In This Week’s Star
- NASA’s David Beaman Helps Prepare Super Heavy-Lift Rocket for Flight
- NASA’s Super Guppy Delivers Rocket Test Article to Marshall
- Lead-up to Launch: NASA Pegasus Barge Crew
- Markings on SLS Provide a Different View of the Artemis I Launch
- Launching Science, Technology on NASA’s Artemis I Mission
- Seven Teams Advance in NASA’s $5M Watts on the Moon Challenge
- Interns Cap Summer Session with Exit Presentations
NASA’s David Beaman Helps Prepare Super Heavy-Lift Rocket for Flight
By Rick Smith
NASA engineer David Beaman thinks like a chess grandmaster, always three or four moves ahead. He oversees 1,000 or so team members – all of them working to fly America’s next deep space rocket and return human explorers to the Moon on the Artemis missions..
Beaman is manager of the Space Launch System (SLS) Engineering & Integration Office at NASA’s Marshall Space Flight Center. As NASA works to deliver the SLS – the first Moon rocket built for humans since the Apollo era, and the most powerful ever built – his office provides a full range of engineering oversight and integration solutions serving NASA space science and exploration missions.
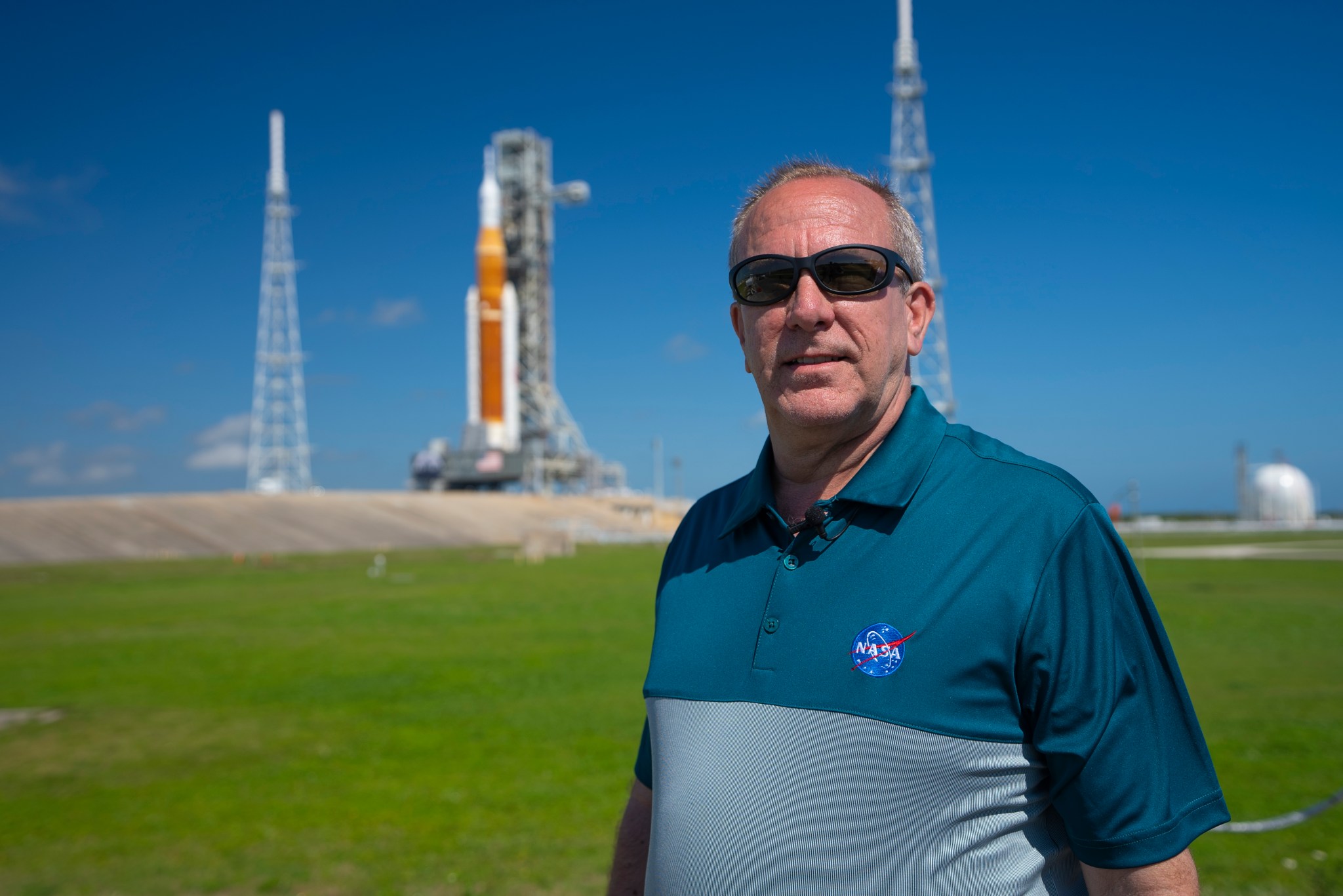
And the chess analogy is no accident; Beaman and his team are always thinking multiple steps ahead, juggling a variety of pieces and countless potential interactions. “We’re responsible for overall requirements and processes for the entire SLS rocket – how they’re implemented at every stage, from design to launch, and how they flow between the element level and the integrated launch vehicle, including the Orion crew vehicle, engineering ground systems and the rocket itself,” he said.
The Engineering & Integration Office conducts hardware and systems analysis for each piece of the rocket – and will do so for the integrated launch vehicle during final checkout and launch preparations. The organization also develops all SLS flight software. Some 300 people in Marshall’s Systems Integration Laboratory conduct exhaustive software modeling and simulation work, Beaman said, “testing vehicle safety margins, putting the rocket through its paces with different launch windows, trajectories and payload mass.”
The team works with operations and ground teams at NASA’s Johnson Space Center and Kennedy Space Center to ensure proper communications between elements and with controllers on the ground. They plan and oversee flight configurations for each launch – countless combinations of mass, hardware, crew, mission and operational constraints. Beaman – who managed the solid rocket boosters for the final 22 space shuttle missions and knows very well how one vehicle element fits into a much bigger picture – likened the task to planning long journeys here on Earth.
“You have a truck that carries 5 tons of sand,” he said. “Your mission is to haul the load from Alabama to Boston. How long is the trip? How often do you need to refuel? How many drivers are needed? Just as all those factors amount to a successful trip, we execute our mission not just by building and flying a safe, reliable rocket, but by factoring in all those operational constraints. This is the very heart of the process.”
Beaman, who grew up in Huntsville, gets his passion for space from his father, Robert Beaman, an early Apollo engineer who helped build the Saturn rockets that carried the first Americans to the Moon. The elder Beaman retired from NASA in 1997 as Marshall’s chief engineer – leaving his son to carry on his legacy.
Beaman earned a bachelor’s degree in electrical engineering in 1990 from the University of Alabama in Huntsville. Prior to joining NASA in 2000, he was a contractor supporting U.S. Army research and development programs at Redstone Arsenal. In 1990, he accepted a position with United Technology and later with United Space Alliance, both of Huntsville, supporting NASA’s Advanced Solid Rocket Motor Program and the Solid Rocket Booster Project.
He was an integral member of Marshall’s Space Shuttle Program, leading various offices from 2002 to 2011. When the shuttle program ended in 2011 and NASA began building SLS, Beaman was named manager of Marshall’s Spacecraft and Payload Integration Office. Marshall Director Jody Singer asked him to assume his current role in 2019.
Beaman is a 2004 recipient of the NASA Medal for Exceptional Achievement, and a 2005 Space Flight Awareness honoree in 2005 for his dedication to quality work and flight safety. He and his wife, Mishele, live in Meridianville. They have two grown sons, Zack and Seth.
Smith, a Manufacturing Technical Solutions employee, supports Marshall’s Office of Strategic Analysis & Communications.
NASA’s Super Guppy Delivers Rocket Test Article to Marshall
Teams at NASA’s Marshall Space Flight Center unloaded the Orion stage adapter (OSA) structural test article from NASA’s Super Guppy cargo airplane Aug. 10.
The Super Guppy is capable of hauling loads of more than 48,000 pounds and boasts a cargo compartment 25 feet tall, 25 feet wide, and 111 feet long. Its unique, hinged nose can open to 110 degrees, allowing NASA teams to load and unload large hardware pieces and other oversized cargo from the front end of the craft.
Engineers at Marshall designed and built the OSA test article to help prepare the agency’s Space Launch System (SLS) rocket for flight. The 5-foot-tall, 18-foot-diameter test article is structurally identical to the flight version of the Orion stage adapter, which connects the rocket’s interim cryogenic propulsion stage to the Orion spacecraft. The test article will be stored at Marshall, where it will continue to serve as an engineering resource.
The flight version of the Orion stage adapter is integrated with the SLS rocket and awaiting its maiden spaceflight during NASA’s Artemis I mission, scheduled to launch no earlier than Aug. 29 The Artemis I OSA will deploy 10 CubeSats, or small satellites, to conduct various science and technology demonstrations in deep space.
Through Artemis missions, NASA will land the first woman and the first person of color on the Moon, paving the way for a long-term lunar presence and serving as a steppingstone to send astronauts to Mars.
Lead-up to Launch: NASA Pegasus Barge Crew
Leading up to the Artemis I launch, the Marshall Star is spotlighting team members at NASA’s Marshall Space Flight Center and Michoud Assembly Facility and how they are contributing to the mission. This issue features the NASA Pegasus barge crew: Marine Operations Manager and team lead Joseph Robinson; Marine Operations Coordinator Terrance Fitzgerald; Able Seaman and crew supervisor Jeffery Whitehead; Marine Engineer Scott Ledet; and Ordinary Seaman Devon Mauffray.
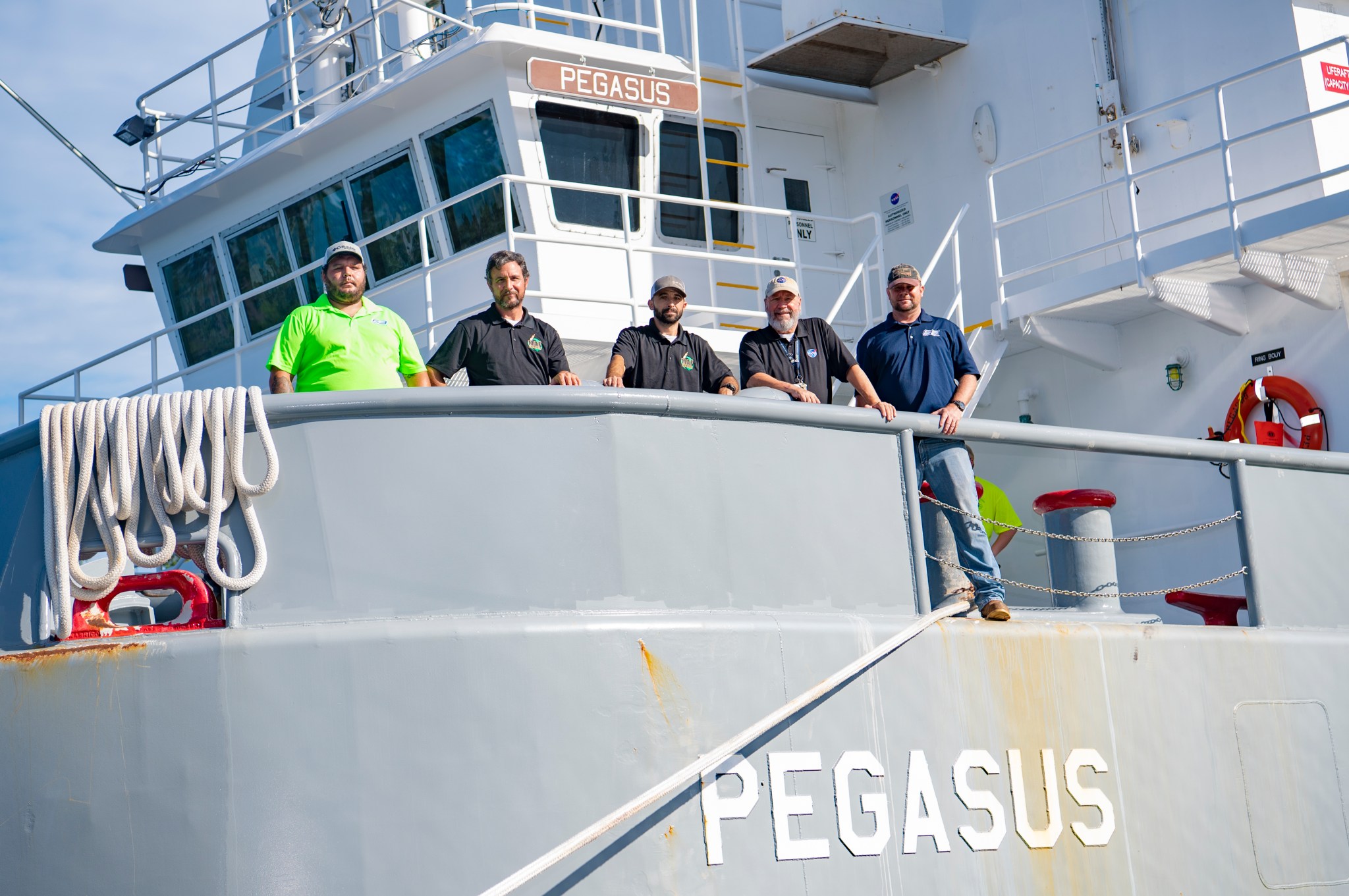
Question: What is your role with the upcoming Artemis I launch?
The barge crew was responsible for transporting structural test articles to Marshall for testing prior to assembly of the Space Launch System (SLS) core stage for Artemis I. The crew maintains, mans, and transports the SLS core stage to Kennedy Space Center for launch. If the rocket can’t get transported, then the launch can’t happen.
Question: What does it mean to you to be involved with the Artemis Generation and NASA’s return to the Moon and beyond?
“It’s bigger than anything I’ve been a part of. It brings me great pride. My grandfather and grandmother worked at Michoud for the Apollo mission, so it’s with great pride that I follow in their footsteps,” Ledet said.
“It’s not the destination; it’s the journey,” Robinson said. “We spent six days together on the barge in the Gulf of Mexico and we were the only ones around the rocket. Many are involved in making this launch possible, and we’re a small but critical part.”
“There’s not many times in history that people have joined together and pooled their human and financial resources to achieve something of this magnitude. It’s like divine providence is guiding us,” Whitehead said.
“Our crew is diverse. We’re all mariners but come from different backgrounds. We each apply our strengths and come together to contribute to Artemis and make the barge what is today,” Robinson said.
Question: How did you become interested in a career with NASA?
Fitzgerald began his NASA career, with support from Robinson while in the Coast Guard, working with the crew that loaded the external fuel tank onto Pegasus during the Space Shuttle Program. While Pegasus sat unused between shuttle and Artemis, Fitzgerald worked as a NASA harbor master in anticipation Pegasus would be brought back for future NASA missions, and together with Robinson, enthusiastically rejoined the barge crew when Pegasus was recommissioned for Artemis.
Whithead, Mauffray, and Ledet joined the crew during Artemis. They stood out to Robinson and Fitzgerald not just for their technical skills but for their ability to get along well with others.
“When you’re in the middle of the Gulf, with minimal resources, we have to be able to get along and rely on each other. Otherwise, we can’t get the job done,” Fitzgerald said.
Question: In your view, what makes the launch of Artemis I and future missions so important?
The crew feels that the Artemis I launch is so important because it pushes the limits of ingenuity and technology. Necessity is the mother of invention. They believe that when we push ourselves to the limit, we find new ways to achieve what seemed impossible. What NASA does, percolates to the rest of the world – cell phone cameras, temper foam, invisible braces.
Like many explorers before them, the crew feels we’re paving the way for deeper exploration and discovery of new technologies. Resources and opportunities for new adventures for future generations become possible. The crew sees a lot of companies getting into space but to them, NASA is the brand when it comes to space and is still the leader in the industry.
Question: Where will you watch the launch?
The crew will probably watch it at the Michoud viewing party.
Markings on SLS Provide a Different View of the Artemis I Launch
By Will Bryan
A picture is worth a thousand words. For engineers building, launching, and flying the rocket that will enable NASA’s next era of space exploration, a photo is worth a thousand data points. Data points that will land the first woman and first person of color on the Moon and send humanity further out in the solar system than ever before.
When NASA’s Artemis I mission launches later this month, thousands of cameras will capture the historic first flight of NASA’s Space Launch System (SLS) rocket and Orion spacecraft.
Some cameras, though, are focused on carefully placed markings on the rocket, spacecraft, and mobile launcher. These cameras aim to capture portions of the countdown and launch and will provide valuable data to engineering teams following launch and flight.
A variety of black-and-white patterns are painted on the rocket and spacecraft and used as targets for the cameras. Some designs, like the checkered rings on each solid rocket booster, are used by cameras on the rocket. In the case of the black ring below the nose cone on the left-hand solid rocket booster, it allows the engineers to easily distinguish the right booster from the left since the vehicle is very symmetric and some of the cameras will have a tight field of view. Other patterns, though, are best viewed at a distance.
“If you look at the SLS core stage and the twin solid rocket boosters, launch pad, and launch tower, you will see alternating black and white squares that appear like checkerboard patterns,” said Beth St. Peter, SLS Imagery Integration team lead at NASA’s Marshall Space Flight Center. “Each marking has a specific purpose. In general, the markings are used to precisely measure motion during dynamic events during liftoff and separation. With specific cameras, we will track those crosshairs of the markings and form ‘triangles’ of multiple patterns to help with our post flight reconstruction analysis tasks.”
Critical events, such as solid rocket booster separation from the core stage, will be closely studied and compared with computer model simulations.
“Imagery and data we collect will help validate the computer models, and we might even find that we can relax some of the constraints based on the photogrammetry data,” St. Peter said.
The shape of each pattern is also important. Squares and rectangles provide sharp edges, which allow computer software to precisely determine pixel edges and, by extraction, movement of those pixels. Black-and-white patterns are used because the two colors provide the most contrast, which helps ensure the teams are tracking the same point over time and also from multiple cameras.
During the wet dress rehearsal activities, St. Peter and her team carefully watched numerous camera angles to ensure the rocket was not experiencing too much stress as more than 730,000 gallons of super-cooled liquid hydrogen and liquid oxygen were loaded into the rocket’s propellant tanks.
Placing the markings on the rocket, spacecraft, and mobile launcher is almost a science itself. Some photogrammetric markings are located on known sightlines from previously installed cameras around the launch pad. The markings also have to be placed where extreme cold from propellants or extreme heat from launch will not affect them.
Photogrammetry will be important when the interim cryogenic propulsion stage and Orion separate from the empty core stage and launch vehicle stage adapter. Separation will be monitored with a different kind of technology.
“Instead of using painted markings, we’re using retroreflector markings,” St. Peter said. “These reflectors will direct light bounced off them to the source – in this case, an onboard camera which has a light source. Retroreflectors are perfect in low-light and changing light conditions like what we experience during this key separation event.”
As NASA continues to launch and fly SLS on increasingly complex missions, the markings on SLS will evolve. Artemis II and Artemis III will also fly the first configuration of SLS, known as Block 1, and the markings will remain similar to those on the Artemis I rocket. On Artemis II, astronauts will use additional markings with reflective targets on the interim cryogenic propulsion stage and Orion stage adapter to fly Orion and test out its handling capabilities during a rendezvous and proximity operations demonstration.
Beginning on Artemis IV, the second configuration of SLS, known as Block 1B, will feature a more powerful upper stage that replaces the interim cryogenic propulsion stage. Block 2, debuting on the ninth flight of SLS, will feature newly designed advanced solid rocket boosters.
Bryan, a Manufacturing Technical Solutions employee, supports SLS Strategic Communications.
Launching Science, Technology on NASA’s Artemis I Mission
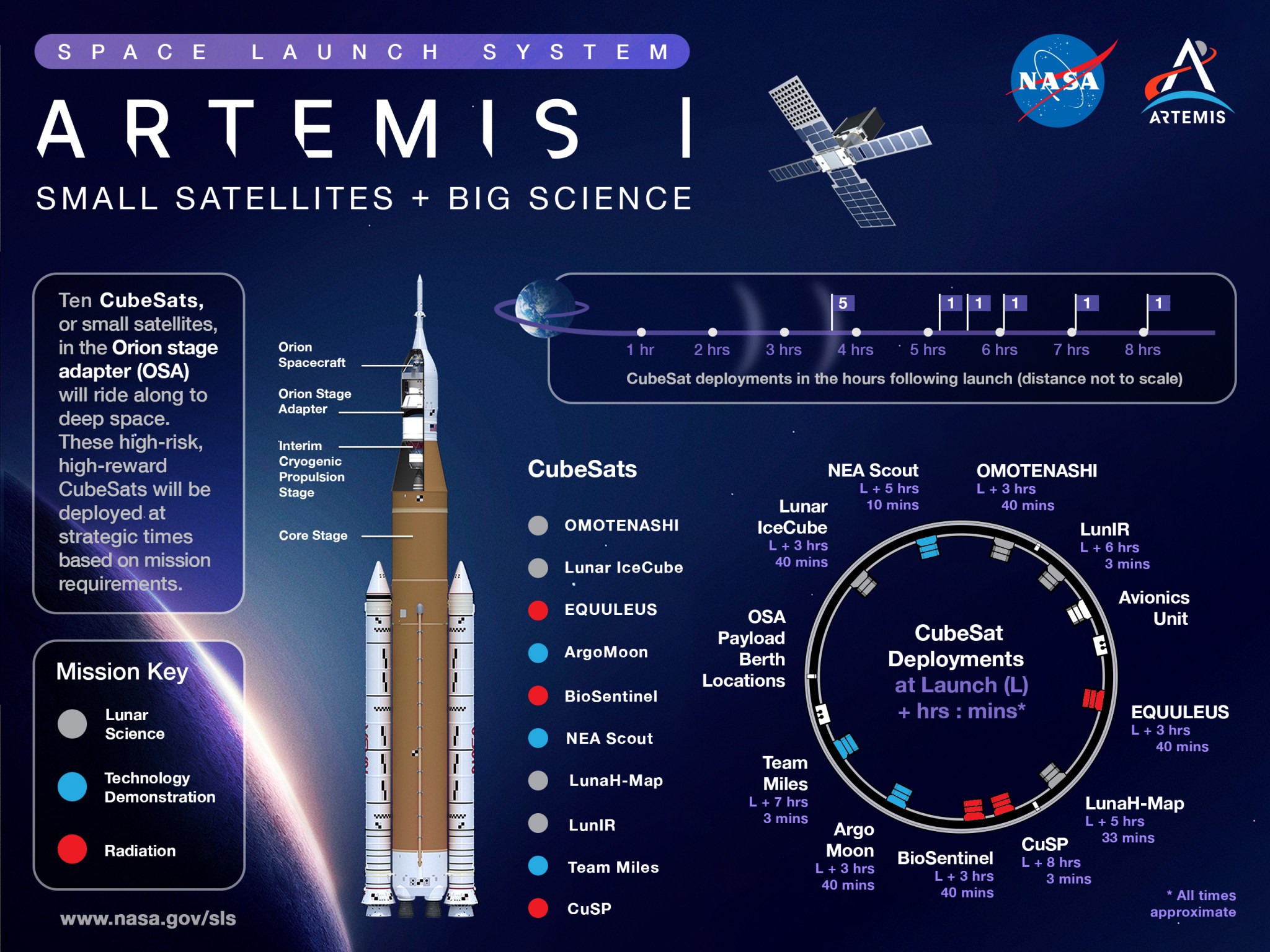
Learn more about the secondary payloads flying on Artemis I: https://www.nasa.gov/launching-science-and-technology.html Credits: NASA/Kevin O’Brien
When NASA’s Space Launch System (SLS) rocket launches the agency’s Artemis I mission to the Moon, 10 CubeSats, or small satellites, will be hitching a ride inside the rocket’s Orion stage adapter. International space agency partners and universities are involved with several of the different secondary payloads. The shoebox-sized CubeSats will be deployed from the Orion stage adapter at strategic locations after NASA’s Orion spacecraft separates and is a safe distance away. From there, each of the secondary payloads will carry out different science and technology demonstrations in deep space. Learn more about the secondary payloads flying on Artemis I here. (NASA/Kevin O’Brien)
Seven Teams Advance in NASA’s $5M Watts on the Moon Challenge
By Tee Quillin
With the upcoming launch of Artemis I, NASA is setting the stage to land the first woman and the first person of color on the Moon. Future Artemis astronauts living and working on the lunar surface will require rugged technologies that can store energy and deliver continuous, reliable power.
Toward that goal, NASA has announced seven teams advancing to the next level of the agency’s Watts on the Moon Challenge. The $5 million, multilevel prize competition challenges innovators from all walks of life to develop pioneering power systems light enough for spaceflight and tough enough to withstand the harsh lunar environment.
“Building a strong infrastructure on the Moon is critical to enabling sustained human presence on the Moon and beyond,” said Denise Morris, acting program manager for NASA’s Centennial Challenges at Marshall Space Flight Center. “The Watts on the Moon Challenge will get us one step closer by providing power transmission and energy storage solutions that will help future Artemis astronauts explore more of the lunar surface than ever before.”
The second phase of the challenge kicked off in February with a design competition. Phase 2, Level 1 challenged solvers to submit concepts for drawing power from an existing source and delivering it over nearly two miles under the same temperature extremes and vacuum conditions found on the lunar surface.
The winning teams were chosen from submissions of technical documentation, including detailed engineering designs and analyses. A panel of judges reviewed, evaluated, and scored submissions based on key performance metrics such as minimal mass and maximum efficiency. Seven winning team will receive $200,000 each from NASA and move on to compete in Phase 2, Level 2.
The Phase 2, Level 1 winners are:
- Electric Moon of Columbus, Ohio
- Orbital Mining Corporation of Golden, Colorado
- Philip Lubin’s Team of Santa Barbara, California
- Michigan State University Planetary Surface Technology Development Lab of Houghton
- Skycorp of Santa Clara, California
- Virtus Solis Technologies Inc. of Troy, Michigan
- X-Wheel Inc. of Hialeah, Florida
“It’s really exciting because we’re developing new technology that will enable continuous human presence on the lunar surface,” said Rob Button, deputy chief of the Power Division at NASA’s Glenn Research Center. “Specifically, we’re addressing long distance power transmission and energy storage in very cold conditions.”
Phase 2, Level 2 challenges these seven teams to develop and test key parts of their solutions. Up to four teams will win equal shares of $1.6 million and move on to compete in the Watts on the Moon Challenge finals. To close out the challenge, the four finalist teams will have to prove the success of their solution inside a vacuum chamber for two top prizes worth a total of $1.5 million.
In Phase 1 of this challenge, NASA awarded a total of $500,000 to seven teams in May 2021. Sixty teams submitted original design concepts aimed at meeting future needs for robust and flexible technologies to power human and robotic outposts on the Moon.
The Watts on the Moon Challenge is a NASA Centennial Challenge led by the agency’s Glenn. NASA has contracted HeroX to support the administration of this challenge. Marshall manages Centennial Challenges on behalf of the agency’s Prizes, Challenges, and Crowdsourcing Program in the Space Technology Mission Directorate.
Quillin, a Media Fusion employee, supports Marshall’s Office of Strategic Analysis & Communications.
Interns Cap Summer Session with Exit Presentations
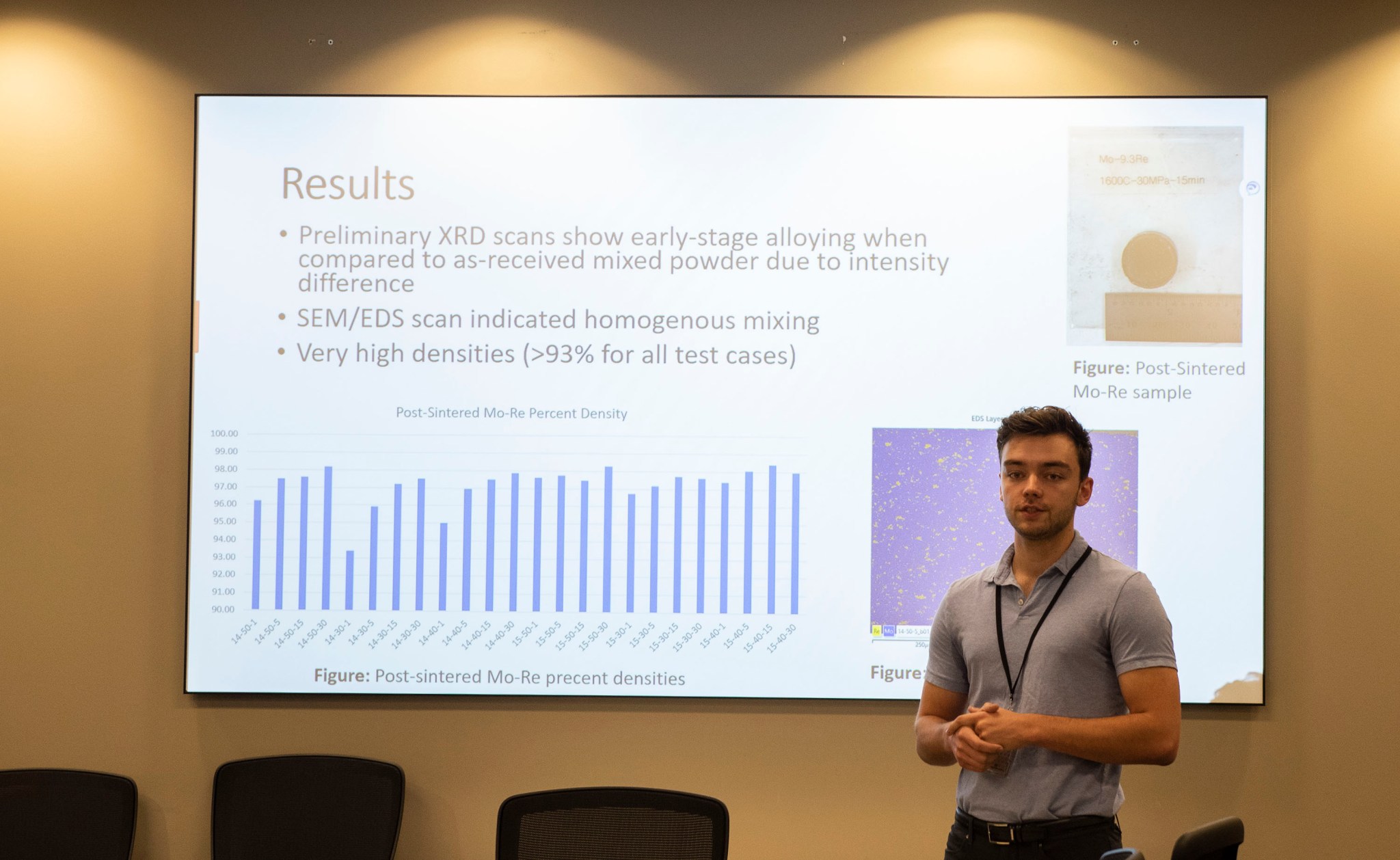
Toren Hobbs, a senior studying materials science at Ohio State University and an intern at NASA’s Marshall Space Flight Center, shares findings from his work supporting NASA’s Refractory Alloy Additive Manufacturing Build Optimization, or RAAMBO, during an exit presentation for the 2022 summer internship session. More than 100 interns brought their summer internships to a close with similar presentations to their peers and colleagues across the center. (NASA/Danielle Burleson)
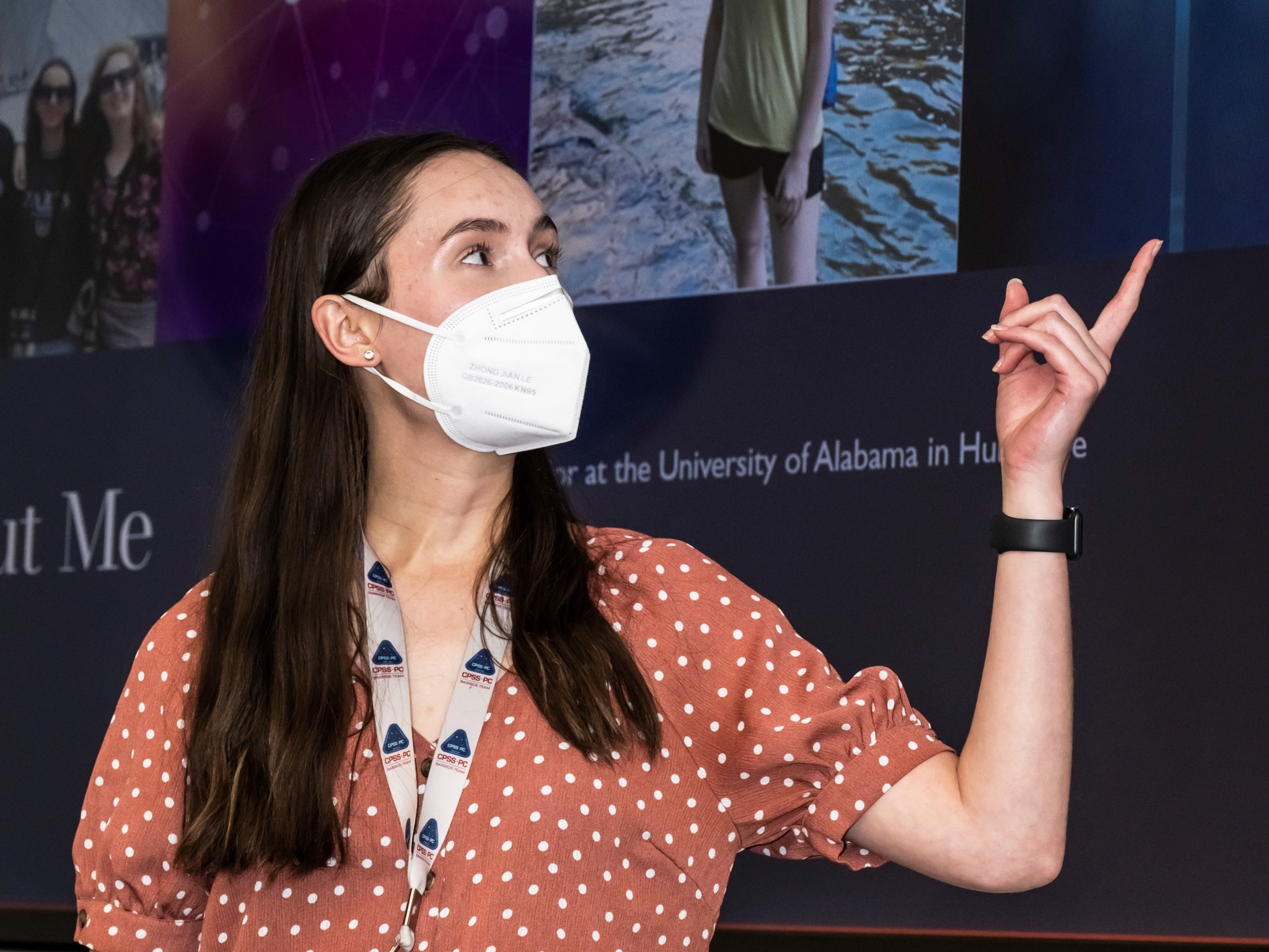
Marshall intern Allison Jones, a senior at the University of Alabama in Huntsville, discusses her summer project designed to improve project monitoring related to the International Space Station. NASA’s Southeast Regional STEM Engagement Office manages science, technology, engineering, and math engagement activities at Marshall by creating meaningful opportunities for both mentors and interns. For more information on NASA’s internship programs, visit here. (NASA/Mick Speer)