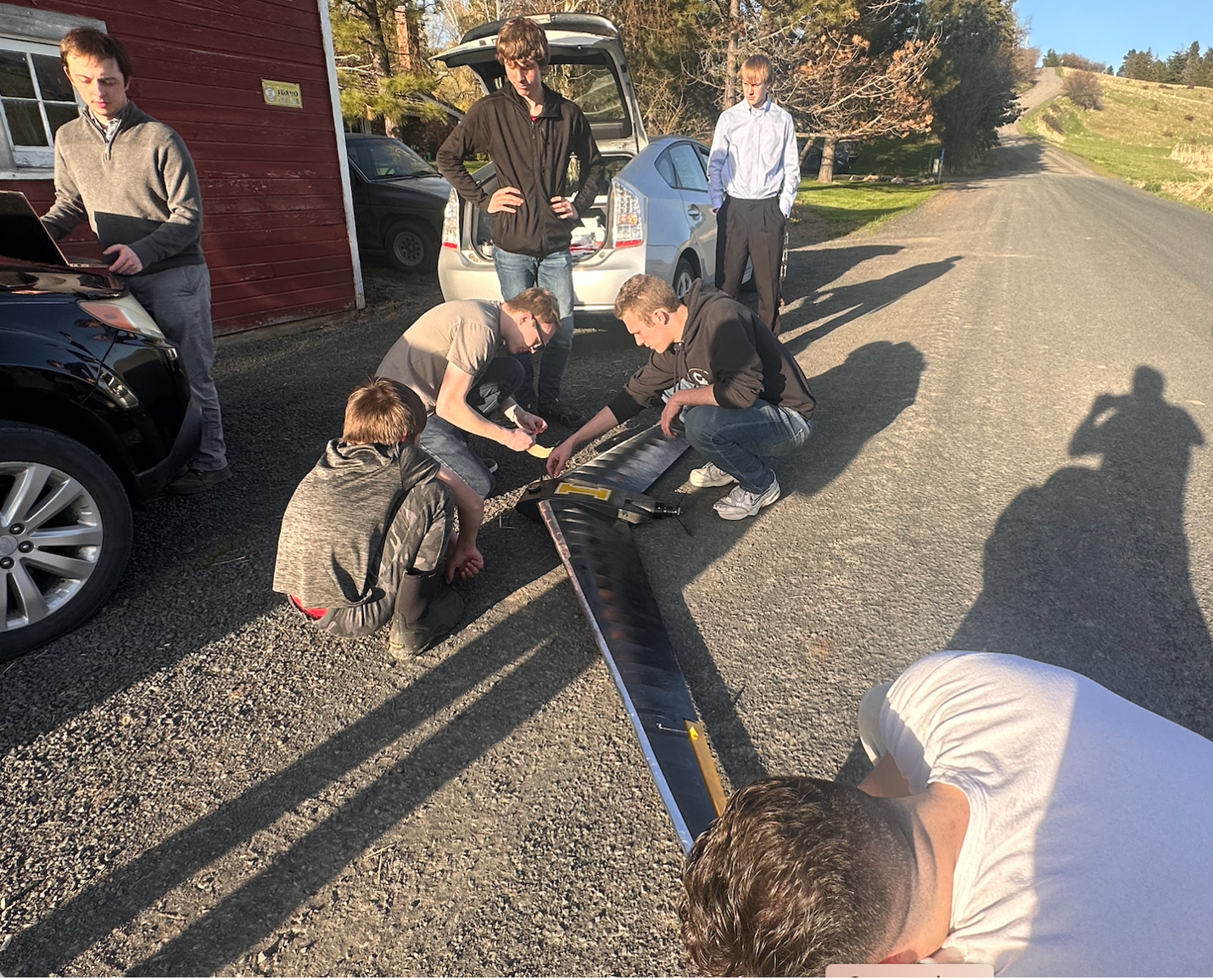
University of Idaho students learned real-world engineering skills during the 2022-2023 school year while advancing two NASA technologies – a tailless aircraft design using wing twists to maneuver, and a process to assemble thin-film solar panels using robotics and 3D printing.
One group of students designed, built, and flight-tested a drone using the Prandtl-D, Preliminary Research Aerodynamic Design to Lower Drag, developed at NASA’s Armstrong Flight Research Center in Edwards, California. Looking like a boomerang, the Prandtl design mimics bird flight, using twists in its wingtips for maneuvering.
The students said their work is a first step in proving the commercial viability of the Prandtl-D, which could have such uses as watching over farmland and spotting wildfires.
The students set goals for their airplane of a minimum speed of 30 mph, a maximum speed of 50 mph, a carrying capacity of at least one pound, and the ability to fly for at least an hour.
Their battery-powered, 11-foot airplane made from Balsa wood, carbon fibers, and organic materials surpassed their goals, having a stall speed, the minimum speed needed for controllable flight, of 28 mph, hitting a top speed during testing of 55 mph. The airplane stayed aloft for 118 minutes, nearly doubling their goal, and carried a 1.5-pound payload that included a flight controller and a camera.
The aircraft, ground launched by a bungee cord, made nine flights, during which the team noticed vibration at the higher cruise speeds. A future team will work to address that issue.
The students shared that, “the Prandtl-D wing design is commercially viable,” in a report at a recent engineering expo held at the university. “The airfoil produces an excellent platform for a wide variety of UAV applications through increased efficiency, stability, and control simplicity.”
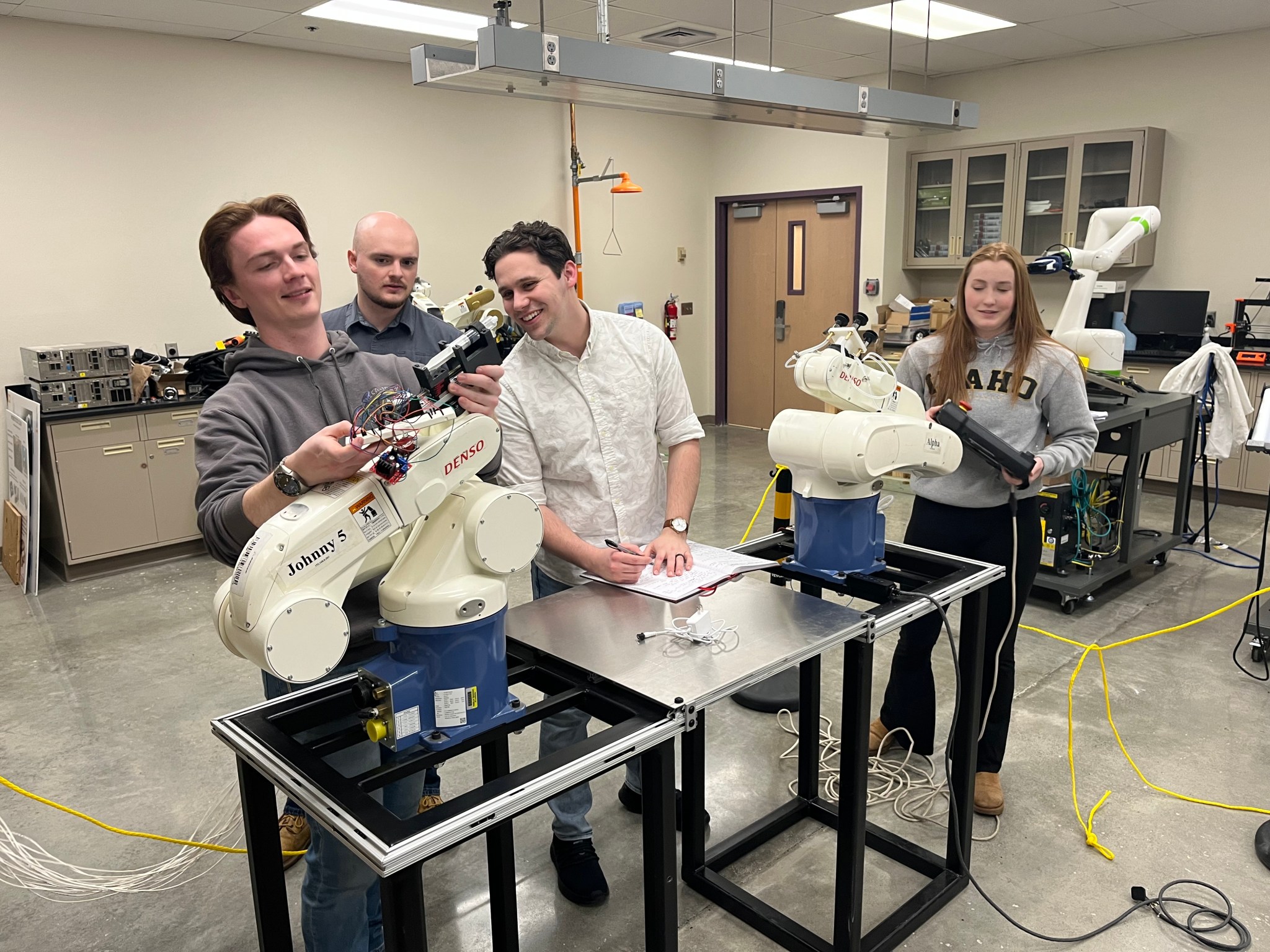
A second group of students worked with technology called PAPA, or Print-Assisted Photovoltaic Assembly, developed at NASA’s Marshall Space Flight Center in Huntsville, Alabama. The students designed and demonstrated an automated assembly process for turning thin-film solar cells into larger photovoltaic arrays using two robotic arms working in tandem. NASA is eyeing the use of such thin-film cells to power spacecraft and could even use the technology for creating solar arrays in space, enabling long-term spaceflight. The cost to build such arrays is about $450 per kilowatt while an automated process can cut the cost to $25 per kilowatt and eliminate human errors.
The students used PAPA to accomplish four tasks robotically including applying adhesive, placing the cells, printing the electronic connections between the cells, and adding a protective cover.
The students used substitute materials that mimicked the real materials but cheaper, allowing for more testing. The students had to tackle challenges such as cell breaking during placement and getting the adhesive applied consistently.
The students wanted the robotic arms to complete the assembly process without human intervention and to do it under 35 minutes. They achieved both goals, with the assembly process taking about nine minutes without any operator intervention.
The university was able to provide the hands-on engineering experiences to the students thanks to NASA’s Technology Transfer University, or T2U, which connects universities with NASA-developed technologies.
“This one of the best examples of what T2U can be,” said Brian Boogaard, NASA Armstrong’s T2U representative. “You’ve got a highly motivated faculty and you have really sharp students. The students built a lot of technology, they did a lot of great documentation, great design work, and a lot of good testing. It went really well.”
Students in the 2023-2024 school year will be able to pick up both projects and continue to develop the technologies, pushing them even closer to being ready for the marketplace.
“This is helping advance the art of the technology,” Boogaard said. “It’s also giving a bunch of students who are about to hit the workforce the ability to get their hands on this technology.”
To learn more about NASA’s T2U program, visit: https://technology.nasa.gov/t2u