Marshall, Michoud Team Members Honored with Management Award
By Taylor Goodwin
Team members from NASA’s Marshall Space Flight Center and Michoud Assembly Facility were honored with the agency’s Space Flight Awareness Management Award in a virtual ceremony March 11.
The annual award is presented to NASA civil servant and contractor midlevel managers who consistently demonstrate loyalty, empowerment, accountability, diversity, excellence, respect, sharing, honesty, integrity, and proactivity. The Marshall recipients were: Judy Ballance, Joshua Barnard, Tad Britton, Michael Chumley, Charlie Conway, Michael Hollingsworth, Lawrence J. Humpal, and Todd Nicholson. The Michoud honorees were Jaelene Cumba, Paul Decker, and Anthony Hankinson.
Former NASA astronaut Kenneth Bowersox and current deputy associate administer of the agency’s Human Exploration and Operations Mission Directorate – veteran of five space shuttle launches and multiple stays on the International Space Station – praised award recipients.
“There have been a lot of big challenges over the past year that have affected each of our team members differently,” Bowersox said, “and what amazes me is that those challenges have not stopped us from making great strides in our human spaceflight missions. That progress is due to the creativity and hard work of the folks we are honoring today.”
NASA astronaut James Kelly – who twice served as a space shuttle pilot and logged more than 141 hours in space – echoed Bowersox. “This is a chance for current and former astronauts to come back and say thank you for all of the hard work you’ve done for the space program,” he said. “Midlevel managers are really where the rubber meets the road. You have to keep track of details and all the little things that go on in the background. You’re the backbone of the mission.”
The awardees and their accomplishments included:
- Ballance, for her exceptional engineering achievement, leadership, dedication, and personal commitment in the delivery of unique and cutting-edge avionics and optics spaceflight hardware for multiple Human Exploration and Operations Mission Directorate, Science Mission Directorate, and Space Technology Mission Directorate programs and projects.
- Barnard, for providing the tools, resources, and support needed for the Space Launch System Exploration Upper Stage Flight Vehicle team to excel. His efforts have allowed the team to design, iterate, provide creative resolutions, and adapt to change.
- Britton, for his significant contributions to SLS core stage rocket propulsion hardware development. Operating with the utmost integrity and accountability, his management of Boeing’s efforts have been critical to mission success.
- Chumley, for mentoring and empowering his team to perform with integrity at the highest levels, which has allowed him to consistently acquire quality hardware within SLS program cost and schedule demands. His planning skills and innovative thinking have allowed him to successfully support multiple teams in the program including core stage and exploration upper stage development, supplier hardware development, and Michoud production.
- Conway, for exemplifying the highest standards required of the SLS Program. His expertise as a subject matter expert has been recognized by peers from the technical communities of both the company and customer organizations. Much of his leadership work is focused on identifying risk and controls needed to minimize or eliminate the possibility of failure.
- Hollingsworth, for his results-oriented approach to complex human spaceflight testing. Examples of hardware that has been tested by his team are the advanced recycle tank assemblies, nitrogen oxygen recharge system, NASA docking system, hatches, windows, and space station payloads.
- Humpal, for leading the SLS Avionics Test Team. He successfully manages complex projects involving significant challenges to execute a wide range of testing activities supporting multiple customers.
- Nicholson, for successfully leading the execution of the build of the complex SLS engine section. His leadership enabled team focus and meeting of commitments in a dynamic environment with focus on safety and reliability requirements to ensure yielding the safest design possible and meeting the needs of NASA on schedule commitments.
- Cumba, for excellent management of the SLS Engine Section Electrical team. She led with a plan and the ability to adjust when needed as constraints arose and obstacles were presented. Her ability to plan out the future development made the daily scope of work easier for technicians and allowed coordination with essential sections for difficult installations.
- Decker, for modeling true integrity as an advocate for SLS mission assurance and setting the bar of excellence when assessing nonconforming conditions for acceptance or repair.
- Hankinson, for his outstanding leadership in his role as an SLS quality manager. His attention to detail and pride in workmanship set high expectations for his team. His accountability is seen throughout his day-to-day operations and his professionalism radiates through his actions. He has been effective in training his teams with the necessary knowledge and providing the appropriate tools to improve quality response times.
Each awardee will receive a special commemorative spaceflight item.
Goodwin, a Media Fusion employee, supports Marshall’s Office of Strategic Analysis & Communications
Second SLS Green Run Hot Fire Test Set for March 18
NASA conducts the first Green Run hot fire test of the core stage for the agency’s Space Launch System rocket on the B-2 Test Stand at Stennis Space Center on Jan. 16. The agency is targeting a two-hour test window that opens at 2 p.m. CDT on March 18 for the second hot fire test and plans to begin live coverage on NASA Television, the agency’s website, and the NASA app approximately 30 minutes before the hot fire. Updates on operations and the target hot fire time will be provided at @NASA on Twitter and the Artemis blog. (NASA)
Wayne Bordelon recognized as HEO HErO
Wayne Bordelon is the latest team member from NASA’s Marshall Space Flight Center to be named a HEO HErO. Bordelon developed a strategy and defined content for endorsement of the Space Launch System’s System Engineering and Integration team for the Artemis I Flight Readiness Review, providing a path to a successful mission. Each week, NASA’s Human Exploration and Operations Mission Directorate recognizes HEO HErOes, team members from across the agency who have made vital contributions in their support of NASA’s mission to land the first woman and next man on the Moon by 2024. (NASA)
Science on High: Space Station Support Teams at Marshall Celebrate Two Decades of Achievement in Orbit
By Rick Smith
Ask International Space Station facility engineers and payload operations teams at NASA’s Marshall Space Flight Center what makes them proudest, looking back on two decades of developing, testing, and supporting science in orbit. Many will glance upward, as if the source of that pride might be passing overhead at that moment, 250 miles up.
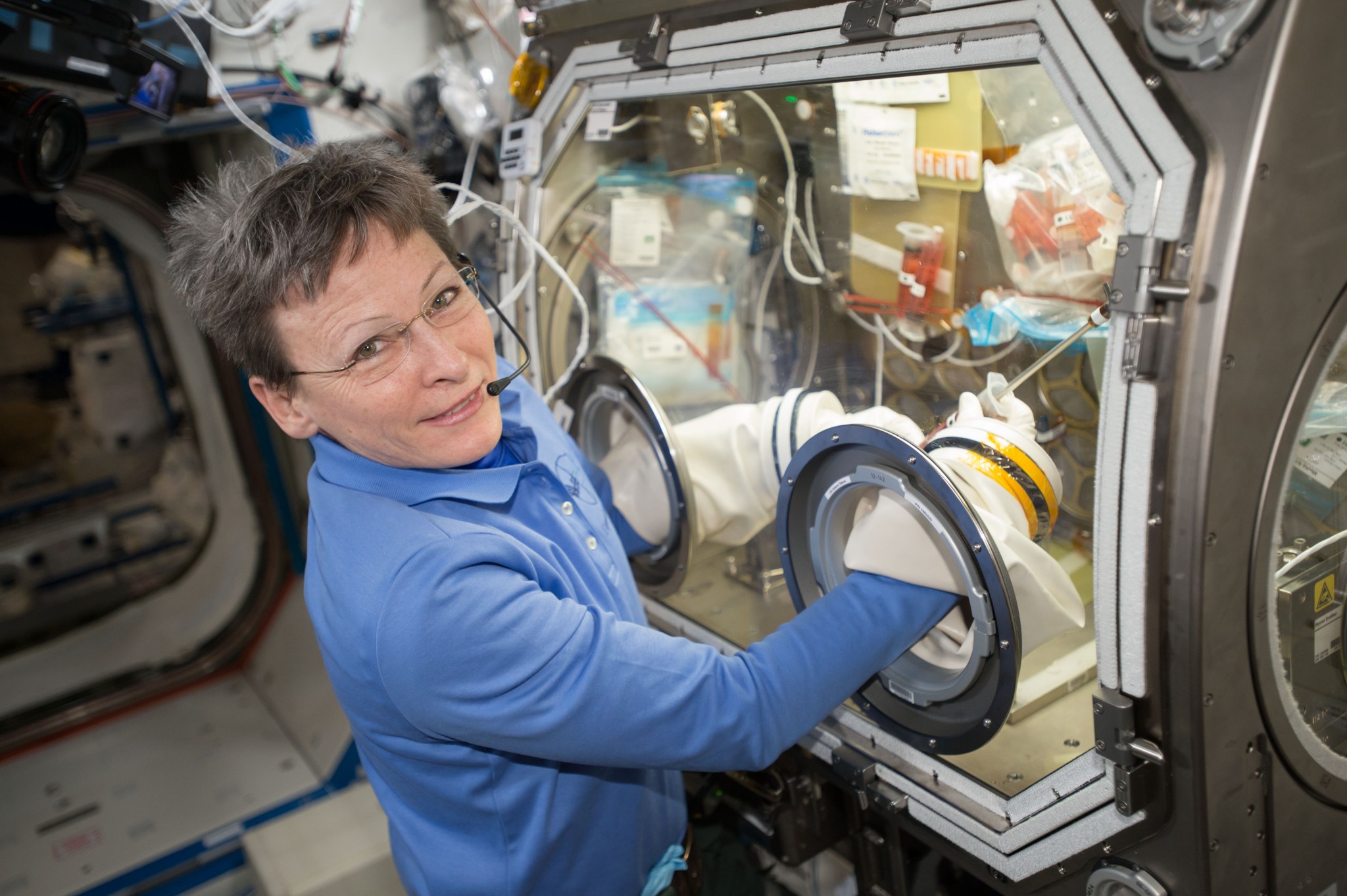
Just as often though, they look to one another.
“We all share one goal: to get experiments developed, tested, manifested and flown to space, successfully conducted in orbit, and returned to Earth for analysis and practical application,” said Shawn Reagan, materials science research portfolio manager in Marshall’s International Space Station Projects Office. “And it’s all in service of furthering our scientific knowledge, advancing our journey of exploration into the solar system, and aiding development of a thriving commercial space economy.”
Currently celebrating more than 20 years of continuous crew operations, the station is a marvel of teamwork. It’s home to round-the-clock science, with some 200 experiments underway at any given moment, overseen by astronauts and science teams on the ground. Crew and station operations are led by NASA’s Johnson Space Center, while Marshall oversees all payloads from its Payload Operations Center, monitoring use of the 15 unique science hardware facilities developed, built, and managed there for the agency.
Central among them are the “EXpedite the PRocessing of Experiments to the Space Station” multipurpose payload shelving units, or EXPRESS Racks. Developed and tested at Marshall by NASA and Boeing, the first two racks were delivered to the space station on STS-100 in 2001 and have been in continuous operation ever since. Today, there are 11 of them – including three streamlined Basic EXPRESS Racks – the last delivered in 2020.
Up to 80 experiments may be in process in the racks at a time, controlled by station crew or remotely by NASA personnel in Marshall’s Payload Operations Integration Center. There, a cadre of nearly two dozen team members monitor the racks around the clock, every day of the year, communicating in real time with the crew and researchers on the ground.
“The sheer volume of science that’s been conducted using the racks is overwhelming,” said Shaun Glasgow, former EXPRESS Racks project manager at Marshall, now project manager for the Material Science Research Rack. NASA estimates the racks have yielded more than 99 years of combined operational hours since the first were installed in 2001 – contributing to about 900,000 combined hours of research.
“As we prepare to return human explorers to the Moon and journey on to Mars, it’s even more exciting to consider all the scientific investigations still to come,” he added.
Marshall also manages the station’s self-contained Microgravity Science Glovebox and Life Sciences Glovebox, installed in 2002 and 2018, respectively.
Built by German developer Astrium for the European Space Agency and flight-tested at Marshall, the Microgravity Science Glovebox remains a permanent, high-demand fixture on station. Crew members use built-in glove ports in the sealed facility to safely manipulate liquids, particulates, and even open flame – conducting investigations in the areas of fluid physics, combustion science, biotechnology, materials science, and more. The facility has enabled more than 60,000 hours of powered science research to date.
Demand on the glovebox was so great that the space station partners commissioned a second dedicated facility, the Life Sciences Glovebox. The new facility, roughly the size of a large fish tank, primarily aids research into microgravity’s long-term impact on the human body. It was built by the Japan Aerospace Exploration Agency and the Dutch firm Bradford Engineering. Marshall contributed the secondary support structure, power system, and thermal control system. As with the racks, glovebox experiments are supported 24 hours a day by dedicated personnel in Marshall’s Payload Operations Integration Center.
Dramatically extending the station’s research capabilities are two unique lab facilities, the Materials Science Research Rack and the Window Observational Research Facility, better known as WORF. Jointly developed by NASA and ESA and launched in 2009, the Materials Science Research Rack houses the European Materials Science Laboratory. Capable of reaching temperatures up to 2,500 degrees Fahrenheit, it enables studies of metals, alloys, semiconductors, ceramics, glasses, and advanced metallurgical processes. Designed and built by Boeing at Marshall, WORF offers Earth science and space science researchers the means to observe environmental changes on Earth, track hurricanes and other natural disasters, and document meteor showers and other near-Earth phenomena.
David Brady, associate program scientist in NASA’s ISS Program Research Office at Johnson, says there have been three distinct chapters in the life of the space station.
“Its first decade was devoted to assembly in orbit, and its second was all about research and technology development, continuing to grow and refine its utility as a landmark science platform,” Brady said. “Now we’re in the station’s third decade, the era of full scientific utilization, expanded commercial value, and global partnership.”
Lynn Farris, ISS Payload Facilities team lead, said Marshall’s payload facility project managers welcome the challenge. “During initial station construction, we were lucky to log eight hours of science each week. Now the 15 station payload facilities managed by Marshall can clock in excess of 100 hours per week,” she said.
Farris heads the team that helps scientists plan and verify new glovebox and rack experiments, conducting preflight tests using the Payload Rack Checkout Unit housed in Marshall’s Space Station Integrated Test Facility. Marshall also maintains a specialized checkout facility, complete with furnace, for developing and certifying Materials Science Research Rack payloads. Additional Payload Rack Checkout Units reside at Johnson and at NASA’s Kennedy Space Center and Glenn Research Center.
Marshall facilities and payload operations teams also work closely with the station crews on the other end of the process. “The crew’s feedback improves our processes, and helps us gauge how well the hardware is working and where it needs refinement,” Farris said.
Science teams and hardware developers at Marshall are already looking ahead to new challenges, drawing from their successes on the space station to develop next-generation experiment racks and lab facilities that could serve in NASA’s proposed Gateway lunar orbiting outpost and on future research bases on the Moon and, in time, Mars.
The space station has been home to 242 individuals from 19 countries, working with more than 4,000 scientists in 108 countries to conduct some 3,000 total research investigations. Learn more about station research and technology here.
Smith, a Manufacturing Technical Solutions employee, supports Marshall’s Office of Strategic Analysis & Communications. Read the complete NASA feature story here.
20 Years of Space Station: Expanding, Evolving, Trailblazing
Editor’s note: This is the fifth in a five-part series highlighting scientific and technological breakthroughs that have been achieved over the past two decades as a result of International Space Station science. This research helps humanity explore farther into space while also benefiting life on Earth. The Payload Operations Integration Center at NASA’s Marshall Space Flight Center schedules, assists with, and coordinates all experiments on the station’s U.S. Orbital Segment.
Astronauts aboard the International Space Station have conducted long-duration research in microgravity – a feat possible only within the orbiting laboratory – for 20 years. That research has led to numerous discoveries, scientific publications, unique opportunities, and historic breakthroughs. Among these breakthroughs, the crew has expanded the field of colloid research, evolved fluid physics research, 3D printed in microgravity, and supported natural disasters response activities.
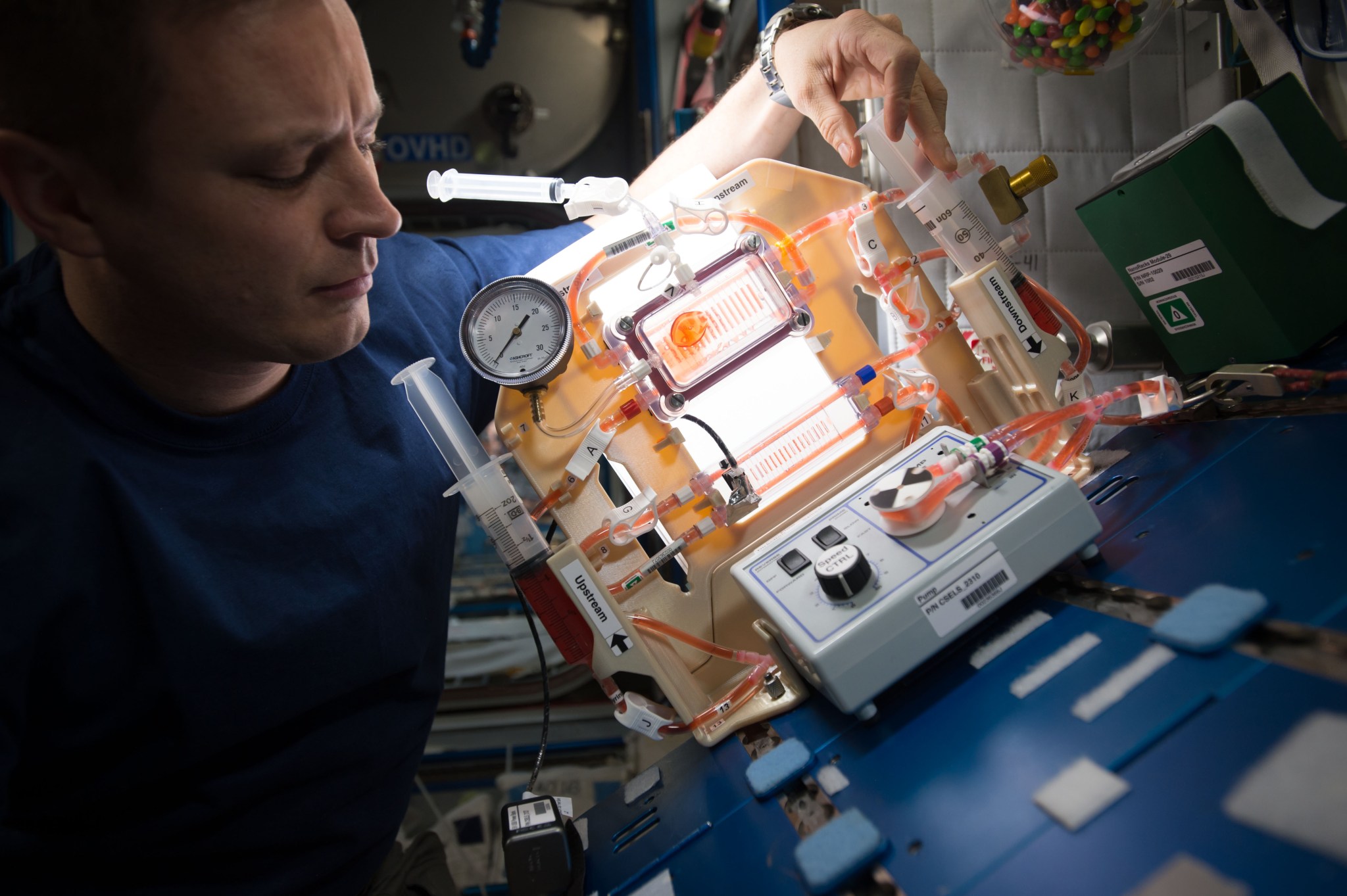
Colloid research: Toothpaste, 3D printing, pharmaceuticals, and detecting shifting sands on Mars may not seem related to each other, yet each stands to benefit from improvements made thanks to years of research on colloids aboard the space station.
Colloids are mixtures of tiny particles suspended in a liquid. They occur in many forms, including natural mixtures such as milk and muddy water, as well as a range of manufactured products from shampoo to medicine to salad dressing. Space station research has explored subjects such as stabilizing these mixtures and colloid behaviors that can be applied to products on Earth.
Studying colloids on Earth is complicated by gravity, which causes some particles to rise and others to sink. Microgravity removes that complication and makes possible research that can help companies design better products.
Fluid physics research: Fluid covers Earth, but sending fluids to space can help scientists better understand them. Space station fluid research began with the fundamental analysis of how fluids behave in microgravity. That research has evolved into the testing of advanced medical devices and heat transfer systems.
Rodent Research-6 tested tiny nanofluidic devices that, when implanted under the skin, could allow for the continuous delivery of drugs into a patient’s system. This process reduces the need for frequent injections or pills. A series of experiments used microgravity to study capillary forces – small forces that move a fluid along a narrow tube. Systems using capillary forces can be simpler because they rely on shapes and fluid dynamics rather than machinery to move liquid.
3D printing in microgravity: Testing printers on the station paves the way for future space missions to be more independent of Earth. Needed items could be 3D printed rather than sent from Earth and carried for the entire journey.
The first 3D printer flew to the space station in 2014. Developed by Made in Space, the printer produced dozens of parts that researchers analyzed and compared with those made on the ground. Analysis revealed that microgravity had no significant effects on the process, demonstrating that a 3D printer works normally in space.
Later experiments used recycled plastic to print objects and a specialized bioprinter to print human tissue. The BioFabrication Facility took small steps toward printing human organs and tissues in microgravity, using ultrafine layers of bioink. Printing human tissue is a part of a long-term plan to manufacture entire human organs in space using refined biological 3D-printing techniques. This effort could help provide increased access to organs for transplants on Earth.
Responding to natural disasters: With handheld camera imagery as a core component, the station has become an active participant in orbital data collection to support disaster response activities both within the U.S. and abroad. Astronauts snap images of disasters such as storms and fires throughout their progression, documenting cloud cover, flooding, and changes to the land. Pictures also are taken using mounted station cameras like the SS-HDTV and HDTV-EF2. SS-HDTV, developed to take night images of Earth, can be used to check if power has been restored to cities after a disaster.
The Lightning Imaging Sensor mounted on the station also detects the distribution and variability of lightning in order to improve severe weather forecasting. The ISS SERVIR Environmental Research and Visualization System has helped developing countries enhance their environmental decision-making processes.
Facial Recognition System in Use at 2 Redstone Gates
By Jonathan Stinson
Redstone Arsenal began a pilot program March 15 using facial recognition software to grant access to members of the workforce, including team members at NASA’s Marshall Space Flight Center.
Cameras are installed at lane 3 of Gate 1 on Martin Road East, and lanes 3 and 4 of Gate 9 on Rideout Road. These lanes are marked with the letters “SOV,” which stands for single-occupancy vehicle. Drivers carrying passengers, even if the driver is a trusted traveler, must use one of the other lanes.
Marshall team members who registered themselves in the arsenal’s Automated Installation Entry System at the Gate 9 Visitor Control Center are authorized to use the facial recognition lanes. All other team members should avoid the newly marked lanes.
“The process to register all Marshall employees and contractors for the Automated Installation Entry System is still being worked with the arsenal and more information will be distributed as it is available,” said Bill Marks, deputy director of Marshall’s Office of Center Operations. “Team members should not go to the visitor’s center to register unless specifically told to do so by their supervisor, and should continue through the non-facial recognition lanes by showing their NASA badge as usual until further notice.”
The facial recognition software works by scanning a motorist’s facial features through their windshield and comparing with the operator’s photo on file with the Automated Installation Entry System.
“The facial recognition lanes provide rapid and continuous vetting and a nonstop transition through the access control point,” said Ron Thomas, director of operations for the U.S. Army Garrison.
Motorists should ensure that they are not wearing any facial or head coverings – such as masks, hats, and sunglasses – that would obscure the scan. Also, heavily tinted windshields or dashboards cluttered with items like GPS devices and cellphone holders that might obscure the driver’s face can adversely affect the system. According to officials, prescription glasses needed for driving should be worn, but might interfere with the system. If so, the driver should stop and have the guard scan their common access card or view their NASA badge.
When approaching the gate, motorists should maintain about two car lengths between their vehicle and the car in front of them and travel 3-5 mph. Drivers are also asked to keep their driver-side window down while passing through the gate so a guard can see the driver.
Motorists will know they’ve been granted access when the red X above the card station turns into a green arrow. If the red X remains throughout the approach, then the driver must stop and engage with the guard, who will verify the driver’s access credentials. According to officials, the most common reasons for not getting a green arrow are if the driver is not registered, they do not have a valid photo on file, or if the system is impeded from scanning facial features.
Motorcyclists and bicyclists should not use the single-occupancy lanes.
Stinson is assistant editor of Redstone Arsenal’s Redstone Rocket. Marshall Star editor Daniel Boyette, an LSINC Corporation employee, contributed to this story.
Reclusive Neutron Star May Have Been Found in Famous Supernova
Since astronomers captured the bright explosion of a star on February 24, 1987, researchers have been searching for the squashed stellar core that should have been left behind. A group of astronomers using data from NASA space missions and ground-based telescopes may have finally found it.
As the first supernova visible with the naked eye in about 400 years, Supernova 1987A, or SN 1987A, sparked great excitement among scientists and soon became one of the most studied objects in the sky. The supernova is located in the Large Magellanic Cloud, a small companion galaxy to the Milky Way, only about 170,000 light-years from Earth.
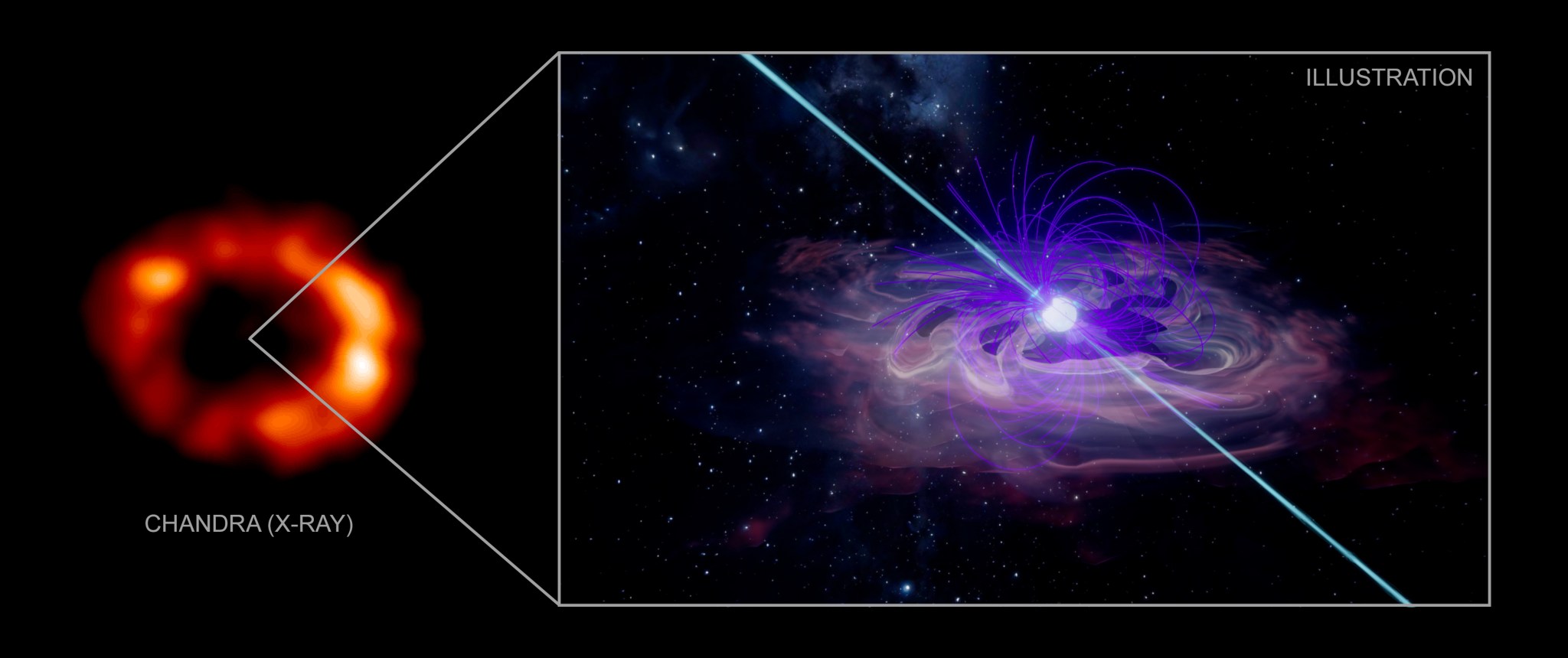
While astronomers watched debris explode outward from the site of the detonation, they also looked for what should have remained of the star’s core: a neutron star.
Data from NASA’s Chandra X-ray Observatory and previously unpublished data from NASA’s Nuclear Spectroscopic Telescope Array, or NuSTAR, in combination with data from the ground-based Atacama Large Millimeter Array, or ALMA, reported last year, now present an intriguing collection of evidence for the presence of the neutron star at the center of SN 1987A.
“For 34 years, astronomers have been sifting through the stellar debris of SN 1987A to find the neutron star we expect to be there,” said the leader of the study, Emanuele Greco, of the University of Palermo in Italy. “There have been lots of hints that have turned out to be dead ends, but we think our latest results could be different.”
When a star explodes, it collapses onto itself before the outer layers are blasted into space. The compression of the core turns it into an extraordinarily dense object, with the mass of the Sun squeezed into an object only about 10 miles across. These objects have been dubbed neutron stars, because they are made nearly exclusively of densely packed neutrons. They are laboratories of extreme physics that cannot be duplicated on Earth.
Rapidly rotating and highly magnetized neutron stars, called pulsars, produce a lighthouse-like beam of radiation that astronomers detect as pulses when its rotation sweeps the beam across the sky. There is a subset of pulsars that produce winds from their surfaces – sometimes at nearly the speed of light – that create intricate structures of charged particles and magnetic fields known as pulsar wind nebulae.
With Chandra and NuSTAR, the team found relatively low-energy X-rays from SN 1987A’s debris crashing into surrounding material. The team also found evidence of high-energy particles using NuSTAR’s ability to detect more energetic X-rays.
There are two likely explanations for this energetic X-ray emission: either a pulsar wind nebula, or particles being accelerated to high energies by the blast wave of the explosion. The latter effect doesn’t require the presence of a pulsar and occurs over much larger distances from the center of the explosion.
The latest X-ray study supports the case for the pulsar wind nebula – meaning the neutron star must be there – by arguing on a couple of fronts against the scenario of blast wave acceleration. First, the brightness of the higher energy X-rays remained about the same between 2012 and 2014, while the radio emission detected with the Australia Telescope Compact Array increased. This goes against expectations for the blast wave scenario. Next, authors estimate it would take almost 400 years to accelerate the electrons up to the highest energies seen in the NuSTAR data, which is over 10 times older than the age of the remnant.
“Astronomers have wondered if not enough time has passed for a pulsar to form, or even if SN 1987A created a black hole,” said co-author Marco Miceli, also from the University of Palermo. “This has been an ongoing mystery for a few decades and we are very excited to bring new information to the table with this result.”
If this is indeed a pulsar at the center of SN 1987A, it would be the youngest one ever found.
NASA’s Marshall Space Flight Center manages the Chandra program. The Smithsonian Astrophysical Observatory’s Chandra X-ray Center controls science from Cambridge Massachusetts and flight operations from Burlington, Massachusetts.
NuSTAR is a Small Explorer mission led by the California Institute of Technology and managed by NASA’s Jet Propulsion Laboratory for the agency’s Science Mission Directorate. NuSTAR was developed in partnership with the Danish Technical University and the Italian Space Agency, which provides the mission’s ground station and a mirror archive. NuSTAR’s mission operations center is at the University of California, Berkeley, and the official data archive is at NASA’s High Energy Astrophysics Science Archive Research Center.
Read the entire feature here.
Read more about Chandra here. For more Chandra images, multimedia, and related materials, visit here.
This Week in NASA History: Space Shuttle Enterprise Arrives at Marshall for Vibration Testing – Mar. 18, 1978
This week in 1978, the space shuttle Enterprise arrived at NASA’s Marshall Space Flight Center for mated vertical ground vibration testing, which marked the first time the entire shuttle compliment – orbiter, external tank, and solid rocket boosters – were mated vertically. Here, Enterprise is offloaded at Redstone Arsenal Airfield before being moved to Marshall’s Dynamic Test Stand. Today, Marshall is playing a vital role in the Artemis program by developing the Space Launch System, the backbone of NASA’s exploration plans and the only rocket capable of sending humans to the Moon and Mars. The NASA History Program is responsible for generating, disseminating, and preserving NASA’s remarkable history and providing a comprehensive understanding of the institutional, cultural, social, political, economic, technological, and scientific aspects of NASA’s activities in aeronautics and space. For more pictures like this one and to connect to NASA’s history, visit the Marshall History Program’s webpage. (NASA)