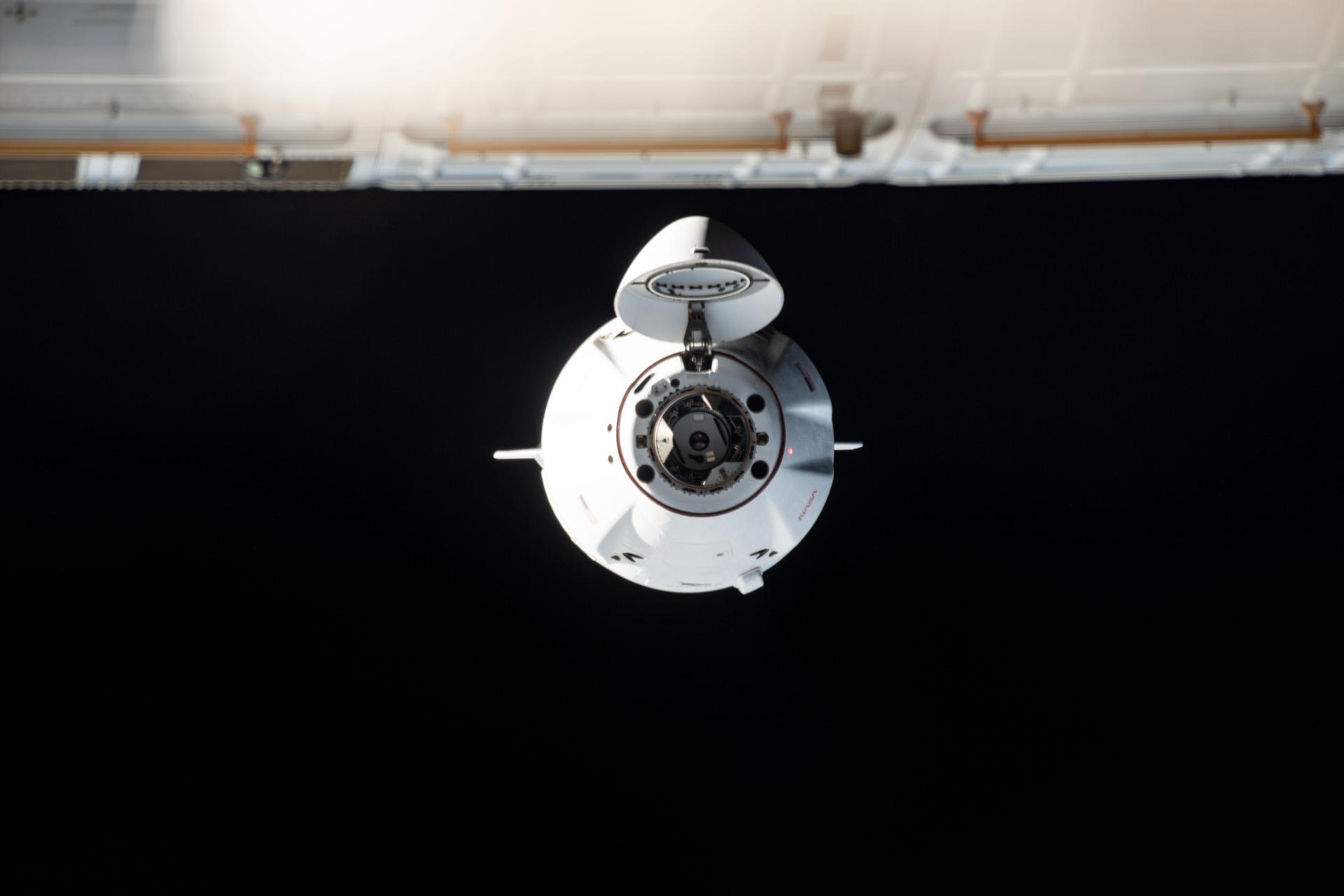
Following its launch on July 14, 2022, two NASA-supported optical fiber manufacturing payloads arrived at the International Space Station on July 16 aboard a SpaceX Commercial Resupply Services mission (CRS-25). The innovations will be used to demonstrate automated production of high-quality optical fibers in microgravity for use in applications on Earth. The payloads are Space Fibers 3 developed by San Diego-based FOMS, Inc. and the Orbital Fiber Optic Production Module (ORFOM) from Mercury Systems of Torrance, California.
Both Space Fibers 3 and ORFOM leverage suborbital research from NASA’s Marshall Space Flight Center showing that optical fibers produced in microgravity have fewer imperfections compared with fibers manufactured on Earth. These flexible, transparent fibers permit data transmission over longer distances and at higher bandwidths than electrical cables. They are used widely in fiber optic communications, and the potential performance improvements of manufacturing them in microgravity have spurred a rapid increase in interest for space-based manufacturing over the last decade. Telecommunications equipment, semiconductors, lasers for medical and scientific uses, thermal imaging, and spectroscopy are just a handful of Earth-based applications that could benefit.
“Our goal is to produce far superior fiber in space. The science is sound – but the best manufacturing approach needs to be further matured and validated on orbit,” said Kevin Engelbert, portfolio manager for NASA Johnson Space Center’s In Space Production Applications (InSPA) project, which selected the FOMS and Mercury Systems hardware for station demonstrations. “Suborbital flight testing serves as a valuable stepping stone as it allows us to assess hardware performance in microgravity relatively quickly and cost effectively before deploying it on the station.”
NASA’s early research in the 1990s to investigate optical fiber manufacturing in microgravity leveraged suborbital rocket research. Additionally, a 2012 Small Business Innovation Research (SBIR)-funded project with the U.S. Air Force, NASA, and industry leveraged parabolic flights – which provide brief, repeated intervals of weightlessness – to study optical fiber production. The flights specifically investigated production of ZBLAN (Zirconium Barium Lanthanum Aluminum Sodium Fluoride) optical fiber in microgravity, and again found that the fibers were smoother and more uniform than those produced in ground-based labs.
More recently, parabolic flights by Zero Gravity Corporation in 2020 and 2021, funded by NASA’s Flight Opportunities program and SBIR, allowed both FOMS and Mercury Systems to test hardware improvements made since previous station demonstrations.
“With each new generation of hardware, we bring in innovative changes to the microgravity fiber manufacturing process. Validating those improvements on parabolic flights helps us learn even more and succeed,” said Avinash Vasudevan, Director of Systems Engineering at Mercury Systems and principal investigator for ORFOM. “For a small business, this is a tremendous benefit.”
During previous tests aboard the station, the Mercury Systems team was able to produce fiber up to 65 feet (20 meters) long, but the process was largely manual and therefore time consuming and expensive. To address this, both Mercury and FOMS leveraged parabolic flights to evaluate automation approaches to decrease astronaut interaction, which could help increase fiber production to industry scale.
In the coming weeks, station astronauts will load raw materials (a thin cylinder of ZBLAN glass) into the production facility, while the rest of the operation – clamping the initial fiber draw onto a spool and then pulling the full length of thin optical fiber – will be automated. To help prepare station astronauts, the teams used recent parabolic flights to hone instructions for the crew and practice them in microgravity.
The flights also helped them troubleshoot hardware problems before heading into orbit.
“The first of our three parabolic flights demonstrated multiple challenges that we didn’t expect,” recalled Dr. Dmitry Starodubov, FOMS chief scientist and principal investigator for Space Fibers 3. “So, we redesigned our fiber processing capability and ended up with dramatically improved hardware that we were able to test again on the second and third flights, producing over 100 feet (30 meters) of fiber. This is a great value to learn from the challenges you encounter in microgravity conditions.”
Fiber manufacturing runs using the new hardware from FOMS and Mercury Systems are expected to last up to two weeks for each payload on the station. NASA’s InSPA program will assess results to help inform future hardware improvements and steps toward potential optical fiber manufacturing in space in the coming years.
About Flight Opportunities
Flight Opportunities rapidly demonstrates promising technologies for space exploration, discovery, and the expansion of space commerce through suborbital testing with industry flight providers. The program is funded by NASA’s Space Technology Mission Directorate at the agency’s Headquarters in Washington, and managed at NASA’s Armstrong Flight Research Center in Edwards, California. NASA’s Ames Research Center in California’s Silicon Valley manages the solicitation and evaluation of technologies to be tested and demonstrated on commercial flight vehicles.
Nicole Quenelle
Armstrong Flight Research Center