Teams of NASA researchers put their next-generation technologies to the microgravity test in a series of parabolic flights that aim to advance innovations supporting the agency’s space exploration goals.
These parabolic flights provide a gateway to weightlessness, allowing research teams to interact with their hardware in reduced gravity conditions for intervals of approximately 22 seconds. The flights, which ran from February to April, took place aboard Zero Gravity Corporation’s G-FORCE ONE aircraft and helped to advance several promising space technologies.
Under the Fundamental Regolith Properties, Handling, and Water Capture (FLEET) project, researchers tested an ultrasonic blade technology in a regolith simulant at lunar and Martian gravities. On Earth, vibratory tools reduce the forces between the tool and the soil, which also lowers the reaction forces experienced by the system. Such reductions indicate the potential for mass savings for tool systems used in space.
This flight test aims to establish the magnitude of force reduction achieved by an ultrasonic tool on the Moon and Mars. Regolith interaction, including excavation, will be important to NASA’s resources to support long-duration lunar and Martian missions.
This experiment represents the success of an international effort three years in the making between NASA and Concordia University in Montreal, Quebec.
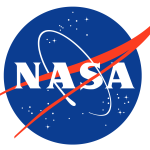
Erin Rezich
Project Principal Investigator
“This experiment represents the success of an international effort three years in the making between NASA and Concordia University in Montreal, Quebec. It was a NASA bucket list item for me to conduct a parabolic flight experiment, and it was even more special to do it for my doctoral thesis work. I’m very proud of my team and everyone’s effort to make this a reality,” said Erin Rezich, project principal investigator at NASA’s Glenn Research Center in Cleveland, Ohio.
The FLEET project also has a separate payload planned for a future flight test on a suborbital rocket. The Vibratory Lunar Regolith Conveyor will demonstrate a granular material (regolith) transport system to study the vertical transport of lunar regolith simulants (soil) in a vacuum under a reduced gravity environment.
These two FLEET payloads increase the understanding of excavation behavior and how the excavated soil will be transported in a reduced gravity environment.
3D Printed Technologies Take on Microgravity
Under the agency’s On-Demand Manufacturing of Electronics (ODME) project, researchers tested 3D printing technologies to ease the use of electronics and tools aboard the International Space Station.
Flying its first microgravity environment test, the ODME Advanced Toolplate team evaluated a new set of substantially smaller 3D printed tools that provide more capabilities and reduce tool changeouts. The toolplate offers eight swappable toolheads so that new technologies can be integrated after it is sent up to the space station. The 3D printer component enables in-space manufacturing of electronics and sensors for structural and crew-monitoring systems and multi-material 3D printing of metals.
“The development of these critical 3D printing technologies for microelectronics and semiconductors will advance the technology readiness of these processes and reduce the risk for planned future orbital demonstrations on the International Space Station.
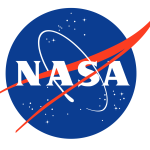
curtis hill
ODME Project Principal Investigator
NASA researchers tested another 3D printing technology developed under the agency’s ODME project for manufacturing flexible electronics in space. The Space Enabled Advanced Devices and Semiconductors team is developing electrohydrodynamic inkjet printer technology for semiconductor device manufacturing aboard the space station. The printer will allow for printing electronics and semiconductors with a single development cartridge, which could be updated in the future for various materials systems.
NASA’s Flight Opportunities program supported testing various technologies in a series of parabolic flights earlier this year. These technologies are managed under NASA’s Game Changing Development program within the Space Technology Mission Directorate. Space Enabled Advanced Devices and Semiconductors technology collaborators included Intel Corp., Tokyo Electron America, the University of Wisconsin-Madison, Arizona State University, and Iowa State University. The Space Operations Mission Directorate’s In-Space Production Applications also supports this technology. Advanced Toolplate Technology collaborated with Redwire and Sciperio. The Ultrasonic Blade technology is a partnership with NASA’s Glenn Research Center in Cleveland, Ohio, and Concordia University in Montreal, Quebec, through an International Space Act Agreement.
For more information about the Game Changing Development program, visit: nasa.gov/stmd-game-changing-development/
For more information about the Flight Opportunities program, visit: nasa.gov/stmd-flight-opportunities/