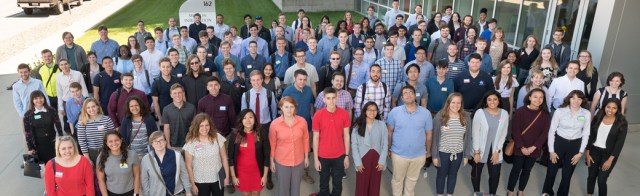
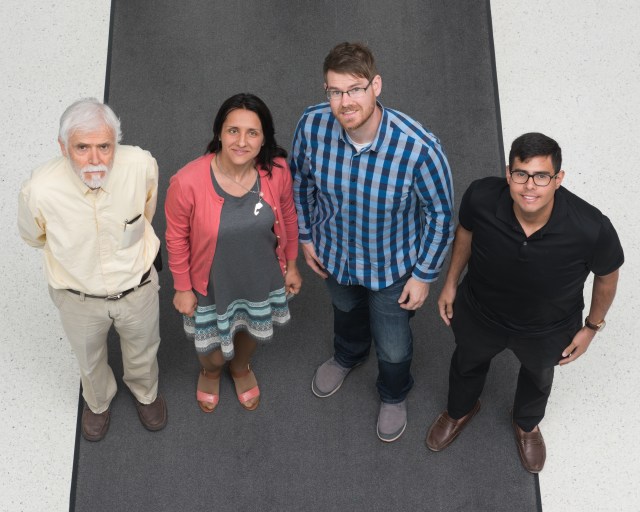
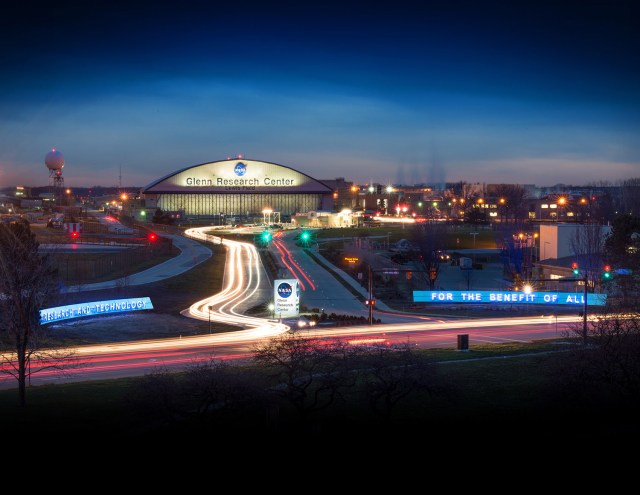
2024 NGFFP Additional Focused Areas
Research Area/Topic #1:
Propulsion, gas turbine combustion, transcritical fuel spray mixing
Description of Research Work to be performed:
1. Brief Background and NASA Mission/Program support:
The work in this project is supported by NASA’s Aeronautics Research Mission Directorate under the Transformational Tools and Technologies (TTT) Project where TTT helps to develop computational and experimental tools and technologies for predicting aircraft propulsion performance. In one part of this project specifically, the focus is on experimental, transcritical fuel spray mixing related to gas turbine combustion applications.
As gas turbine combustors move toward higher operating pressures and temperatures, the jet fuel injected into the combustor may transition from a classical spray of liquid droplets towards transcritical, diffusive mixing. Experimental imaging data were acquired to show the differences in mixing behaviors for relevant aviation fuels at conditions simulating gas turbine combustors. This data will further help understanding these mixing regimes and their effects on combustion performance. The data and resulting analysis can also help in the development and validation of future computational models.
2. Objective(s) of project:
An existing data set consists of thousands of shadowgraph-like images with droplets undergoing either classical or transcritical mixing. The goal of this project is focused on using and developing image analysis and/or machine learning tools to differentiate between classical and transcritical mixing regimes. Secondly, it is important to characterize and quantify the size and shape of the droplets in each mixing regime.
3. Specific faculty assignment:
The specific faculty assignment requires developing image analysis and/or machine learning tools to:
- Identifying droplets in the images and classifying each identified droplet as undergoing either classical mixing or transcritical mixing.
- Determining standard statistics of liquid droplet size distributions
- Quantifying shape measurements of transcritical fuel mixing (i.e. perimeter, aspect ratio, etc.)
4. Expected outcome(s) from assignment:
The expected outcomes from the assignment are:
- Developed methods, computer code scripts, and/or machine learning tools that:
- Accomplish the three tasks laid out in part 3
- Provide an organized workflow with written comments to guide future users
- A final report is expected at the end of the followship which shall:
- Document the details on the developed methods
- Summarize the results from the developed image analysis methods used on the existing data set
GRC Point-of-Contact:
Tyler Capil: tyler.g.capil@nasa.gov
Kathy Tacina: kathleen.m.tacina@nasa.gov
Applicable GRC Area (s) of Expertise:
Aircraft Propulsion
Research Area/Topic #2:
Mixed gas refrigerant study for integrating cryocoolers with large cryogenic tanks
Description of Research Work to be performed:
1. Brief Background and NASA Mission/Program support:
NASA is looking at the development of large cryocoolers for human space flight applications between 20 K and 120 K. In order to integrate cryocoolers onto a tank in microgravity and aid in the cooling of large surfaces and fluids within those surfaces, forced convection loops are required. These forced convection loops, when applied to a tank surface are called Broad Area Cooling. Usually there are two manifolds with some number of tubes attached to the tank in between the manifold, often this number of tubes can be greater than 10. There are two possible forced convection loops: if a stirling or pulse tube cryocooler is used, the forced convection loop consists of a small fan, a heat exchanger with the cryocooler cold head, and the tubing between the cryocooler and the tank and around the tank (see Fig A); if a reverse-Brayton cryocooler is used, the loop is a part of the cryocooler itself and the working fluid is used through the whole cycle, including the tubing on the tank (see Fig B). These cryocoolers are currently planned to be flown on the Human Landing System with Blue Origin and also for all Mars Transportation implementations.
2. Objective(s) of project:
In general, there are two fluids which are most frequently used as a working gas for cryocoolers, helium and neon, with helium being used more on the colder side and neon being used on the warmer side. Both fluids have their advantages and disadvantages and recently terrestrial systems have been using mixes of the two fluids. It is desired to investigate any advantages to mixed gases on the cycles discussed over the temperature ranges discussed. Analysis should assume 150 W of lift for the cryocooler sizing, parasitic heat losses along the tubing should be ignored.
3. Specific faculty assignment:
Investigations should focus on the modeling of the cryocooler systems using mixed gas refrigerants. Specifically:
- Reverse Brayton Cycle refrigeration:
- Between 20 K and 120 K
- With helium/neon mixtures between 0% helium and 100% helium
- Forced convection loops or oscillating heat pipes
- Between 20 K and 120 K
- With helium/neon mixtures between 0% helium and 100% helium
- Use of other novel gasses such as hydrogen that might improve performance
Analysis should focus on the following Key Performance Parameters:
- Pressure drop vs mass flow rate for a given flow configuration
- Mass/Heat transfer surface area required to exchange the heat between the working fluid and the tank wall
- Input power required for pumps/compressors/fans to circulate the fluid
4. Expected outcome(s) from assignment:
- Final Report detailing:
- Optimal mixture ratio as a function of temperature between 20 K and 120 K for both options using the given KPPs
- Sensitivity to mixture ratio as a function of temperatures between 20 K and 120 K for both options
- Monthly (or bi-monthly if preferred) updates with the grant overseer
- Specific analysis codes developed for this investigation
5. Final report is expected at the end of Fellowship
GRC Point-of-Contact:
Wesley Johnson: Wes.Johnson@nasa.gov
Ben Nugent: Benjamin.t.Nugent@nasa.gov
Applicable GRC Area (s) of Expertise:
Materials and Structures for Extreme Environments
Registration Application
Important Dates
Application period Opens: Monday, November 13, 2023
Application period closes: Sunday, January 14, 2024
Anticipated awardees announcement date: Friday, April 5, 2024
2024 session dates: June 3, 2024, to August 9, 2024
Note: extensions beyond the official 10-week Fellowship period may be granted, if deemed mutually beneficial and funding is available.
Contact Information
Ebony Moreen M.Ed. & MBA
Program Specialist – NASA Glenn Office of STEM Engagement
ebony.moreen@nasa.gov
Phone: (216) 433-6505
Glenn Research Center – Office of STEM Engagement
Phone: (216) 433-6505
Email: GRC-NGFFP@mail.nasa.gov
Latest Content
Stay up-to-date with the latest content from NASA as we explore the universe and discover more about our home planet.
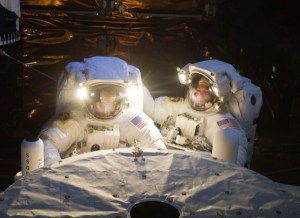
“Trying to do stellar observations from Earth is like trying to do birdwatching from the bottom of a lake.” James…
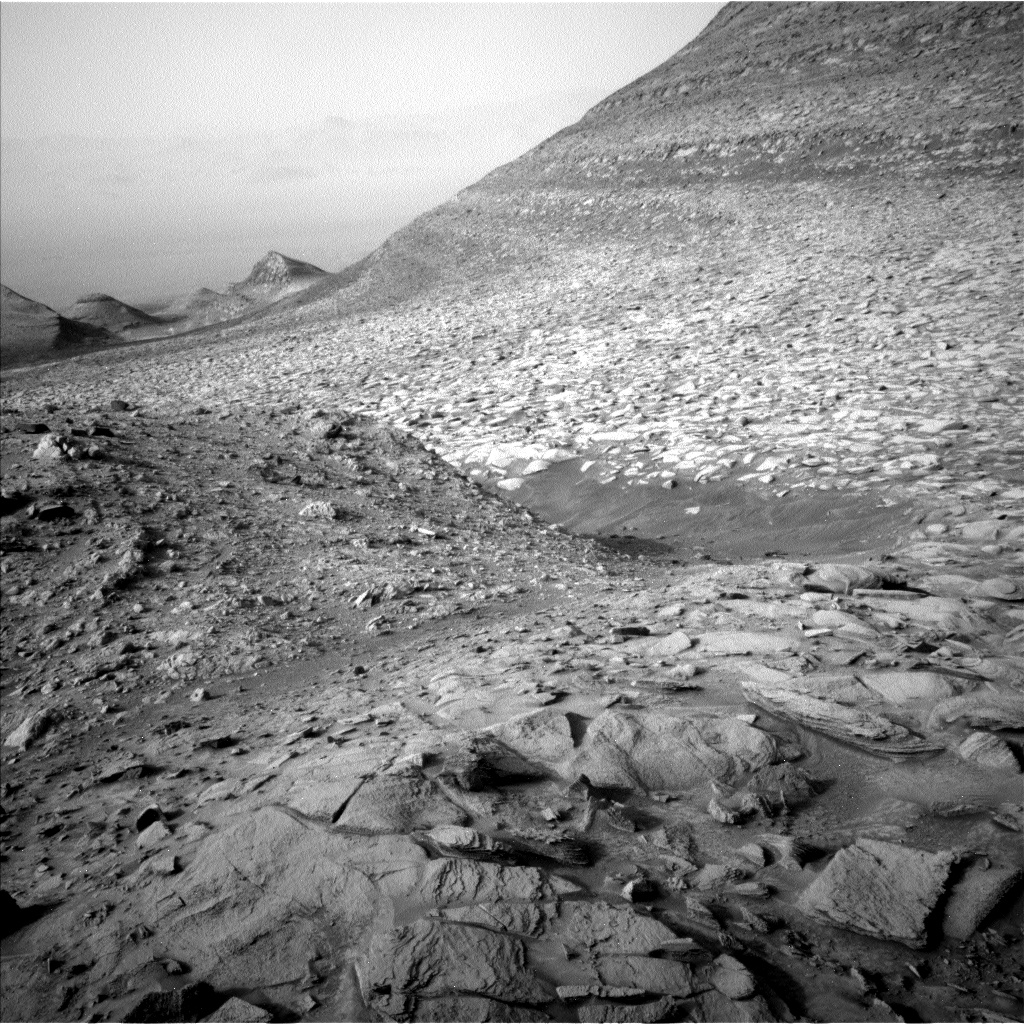
We planned quite a drive on Wednesday, with lots of twists and turns over very bumpy terrain, so the team…

The foundation is set at NASA’s Kennedy Space Center in Florida for launching crewed missions aboard the agency’s larger and…