NASA Leadership Visits Michoud to Tour Factory, Meet Workforce
By Matt Higgins
NASA Administrator Bill Nelson and Deputy Administrator Pam Melroy visited the agency’s Michoud Assembly Facility on Dec. 8 for tours and briefings on the facility’s vital role in NASA’s exploration missions. Michoud is America’s rocket factory, building components for the Space Launch System (SLS) rocket and Orion spacecraft that will return humans to the Moon.
It was the first time Nelson and Melroy visited Michoud in their current roles.
Nelson and Melroy toured the 43-acre manufacturing facility and spoke with NASA engineers and subject matter experts. They saw the core stage liquid hydrogen tank for the Artemis II mission, Orion hardware products, and the tooling at Michoud built specifically for SLS. NASA’s Artemis missions will land the first woman and first person of color on the Moon. Prime contractor Boeing is building the core stage, which will be the largest rocket stage ever flown. It will store 733,000 gallons of super-cooled liquid hydrogen and liquid oxygen to fuel the four RS-25 engines that power the rocket. Lockheed Martin is manufacturing the Orion crew module, and its workers are also developing a launch abort system to protect the crew.
Since 1961, Michoud has been the nation’s premiere site for manufacturing and assembly of large-scale space structures. The facility has played a vital role in the Apollo, Space Shuttle, and now Artemis programs. Michoud is currently producing hardware for the Artemis II through Artemis IV missions. Artemis I launch is scheduled for February.
“It’s an exciting time, and we’re grateful for what you do here. This is the beginning of a process that creates the most complicated machine ever created by mankind, and it’s going to take our astronauts back to the Moon,” Nelson said.
The integrated system of SLS and Orion is currently stacked together at NASA’s Kennedy Space Center and is entering the final phase of testing and preparations for the upcoming uncrewed flight test around the Moon.
“To see pieces of Artemis II, III, and IV… it just makes my heart soar!” Melroy said.
After an employee luncheon, Nelson and Melroy attended the Michoud Windshield Tour to discuss infrastructure, hurricane damage, tornado damage, the Extended Use Lease agreements, and green spaces available for development.
In October 2020, Hurricane Zeta made landfall as a Category 2 storm in the New Orleans area. Zeta caused 50,000 square feet of roof damage to the facility. The emergency ride-out crew at Michoud recorded wind gusts of 101 mph.
In August 2021, Hurricane Ida made landfall in Louisiana as a Category 4. Emergency ride-out crew recorded wind gusts of 110 mph and 13 inches of rain before sensor’s failed. Ida damaged the roofs still under repair from Zeta, and the storm’s rainfall intruded into many buildings on-site including the factory floor.
Jody Singer, director of NASA’s Marshall Space Flight Center, accompanied Nelson and Melroy, and praised the commitment of Michoud’s workforce.
“This workforce, despite the weather events, the impacts of COVID, continues to survive, put in long hours here and at home with their own recovery. That’s a lot of stress on our team, but our team is doing great!” she said.
Nelson and Melroy also highlighted the appropriations NASA secured in the recently passed funding law to help Michoud repair damage caused by Hurricane Ida.
“I’m very grateful to the Congress that they agreed to our request for Michoud and Stennis that we get emergency supplemental appropriations for infrastructure,” Nelson said.
Michoud crews are underway making repairs from hurricane damages.
Higgins, a Manufacturing Technical Solutions employee, supports Michoud through Marshall’s Office of Strategic Analysis & Communications.
NASA Launches New Mission to Explore Universe’s Most Dramatic Objects
NASA’s Imaging X-ray Polarimetry Explorer mission launched at midnight CST on Dec. 9 on a SpaceX Falcon 9 rocket from NASA’s Kennedy Space Center.
A joint effort with the Italian Space Agency, the IXPE observatory is NASA’s first mission dedicated to measuring the polarization of X-rays from the most extreme and mysterious objects in the universe – supernova remnants, supermassive black holes, and dozens of other high-energy objects.
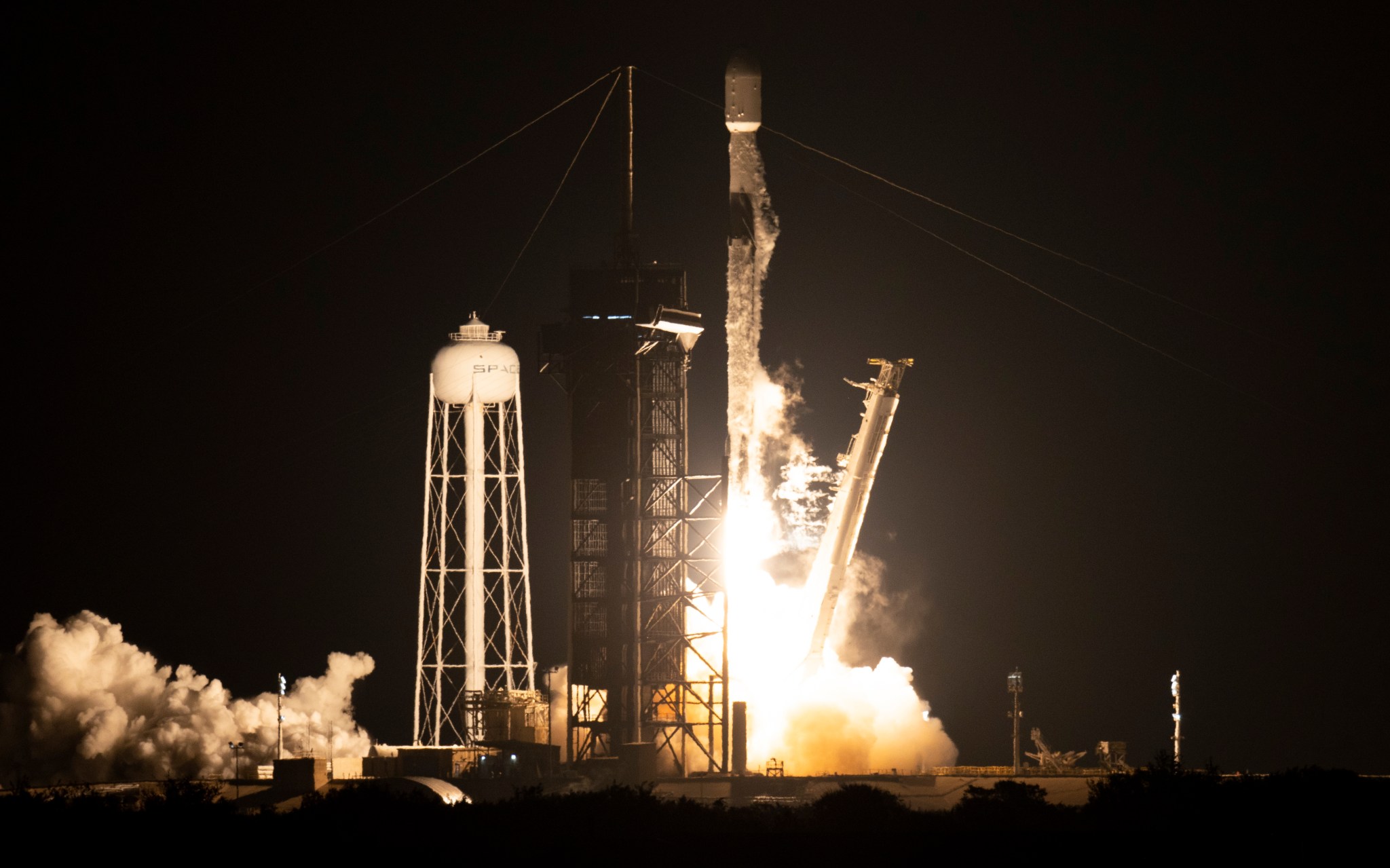
“IXPE represents another extraordinary first,” said Thomas Zurbuchen, associate administrator for the Science Mission Directorate at NASA Headquarters. “Together with our partners in Italy and around the world, we’ve added a new space observatory to our fleet that will shape our understanding of the universe for years to come. Each NASA spacecraft is carefully chosen to target brand new observations enabling new science, and IXPE is going to show us the violent universe around us – such as exploding stars and the black holes at the center of galaxies – in ways we’ve never been able to see it.”
The rocket performed as expected, with spacecraft separation taking place 33 minutes into flight. Approximately one minute later, the spacecraft unfurled its solar arrays. IXPE entered its orbit around Earth’s equator at an altitude of approximately 372 miles. About 40 minutes after launch, mission operators received the first spacecraft telemetry data.
“It is an indescribable feeling to see something you’ve worked on for decades become real and launch into space,” said Martin Weisskopf, IXPE principal investigator and chief of X-ray astronomy at NASA’s Marshall Space Flight Center. Weisskopf, who previously spearheaded development and delivery of the Chandra X-ray Observatory, came up with the idea for the IXPE spacecraft and has conducted seminal experiments in X-ray astronomy since the 1970s.
“This mission would not be possible without Marshall’s unique, world-class capabilities in X-ray astrophysics,” wrote Marshall Director Jody Singer, congratulating her team in the wake of the successful launch. “Your important work enables NASA to test and refine our theories of how the universe works and leads to groundbreaking research for decades to come. I’m so proud of this historic accomplishment!”
IXPE carries three state-of-the-art space telescopes with special polarization-sensitive detectors. Polarization is a property of light that holds clues to the environment from which the light originates. The new mission builds on and complements the scientific discoveries of other telescopes, including Chandra, NASA’s flagship X-ray telescope. First light operations are scheduled to begin in January.
“This is just the beginning for IXPE,” Weisskopf said.
Marshall manages the IXPE mission for the agency’s Science Mission Directorate as a project of the NASA Explorers Program. IXPE is an international collaboration between NASA, the Italian Space Agency, and partners and providers in 12 other countries. Marshall built the three X-ray telescopes. The Italian Space Agency contributed IXPE’s polarization detectors. Ball Aerospace in Broomfield, Colorado, provided the spacecraft and manages spacecraft operations at the University of Colorado Boulder’s Laboratory for Atmospheric and Space Physics. NASA’s Goddard Space Flight Center manages the Explorers Program.
NASA’s Space Launch System Engineering Support Center Prepares for Artemis I
By Alyssa Lee
As teams at NASA’s Kennedy Space Center continue Artemis I launch day preparations, crews at the Space Launch System’s (SLS) Engineering Support Center at NASA’s Marshall Space Flight Center are joining simulations to practice their role in the exploration of the Moon and beyond.
The SLS Engineering Support Center will provide support from the ground during Artemis launches by monitoring data and solving challenges that may occur before and during SLS’s first flight on Artemis. The support center allows the SLS team to connect not only with Kennedy, but also with experts at various locations across the United States to support ground processing, testing, launch, and flight operations for the rocket in real time.
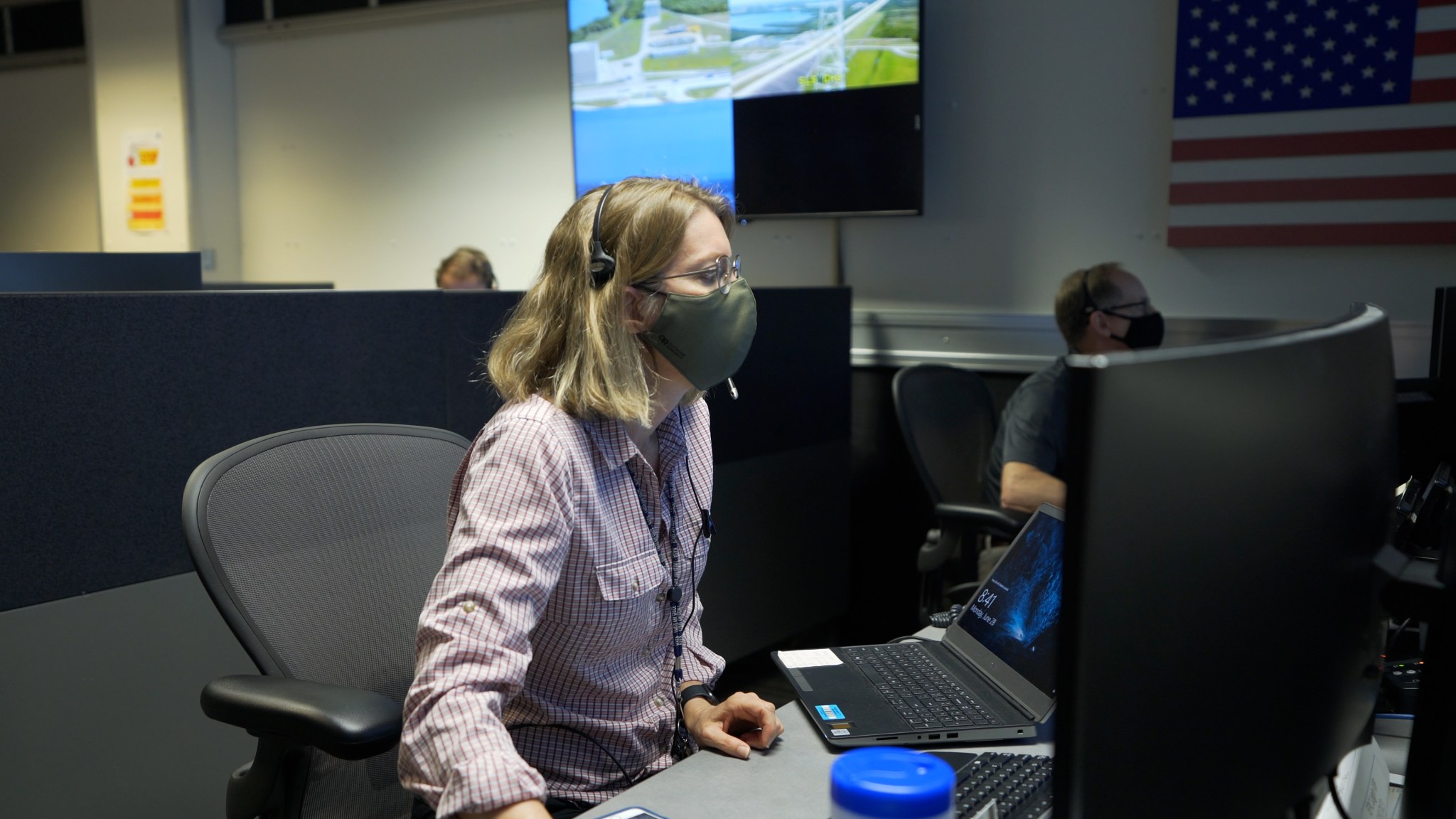
“The team working in the SLS Engineering Support Center at Marshall are people with the most knowledge about the rocket’s hardware and how it operates,” said Doug Parkinson, SLS Launch Integration and Mission Operations lead at Marshall. “If any issues come up with SLS hardware operations, you need those experts on hand and ready to help quickly resolve the issue so that the Artemis I launch countdown can stay on track. “
The SLS support center provides mission-critical capabilities of voice loops, video streaming, and telemetry distribution to those working in the control room, and they can connect and share information with other experts, such as industry partners who have developed SLS hardware, in a matter of seconds.
Artemis I will be an uncrewed flight test to launch the SLS rocket and send the Orion spacecraft around the Moon and back to Earth. On launch day, the team in the support center will work with the team in Kennedy’s Launch Control Center by monitoring everything from the health of the rocket to day-of-launch environmental conditions like wind and heat. After liftoff, the support center will then coordinate with the Mission Control Center at NASA’s Johnson Space Center for the remainder of the mission.
Before the mission, the team prepares for Artemis missions through simulations in which they practice every aspect of the mission. Pre-launch simulations include powering on the rocket through engine ignition. Other simulations include ascent mission phases like trans-lunar injection, or TLI burn, the maneuver that SLS will use to send Orion toward the Moon. From launch countdown to flight operations, simulations allow the team to exercise the functionality of the facilities and even practice working real challenges that might occur during various milestones before and during flight.
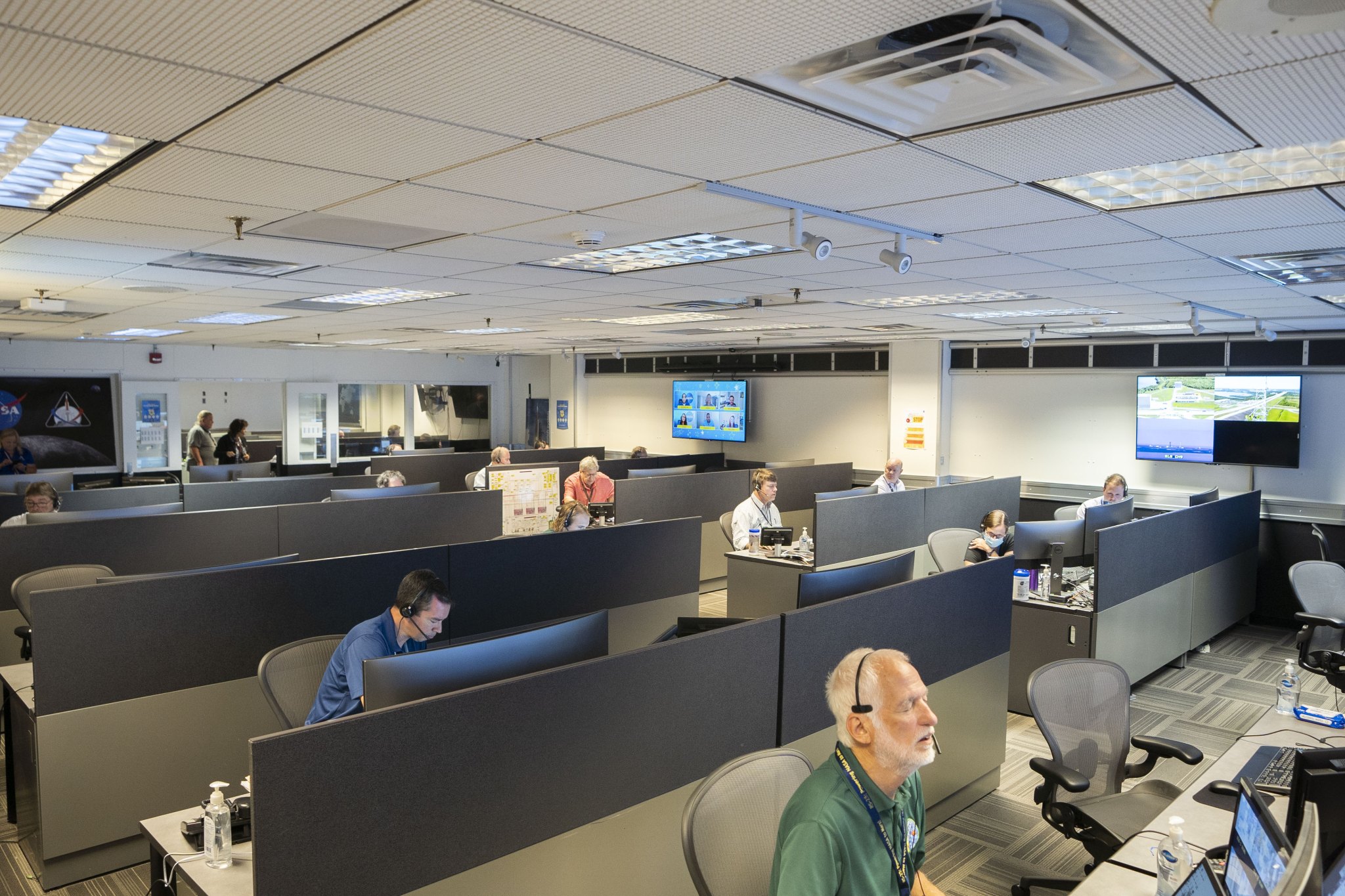
Several weeks before launch, the SLS rocket and Orion will roll the roughly 4 miles to Pad 39B atop the crawler-transporter for a wet dress rehearsal, the last major test before the Artemis I launch. The Kennedy launch team, which includes the SLS program manager and other SLS and Orion leads, will conduct pre-launch activities down to the last 10 seconds before launch. This includes all power-on activities, systems checkouts, propellant loading, and thermal conditioning. Over 200 SLS team members will be positioned in Marshall’s engineering support center and other remote locations across the country for this rehearsal, working in the same positions that they will support during launch.
“Wet dress rehearsal will ensure our team is prepared for a successful Artemis I mission, the first integrated flight of the Space Launch System rocket and Orion spacecraft,” said David Beaman, SLS Systems Engineering and Integration lead at Marshall. “Artemis I is the start of many Artemis missions that we will be supporting, and an important learning experience leading up to Artemis II, the first flight to send crew in Orion around the Moon and back to Earth.”
Teams working in the engineering support center will support not only Artemis I, but also future missions that land the first woman and first person of color on the Moon and prepare for human missions to Mars.
Lee, a Media Fusion employee, supports Marshall’s Office of Strategic Analysis & Communications.
Artemis II Rocket Hardware Ready for Final Outfitting
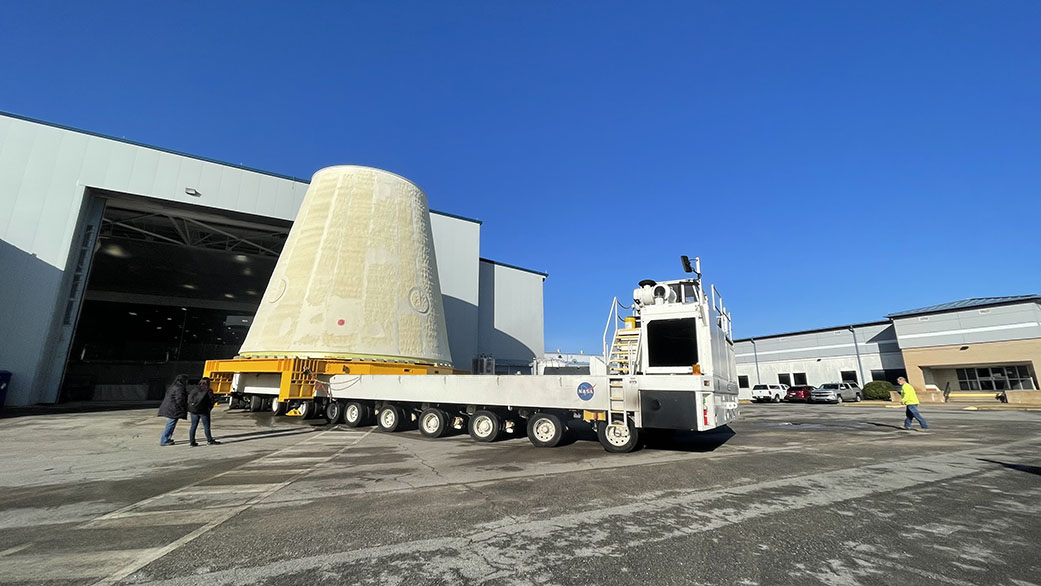
Technicians at NASA’s Marshall Space Flight Center move the Space Launch System (SLS) launch vehicle stage adapter for the Artemis II mission to another manufacturing area Dec. 8 to finish outfitting the flight hardware. The adapter was built at Marshall by lead contractor Teledyne Brown Engineering in Huntsville. Teams recently completed applying the spray-on foam insulation that will protect the rocket hardware during flight. Now, crews will outfit the inside of the adapter with platforms that will allow teams to access the inside during assembly with the rest of the rocket. Technicians will also install special systems that allow the adapter and the core stage to separate from the Interim Cryogenic Propulsion Stage. The adapter connects the rocket’s core stage to the Interim Cryogenic Propulsion Stage, which provides the power to perform the trans-lunar injection maneuver to send the Orion spacecraft to the Moon. The Artemis II mission will be the first to return American astronauts to lunar orbit. (NASA)
Watch NASA Build Upper Portion of Artemis II Rocket Stage
Teams at NASA’s Michoud Assembly Facility completed the upper portion of the core stage that will help power Artemis II, the second flight of NASA’s Space Launch System rocket and the first crewed Artemis mission to the Moon. The 66-foot-tall section makes up the top portion of the core stage. Teams used heavy-lift equipment to carefully lower and stack the liquid oxygen tank, intertank, and then the forward skirt on top of one another in a special stacking cell at Michoud. Then, they integrated and tested the various systems inside the upper portion of core stage. Later, teams will join the forward assembly with the liquid hydrogen tank and the engine section to complete the entire core stage. (NASA)
Father’s Foundry Job Inspires Dr. Sharon Cobb to Pursue NASA Career Path
By Gina Hannah
Career inspiration can come from many places. For Space Launch System (SLS) Program Associate Manager Dr. Sharon Cobb, it was her father’s work at a foundry in Birmingham, Alabama.
During a family employee event, Cobb saw molten steel being poured into molds to form large ignots, large metal blocks that would later be made into usable structures, and she was hooked.
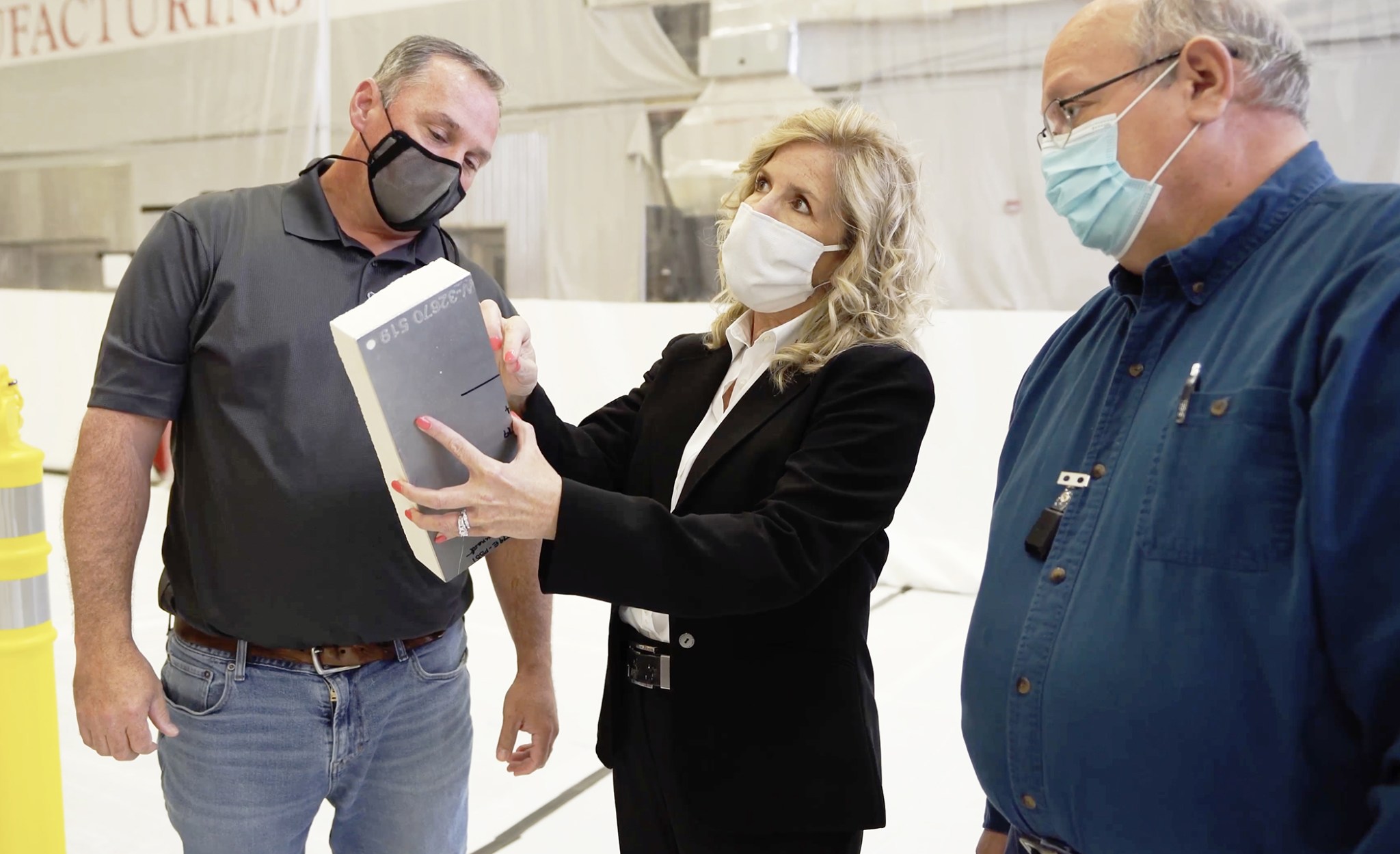
“I was just fascinated and in awe,” Cobb said. “The thing that was most exciting to me was watching them pouring these vast amounts of red-hot metal into the molds and watching that process of it cooling and the crackling of the skin as it cooled. Watching them pour that ingot and then forming it into a usable shape – that was fascinating to me – that you could transform materials into something different based on how you process them.”
That fascination with how raw materials can be transformed into things that make life better led Cobb to a 35-year career with NASA that ranged from pioneering projects in a materials lab at NASA’s Marshall Space Flight Center to teaching a materials science class to astronauts before they conducted experiments on the International Space Station.
Today, Cobb oversees design, manufacture, testing, and assembly of the world’s most powerful and most capable rocket, NASA’s Space Launch System that will return astronauts to the Moon for the first time since the Apollo program. High-energy SLS launches can also send robotic spacecraft deep into the solar system faster than any rocket in existence today.
Cobb said her career trajectory would likely have been very different without that exposure to her father’s work as well as encouragement that came from him and from teachers in school.
“My guidance counselor always told me, ‘If you like math and science, you should consider engineering.’ At the time, I didn’t even know what engineering was!” she said. During her senior year of high school, Cobb had the opportunity to visit the materials department at the University of Alabama at Birmingham where she saw demonstrations on how different materials were processed.
“It was almost like magic. You could completely change a material’s properties just by the way you processed it from liquid to solid,” Cobb said. “I had always been curious about how things worked, and this sparked my interest. I really wanted to know why and how you could do that.”
Cobb earned bachelor’s and master’s degrees in material engineering from the University of Alabama at Birmingham and a doctorate in materials science and engineering from the University of Florida in Gainesville. She also continued learning from her father. “I would come home from school and we would talk about some of the things I’d learned, and he would tell me some of the things that were going on at the plant and the reports that he got to write,” she said. “We enjoyed having lots of technical discussions about my classes and how it related to his work in the foundry.”
During graduate school, Cobb had her first opportunity to work for NASA, assisting one of her advisers who had taken a summer faculty position. “We were working on a flight experiment that would fly on the space shuttle. The idea that we could process materials without gravity was a really exciting concept,” Cobb said. She joined the agency full-time in 1986 as a research scientist, conducting pioneering studies on the effects of reduced-gravity processing on a variety of complex semiconductor materials.
Her NASA career spans work both in and out of the lab, including a stint at NASA Headquarters as a program executive for a team studying how materials might be mined from the Moon and used to build parts via additive manufacturing that would be needed on a mission. One of the projects Cobb led as a senior scientist was the Materials Science Research Rack-1 on the space station which is still in use today for in-space materials experiments.
“It’s really exciting to see those experiments that we planned so many years ago being implemented on the space station,” she said. “One of the things I got to do in the lab was learn about building flight hardware that would then be used in space to process these materials. That has led throughout my career to my interest in building flight hardware that enables things to be done in space. Those materials I thought were magic so many years ago are an important part of building flight hardware and are key to making it possible for us to safely transport humans and equipment into space to do things we’ve only dreamed were possible.”
Cobb is now part of the team building a new generation of hardware that will enable the next era of space exploration. The Artemis program will expand humanity’s presence beyond Earth, starting with a sustainable lunar presence and enabling the next giant leap: sending humans to Mars.
Hannah, an LSINC employee, supports SLS Strategic Communications.
Engineer Peter Berg Supports Artemis with State Analysis Model
By Savannah Metz
As NASA and the rest of the world get ready for the Artemis I lunar mission, and the first flight of the Space Launch System (SLS) rocket, Marshall Space Flight Center’s Engineering Directorate is contributing to the mission in a variety of ways.
Engineer Peter Berg, design and analysis team lead for the Integrated System Health Management & Automation Branch, uses a state analysis model in his work with mission and fault management to support Artemis.
Mission and fault management develops algorithms that monitor and control the internal conditions of the SLS rocket before and during flight.
Working in a simulated environment, the state analysis model and its algorithms take the status of parts from different subsystems, such as valves within the main propulsion system. The model will determine if the entire system can function under the given conditions. If one subsystem is operating in an off-nominal state, the model can determine if this will affect other subsystems. The team simulates potential issues before launch. During launch, they work “on-call” to run additional test cases if it is necessary to resolve any issues.
Berg has been with NASA for more than 14 years. In addition to supporting the Artemis missions, he has worked on many other projects and programs, including the Lunar Atmosphere and Dust Environment Explorer.
We sat down with Berg to understand how the state analysis model is helping NASA go back to the Moon.
Question: Why is the state analysis model important to Artemis?
Berg: The advancement of the state analysis model has allowed for quick analysis of vehicle dynamics, failure scenarios, and subsystem interactions during the Artemis I mission. These quick looks at different scenarios allow the team to accurately identify problems and potential solutions before flight. The software environment also allows us to easily execute mission and fault management algorithms, helping manage conditions with SLS.
Our very talented team’s hard work and dedication have allowed the state analysis model with certified simulators to match the SLS System Integration Lab and Green Run data with great accuracy for the Artemis I mission.
Question: How has your work contributed to Artemis leading up to the launch?
Berg: The state analysis model has been used in a simulated environment and with test hardware to provide rapid testing of the mission and fault management algorithms to provide enhanced launch vehicle risk reduction. The models help engineers identify complex interactions between integrated systems that might have negative effects. For example, if the model reads an error with the cryogenic level sensor system, this could cause a negative effect on the main propulsion system. These interactions help find potential gaps in mission requirements.
The model provides accurate assessments of what-if scenarios quickly. Previously, it could take multiple engineers much longer. It also has helped develop intelligent launch vehicle test cases that provide the most coverage with fewer runs and pretty accurate predictions for developing success criteria.
Question: What benefits to Artemis have you seen from using your models?
Berg: The state analysis model has incredible benefits for risk reduction when it comes to the evaluation of a vehicle design as well as operations and software development. The rapid test execution opens up many more possibilities for the team to do large batches of what-if cases that span multiple failure cases. Being able to quickly close out potential risks to the vehicle allows for continued progress and future launch success.
One of the other consequential benefits of having a model that’s easy to build and execute is that we are able to use the state analysis model to rapidly bring new engineers up to speed. Additionally, because the model is a new concept, it encourages these engineers’ creativity to find new ways to solve problems.
Question: What’s been most exciting for you in supporting Artemis?
Berg: I’ve always wanted to be an engineer and continue to be inspired by the giants upon whose shoulders I now stand. Working on Artemis – sending the next people to the Moon and to Mars – is a great environment to be creative and use some of my previous personal spaceflight experience.
I’ve also learned from the extensive experience of my colleagues at Marshall and around the agency. Such a bold goal inspires all of us to develop technologies and processes to solve the tough problems, which can be applied to everyday problems here on Earth. It’s been great seeing how Artemis provides a similar inspiration to the next generation of engineers – those who will take us far beyond whatever we think will come next.
Question: What is next for the state analysis model?
Berg: Because it has proven effective, NASA plans to continue using this technology with future Artemis missions, the Human Landing System, Mars Ascent Vehicle, and Solar Cruiser.
Historically Unique Capability: The X-ray and Cryogenics Facility
By Brian Odom
Most everything about the world of high-energy astrophysics is difficult. The math is complex, the margin between risk and failure is narrow, and once an experiment leaves the launch pad, there is little chance of fixing a problem. The fact that Earth’s atmosphere absorbs most X-rays is good for humans but bad for testing experiments designed to detect X-rays. Luckily, NASA’s Marshall Space Flight Center developed a solution.
Originally completed in 1976 for testing the X-ray mirrors for the Einstein Observatory (HEAO-2), the X-ray and Cryogenics Facility is a critical and storied pillar of Marshall’s infrastructure. In 1976, NASA needed a way to recreate the environment X-ray experiments would find once in orbit to test the grazing incidence mirrors. From the outside, the most notable thing about the facility is the 1,700-foot guide tube the simulated X-ray sources traverse to the main building and the instrument vacuum chamber.
As the facility evolved over the decades, it left an imprint on many NASA programs. Numerous rounds of important testing were conducted during the development of the Chandra X-ray Observatory in the late 1980s and 1990s. That testing proved critical to the success of that mission that continues to produce incredible science. In 2002, the facility hosted testing of the Solar X-ray Imager for the GOES-12 satellite, and in 2005, tested the critically important X-ray telescope for Hinode – a mission developed to explore the solar magnetic fields and the forces that drive the dynamic forces of the solar atmosphere. Without the facility, mitigating many of the risks associated with those revolutionary missions would have proved impossible.
Several modifications over its 45-year history allow the facility to continue to play a vital role in proving out experimental space hardware. One of the recent missions to go through the facility was the James Webb Space Telescope, which is scheduled to launch Dec. 24. From 2008 to 2011, the facility’s 7,600-cubic foot helium cooled vacuum chamber was used for verification of several components of the observatory including chilling the Webb mirrors – down to minus 414 degrees Fahrenheit – and testing the structural stability of the primary mirror segment assemblies and backplane support structure.
As new missions come and go, this Marshall facility stands ready to test X-ray optics, detectors, and telescopes or perform mission-critical technology readiness demonstrations. Whether the goal of a mission is exploring the Sun or looking back to the early formation of the universe, the important work conducted in the facility ensures these missions will be prepared for the harsh environments they encounter in space.
Odom is Marshall’s historian and the acting NASA chief historian.
LCRD Launch Highlighted on ‘This Week at NASA’
“This Week @NASA,” a weekly video program broadcast on NASA-TV and posted online, featured the launch of NASA’s Laser Communications Relay Demonstration (LCRD).
On Dec. 7, LCRD and a joint NASA-U.S. Naval Research Laboratory experiment on solar energetic particles rode to space on a Department of Defense mission from Cape Canaveral Space Force Station in Florida. LCRD aims to highlight the next era of space communications, demonstrating space-to-ground laser communications. The technology will also receive and transmit data from an optical terminal that NASA will place on the International Space Station.
LCRD is funded and managed through NASA’s Technology Demonstration Missions program, located at the agency’s Marshall Space Flight Center.
View this and previous episodes at “This Week @NASA” on NASA’s YouTube page.