Clutching a brace of arrows in its left talon and an olive branch in its right, the bald eagle on the Great Seal of the United States symbolizes the nation’s desire for peace, but also readiness for war. For manmade birds of prey – military aircraft – Langley would play an essential role in improvements and enhancements. Langley, born one year before the end of World War I, tackled some of the most daunting challenges faced by U.S. fighters, bombers and reconnaissance aircraft.
As Langley expanded and matured during the 1920s and 1930s, military planners took advantage of the laboratory’s capabilities. Prior to the outbreak of World War II, by the late 1930s, Langley was called upon by aircraft companies and the military to examine the latest American military airplane prototypes. Lives would depend on how fast warplanes flew and how efficiently they used fuel. Streamlining an entire aircraft surface as much as possible – drag reduction, or “cleanup” – significantly improved military airplane performance.
Additional Langley wartime efforts focused on stability and control issues, compressibility effects that plagued planes as they tried to go faster, ditching, and studies related to seaplanes. Langley was also enlisted to develop means and methods for helicopters to search for and rescue military personnel separated from their units during battle.
Although sharply divergent in purpose and intent, civilian and military aviation share common technologies. In the decades to come, Langley research would lead to such advancements as more efficient structures and components, advanced wing designs, robust digital controls, and glass cockpits, among other innovations.
The U.S. Department of Defense continues to seek Langley’s help in assessing competing aircraft designs. Langley’s extensive aggregation of wind tunnels, simulators and computational facilities are routinely used for military-airplane and helicopter evaluations and refinements. The Defense Department frequently requests the participation of Langley on review boards and accident investigations, and works with Langley researchers to solve other problems as they occur.
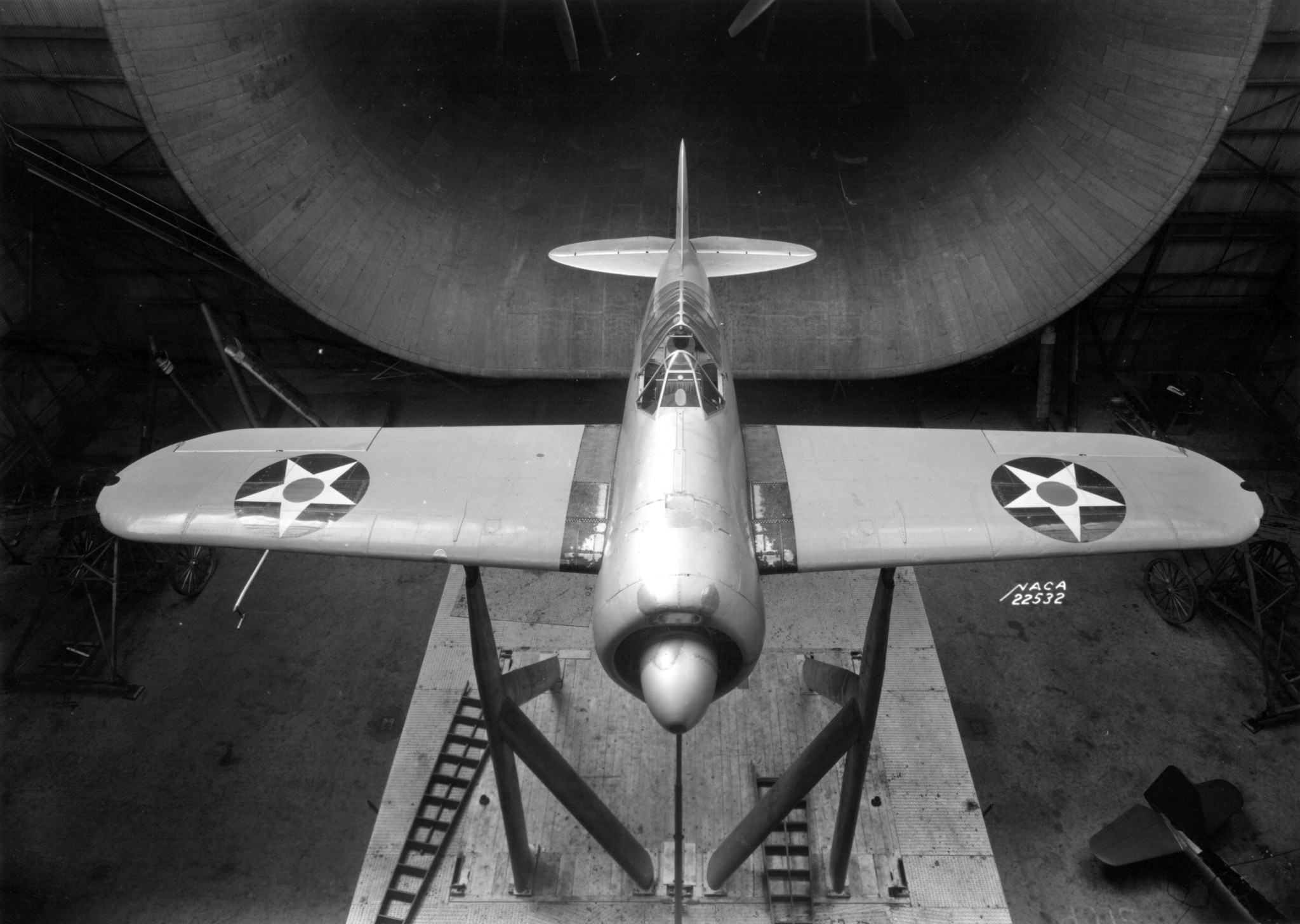
Turning the War Tide
Improvements in aircraft speed, range and maneuverability ultimately helped turn the World War II tide in favor of the Allies. Langley took center stage with work on fighter upgrades, none perhaps more important than drag cleanup.
Studies began with installation of a full-size aircraft in a full-scale wind tunnel, taking off all antennas and other items sticking out from the aircraft body, and then covering the entire airplane surface with tape. Measurements were made of the resultant smoothed surfaces. Gradually, engineers would remove the tape strips and determine the drag created by every part of the airplane. Subsequent reports identified areas of concern and made recommendations on how to correct them. Flight tests usually followed to confirm the drag-cleanup recommendations, and to help industry and the military in the quest for maximum performance.
As a result of drag cleanup, the P-51 Mustang went on to become a highly effective long-range escort support for heavy strategic bombers, outclassing most enemy fighter opposition in aerial combat. Back in the lab, work continued on ways to further decrease drag on wings. Research also intensified on aircraft spin, a potentially fatal downward loss-of-control spiral. Both the U.S. Army and the Navy required that every fighter, light bomber, attack plane and trainer be tested in spin tunnels, work that contributed to changes in airplane tail design, a factor instrumental in helping pilots recover from high-speed dives.
Langley research helped with the development of wartime dive-recovery flaps, components that helped pilots overcome compressibility, the change in airflow over wing surfaces as aircraft approach the speed of sound. Other crucial projects involved means of strengthening a bomber fuselage and bomb bay doors to enable aircrews to withstand water impacts as a plane ditched, and modifications to seaplanes so pilots wouldn’t lose control as their craft bobbed and dipped during takeoffs and landings.
Refining Vertical
As challenging as was the invention of forward-flying airplanes, even more daunting was the issue of vertical flight. Although the first practical helicopter didn’t appear until the mid-1930s, one of Langley’s earliest projects was testing in 1922 of several “helicopter propellers.” The helicopter’s predecessor, the autogyro, was studied at Langley, work that formed the basis for better understanding of rotor aerodynamics, rotor aeromechanics and blade structural dynamics, all put to use to enhance and optimize helicopter operation.
In the 1920’s and 1930’s instrumentation to analyze and assess helicopter performance wasn’t usually commercially available, so Langley made its own from scratch. By World War II, basic research at Langley proceeded on a wide range of rotary-wing flight topics. By the time the war ended, the helicopter had flown in combat, proved its value as a life-saving craft, and was adapted for both land- and sea-based operation.
In the decades following, Langley, in a partnership with the U.S. Army that officially began in 1965, used an emerging suite of computerized tools and sophisticated wind tunnel tests to assess vertical lift structures, components, control systems and vehicle integrity. Military helicopter models and components were instrumented and evaluated. Full-scale vehicles were likewise studied, especially as vertical takeoff and landing – known as V/TOL – hybrid aircraft were introduced.
Most recently, crashworthiness tests of a highly instrumented former Marine helicopter were conducted at Langley’s Transport Rotorcraft Airframe Crash Testbed, results from which will be geared toward improving rotorcraft performance and efficiency, and protecting passengers and cargo by boosting fuselage durability in the event of an accident.
For decades of contributions to the advancement of helicopters and other vertical flight aircraft, in 2015 Langley was recognized by the AHS International Corporation as a Vertical Flight Heritage Site.
Powerful with Little Equal
Fast, powerful, and sporting the most advanced electronic instrumentation available, modern American military aircraft have little equal worldwide. Langley’s work ensured that high performance continued as an airfleet hallmark. Support of and participation in critical military development programs progressed into the early 1990s as Langley teamed with U.S. Army, Air Force and Navy research organizations. The military received assistance from Langley expertise, facilities and problem solving, while researchers obtained data to validate Langley technology and predictive methods.
Specific Langley help included tests of the F-22 Raptor fighter in Langley’s 20-Foot Vertical Spin Tunnel; the effects of external weapons on aerodynamics of the F-117 stealth attack aircraft in the Langley 16-Foot Transonic Tunnel; and Langley-overseen drop-model tests of the spin resistance of the F/A-18E Super Hornet at NASA’s Wallops Flight Facility. In the latter case, Langley also addressed the vexing problem of Super Hornet “wing drop,” an abrupt and uncommanded rolling motion of the aircraft during certain flight conditions. The solution: structural modifications to a small section of the upper surface of the wing at the point where it folds for aircraft carrier operations
Langley also played a major role in military transport development. Langley’s contributions to the C-17 Globemaster III included a powered-lift concept used for the airplane’s short-field performance, in which wing flaps divert the engine exhaust downward for increased takeoff and landing performance; supercritical wing technology for increased aerodynamic cruise efficiency; winglets positioned at the wingtips for increased aerodynamic efficiency; and composite structures for greater fuel efficiency and range. For the C-130 Hercules series, Langley research helped with the craft’s composite wing structures and materials, computer-based methods for design and structural analysis, and glass cockpit displays featuring liquid-crystal flat-panel technology.
Langley continued to research propulsion, thermal and structural integration issues on a number of largely military hypersonics programs through the end of the century, including the National Aerospace Plane; the Hyper-X, which included the U.S Air Force X-43; and the Air Force X-51 Waverider and the Hypersonic International Flight Research Experimentation (HIFiRE) Program, which explored fundamental technologies supporting practical hypersonic flight. Within the last several years, Langley was also a key technology player in development of hybrid wing/blended wing body aircraft concepts for possible use as future military cargo planes.