In This Week’s Star
- NASA Proceeding to SLS Green Run Hot Fire
- Larry Leopard Named Marshall’s Associate Director, Technical; Mary Beth Koelbl Will Lead Engineering Directorate
- Ginger Flores Named Deputy Manager of Human Exploration Development & Operations Office
- John Vickers Named Senior Leader for Advanced and In-Space Manufacturing Capabilities
- Marshall Science Mission Among Four Selected for New NASA Pioneers Program
- NASA Completes Design Review of SLS Exploration Upper Stage
- Watch Crews Build the Launch Vehicle Stage Adapter for Artemis II
- This Week in NASA History: 1st RS-25 Engine Test of 2015 – Jan. 9, 2015
NASA Proceeding to SLS Green Run Hot Fire
NASA is targeting a two-hour test window that opens at 4 p.m. CST on Jan. 16, for the final test in the Space Launch System Green Run test series – the hot fire. The hot fire is the culmination of the Green Run test series, an eight-part test campaign that gradually brings the core stage of the agency’s SLS rocket to life for the first time.
NASA conducted the seventh test of the Green Run test series – the wet dress rehearsal – on Dec. 20 at NASA’s Stennis Space Center. The wet dress rehearsal test marked the first time cryogenic, or super cold, liquid propellant was fully loaded into and drained from the SLS core stage’s two huge tanks. The wet dress rehearsal provided structural and environmental data, verified the stage’s cryogenic storage capabilities, demonstrated software with the stage’s flight computers and avionics, and conducted functional checks of all the stage’s systems.
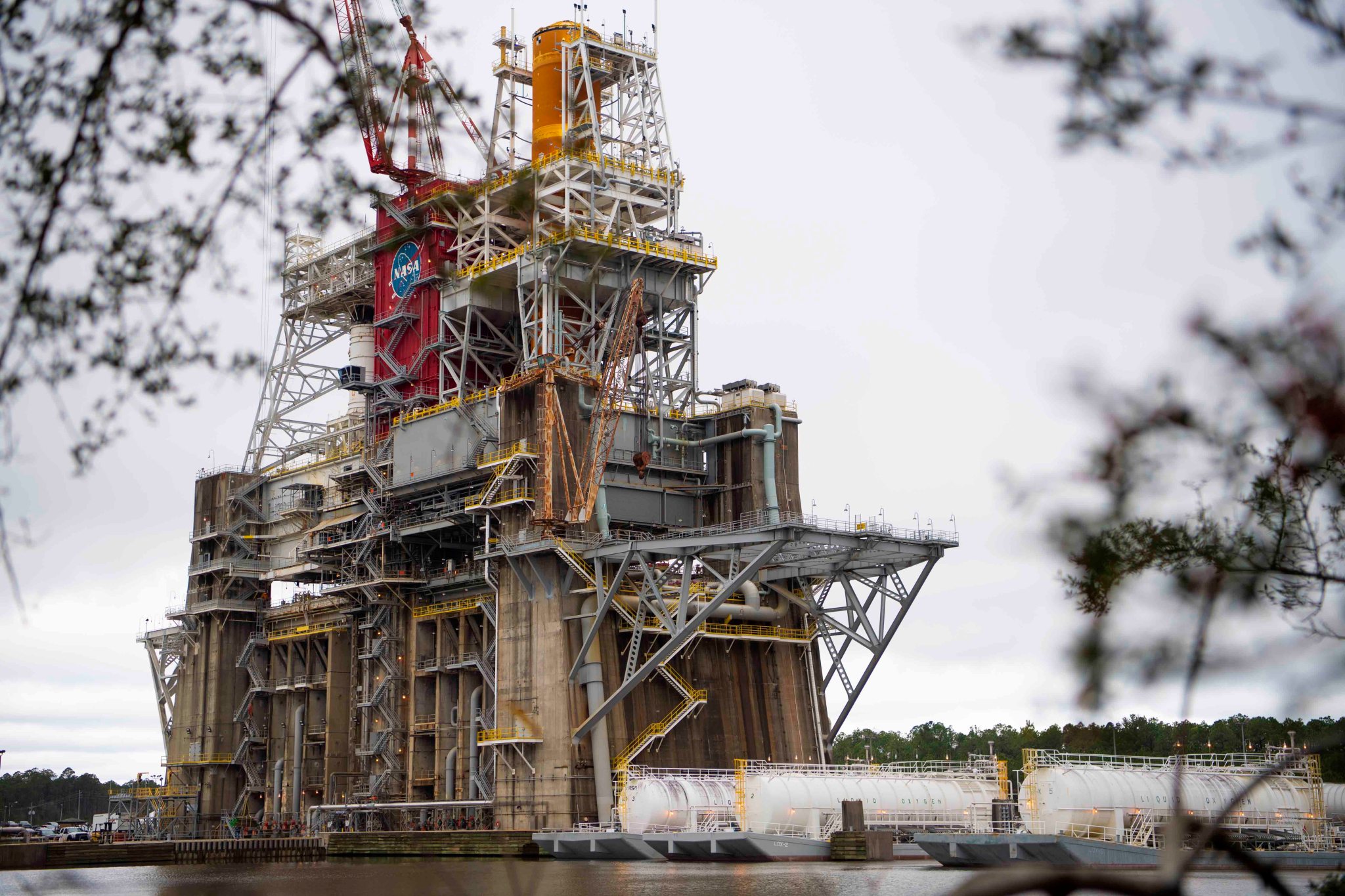
The end of the test was automatically stopped a few minutes early due to timing on a valve closure. Subsequent analysis of the data determined the valve’s predicted closure was off by a fraction of a second, and the hardware, software, and stage controller all performed properly to stop the test. The team has corrected the timing and is ready to proceed with the final test of the Green Run series.
“During our wet dress rehearsal Green Run test, the core stage, the stage controller, and the Green Run software all performed flawlessly, and there were no leaks when the tanks were fully loaded and replenished for approximately two hours,” said Julie Bassler, SLS Stages manager at NASA’s Marshall Space Flight Center. “Data from all the tests to data has given us the confidence to proceed with the hot fire.”
The upcoming hot fire test will fire all four of the stage’s RS-25 engines simultaneously for up to eight minutes to simulate the core stage’s performance during an Artemis launch.
Together with the four RS-25 engines and its twin solid rocket boosters, the SLS rocket produces 8.8 million pounds of thrust to send NASA’s Orion spacecraft, astronauts, and supplies beyond Earth’s orbit to the Moon. Offering more payload mass, volume capacity, and energy to speed missions through space, the SLS rocket — along with NASA’s Gateway in lunar orbit, the human landing system, and Orion — is part of NASA’s architecture for deep space exploration through the agency’s Artemis program. No other rocket is capable of carrying astronauts in Orion around the Moon in a single mission. For more information about SLS, visit https://www.nasa.gov/exploration/systems/sls/index.html Credits: NASA
“The next few days are critical in preparing the Artemis I rocket stage, the B-2 Test Stand at Stennis, and the test team for the finale of the Green Run test series,” said Barry Robinson, project manager for SLS core stage Green Run testing at Stennis. “The upcoming Green Run hot fire is the culmination of a lot of hard work by this team as we approach a key milestone event for NASA’s Artemis missions.”
After the firing at Stennis, the core stage for SLS will be refurbished and shipped on the agency’s Pegasus barge to NASA’s Kennedy Space Center. The stage will then be assembled with the other parts of the rocket as well as NASA’s Orion spacecraft in preparation for Artemis I.
Live hot fire coverage will begin at 3:20 p.m. on NASA Television and the agency’s website, followed by a post-test briefing approximately two hours after the test concludes.
For the latest on Green Run, visit the Artemis blog.
Larry Leopard Named Marshall’s Associate Director, Technical; Mary Beth Koelbl Will Lead Engineering Directorate
Larry Leopard has been appointed associate director, technical, of NASA’s Marshall Space Flight Center, following the retirement of Preston Jones. Mary Beth Koelbl succeeded Leopard as director of Marshall’s Engineering Directorate.
Leopard will provide expert advice in all facets of the center’s responsibilities by conducting special studies; providing authoritative advice and assistance in policy review; managing and reporting on centerwide and directorate metrics; and developing benchmarking strategies.
Leopard joined NASA in 1990. His early work at Marshall included contributions to space shuttle propulsion elements; the Space Shuttle Main Engine Technology Test Bed; Rocket-Based Combined Cycle propulsion technology; Fastrac 60K engine; International Space Station payloads, Environmental Control and Life Support Systems, and research facilities for the space station; small satellite technology demonstrations; and multiple science instruments. Since his appointment to the Senior Executive Service in 2008, Leopard has held several leadership roles within the Engineering Directorate – including deputy director of the Propulsion Systems Department, deputy and director of the Space Systems Department, Engineering Directorate deputy director and, most recently, director of the Engineering Directorate.
The Senior Executive Service is the personnel system that covers most of the top managerial, supervisory, and policy positions in the executive branch of the federal government.
Throughout her 33-year NASA career, Koelbl has worked in many Marshall organizations, supporting large, complex propulsion systems development and operations efforts for such NASA programs and projects as the Space Launch System, the world’s most powerful rocket set to carry American astronauts to the Moon and ultimately to Mars, NASA’s Commercial Crew Program and various planetary lander development activities. She also contributed to historic efforts such as the space shuttle main engine technology test bed, the Fastrac 60K engine, all shuttle propulsion elements, Altair and the Ares upper stage and upper stage engine.
Koelbl joined Marshall in 1986 as an aerospace engineer in the Turbomachinery and Combustion Devices Branch. She was named deputy group lead of the Engineering Directorate’s Engine Systems Engineering Group in 2000 and group leader in 2003. In 2005, following a center-wide reorganization, Koelbl was named branch chief of the Engine and Main Propulsion Systems Branch. She was promoted to division chief of the Propulsion Systems Division in 2011, and later that year was named to the Senior Executive Service position of deputy director of the Propulsion Systems Department. Most recently, she served as deputy of the Engineering Directorate.
A native of Iowa City, Iowa, Koelbl earned a bachelor’s degree in mechanical engineering in 1985 from the University of Iowa. She has been the recipient of many prestigious awards, including a NASA Exceptional Service Medal in 2018, a NASA Leadership Medal in 2007, a Space Flight Awareness Award in 2005 and a Silver Snoopy in 1996.
Ginger Flores Named Deputy Manager of Human Exploration Development & Operations Office
Ginger Flores has been named deputy manager of the Human Exploration Development & Operations Office at NASA’s Marshall Space Flight Center.
Flores, who was manager of the Habitation Systems Development Office since 2018, succeeds Joseph Pelfrey, who was recently named manager of Marshall’s Human Exploration Development & Operations Office. Flores is responsible for assisting Pelfrey in managing and implementing Marshall’s work portfolio in the areas of human exploration and transportation projects; habitation systems; payload and mission operations and integration; and project development and integration for International Space Station payloads, facilities, and environmental control and life support systems.
In 1991, Flores started her NASA career as a co-op student supporting the Engineering Cost Group in Program Development. She joined NASA as a civil servant in 2002 and worked as a lead cost engineer in Marshall’s Systems Management Office. Prior to joining NASA, she was a senior process engineer at Adtran Inc., supporting new products and technologies engineering.
In 2003, Flores moved to the Microgravity Research Program Office as the project manager for the Lab-On-a-Chip Application Development. She was responsible for managing both a space station payload project and a complementary technology development project. In 2006, she was named associate project manager at Marshall for the Orion service module element and was responsible for planning, directing, and implementing all Marshall project activities in support of NASA’s Glenn Research Center’s Service Module Project Office.
Flores accepted a detail assignment in 2007 as executive officer to the associate administrator for Program Analysis and Evaluation at NASA Headquarters.
She returned to Marshall in 2008 as project manager for the Microgravity Science Glovebox. In 2011, Flores was named team lead of the ISS Payload Projects Team in Marshall’s space station office.
In 2015, Flores was the acting deputy manager in the International Space Station Office. In 2016, she moved to Marshall’s Science and Technology Office to become acting deputy program manager and program manager for the Technology Demonstration Missions Program Office. As a manager within the Space Technology Mission Directorate, Flores developed and demonstrated space flight technologies that infused critical human exploration, science, and commercial space missions and met NASA’s strategic mission needs.
In 2019, Flores was appointed to the Senior Executive Service as manager of both the Habitation Systems Development Office and the Gateway habitation element. The Senior Executive Service is the personnel system covering most top managerial, supervisory, and policy positions in the executive branch of the federal government.
A native of Huntsville, Flores received both a bachelor’s and master’s degree in industrial and systems engineering, in 1993 and 1998 respectively, from the University of Alabama in Huntsville. She and her husband, Anthony, live in Huntsville.
John Vickers Named Senior Leader for Advanced and In-Space Manufacturing Capabilities
John Vickers has been appointed to the senior level position of senior leader for Advanced and In-Space Manufacturing Capabilities in the Materials and Processes Laboratory at NASA’s Marshall Space Flight Center.
Vickers will be responsible for stewardship of the center’s and NASA’s crucial crosscutting capabilities for advanced and in-space manufacturing and will lead NASA’s advanced manufacturing strategic technology development planning.
He joined Marshall in 1989 as a senior engineer in the Materials and Processes Laboratory. He has since served in positions of increasing scope and technical authority. In 2003, Vickers was named assistant manager of the Materials and Processes Laboratory and manager of the National Center for Advanced Manufacturing at NASA’s Michoud Assembly Facility.
From 2016 to his present assignment, Vickers concurrently worked as principal technologist for the areas of advanced materials and manufacturing in the Space Technology Mission Directorate at NASA Headquarters, associate director of Marshall’s Materials and Processes Laboratory, and NCAM manager. In addition, he was NASA’s representative to the National Science and Technology Council Subcommittee on Advanced Manufacturing and the Subcommittee on Critical Minerals.
Prior to his NASA career, Vickers worked with Thiokol Corp. of Ogden, Utah, in 1982, where he was responsible for materials properties testing for rocket and missile propulsion systems.
A native of Arab, Alabama, Vickers received a bachelor’s degree in industrial and systems engineering from the University of Alabama in Huntsville. He has received numerous awards, including the NASA Exceptional Service Medal, two NASA Outstanding Leadership Medals, Marshall Director’s commendation awards, Marshall Engineering Director’s award, and the American Institute of Aeronautics and Astronautics’ Holger Toftoy Award. He was also elected to the Society of Manufacturing Engineers College of Fellows.
Vickers and his wife, Lisa, have four children, four grandchildren, and reside in Arab.
Marshall Science Mission Among Four Selected for New NASA Pioneers Program
NASA has chosen four small-scale astrophysics missions – including one led at NASA’s Marshall Space Flight Center – for further concept development in a new program called Pioneers. Through small satellites and scientific balloons, these selections will enable new platforms for exploring cosmic phenomena such as galaxy evolution, exoplanets, high-energy neutrinos, and neutron star mergers.
“The principal investigators of these concept studies bring innovative, out-of-the-box thinking to the problem of how to do high-impact astrophysics experiments on a small budget,” said Thomas Zurbuchen, associate administrator of NASA’s Science Mission Directorate. “Each of the proposed experiments would do something no other NASA telescope or mission can do, filling important gaps in our understanding of the universe as a whole.”
Among them is the proposed StarBurst mission. Led by principal investigator Daniel Kocevski at Marshall, StarBurst is a smallsat instrument payload intended to detect high-energy gamma rays from powerful cosmic events – such as the mergers of neutron stars, or dense remnants of collapsed stars gone supernova. To date, only one such event has been observed simultaneously in gamma rays and gravitational waves. If approved, StarBurst could fly by 2024-25 and identify up to 10 gamma ray burst events per year.
“StarBurst will leverage a decade’s worth of technological advances to make science instrumentation lighter and more efficient,” Kocevski said. Building on findings by NASA’s Fermi Gamma-ray Space Telescope and the National Science Foundation’s Laser Interferometer Gravitational-wave Observatory, StarBurst could deliver data with up to five times the sensitivity of the Gamma-ray Burst Monitor, a key Fermi instrument designed two decades ago at Marshall.
Kocevski, a former doctoral research fellow at NASA’s Goddard Space Flight Center, joined NASA full-time in 2016 as a Marshall astrophysicist. He led development of the Fermi All-sky Variability data portal, which shares gamma ray flare data with astrophysics researchers around the world.
The other three concepts selected were:
- Aspera, a smallsat that will study galaxy evolution through observations in ultraviolet light, examining hot gas in the space between galaxies – the intergalactic medium – as well as the inflow and outflow of gas from galaxies. Carlos Vargas at the University of Arizona in Tucson is the principal investigator.
- Pandora is a smallsat that will study 29 exoplanets orbiting 20 stars in visible and infrared light to clarify sources of signals from stars and planetary atmospheres. Goddard’s Elisa Quintana is the principal investigator.
- PUEO is a high-altitude balloon mission designed to launch from Antarctica to detect signals from ultra-high energy neutrinos – particles that contain valuable clues about the highest energy astrophysical processes, including black hole creation and neutron star mergers. Abigail Vieregg of the University of Chicago is the principal investigator.
After additional definition, all four concept studies will undergo a concept study review before being approved for flight.
The Pioneers program provides opportunities for early-to-mid-career researchers to propose innovative experiments and lead space or suborbital science investigations for the first time. They must be creative in designing missions to keep expenses down, as the cost cap for a Pioneers mission is $20 million. The low price point is enabled in part by the flourishing smallsat industry for Earth observing and internet access, allowing researchers to purchase off-the-shelf spacecraft or make use of telescopes developed by other government agencies.
The program itself is an experiment for NASA. The agency has never solicited proposals for these kinds of astrophysics experiments at such low cost caps with such tight constraints. Some of the concepts may, upon further study, require a bigger budget, meaning they would not ultimately be approved for flight through the Pioneers program.
“We don’t know if there is great astrophysics that can be done in a $20 million satellite, but we challenged the community and they sent in a lot of innovative proposals,” said Paul Hertz, director of NASA’s astrophysics division at NASA Headquarters. “Now, we’re excited to see if they can deliver.”
NASA Completes Design Review of SLS Exploration Upper Stage
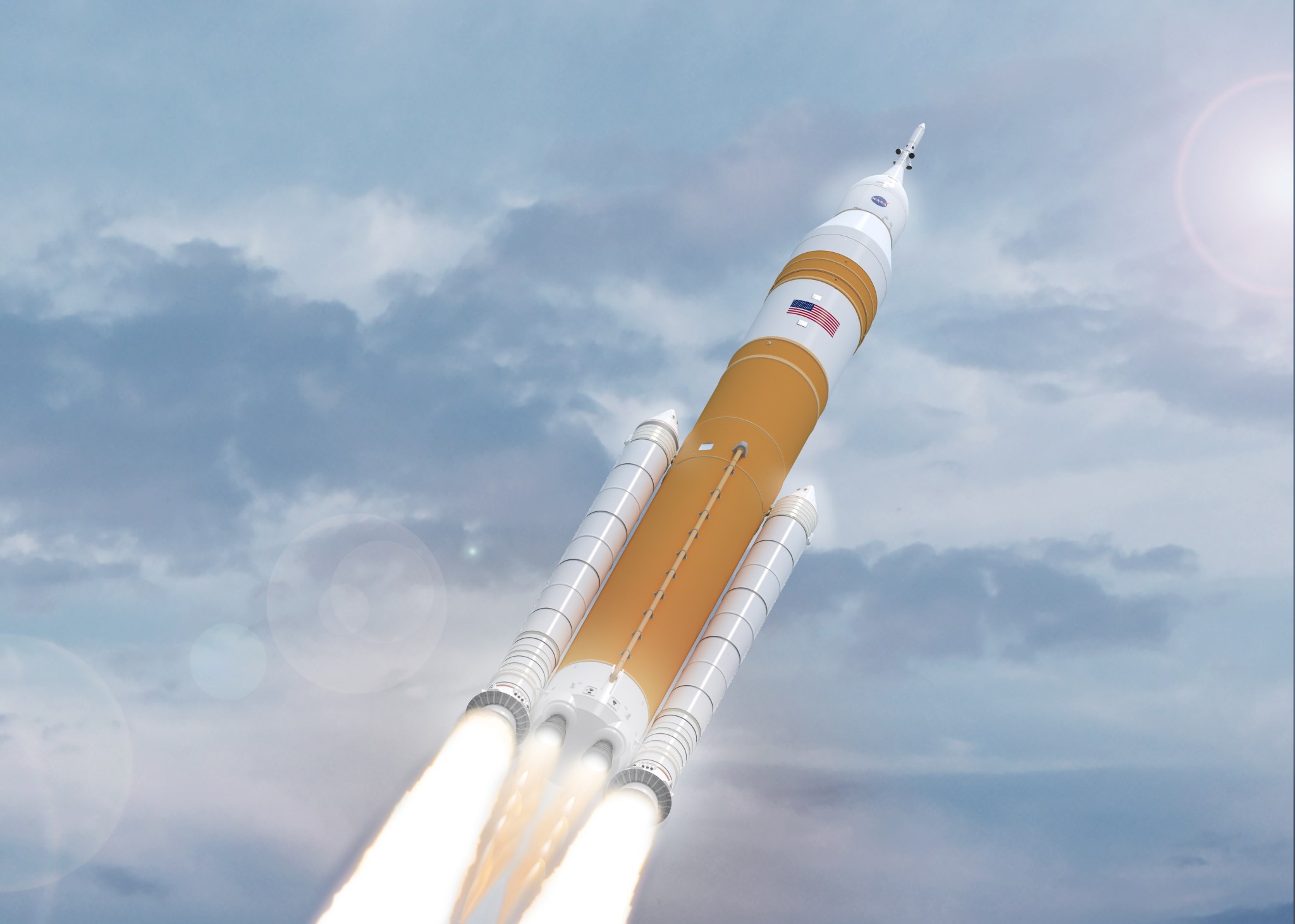
The Exploration Upper Stage for future flights of NASA’s Space Launch System rocket passed its critical design review Dec. 18. A panel of experts evaluated the Exploration Upper Stage in the latest review to determine that the stage’s design meets requirements for future missions. The assessment certifies the stage meets critical design requirements to withstand deep space environments and, when completed, will ensure astronaut safety. The review board also evaluated testing processes, the ability of the industrial base to supply parts and tooling, and production plans. Boeing, the prime contractor for the Exploration Upper Stage as well as the SLS core stage, will manufacture and assemble the upper stage at NASA’s Michoud Assembly Facility. A structural test article of the stage will undergo testing at NASA’s Marshall Space Flight Center. (NASA/Terry White)
Watch Crews Build the Launch Vehicle Stage Adapter for Artemis II
This video shows how crews at NASA’s Marshall Space Flight Center are manufacturing and assembling the launch vehicle stage adapter for the second flight of NASA’s Space Launch System rocket. The launch vehicle stage adapter in this video will be used for Artemis II, the first crewed mission of NASA’s Artemis program. The cone-shaped piece of hardware connects the rocket’s upper and lower stages. The launch vehicle stage adapter is welded together as two unique cones, then stacked on top of one another. Technicians recently moved the aft cone to begin welding the adapter at Marshall. While the larger stages of the SLS rocket are manufactured at other NASA facilities, the launch vehicle stage adapter flight hardware is produced exclusively at Marshall by Teledyne Brown Engineering in Huntsville. For more information about SLS, visit here.
This Week in NASA History: 1st RS-25 Engine Test of 2015 – Jan. 9, 2015
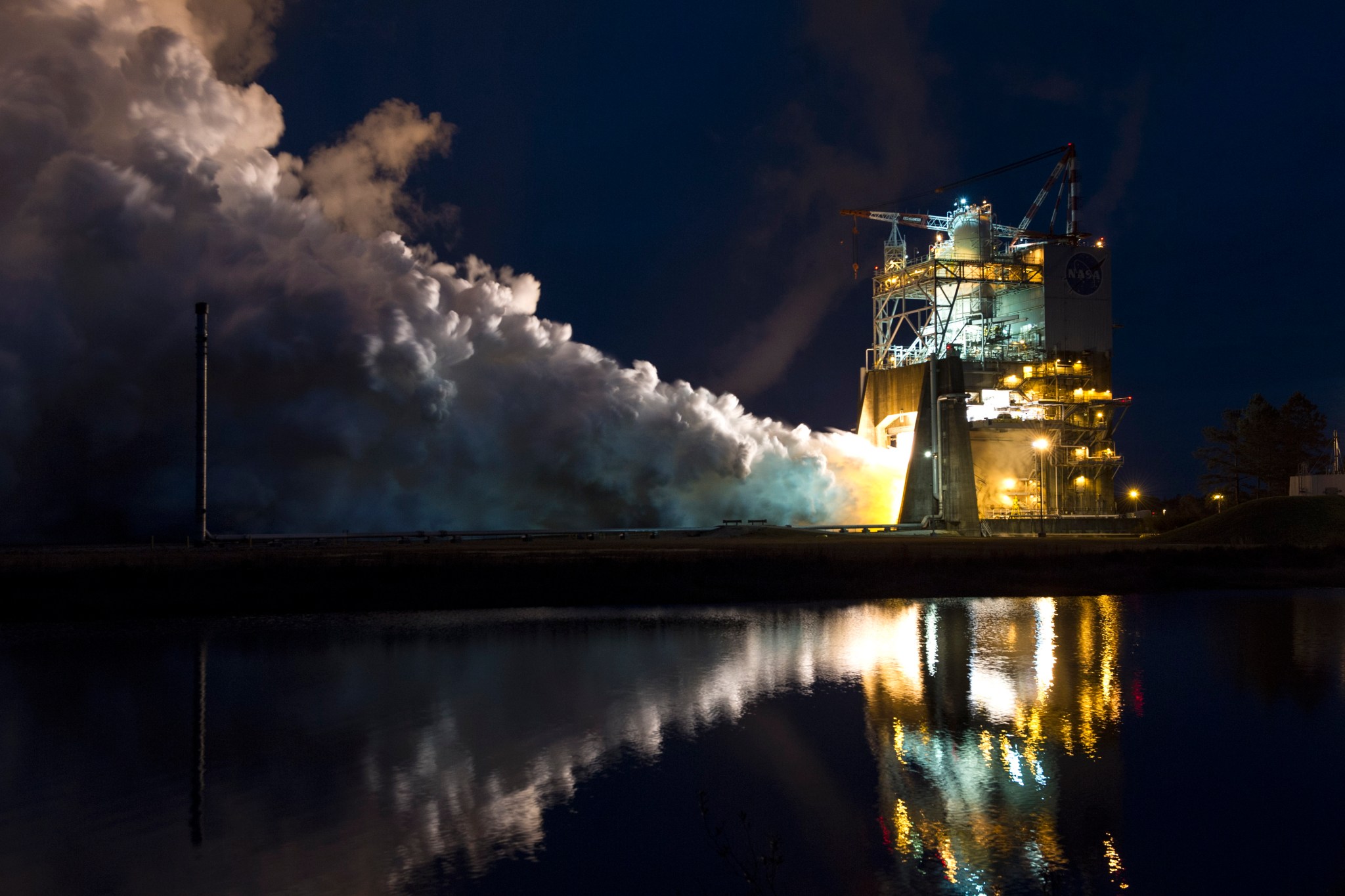
This week in 2015, NASA engineers successfully conducted the first hot fire test of the RS-25 engine and engine controller unit on the A-1 test stand at NASA’s Stennis Space Center. This was the first of eight tests for the development of the engine designed to provide NASA engineers with critical data on the engine controller unit and inlet pressure conditions. Today, NASA’s Marshall Space Flight Center is playing a vital role in the Artemis program by developing the Space Launch System, the backbone of NASA’s exploration plans and the only rocket capable of sending humans to the Moon and Mars. The NASA History Program is responsible for generating, disseminating, and preserving NASA’s remarkable history and providing a comprehensive understanding of the institutional, cultural, social, political, economic, technological, and scientific aspects of NASA’s activities in aeronautics and space. For more pictures like this one and to connect to NASA’s history, visit the Marshall History Program’s webpage. (NASA)