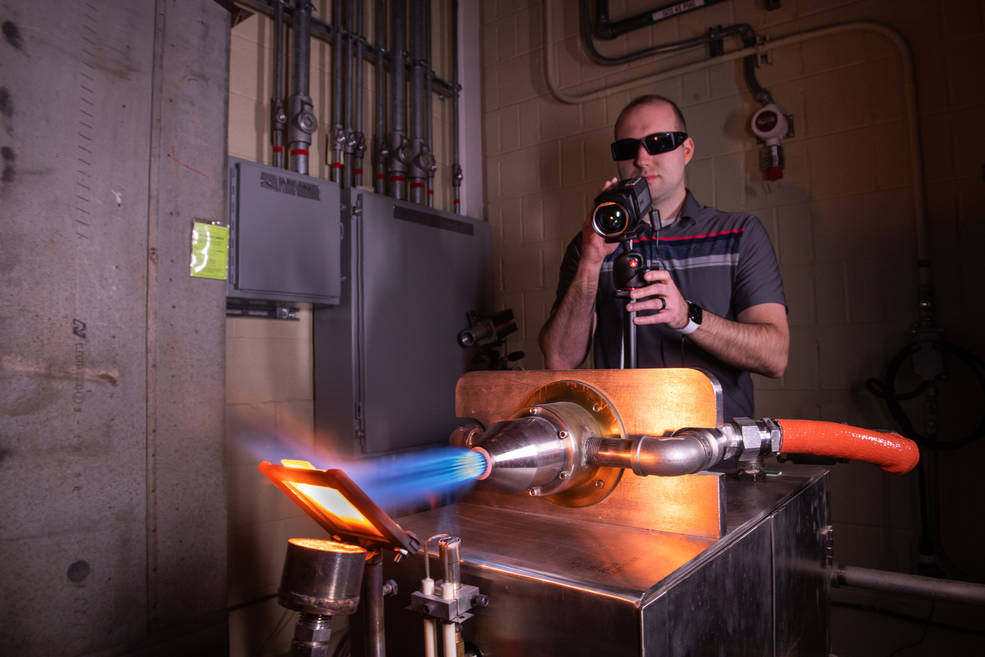
NASA has made significant progress toward its goal of creating a more fuel-efficient jet engine core for next-generation sustainable commercial aircraft.
In just a year and a half since it began, the Hybrid Thermally Efficient Core (HyTEC) project already is moving forward into the advanced testing required before conducting an engine core demonstration with industry partners.
“The first six months of the project, we didn’t have many people coming into the lab due to the pandemic,” said Anthony Nerone, who leads HyTEC from NASA’s Glenn Research Center in Cleveland. “Thanks to our team’s motivation, we hit the ground running and got things moving fast.”
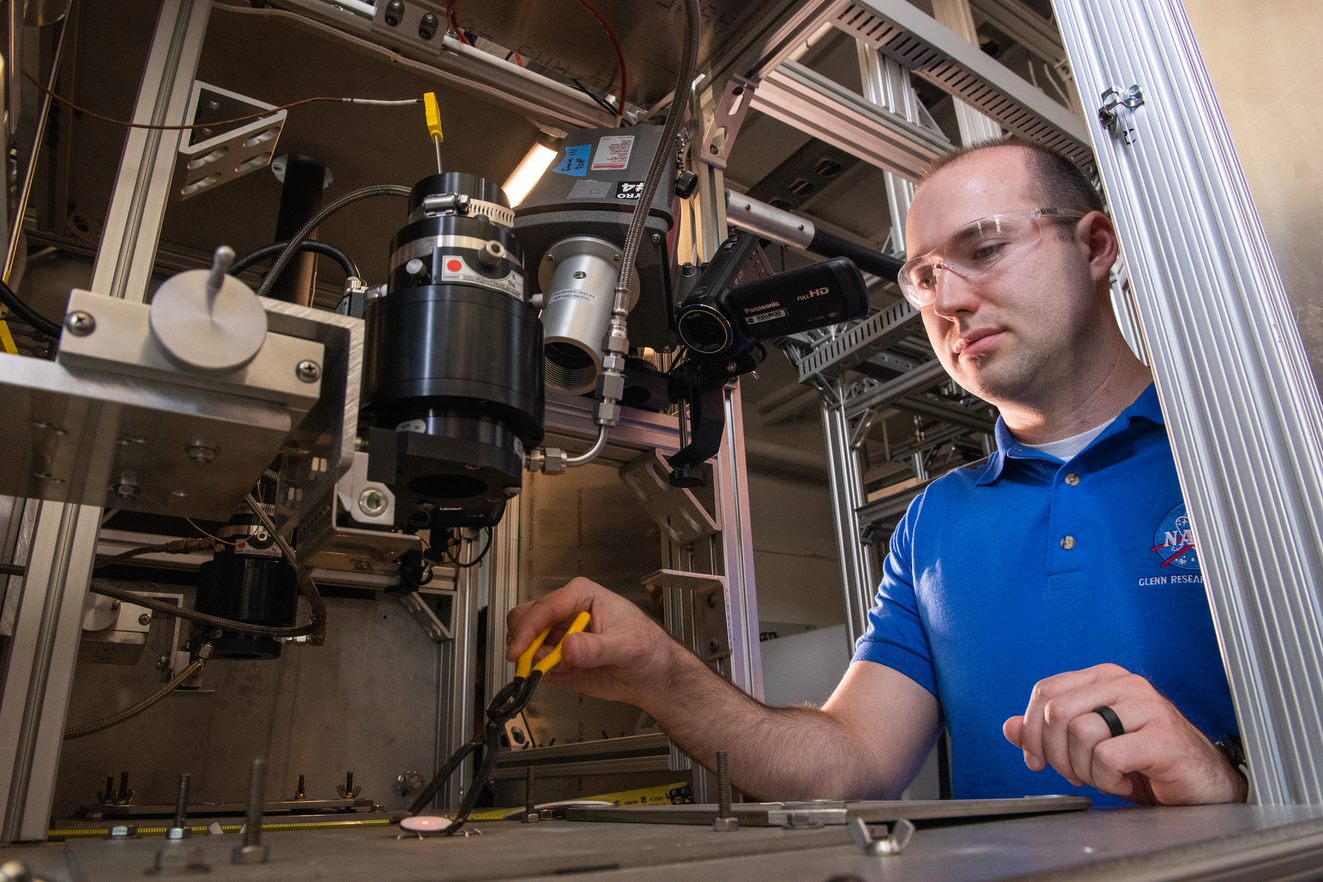
HyTEC aims to develop small turbofan engine cores that reduce fuel burn. The project is a key area of NASA’s Sustainable Flight National Partnership, which seeks to enable net-zero carbon emissions in aviation by the year 2050, in collaboration with government, industry, and academia.
As part of its efforts to achieve the 2050 goal, NASA intends to have HyTEC’s engine core technologies readily available sometime during the 2030s for adoption and potential incorporation into the next generation of more sustainable single-aisle aircraft.
That means HyTEC is on something of a fast track, and the project is conducting its research in lockstep with industry partners to design and test the engine core.
“We’re really excited to work on this technology, especially since it could be flying as soon as 10 years from now,” Nerone said.
Working Inside a Jet Engine
To shrink down the size of a jet engine’s fuel-consuming core while also maintaining the same amount of thrust, the project team is working to develop a number of technologies. Smaller engine cores run at hotter temperatures, requiring new materials that can withstand the heat and need less cooling air.
This phase of HyTEC’s work can essentially be described in a few simple steps: narrow down the best materials, test them thoroughly, and use the winners in an engine core test.
The project already has completed much of the work involved in the first two steps.
Researchers found the materials suited to the task are ceramic matrix composites (CMCs) and environmental barrier coatings (EBCs). Both kinds of materials are made of composites – several different materials mixed together.
The team plans to use CMCs to build engine core components and EBCs to coat components to provide protection from environmental damage.
“We’ve narrowed down the best materials so when we get to our full-on demonstrations, one clear winner can more efficiently be identified,” Nerone said. “The CMCs and EBCs that look promising now graduate to the next round. It’s a sort of screening process.”
But in the material sciences universe, CMCs and EBCs come in many different varieties, so HyTEC researchers are charged with identifying and selecting the best ones before they can begin engine core assembly and testing.
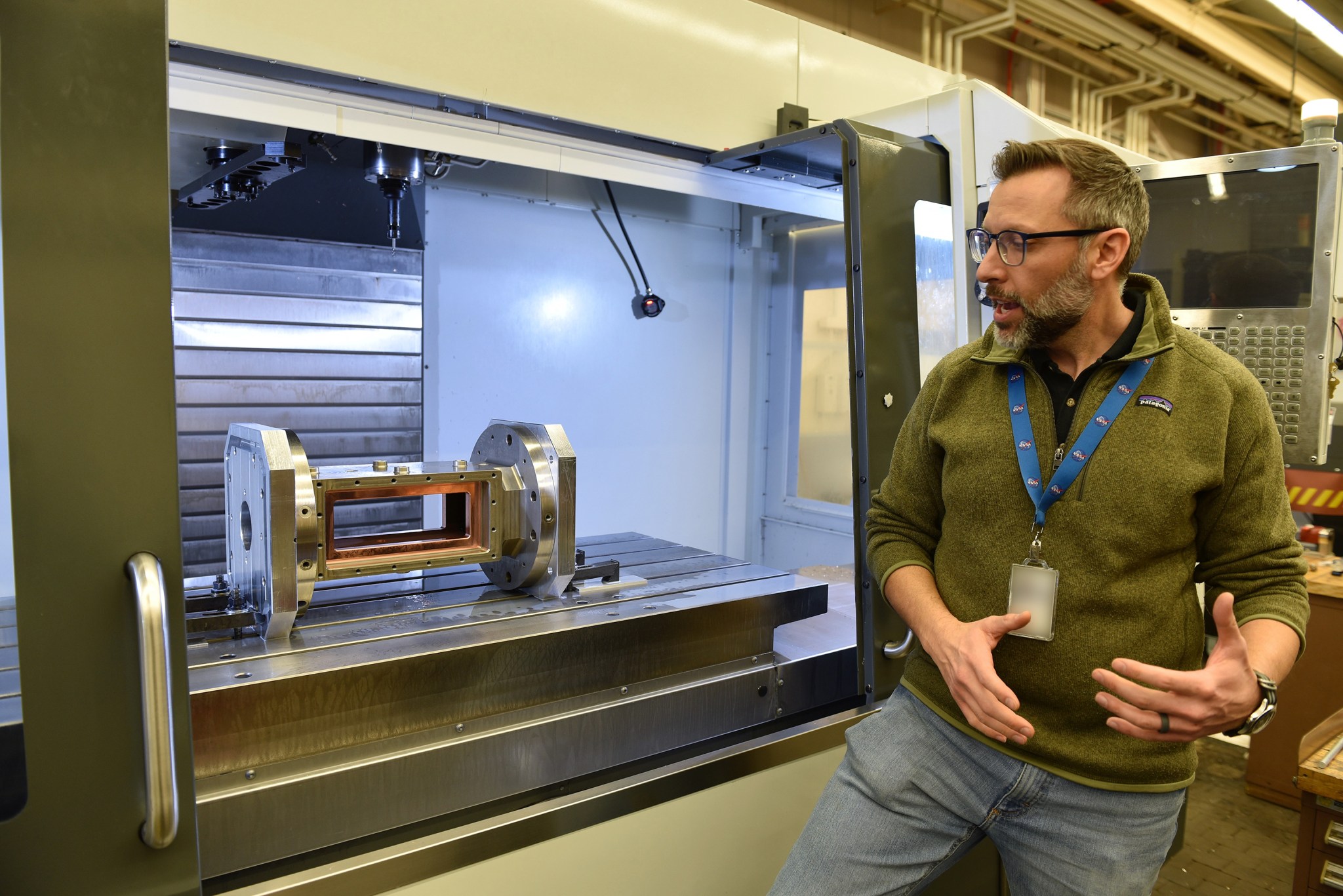
Candidates for the Job
Though composites can withstand extreme heat, they run the risk of potentially degrading and corroding comparatively faster than metals. To find the ones that hold up, HyTEC has put sample composites coated with different EBCs through an array of heat, pressure, and durability tests in NASA Glenn’s materials laboratories.
“In one lab, we have rigs with these huge burners heating small samples of the composites up to thousands of degrees. It’s run 24/7 to see how they hold up,” Nerone said. “After we see which ones perform best, we do more inspection and testing on them.”
For example, in Glenn’s Engine Research Building, HyTEC is using a combustor rig that simulates conditions of a jet engine more closely than the burner rig.
“Using the advanced materials, we build components in the actual size and shape of something that would really be inside a jet engine, then we perform tests in the combustor rig,” Nerone said. “Once we hit them with real engine conditions, the best ones start to emerge.”
Another key element of a jet engine core is its turbine blades. With a smaller core, turbine blades will be much smaller and more challenging to design. Therefore, aerodynamics testing is also part of HyTEC’s research.
“It’s a similar process. When you make everything smaller, the aerodynamics change as well. We make scale models of the turbine blades and see how they perform,” Nerone said.
Researchers test different turbine blade designs at Glenn to determine the best architectures for small core performance. Once they narrow their options down, they can perform larger-scale turbine tests.
Soon, they will be able to move on to even more advanced tests that will be conducted by NASA’s industry partners who are collaborating to conduct engine core tests. The HyTEC team expects that stage to occur a few years from now.
Though its timetable is ambitious, the project is staying the course and the team is driven to accomplish their task. Adding to their motivation is the purpose of the research itself – making aviation more sustainable.
“That’s really the crux of it,” Nerone said. “We’re reducing fuel consumption. It’s a substantial feat.”