Lander Systems
A leader in Lander Systems, Marshall Space Flight Center has the capability to help you land anywhere in the solar system.
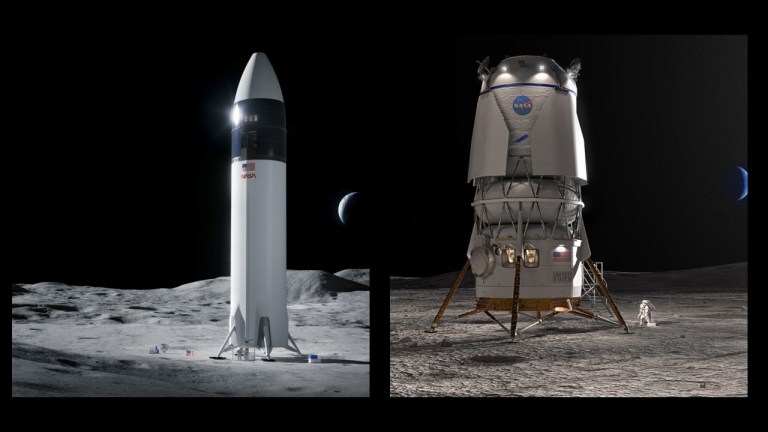
Contents
Overview
Advanced Manufacturing
Unique expertise in applying state-of-the-art advanced manufacturing methods to support development and production of Lander systems
Docking and Rendezvous Testing
State-of-the-art testing facility for simulating docking and berthing, with experience testing almost every U.S. docking and berthing mechanism ever developed
Flight Mechanics and Analysis
Cutting-edge, in-house-developed open-source simu-lation and software tools simulate integrated design elements from launch pad to mission completion
Extensive experience in the design, development, analysis, testing, and certification of GN&C algorithms for human-rated systems
Flight Software Development and Hardware-in-the-Loop Testing
State-of-the-art facilities for flight software development, testing, and formal verification
Real-time hardware-in-the-loop capabilities enable launch vehicle integrated software and avionics hardware systems to be modeled, simulated, and tested early, before finalizing designs
Propulsion Systems, Subsystems, and Components
Propulsion testing facilities enable testing of components, subsystems, subscale motors, and full-scale engines under a variety of configurations and conditions
Modeling and testing capabilities for lander systems, including Plume-Surface Interaction
Cutting-edge propulsion capabilities including 3D printed rotating detonating rocket engines
Space Environmental Effects and Lunar Environment Testing
Test capabilities to characterize the effects of the space environment on materials and systems, from low Earth orbit to deep space. Simulated elements of the space environment include charged particle radiation, plasma, high vacuum, solar ultraviolet (VUV, NUV), atomic oxygen, impact, thermal extremes, Lunar/Martian surface environments including regolith simulants, all either individually or in combinations
Structural Strength and Dynamics Testing
Multiple facilities provide proof, limit, failure, development, qualification, and flight acceptance testing
Decades of experience developing instrumentation for structural and propulsion-related test articles to maximize data return using high-speed data acquisition, visible and thermal imaging, and high-definition audiovisual capture systems
Concept and Trade Studies
Rapid development and analysis of physics-based models to yield an end-to-end design capability for preliminary concepts
Decades of experience in both launch vehicle and space systems design
Cryogenic Fluid Management (CFM)
Design and development of prototype CFM hardware, the creation and use of analytical models to predict subsystem performance, and the execution of ground-based tests using liquid oxygen, liquid hydrogen, and liquid methane to demonstrate the performance, applicability, and reliability of CFM subsystems
In-space Cryogenic Propellant Transfer
Development of systems enabling on-orbit refueling of cryogenic propellants
Do Business with Us
MSFC Partnerships Office
Nick Case
nicholas.l.case@nasa.gov
256.544.8789