Throughout NASA’s 43-acre rocket factory, the Michoud Assembly Facility in New Orleans, engineers are building all five parts of the Space Launch System’s core stage. For the first SLS flight for deep space exploration with NASA’s Orion spacecraft, major structural manufacturing is complete on three parts: the forward skirt, the intertank and the engine section. Test articles, which are structurally similar to flight hardware, and are used to qualify the core stage for flight, are in various stages of production and testing.
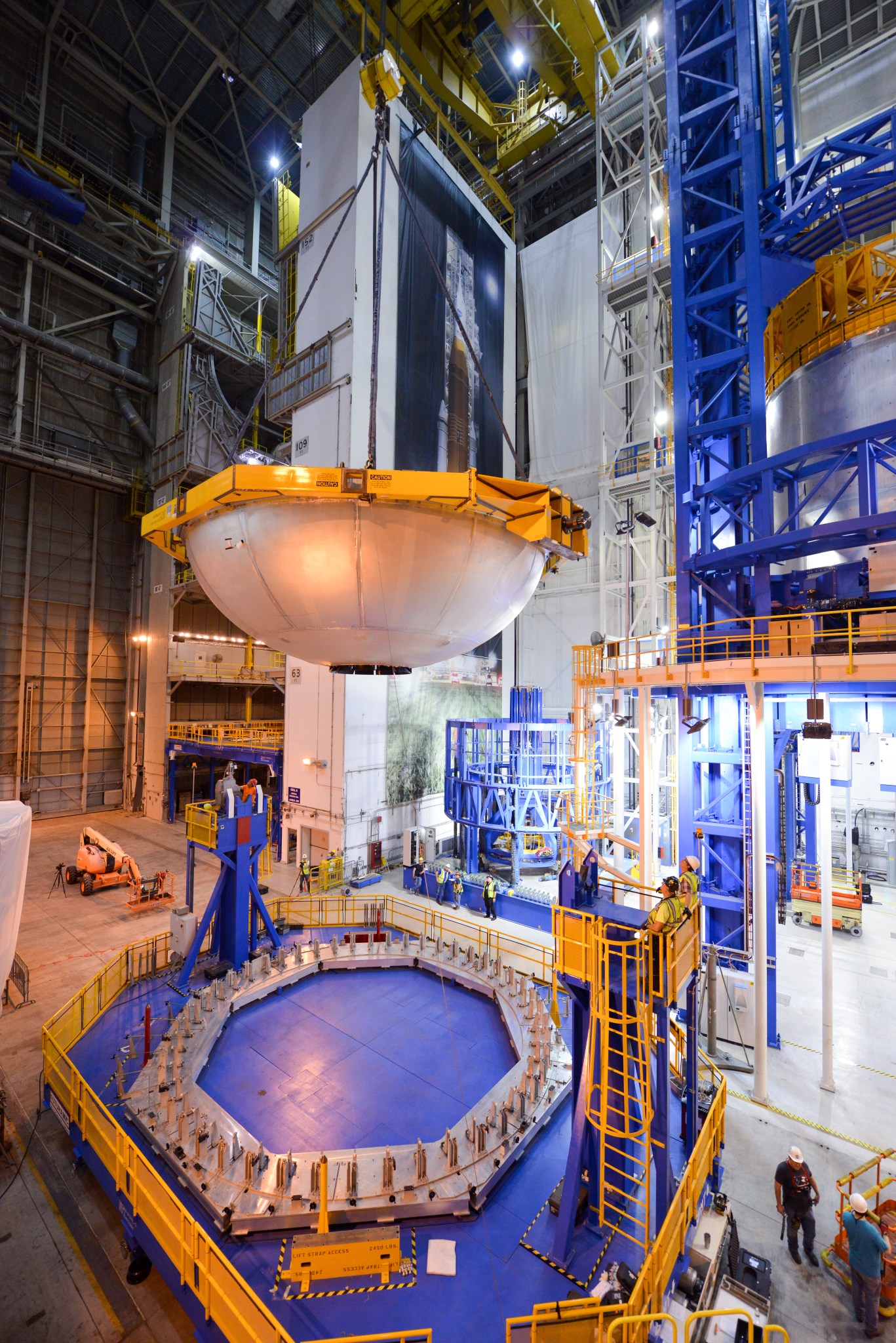
“One of the most challenging parts of building the world’s most powerful rocket has been making the largest rocket stage ever manufactured for the first time,” said Steve Doering, the SLS stages manager at NASA’s Marshall Space Flight Center in Huntsville, Alabama. “The 212-foot-tall core stage is a new design made with innovative welding tools and techniques.”
To build the rocket’s fuel tanks, Boeing, the prime contractor for the SLS core stage, is joining some of the thickest parts ever built with self-reacting friction stir welding. NASA and Boeing engineers and materials scientists have scrutinized the weld confidence articles and developed new weld parameters for making the liquid oxygen and hydrogen tanks for the first SLS mission.
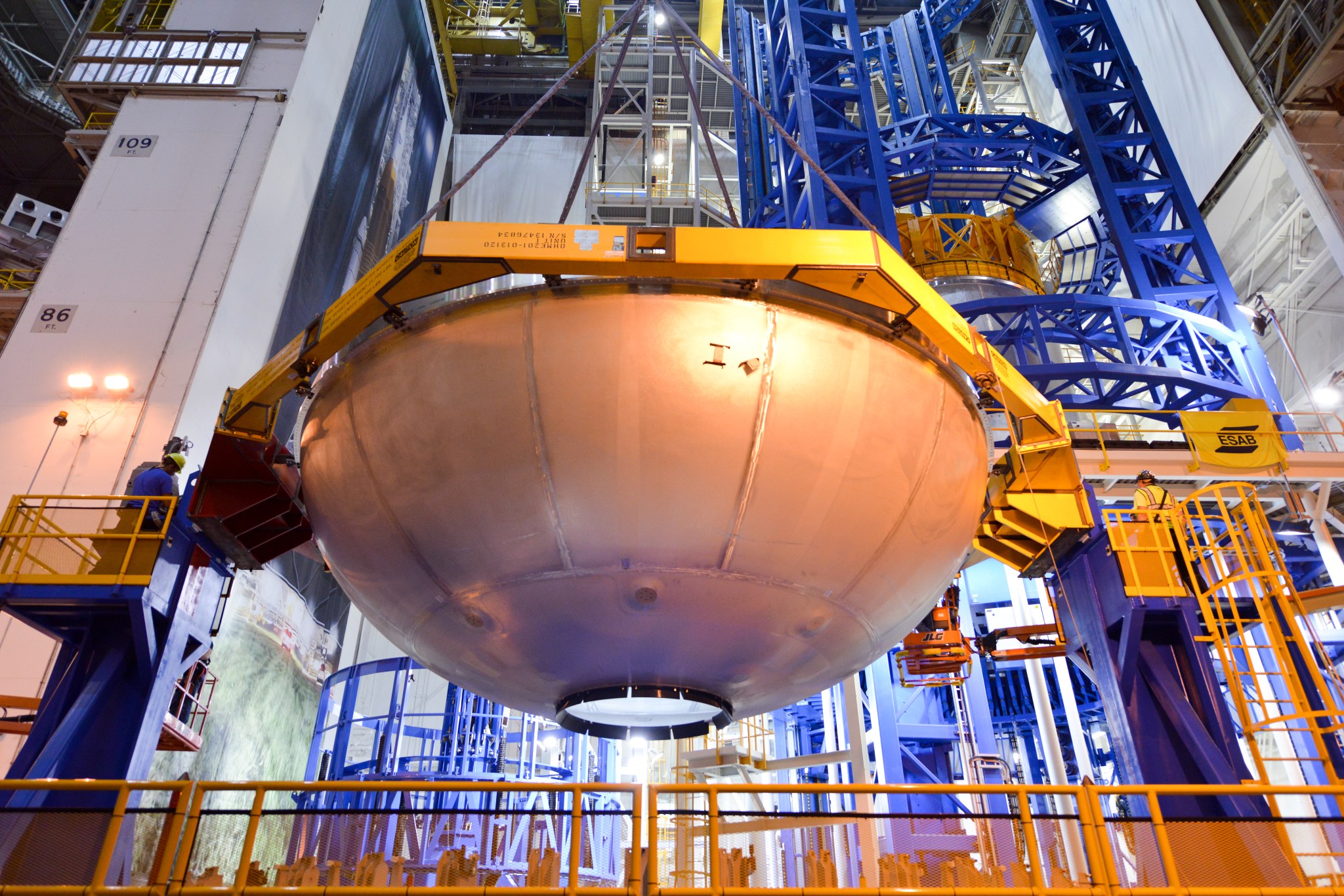
Resuming Welding in the Vertical Assembly Center
The Vertical Assembly Center, the large robotic tool where core stage parts are welded to form major structures, is expected to resume manufacturing next week. NASA halted production in early May after a liquid oxygen tank dome was inadvertently damaged during pre-weld preparations on the infeeder tool. This equipment is what positions the large dome for welding, or feeds it into the tank.
While the mishap investigation is still wrapping up, NASA and Boeing fully inspected the impacted dome and found while the hardware sustained minor damage, it is usable for its original purpose as part of a structural test article. The infeeder tool did sustain some damage during the incident and repairs to the tool are complete. Welding is resuming to finish construction of the liquid oxygen test article by adding the aft, or bottom, dome. Upon completion, the tank will undergo inspection for any flaws, final processing and proof testing.
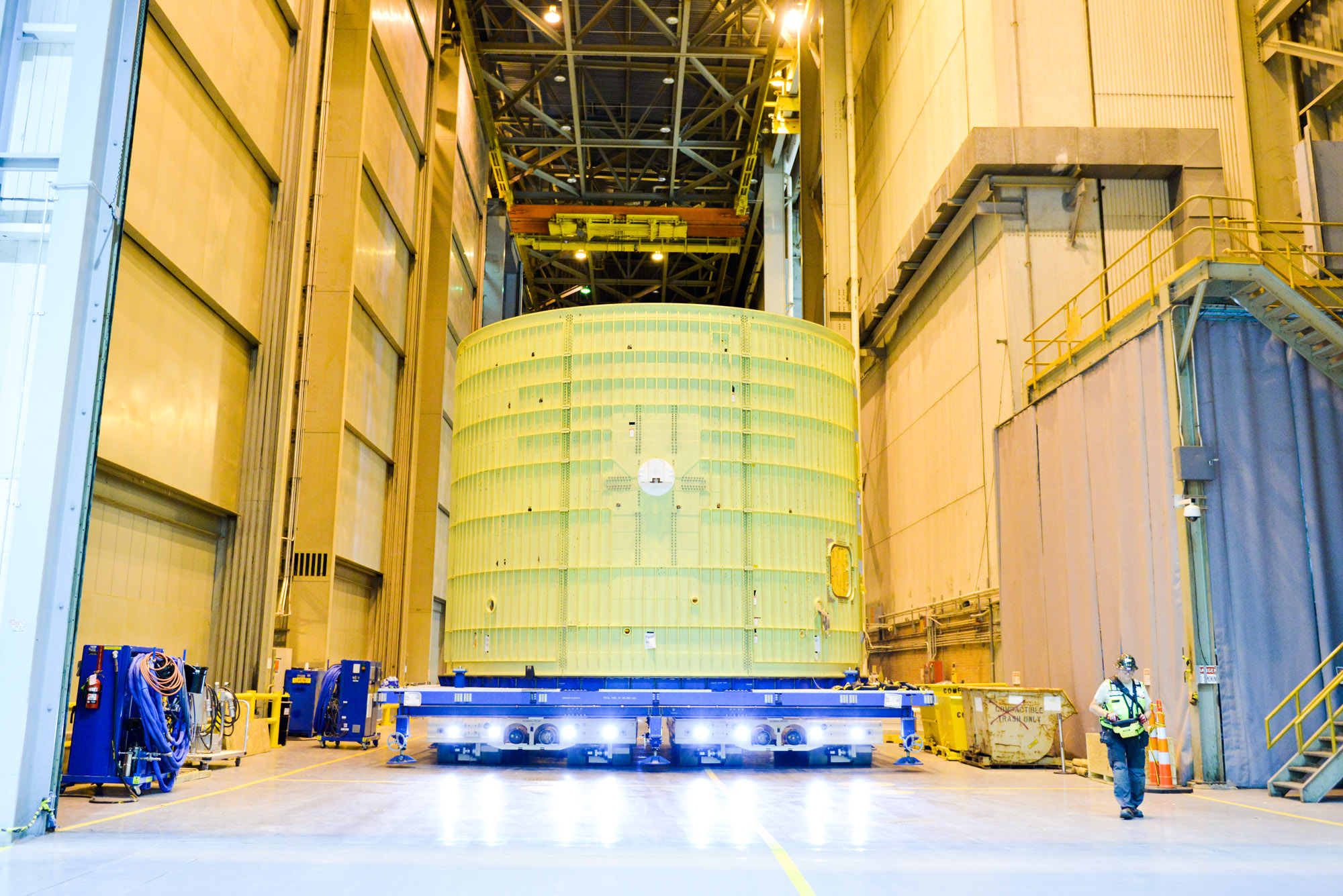
In another area of the factory, domes and segments for the flight liquid oxygen tank await their turn to be joined on the VAC, and Boeing is now completing welding domes and barrels that will make up the liquid hydrogen tank for flight. Recently, major structural construction was completed on flight hardware for the one part of the core stage structure not welded. The intertank walls are too thick to be welded, so its eight panels are connected with 7,500 bolts. The walls have to be extremely strong because of the force it feels from the solid rocket boosters attached to it. To complete assembly on the inside of the core stage, the team is outfitting the intertank along with the flight forward skirt and the engine section structures, with avionics, wire harnesses, tubing, sensors, and propulsion systems.
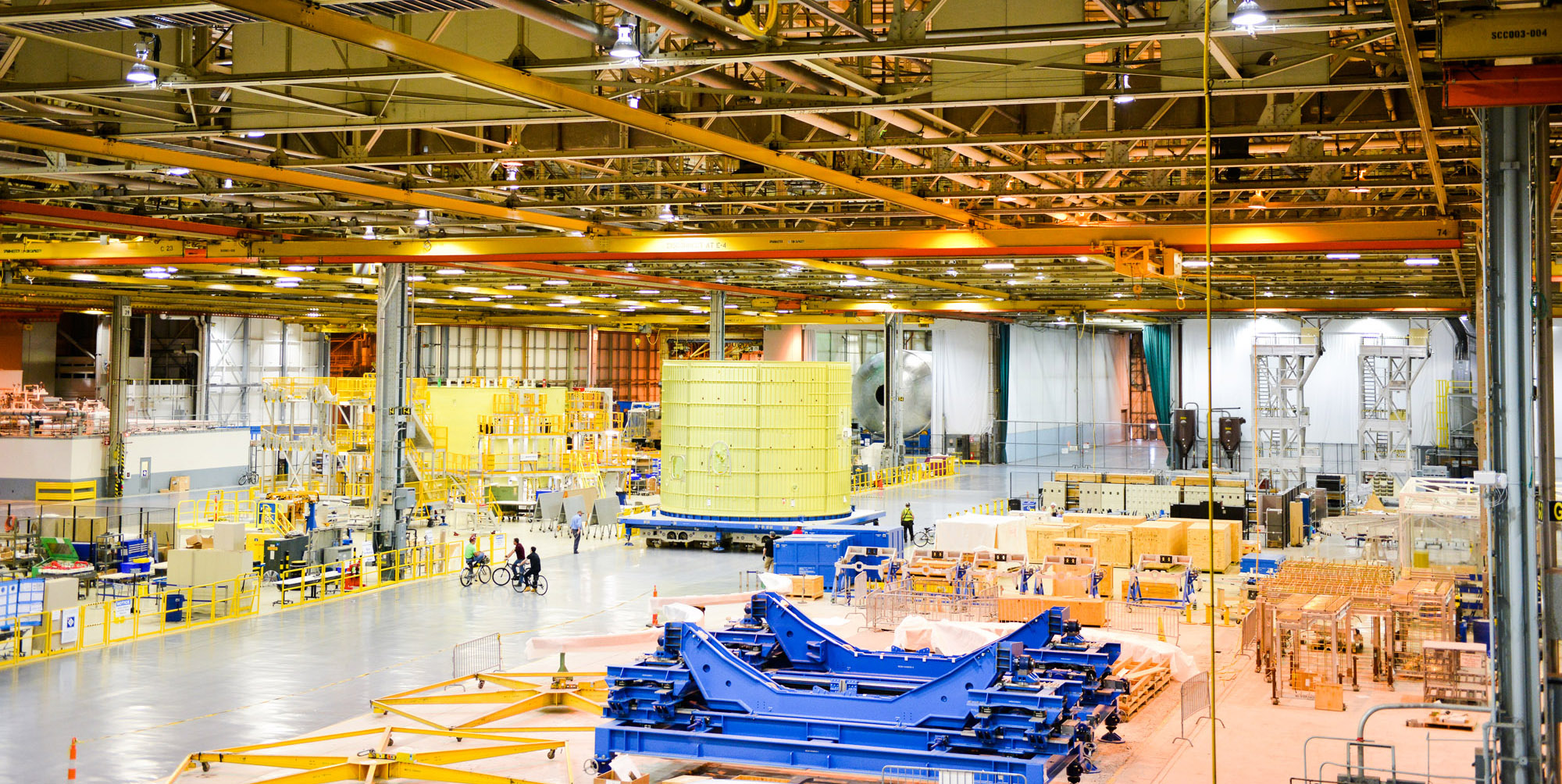
Preparing Hardware for Testing
NASA and Boeing continue to prepare existing hardware for tests to help ensure success of the first SLS flight and crew safety on future missions. Before the tanks are hooked up to feed propellant to the four RS-25 engines or through a test stand propellant system, the tanks have to be cleaned to avoid any contamination. Though the liquid hydrogen structural test article is not fueled, the tank has recently been moved to the cleaning cell to certify the process ahead of the flight tank.
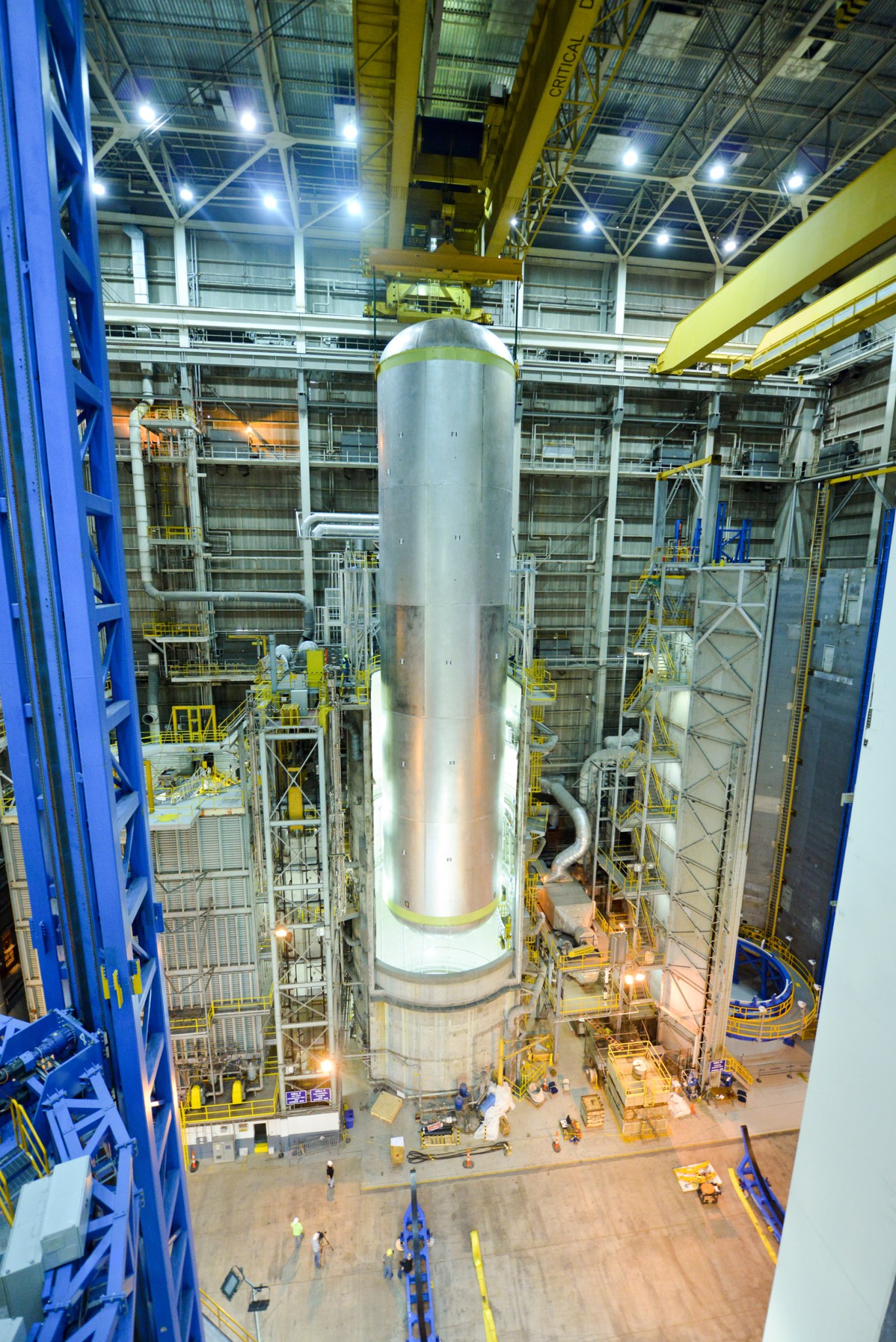
The first structural test article for SLS, an engine section which is similar to the flight article located at the bottom of the rocket’s core stage, is being installed on a test stand at NASA’s Marshall Space Flight Center in Huntsville, Alabama. Hydraulic cylinders will push, pull, twist and bend the engine test article to validate the design and ensure it can withstand the pressure expected during launch and ascent.
“We are conducting the largest NASA launch vehicle test campaign since space shuttle development,” said John Honeycutt, the SLS program manager at Marshall. “The team is focused on delivering hardware to the pad for the first launch. We just completed integrated structural testing for the stage that will send Orion out beyond the moon on the first flight. Now, we’ll be putting the core stage parts through the paces to gain an in-depth understanding of the rocket we are building for the first time as we expose parts of it to the extreme conditions of spaceflight.”
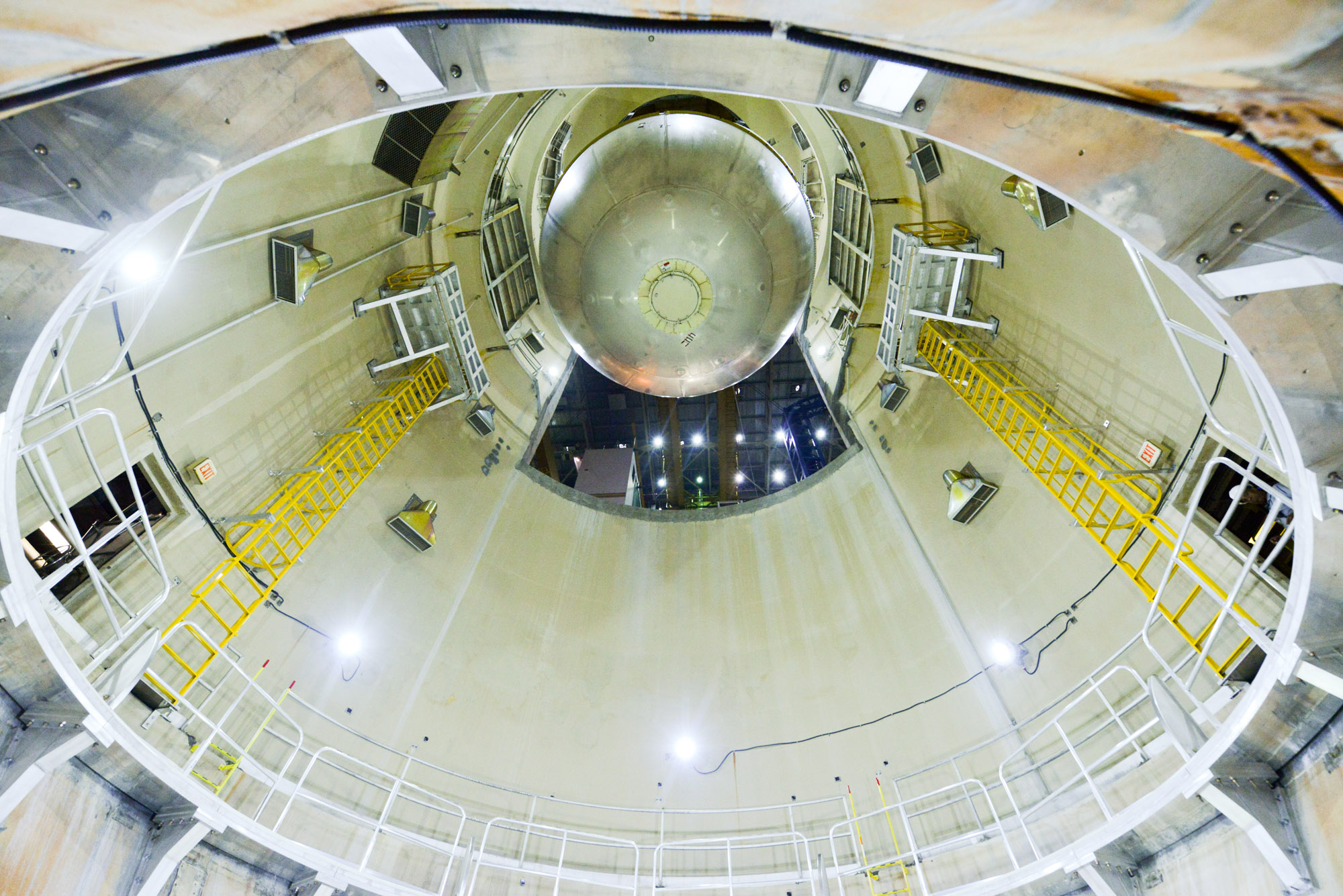