VAB is complete, the mobile launcher will roll back to the pad for several months of full-system testing before updates are completed and teams prepare for crewed missions.
All the work by NASA and its contractors helps set the stage for an even busier 2019, when Orion and SLS will be integrated, tested, and rolled out to the launch pad. That initial test flight of SLS will send Orion beyond where any spacecraft built for humans has ventured. All of this foundational work in 2018 and 2019 will enable NASA’s efforts to build a flexible, reusable and sustainable infrastructure that will last multiple decades and support many complex, deep-space missions.
Rogers, an ASRC Federal/Analytical Services employee, supports the Office of Strategic Analysis & Communications.
NASA Tests 3-D Printed Rocket Part to Reduce Future SLS Engine Costs
By Brian Massey
Engineers successfully hot-fire tested an RS-25 rocket engine with a large 3-D printed part for the first time in December, marking a key step toward reducing costs for future engines that power NASA’s new heavy-lift rocket, the Space Launch System.
During flight, a rocket may experience powerful up-and-down vibrations mainly due to the engines and propellant in the feed lines. This is called the pogo effect and is similar to the up-and-down motion of bouncing on a pogo stick. The 3-D printed part tested, called the pogo accumulator, is a beachball-sized piece of hardware that acts as a shock absorber by regulating liquid oxygen movement in the engine to prevent the vibrations that can destabilize a rocket’s flight.
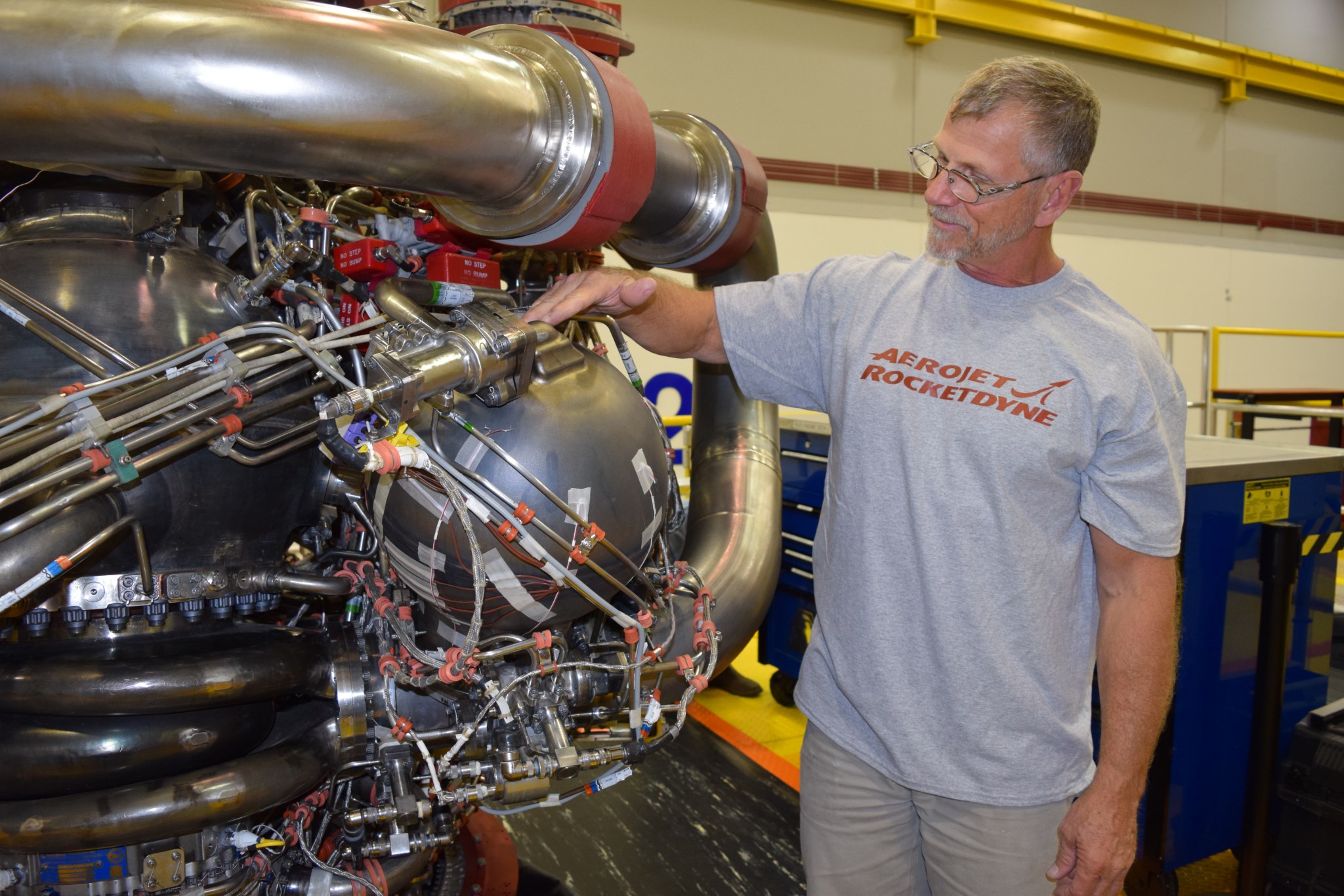
By 3-D printing the pogo accumulator, more than 100 welds were eliminated, reducing costs by nearly 35 percent and production time by more than 80 percent. Initial reports show the 3-D printed hardware performed as expected, opening the door for more components scheduled for future tests.
The test was part of the SLS Program’s RS-25 affordability initiative — a collaborative effort between NASA and industry partner Aerojet Rocketdyne of Canoga Park, California, to reduce the engine’s overall production costs while maintaining performance, reliability and safety.
“As we build future RS-25s, NASA and our partners are taking advantage of innovative manufacturing techniques, including additive manufacturing, or 3-D printing, to make the engines more affordable,” said Andy Hardin engine integration hardware manager for the SLS Program at NASA’s Marshall Space Flight Center. “3-D printing is revolutionizing manufacturing, and the pogo accumulator is the first of many components that can be built more quickly and less expensively.”
To minimize the costs of developing SLS, NASA selected the RS-25 engine, to leverage the assets, capabilities and experience of the Space Shuttle Program. NASA’s fleet of 16 heritage engines have been modified with new controllers and other changes to allow them to launch the more powerful SLS on its first four flights. The SLS Program has ordered six new engines to be built by Aerojet Rocketdyne for future flights.
“With modern fabrication processes, including additive manufacturing, the ‘next generation’ of the RS-25 will have fewer parts and welds, reducing production time as well as costs,” said Carol Jacobs, RS-25 engine lead at Marshall.
Jacobs, who began working with the space shuttle main engine when she joined NASA in 1983, is excited about how new, 21st-century practices can help streamline the production process.
“Reducing the number of welds is very important,” she said. “With each weld comes inspections and possible rework. By eliminating welds, we make the hardware more reliable and the process much more lean and efficient, which makes it more cost-effective.”
The Dec. 13 test was the first in a series of four tests designed to evaluate the operation of the 3-D printed pogo accumulator, and the first in the series to certify the next generation of RS-25 engines. The new, pogo accumulator will be included on all tests moving forward.
“Future tests will incorporate more and more 3-D printed components, with each test series building on the previous tests,” said Hardin.
NASA and Aerojet Rocketdyne plan to incorporate dozens of components made using additive manufacturing techniques into the new RS-25 engines. In addition, nearly every other major component, including the main combustion chamber, nozzle, ducts, valves, electrical and running gear will incorporate affordability improvements using a variety of advanced manufacturing processes. The innovative processes, along with design changes will eliminate more than 700 welds and more than 700 parts, while reducing engine costs.
SLS, which is managed by Marshall, will enable a new era of exploration beyond Earth’s orbit, launching astronauts in the Orion spacecraft on deep-space exploration missions to the Moon and eventually to Mars. On the first flight of SLS, the rocket will send an uncrewed Orion thousands of miles beyond the Moon before the spacecraft returns to Earth.
The four heritage RS-25 engines and flight controllers that will power SLS on that first flight have been certified and are awaiting shipment to NASA’s Michoud Assembly Facility, where they will be joined to the SLS core stage. Major welding on all five parts of the rocket’s core stage for EM-1 has also been completed and the hardware is ready for additional outfitting and testing.
Massey, an ASRC Federal/Analytical Services employee, supports the Office of Strategic Analysis & Communications.
Scientists Take Viewers to the Center of the Milky Way
This new video from NASA’s Chandra X-ray Observatory immerses viewers in a 360-degree view of the center of our home galaxy, the Milky Way. The movie is based on data from Chandra and other telescopes. It gives users a chance to control their own exploration of the environment of volatile massive stars and powerful gravity around the monster black hole, Sagittarius A*, at the Milky Way’s center. Scientists have used the visualization to study the effects Sagittarius A* has on its stellar neighbors. NASA’s Marshall Space Flight Center manages the Chandra program for NASA’s Science Mission Directorate in Washington. The Smithsonian Astrophysical Observatory in Cambridge, Massachusetts, controls Chandra’s science and flight operations. (NASA/CXC/Pontifical Catholic Univ. of Chile /C.Russell et al.)
Marshall Fosters STEM Education Through CubeSat Class in Tennessee
By Amanda M. Adams
NASA’s Marshall Space Flight Center is on a mission to inspire young minds to become the next generation of critical thinkers. By engaging students in space exploration, Marshall encourages learning in science, technology, engineering and mathematics in a way that fosters hands-on learning and discovery.
“As more states incorporate STEM-focused education into their standards, we assist teachers by developing curriculum support materials that help them meet the standards while making learning fun for their students,” said Susan Currie, an education specialist at Marshall.
One example of how Marshall achieves this goal is through collaboration with the Oak Ridge City School System in Oak Ridge, Tennessee. Education specialists and engineers at Marshall assisted in curriculum development that incorporated unique NASA resources, and then trained teachers to use the resources for a new elective engineering course called NASA Project-Based Learning. Marshall engineers also serve as mentors to students in the course. Patrick Hull, a technical assistant in the Structural and Mechanical Design Branch of Marshall’s Engineering Directorate, assisted with this collaboration in the community where he grew up.
“We sought to invest in our community and influence middle school students by exposing them to exciting STEM careers at NASA,” said Hull. At many schools, this type of unique experience in STEM fields is only available in an extracurricular environment.
Hull partnered with Robertsville Middle STEM teacher Todd Livesay to create a project that tasked students with designing and 3-D printing a small, one-unit cube satellite, or 1U CubeSat. Once completed, the students presented their project at Marshall to Hull and a panel of fellow engineers. “To have had an opportunity in junior high to work with a group of engineers from NASA would have been very motivating to me,” said Hull.
“The value of skills learned by our students in this program spans more than just STEM disciplines,” said Holly Cross, career and technical education supervisor for the Oak Ridge City School System. “The mentors from NASA encouraged our students to talk about their project in a conversational manner rather than memorizing for a presentation. Our English teachers have commented on how their presentation skills have developed and matured as a result of their interaction with the NASA engineers.”
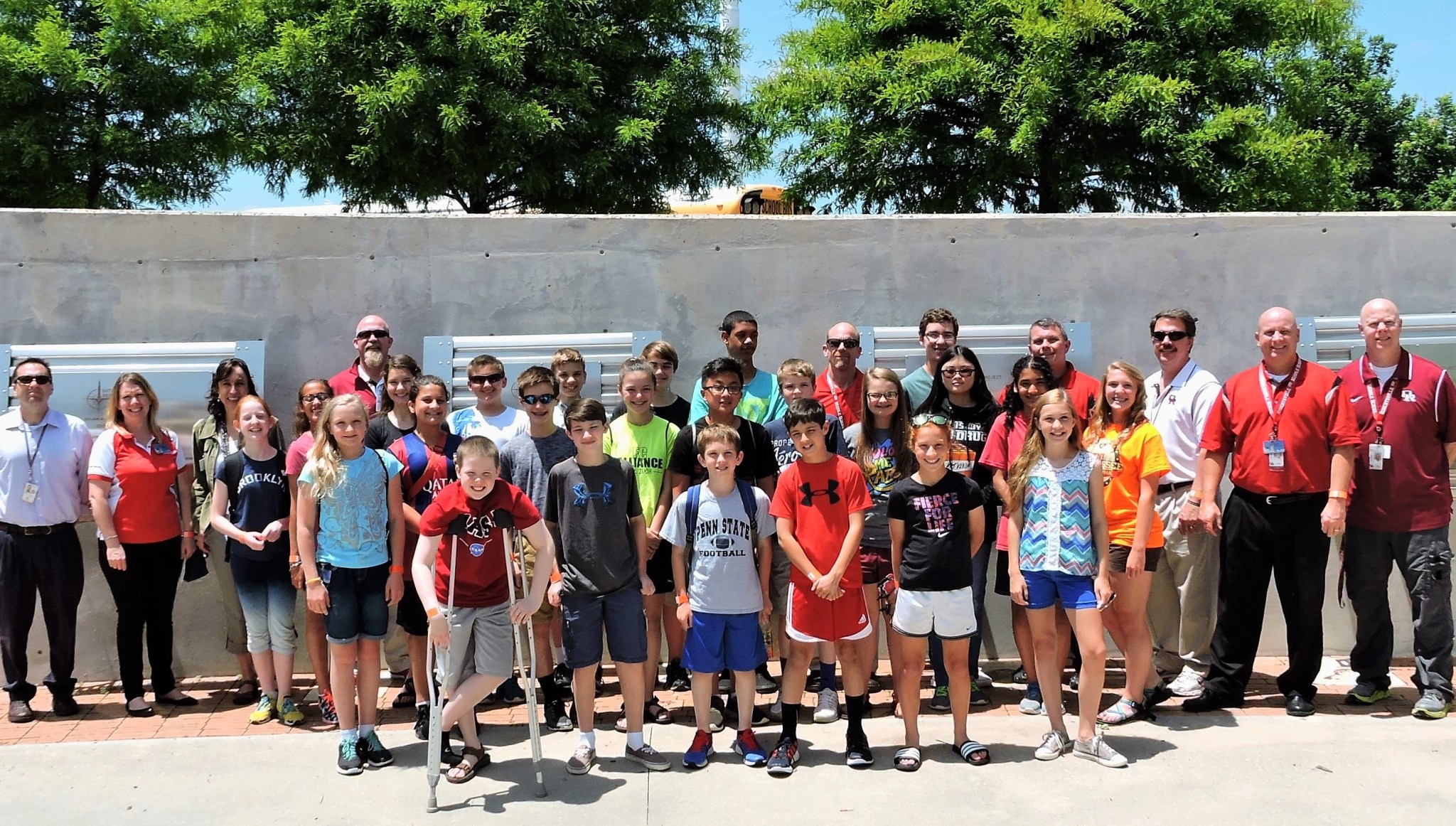
For the 2017 class mission, the students chose a cause that was near to their hearts. In 2016, wildfires ravaged communities in nearby Gatlinburg, Tennessee, taking the lives of 14 residents and leaving more than 2,500 homes and businesses damaged or destroyed. To assist Gatlinburg and other communities impacted by wildfires, the students set out to develop a CubeSat capable of deploying a camera and radio in space to observe and communicate the regrowth pattern of vegetation after a widespread fire. This information can be used to help communities regrow after destruction.
The students submitted their completed project in proposal form to NASA’s CubeSat Launch Initiative to compete for a spot to fly on a future launch. Through the initiative, NASA provides universities, high schools and non-profit organizations access to a low-cost pathway to conduct research in the areas of science, exploration, technology development, education or operations. The students will find out if they were selected when NASA makes its next round of CubeSat selections in February. Selected experiments will be considered as potential payloads on agency launches or for deployment from the International Space Station beginning in 2018 through 2021.
NASA centers nationwide work with schools by developing and providing engineering and science curriculum resources and training at no cost to teachers through the Educator Professional Development Collaborative.
The collaborative is managed by Texas State University in San Marcos as part of NASA’s education offerings. A free service for K-12 educators nationwide, it connects educators with the classroom tools and resources they need to foster students’ passion for careers in STEM and produce the next generation of scientists and engineers.
Adams, an ASRC Federal/Analytical Services employee, supports the Office of Strategic Analysis & Communications.
This Week in NASA History: STS-72 Lands – Jan. 20, 1996
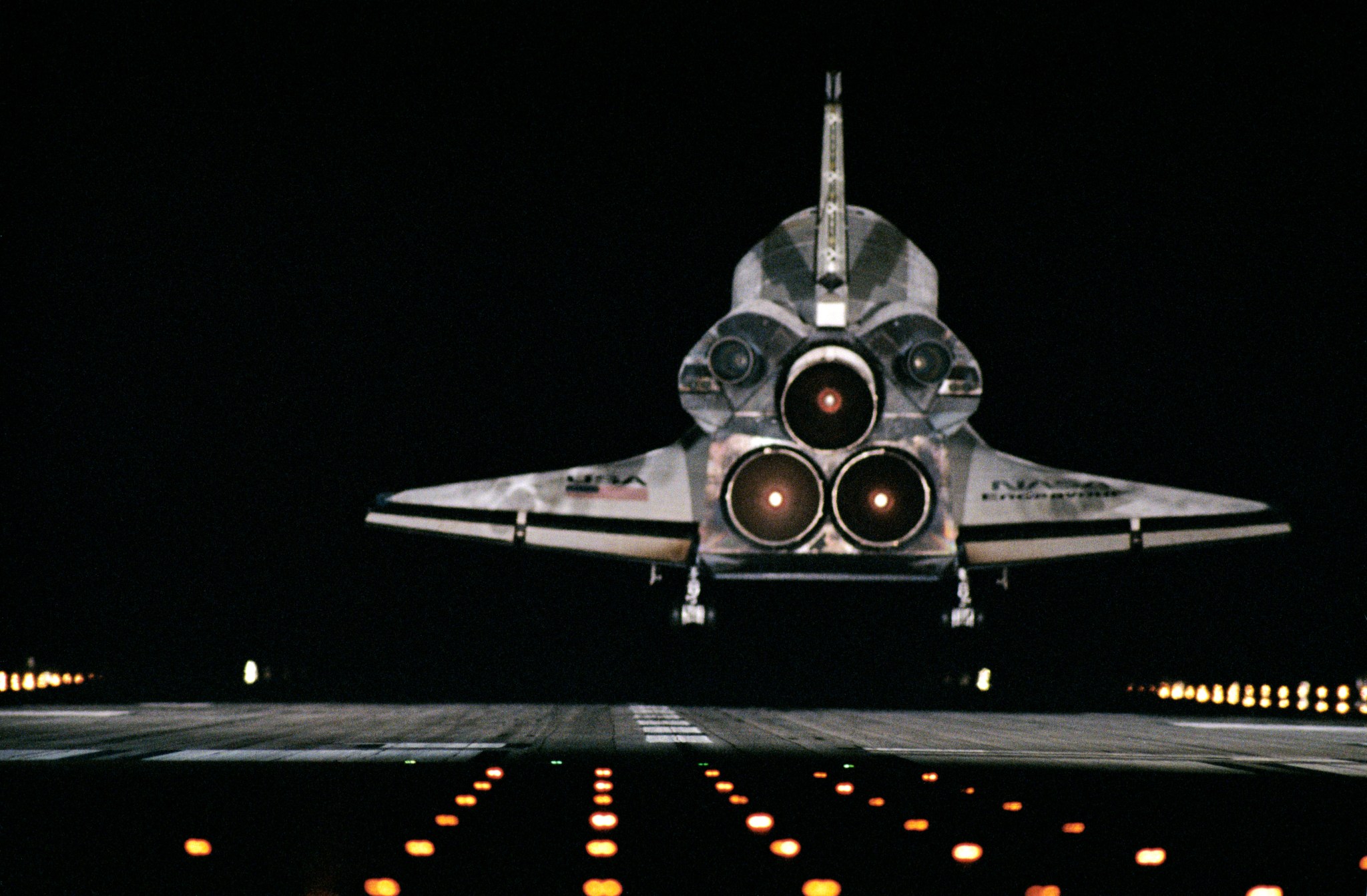
This week in 1996, STS-72 landed aboard the space shuttle Endeavour at NASA’s Kennedy Space Center following a successful eight-day mission. STS-72 was the first shuttle flight of 1996 and was responsible for retrieving the Japanese Space Flyer Unit and deploying the Office of Aeronautics and Space Technology-Flyer. The OAST Flyer, an American minispacecraft, carried four experimental packages: to measure spacecraft contamination levels at low-Earth orbits, to test GPS equipment, to test amateur radio gear and to determine the effects of solar radiation on the explosives aboard satellite systems. Today, the Payload Operations Integration Center at Marshall serves as “science central” for the space station, working 24/7, 365 days a year in support of the orbiting laboratory’s scientific experiments. The NASA History Program is responsible for generating, disseminating and preserving NASA’s remarkable history and providing a comprehensive understanding of the institutional, cultural, social, political, economic, technological and scientific aspects of NASA’s activities in aeronautics and space. For more pictures like this one and to connect to NASA’s history, visit the Marshall History Program’s webpage. (NASA)
Obituaries
Lewis E. Moore, 55, of Huntsville, died Jan. 4. He began working at the Marshall Center in 1986, where he was still employed as an engineer at the time of his death.
James E. Williams, 96, of Huntsville, died Jan. 2. He retired from the Marshall Center in 1980 as an aerospace engineer. He is survived by his wife, Willie H. Williams.
Charles Graff, 93, of Huntsville, died Jan. 1. He retired from the Marshall Center in 1980 as an electrical engineer.
Robert J. Morse Sr., 83, of Huntsville, died Dec. 26. He retired from the Marshall Center in 1996 as an aerospace engineer.
Robert C. Lewis, 90, of Huntsville, died Dec. 24. He retired from the Marshall Center in 1978 as an aerospace engineer. He is survived by his wife, Sara Lewis.
Floyd R. Grissett, 83, of Arab, Alabama, died Dec. 15. He retired from the Marshall Center in 1990 as an engineering technician. He is survived by his wife, Patricia D. Grissett.
Charles R. Bunnell, 84, of Huntsville, died Dec. 11. He retired from the Marshall Center in 1994 as an aerospace engineer.
John A. Chambers, 93, of Birmingham, Alabama, died Nov. 28. He retired from the Marshall Center in 1981 as an aerospace engineer.