When we run into a snag designing a new space vehicle, it can be frustrating for the engineers, scientists, and technologists who have spent months and years getting to that point – but it’s also an opportunity for the team to spring into action and innovate a solution.
That’s just what happened with the Ares I, a previous rocket development effort for destinations including the Moon. Though NASA ultimately decided not to continue Ares development, a revolutionary device created to fix a vibration challenge in the rocket is still going strong, and its latest version is set to make offshore wind power more efficient and affordable.
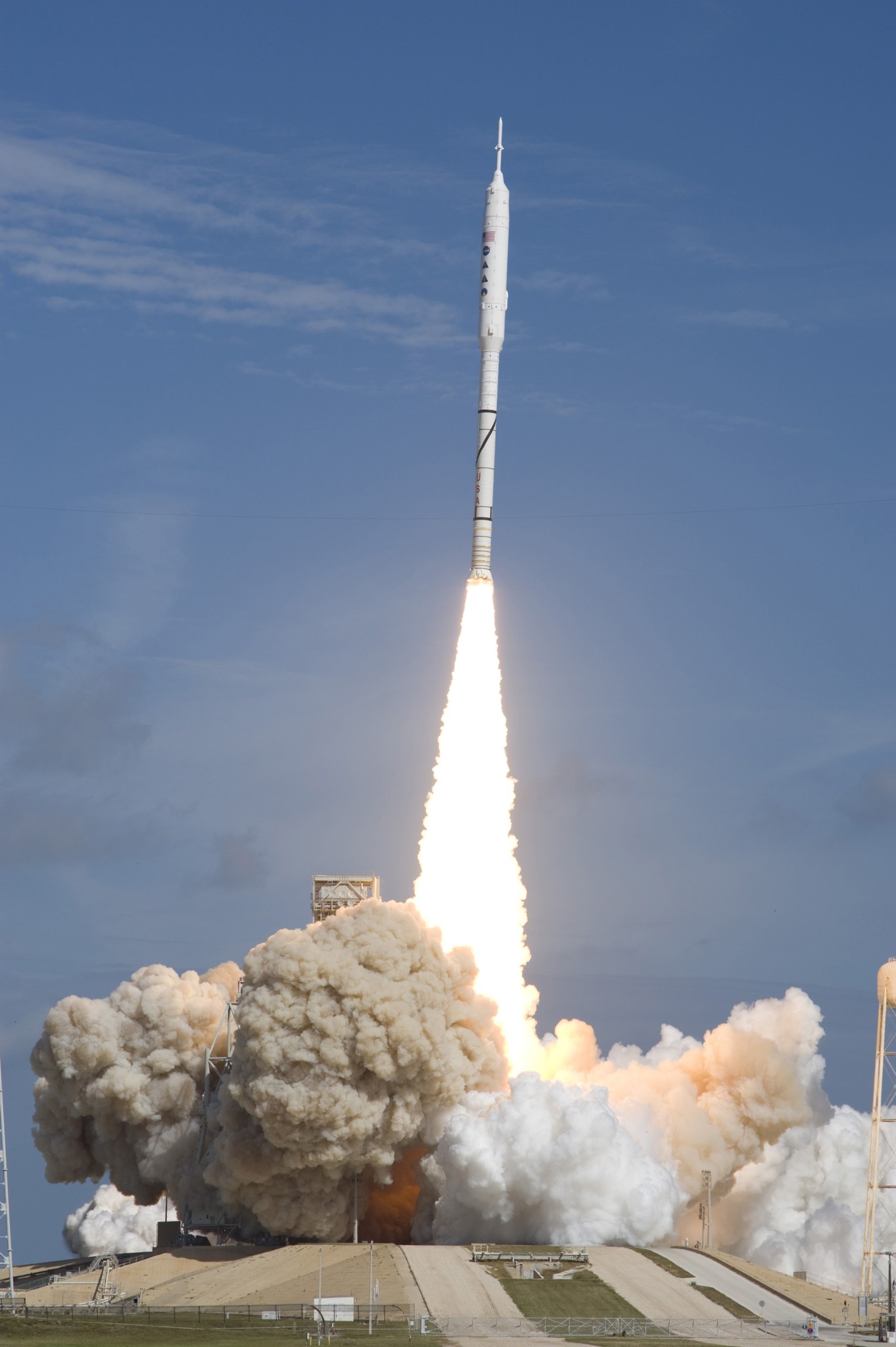
Any rocket is going to vibrate during launch. But if it hits what’s called a resonant mode, those vibrations can be excessive. Tried and true solutions for reducing or preventing undesirable resonant vibrations can require massive redesigns and can be very heavy. Adding more weight is not ideal on a rocket, where every added ounce must be accounted for, so engineers working on the Ares solid rocket booster had to think of something new to keep vibrations within a safe range for the astronauts that might ride along.
Engineers found a way to take advantage of something already on the rocket that had a lot of mass: the liquid fuel stored for the second-stage rocket. A small device loaded into the liquid was able to knock out 50 to 100 times more of the vibrations than they expected it to. They realized the device, which expands and contracts at a specified frequency, moves the fluid in time with the device instead of along with the spacecraft vibration. Essentially, the fluid acts as if it’s no longer part of the spacecraft, which changed the overall resonant response of the rocket.
The physics of it was so surprising, even to other engineers, that many said they didn’t believe it until they saw it for themselves. “It’s like the first time you saw an elevator, if you’ve never heard of an elevator before,” said Ikpoto Udoh, a senior engineer at Houston Offshore Engineering, an Adkins company, of the first time he saw the NASA device in action. “You just stand in front of it and someone steps in and the door closes, and someone else comes out of it a few minutes later.” In other words, almost like magic.
Life After Ares
After the Ares project was discontinued, the team, led by Rob Berry and Jeff Lindner at NASA’s Marshall Space Flight Center in Huntsville, Alabama, wanted to make sure this revolutionary device got put to good use. The Marshall team started by adapting it for buildings – to steady them in case of earthquakes or, in the case of very tall skyscrapers, even high winds – and a license was quickly snapped up by Thornton Tomasetti, a New York-based engineering firm.
Berry and Lindner weren’t done. They wanted to adapt the device, which they are now calling fluid structure coupling technology, for use in a maritime environment, like offshore platforms. After all, the device works best with fluid masses, noted Berry, and “one of the logical places where there is a lot of fluid is in maritime environments.”
He knew they needed to demonstrate it, however, before the maritime industry would be ready to sign on. “Our goal was to show the industry that this technology applies to their use cases, that it does work, and that it is implementable. They loved the idea, for a building, but nobody wanted to take that leap, so we had to go show it,” Berry said.
To do that, Berry teamed up with the University of Maine in 2018, which has a wave tidal pool to simulate maritime conditions and a subscale wind turbine to test the device on.
With a small investment of around $90,000 from NASA’s Technology Transfer program as well as additional seed funding from the university, they set up a test case, with impressive results. They were able to knock out about 90% of the up and down motion with the device. In other words, the wind turbine bobbed up and down in the waves with the device turned off, but essentially sat level with it turned on, even as the waves continued to roll by.
Cheaper, More Efficient Wind Energy
That demonstration is already paying dividends. Thanks in part to the results, Houston Offshore Engineering is exploring using the device on its offshore platforms.
The company, as well as the University of Maine, separately received funding to develop the technology from the Department of Energy’s ATLANTIS project, which aims to reduce the cost of offshore wind energy to make it more competitive with widespread but less environmentally friendly energy sources. The DOE is interested because, while land-based wind farms have started to gain traction in parts of the U.S., offshore wind offers several advantages. For one, wind speeds over water tend to be faster and steadier, which means more, and more reliable, energy. And offshore wind is particularly beneficial for coastal urban areas, where land space is at a premium – and where more than half the U.S. population already lives.
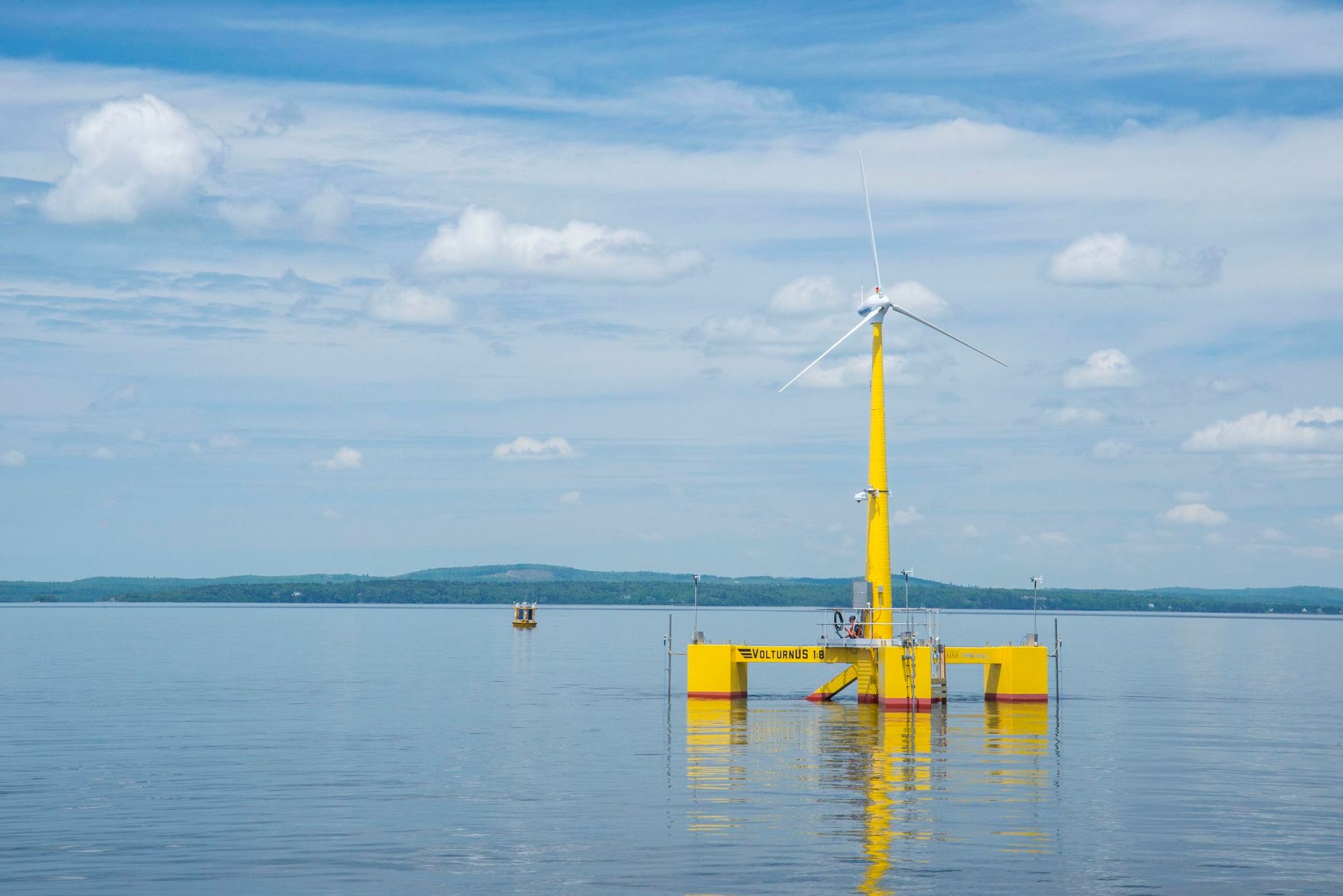
Their two proposals, which plan to leverage the NASA device, were among just 13 winning proposals out of many hundreds of entries.
That’s because, by reducing the platform’s motion in the ocean, the fluid-structure coupling dampers make wind turbines significantly more efficient at producing energy. “When the platform pitches about dynamically, it affects the ability of the blades to capture sufficient wind in a consistent way,” explained Udoh.
Making the platform heavier can also reduce that motion but significantly increases the cost. With a fluid structure coupling device damping the movement instead, that opens the possibility of getting high energy generating performance out of a much smaller, less expensive platform, explained Chris Allen, a research engineer at the University of Maine, who led the project with Anthony Viselli, the manager of offshore model testing and structural design at the university’s Advanced Structures and Composites Center.
“This is what we’re looking at here, an out-of-the-box type of idea to reinvent the way people look at offshore wind,” Allen said, adding that “if we can be successful implementing this in offshore wind turbines, we could really be ahead of the game at being able to deliver offshore wind energy at an incredibly competitive price.”
Berry said, “the space agency does this because it’s in the best interests of taxpayers and industry to get this technology out there. And we also know the secondary benefit back to NASA is that we would learn more about the physics of this new technology.”
“Everybody wins in this one. There are no losers.”
NASA has a long history of transferring technology to the private sector. The agency’s Spinoff publication profiles NASA technologies that have transformed into commercial products and services, demonstrating the wider benefits of America’s investment in its space program. Spinoff is a publication of the Technology Transfer program in NASA’s Space Technology Mission Directorate. For more information on how NASA is bringing its technology down to Earth, visit:
By Naomi Seck
NASA’s Spinoff Publication