
NASA researchers have completed testing on a scale model of a unique aircraft wing, gaining data that will help build larger versions of the design with the goal of improving fuel efficiency.
The model tested at NASA’s Armstrong Flight Research Center in Edwards, California, is a 6-foot version of the Transonic Truss-Braced Wing (TTBW). This concept involves a wing braced on an aircraft using diagonal struts that also add lift and could result in significantly improved aerodynamics.
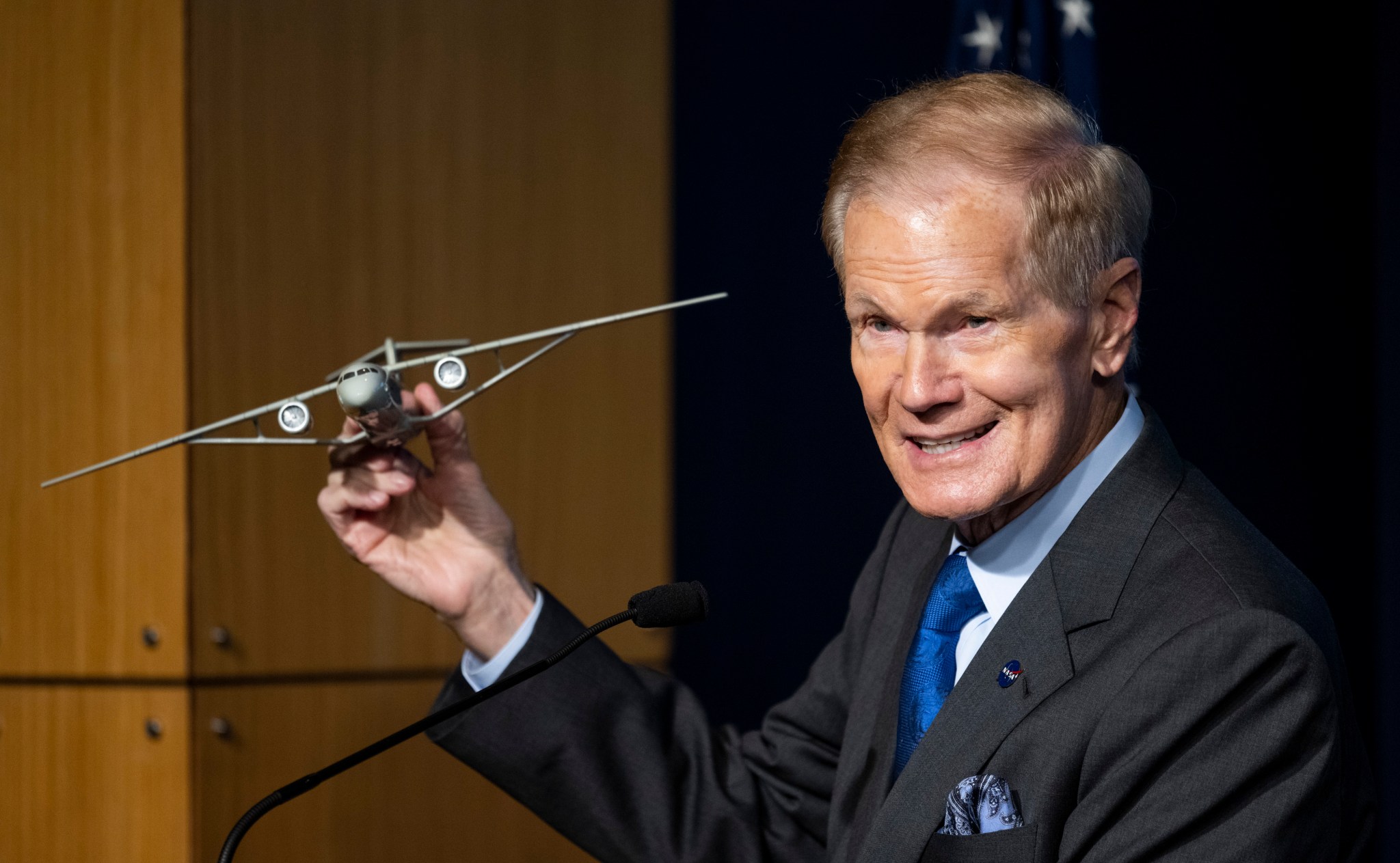
During load testing, researchers observed the interaction of the model strut and wing, as well as the forces affecting each, said Frank Pena, mock wing test director at the NASA Armstrong Flight Loads Laboratory. Until now, researchers had no calculations to estimate how forces transferred from the main wing to the strut. Information the team gathered from the model will enable them to calculate what will happen when NASA builds a larger wing.
“We identified early that we needed to learn more about how these structures with the strut respond to load and to see what additional information we may need for a calibration of a bigger structure,” Pena said. “We decided to use the load cell between the strut and the main wing to help us track down some of this missing information that otherwise could not be obtained.”
The Armstrong team will use the 6-foot model data to guide the design of a 10-foot version, in coordination with NASA’s Langley Research Center in Hampton, Virginia, which has worked on the TTBW concept for decades. The 10-foot wing will have a swept-back angle closer to the TTBW concept developed at Langley. It differs from the smaller wing version, which focused on testing instrumentation and methods. The larger wing will also have more representative connections between the fuselage and the strut and wing.
In addition to NASA’s current TTBW research, which began more than a year ago, the agency also made an award in January for a TTBW proposal submitted by The Boeing Company for the Sustainable Flight Demonstrator project. Boeing will work with NASA to build, test, and fly a full-scale demonstrator aircraft and validate technologies aimed at dramatically reducing fuel burn and carbon emissions. The project’s goal is to inform a new generation of single-aisle aircraft that will help the U.S. achieve its goal of net-zero greenhouse gas emissions by 2050.
While much of the hardware for the 6-foot mock wing was readily available to Flight Loads Laboratory staff, some parts required the sheet metal capabilities of NASA Armstrong’s Experimental Fabrication Branch, Pena said. For example, the root of the truss sweep angle and the angle between the wings of the aircraft – known as a dihedral – required custom components, along with the adaptor plate for the three-axis load cell interface.
Success in testing the 6-foot and 10-foot wings could provide additional information for deciding if researchers will use the NASA Armstrong-developed Fiber Optic Sensing System (FOSS) to gather data for the future full-scale Sustainable Flight Demonstrator aircraft. The sensing system can take thousands of strain measurements along an optical fiber about the thickness of a human hair, which could resolve some of the challenges in gathering data along the extra-long, thin wings. The team used it successfully with the 6-foot model.
“FOSS generated 125 gigabytes of data,” Pena said. “The testing was really smooth, and we finished it in one afternoon.”
The 10-foot wing design is expected to be complete this year, with testing at NASA Armstrong set for later this year or 2024.
The TTBW models, part of NASA’s Advanced Air Transport Technology project, are aimed at learning more about the concept and will indirectly benefit the Sustainable Flight Demonstrator. NASA Armstrong will also play other, more direct roles with the Sustainable Flight Demonstrator. These will include piloted simulation work, structural testing, technical expertise, flight testing, and the development of potential instrumentation and sensors. Armstrong will also provide facilities and equipment such as control rooms, radars, video tracking, hangars, and chase aircraft.