An ensemble of microscopes, medical-style equipment, and other 3D scanners is providing insights that could help human and robotic explorers survive the harsh environments of deep space, the Moon, Mars and beyond.
Earth’s atmosphere protects us from the threat of tiny meteors – micro-meteorites no bigger around than the thickness of a fingernail and traveling faster than a speeding bullet – because they burn up in our atmosphere. However, explorers traveling beyond our protective blanket of air need strategies to protect from micro-meteorites collisions, as well as technologies to evaluate the damage they can cause.
“Studying micrometeorite impacts in lunar samples helps to find materials and methods to build habitats and protective gear for future Moon and Mars explorers,” Materials Scientist Dr. Justin Jones said. At NASA’s Goddard Space Flight Center in Greenbelt, Maryland, Jones has spent the last several years investigating a variety of 3D scanning technologies, most recently for their ability to analyze tiny micro-meteorite impact craters on Apollo-era Moon samples. He obtained high-resolution 3D scans (i.e., as micro-topographic maps) and measurements of the so-called zap pits, or micro-craters left behind by these collisions.
As NASA considers long-term exploration of the Moon, Mars, and beyond, in-situ resources found in those environments will be used to build shelters and provide building materials as well as other resources such as water and oxygen to sustain our explorers. Jones’ work focused on technologies allowing explorers and scientists to examine and even look inside a material without destroying it. These non-destructive scanning technologies will also help evaluate the strength and suitability of items made in space and the materials and samples found on other worlds.
His team, including Goddard Chief Scientist James Garvin and Materials Engineer Stephen Lebair, examined and cataloged dozens of zap pits in the Moon samples while evaluating the strengths and weaknesses of different technologies for assessing materials, responses, and damages.
They found laser confocal microscopy (LCM) performed better at characterizing the shape and form of the zap pits, Lebair said. The confocal microscope focuses a laser in a tight spot, one depth-level at a time, allowing finer spatial resolution than other technologies.
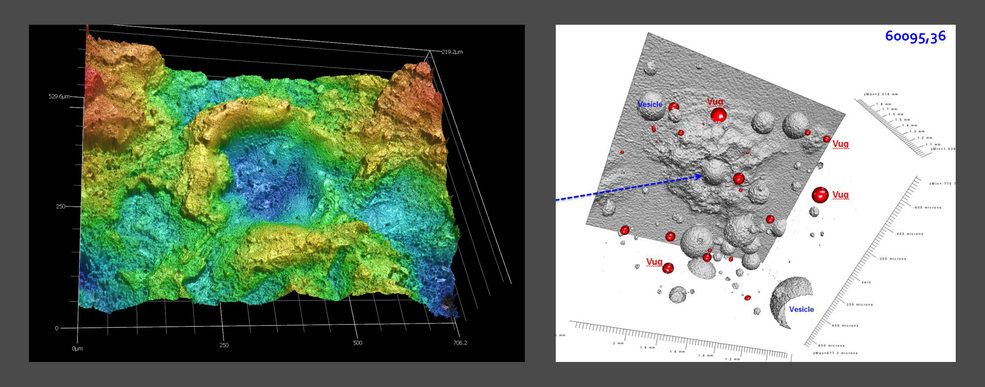
“Scanning electron microscopy (SEM) was the best imaging technique,” Lebair said, “since you don’t have to worry about reflections or artifacts of optical microscopy.”
SEM scans the surface with a focused beam of electrons, which as an added benefit can interact with atoms in the sample. This interaction provides data on the composition of materials through a technique called energy dispersive X-ray spectroscopy, or EDX.
To look beneath the surface, X-ray computed tomography (xCT) reveals the depth and topology of the micrometeorite impact and stresses and deformation caused within the material, Jones said. In addition, it can determine the potential for future failure from equipment after an impact.
The deep imaging enabled by xCT can verify the structural suitability of tools 3D printed in space or shelters built using local materials.
“We want to know the best materials to use,” Jones said, “and how thick should we make these structures. If we’re looking at designing a structural material for habitats, clothing, or other protective materials, we need to understand the depth of an impact beyond what we can see on the surface.”
The xCT scans provide information that otherwise would require difficult, often destructive sample preparation such as cutting or the use of chemicals to analyze sub-surface structures, Jones said. Goddard’s laboratory xCT system provides details as small as a couple microns in size: several times smaller than a human hair.
The beauty and complexity of the images produced by these non-destructive scanners also illustrates the violent forces that turn stone to glass, create cavities within the surface, and even force tiny spheres of metal to coalesce within the surrounding material. Micrometeorite impacts are a commonplace reality on the Moon and in deep space, Jones said. “It is important for NASA to be able to rapidly identify and understand the extent of deformation and mechanisms involved with micrometeorite cratering. We also want to know how this extends to larger impacts out there.”
The International Space Station has an electron microscope as well as a one-sided xCT that can be used on one of its robotic arms to evaluate damage from micrometeorite or debris strikes.
Jones is working on a potential bread-box-sized CT scanner that could operate on the space station. These scanners must operate without the massive rotating ring used in current medical scanning technologies, which could disrupt the orbital platform’s stability. Jones’ project would use the instant on/off X-ray sources developed by Goddard Astrophysicist Keith Gendreau (CuttingEdge) to develop a scanner using few or no moving parts.
Non-destructive scanning can also help explorers select the best specimens to gather as scientific samples for return to Earth, Jones said, revealing some of their history, internal structure, and component materials.
“NASA’s Artemis Program will benefit from Jones’ work,” Garvin added, “as it plans lunar-surface-based systems for the human basecamp on the Moon.”
By Karl B. Hille
NASA’s Goddard Space Flight Center in Greenbelt, Md.