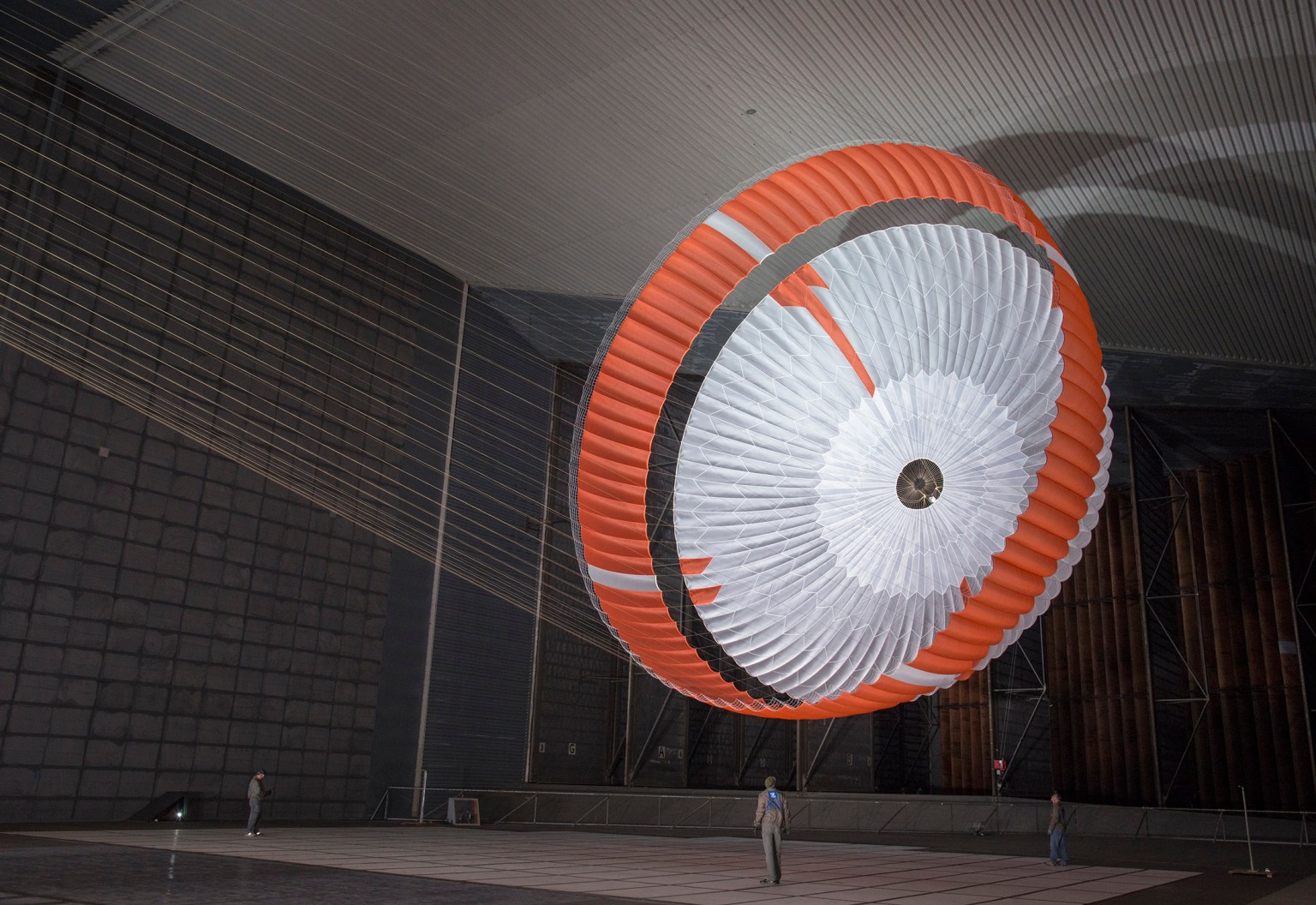
Ames Contributions to Mars 2020 Mission
NASA’s Ames Research Center in California’s Silicon Valley made key contributions both to the Mars 2020 Perseverance rover mission and the Ingenuity Mars Helicopter mission.
NASA will launch the Mars 2020 Perseverance rover to better understand the climate and geology of Mars and search for signs of ancient microbial life as part of its astrobiology mission. The rover is the largest, heaviest, most sophisticated vehicle NASA has ever sent to Mars. It will collect samples of Martian rock and soil that are planned to be picked up by subsequent robotic missions and returned to Earth for analysis. Additionally, Perseverance will test new technology that will help us prepare for future robotic missions and human exploration of the Red Planet.
The Mars Helicopter, Ingenuity, is riding to the surface of Mars, attached to the belly of Perseverance, to perform a technology demonstration. This small, autonomous aircraft will demonstrate the first powered flight on Mars — or any other planetary body, other than Earth — and transform planetary exploration.
NASA’s Ames Research Center in California’s Silicon Valley made key contributions both to the Mars 2020 Perseverance rover mission and the Ingenuity Mars Helicopter mission.
Ames Contributions Details
Entry Systems
Hit the brakes, manage the heat, and arrive safely
Spacecraft rely on entry systems to successfully transition from space, pass through the atmosphere, and land on a planet’s surface. These systems are the complete suite of technologies, heat shields, parachutes, software, and other articles, that protect crew and payloads inside against the extreme conditions of entry.
Mars 2020 Thermal Protection System
The Mars 2020 mission builds upon the successful architecture of NASA’s Mars Curiosity rover mission and will follow an entry, descent, and landing process similar to Curiosity’s 2012 arrival to the Red Planet. About 90% of the kinetic energy of these approaching spacecraft is dissipated during the entry phase, and that energy is converted to heat. That means things could get pretty toasty for a spacecraft – if it didn’t have a thermal protection system, like those designed by Ames.
The thermal protection system that will protect the Mars 2020 spacecraft when it reaches Mars in 2021 uses a design that closely matches the system developed for the Mars Science Laboratory spacecraft. When that spacecraft plunged into Mars’ atmosphere going about 13,000 miles per hour — slamming on the brakes with aerodynamic drag — the flight conditions generated searing heat. The heat shield reached 3,800 degrees Fahrenheit, but the thermal protection system kept Curiosity safe at a cool temperature of 50 degrees Fahrenheit inside the spacecraft.
Ames led the design, testing, and development of the thermal protection system for that prior mission, including the heat shield, backshell and the parachute’s closeout cone, on which the Mars 2020 systems are based. The backshell is the cone-shaped part of the entry spacecraft that carries the parachute and other components and adjoins the heat shield to encapsulate the rover. The material used in the both the Mars Science Laboratory’s heat shield and the Mars 2020 heat shield, Phenolic Impregnated Carbon Ablator, or PICA, was invented by Ames researchers.
Ames led the effort to verify that the Mars Science Laboratory spacecraft’s thermal protection system design was sufficient for the Mars 2020 mission.
Ames participated in the redesign of the Mars 2020 parachute’s closeout cone’s lid to accommodate the thicker bridle lines of the strengthened parachute that the Mars 2020 spacecraft will deploy during entry. The new lid design required several design and test cycles to ensure that the thermal protection system did not shatter into large pieces prior to parachute deployment.
Ames provided key analysis and testing for the three thermal protection system materials used for the Mars 2020 spacecraft’s aeroshell: the Phenolic Impregnated Carbon Ablator thermal protection material, used for the forward heat shield; SLA-561V, a heritage honeycomb-based material used for the backshell; and Acusil II, the material used on the parachute’s closeout cone.
Additionally, Ames provided independent verification and validation of aerothermal analysis of the Mars 2020 entry environments.
Learn more:
- Ames’ Involvement in Mars Science Laboratory / Curiosity
- Mars Science Laboratory Heat Shield
- Mars Exploration Rovers, Spacecraft: Entry, Descent, and Landing Configuration
Mars Entry, Descent and Landing Instrumentation 2
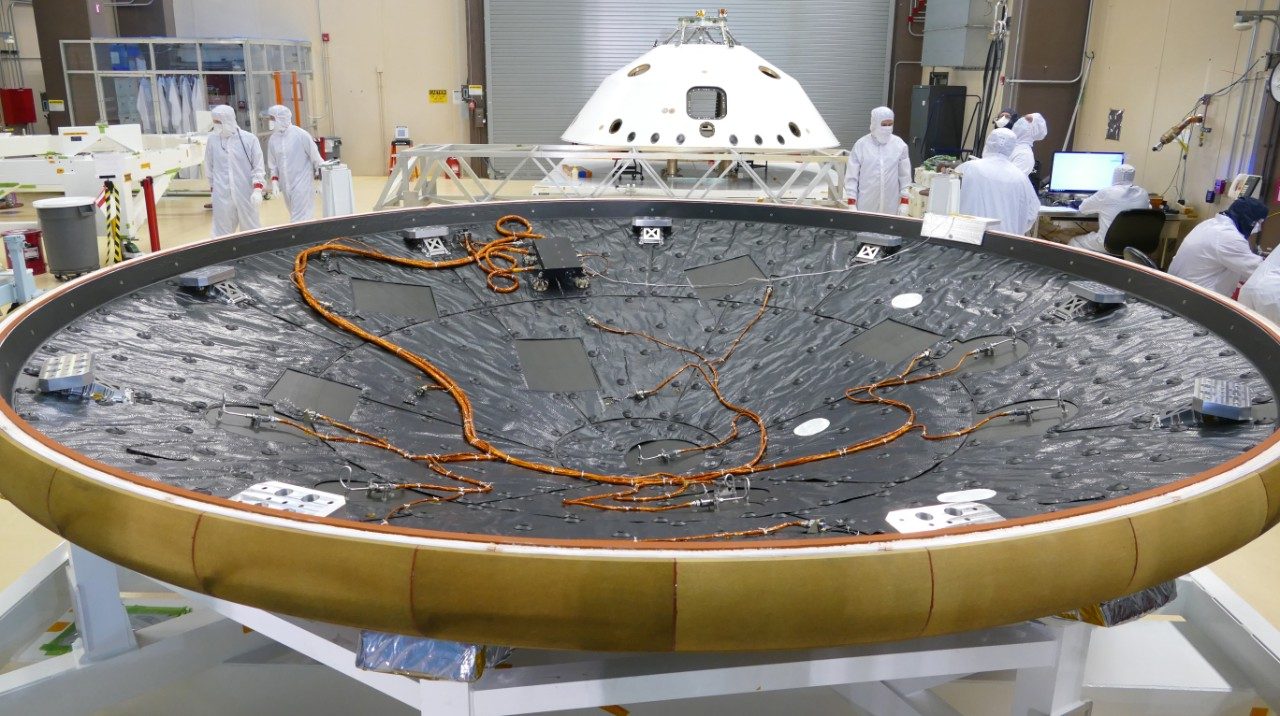
MEDLI2 is based on a successful prior project, the MSL Entry, Descent, and Landing Instrument, that flew temperature and pressure sensors installed on the Mars Science Laboratory heat shield. MEDLI2, a specialized suite of instruments, will collect temperature and pressure measurements on the Mars 2020 spacecraft’s heat shield and backshell during atmospheric entry, spanning about seven minutes of flight when the spacecraft “hits the brakes” and pressure and heating around the spacecraft peaks. Analysis of these data will help us to improve designs of entry systems for future robotic and crewed missions to Mars.
MEDLI2 includes three types of sensors — thermocouples, heat flux sensors, and pressure transducers — and a data acquisition unit to collect the heating and atmospheric pressure experienced by the aeroshell during entry through parachute deployment.
Ames designed and fabricated MEDLI2’s thermocouple plugs for the Mars 2020 spacecraft’s thermal protection system, and performed a series of rigorous tests on the heat flux sensors and radiometer for the backshell of the Mars 2020 spacecraft. These instruments will provide the first direct heat flux measurement on the backshell of an aeroshell for a NASA Mars mission.
Learn more:
For researchers:
Mars 2020 Parachute Wind Tunnel Testing
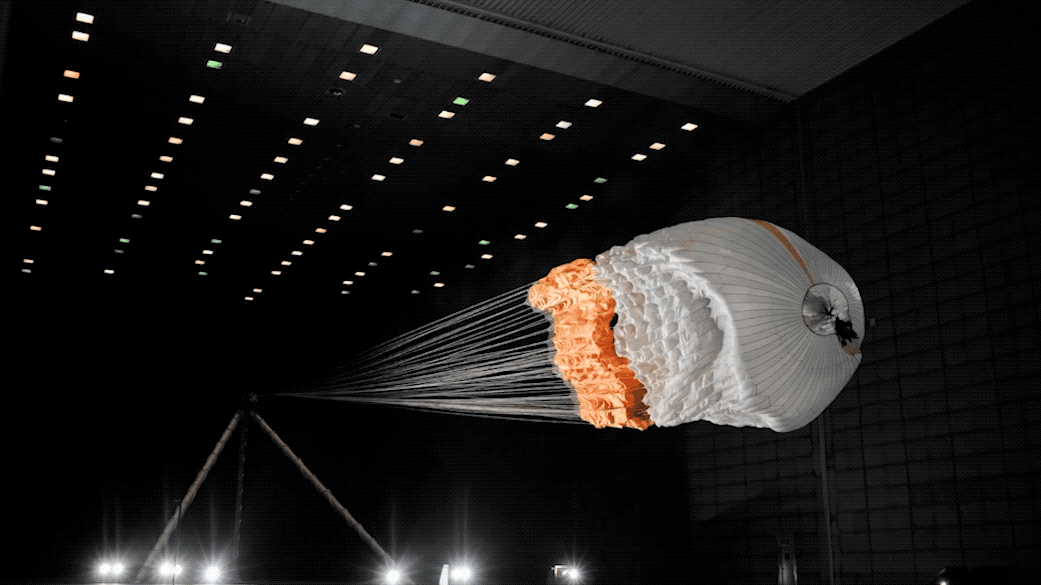
The Mars 2020 parachute is a component of the Mars 2020 spacecraft’s entry system; an unfurled canopy creates aerodynamic drag and functions as a brake to slow the spacecraft as it falls.
Ames tested Mars 2020-type parachutes in the largest wind tunnel on Earth to prove that these parachutes could take the maximum forces expected when the canopy opens on Mars at speeds over 1,000 mph. The main goal of these tests was to show that the parachutes could reach an opening load of 80,000 pounds of drag force without being damaged.
The Mars 2020-type parachutes weigh 180 pounds and are about 50 feet in diameter when they are fully open. Ames’ National Full-Scale Aerodynamics Complex 80- by 120-foot wind tunnel, managed and operated by the U.S. Air Force, is the only facility in the world capable of testing the full-size canopy.
The atmosphere of Mars is about ten times thinner than Earth’s atmosphere, and this difference affects how a parachute opens. It took several seconds for these parachutes to fully open during tests at sea level on Earth. When the Mars 2020 parachute deploys in the thin Martian atmosphere, it will open in less than one second.
The force exerted on the parachute during Mars deployment is the same as during deployment at Ames, when the wind tunnel is running at roughly 75 mph. Ames conducted parachute deployment tests in the wind tunnel running at that speed and proved that these parachutes could withstand the forces they would see while opening in the Martian atmosphere. Successful completion of the wind tunnel tests cleared the way for the high-altitude flight tests to follow.
Ames’ expertise is based in previous experience in testing Mars parachutes. Wind tunnel engineers conducted a full-scale parachute deployment, small-scale and supersonic tests for the Mars Science Laboratory spacecraft, supporting the mission that successfully landed the Curiosity rover on the surface of Mars in 2012.Ames also tested parachutes for the Mars Exploration Rovers Spirit and Opportunity, and the InSight Mars lander.
Learn more:
For researchers:
- Parachute Deceleration System Testing for the Mars Science Laboratory Curiosity rover mission.
Entry Systems Modeling
The entry, descent and landing segment of an interplanetary journey is one of the riskiest parts of any landed mission. Critical systems that safeguard spacecraft during atmospheric entry and deliver missions to the planet’s surface rely on computational design and experiments on individual parts of the system because the full-scale spacecraft cannot be fully tested at real entry conditions prior to use.
The Entry Systems Modeling project develops computer-based technologies and validation experiments that predict spacecraft performance during entry. These capabilities enable safer and more effective designs for NASA entry missions. Ames leads the project and has made several contributions toward the Mars 2020 mission.
The atmosphere of Mars, unlike Earth’s nitrogen- and oxygen-rich atmosphere, is mostly made of carbon dioxide gas. The chemical composition of a planetary atmosphere affects the intensity of the heat that reaches the surface of a spacecraft during entry.
This Ames project established that infrared radiation from carbon dioxide is a key contributor to spacecraft heating during Mars entry. Carbon dioxide radiative heating was not accounted for during the design of the Mars Science Laboratory mission. This discovery ultimately led to an entirely new aerothermal design policy to be implemented for the Mars 2020 spacecraft.
The team calculated the extent of carbon dioxide radiative heating expected during Mars entry conditions and validated these results with shock tube experiments obtained in flight-like conditions. A shock tube is like a very fast wind tunnel. These experiments were conducted in the Electric Arc Shock Tube facility at Ames, the only shock tube in the U.S. capable of simulating the radiative heating experienced by a spacecraft as it enters an atmosphere at high speed.
In addition, the carbon dioxide radiation is predicted to be the dominant source of heating on the rear of the Mars 2020 spacecraft. This is the primary justification for putting a radiometer on the backshell of the spacecraft to directly measure carbon dioxide radiative heating as part of the MEDLI2 instrumentation project.
The Entry Systems Modeling project leads the development of improved models for heatshield materials, including PICA, the thermal protection material used on both the Mars 2020 and Mars Science Laboratory spacecraft. This effort included a dedicated activity in collaboration with MEDLI2 to model a silicone coating on the Mars 2020 heatshield and its effect on thermal response. Understanding the silicone-coated PICA thermal response is required to improve our understanding and interpretation of both the MEDLI and MEDLI2 datasets.
The project also contributed detailed imagery of pre- and post-heated parachute materials for the Mars 2020 program to understand potential fabric degradation.
For researchers:
COCPIT Software
Scientists and engineers will use a specially designed software, known as the Component-based Campaign Planning, Implementation and Tactical software tool, or COCPIT, to plan and schedule all of the Mars 2020 Perseverance rover’s activities while it is on the surface. This tool will help the rover keep track of the complex activities it must conduct using an assortment of scientific instruments. COCPIT ensures all required resources and limitations of a Mars mission are accounted for and allows scientists and engineers to develop plans that are feasible for the rover to execute. By shifting all software support tools to a web-based online framework, as well as introducing a new on-board planner, the total planning time for Perseverance is cut by at least a third when compared to Perseverance’s predecessor, Curiosity.
COCPIT is designed, developed, tested, and deployed, in collaboration with JPL, by the Scheduling and Planning Interfaces for Exploration team from the Human-Computer Interaction group at Ames. The team has worked on mission planning tools for four Mars missions, and their web-based mission planning tool, Playbook, serves as the foundational code on which COCPIT is built. The team’s most recent work with COCPIT is paving the way for the next generation of aids for future human and robotic exploration.
Ingenuity Mars Helicopter
Pushing the limits of vertical flight by flying a helicopter in the extremely thin atmosphere of Mars
Helicopters operate immersed in an atmosphere and need air pressure to fly. They use rotating blades to generate the force of lift that works against the force of gravity to achieve powered, controlled, vertical flight.
The types of helicopters that routinely fly on Earth can only go so high. At higher altitudes, air gets thinner, and the ability for that same helicopter to generate lift and support its own weight is decreased. Less air surrounding the blades means less to push against.
The atmospheric pressure in Jezero Crater, Mars, where Ingenuity will make its first flight, is equivalent to about 100,000 feet above the Earth’s surface. No helicopter has ever ascended to even half that distance above Earth. Mars gravity — about one-third that of Earth — lessens the load for Ingenuity, but will need to be light, weighing four pounds on Earth, to take off in this very thin air.
Ames has been studying Mars helicopters and planetary aerial vehicles – including rotorcraft, vertical lift vehicles, and fixed-wing aircraft – since the late 1990s. Some of the basic flight physics and engineering designs for helicopter rotors were established at the center.
The first hover test and the first forward flight test with rotorcraft under Martian conditions were done in specialized facilities at Ames. These facilities include the Planetary Aeolian Laboratory’s large, low-pressure chamber and the Mars Wind Tunnel, which is operated within the chamber.
Additionally, Ames developed specialized rotor test apparatus for hover and forward-flight rotor testing under Mars-like conditions. This apparatus was also used by Ames personnel to study rotor flow recirculation conditions and the best way to mitigate the effects of that flow recirculation, in the 25-foot space simulator vacuum chamber at NASA’s Jet Propulsion Laboratory in California, prior to the 2016 Mars Helicopter prototype demonstration in that same chamber at JPL.
Ingenuity was designed and developed by JPL. Ames’ expertise led JPL to partner with the center and NASA’s Revolutionary Vertical Lift Technology project from the very beginning of the Ingenuity project.
Ames research engineers provided their expertise and performed detailed work in performance predictions, computational fluid dynamics analysis, analytical and experimental studies of facility installations assessing aerodynamic interference effects of test apparatus implementations, and extensive system identification and control law development and validation.
Ames contributed to the system integration testing of a full-scale prototype of a Mars helicopter — that successfully hovered in the 25-foot space simulator facility in 2016 — as well as the two engineering development models, and the flight development model, Ingenuity, now installed on the Perseverance rover.
This sustained research and development effort that began in 2015 ultimately led to the incorporation of the Ingenuity Mars Helicopter into the Mars 2020 mission. Ames continues to partner with JPL to consider future Mars rotorcraft designs.
Learn more:
- Mars Helicopter
- NASA is With You When You Fly, Even on Mars
- NASA’s Aeronautics Experts Help Prepare Ingenuity to Fly on Mars
For researchers:
- NASA technical webpage: Mars Helicopter Project
- NASA technical webpage: Revolutionary Vertical Lift Technology project
Main Image: A Mars-type parachute, similar to the one installed on the Mars 2020 spacecraft, is tested at the United States Air Force National Full-Scale Aerodynamics Complex 80- by 120-foot wind tunnel at NASA’s Ames Research Center in California’s Silicon Valley. Deployment tests at Ames with the wind tunnel running at about 75 mph proved that these parachutes could withstand the forces they would see while opening in the Martian atmosphere at speeds over 1,000 mph. The parachute is a key component of the Mars 2020 mission’s entry systems that will deliver the Perseverance rover to the surface of the Red Planet. Image credits: NASA/JPL-Caltech
Learn more:
For news media:
Members of the news media interested in covering this topic should reach out to the NASA Ames newsroom.