When the crisis calls come, NASA Langley springs into action – and its researchers can have the last word in figuring out mishaps in space, in the air, and on the ground. Determining the whys and hows can prevent future incidents, protect life and limb, and thwart disasters.
Langley’s long history of aeronautical expertise has been put to use in some of the deadliest occurrences experienced during flight. Among those are structural issues, usually due to unanticipated interactions between aircraft components stressed by takeoffs and landings, as well as environmental conditions aloft. Such was the case with the Lockheed L-188 Electra, a turboprop-driven airliner, two flights of which crashed, first in 1959 in Texas and again in 1960 in Indiana.
Researchers working in Langley’s new Transonic Dynamics Tunnel pinpointed the cause: “whirl mode flutter,” a wobbling motion generated by frequency interactions between the Electra’s large propellers and its too-flexible wings, which shook themselves apart in flight. Extensive modifications to the Electra’s superstructure and wing mounts solved the problem. Upgraded Electras flew without in-flight incidents through the 1980s. The basic Electra design was used in building the U.S. Navy’s P-3 Orion, the foundation of the nation’s airborne anti-submarine warfare effort.
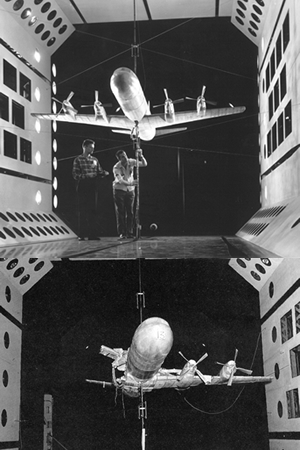
Explosive decompression and peel-back of a top portion of the fuselage of Aloha Airlines Flight 243 occurred in 1988. Langley researchers helped pinpoint the cause: areas of corrosion and metal fatigue around rivet areas. Takeoffs, landings and continual air-pressure changes weakened connecting fuselage joints. Changes in maintenance procedures and manufacturing techniques eliminated any reoccurrences.
The incident led the Federal Aviation Authority (FAA) to instigate its Aging Airplane Program to monitor and correct any aging-related issues that could affect the commercial air fleet. For its part, Langley developed a series of noninvasive diagnostic measures to find cracks and corrosion in aging aircraft before they propagated into anything serious.
But perhaps the most significant emergency-prevention work done by Langley was in the 1980s and 90s to help aircraft detect and avoid wind shear, an enormous down-flow of air in the vicinity of large thunderstorms that was implicated the loss of hundreds of lives in crashes, usually during airplane takeoffs and landings. Langley researchers helped develop radar and sensor arrays that identified oncoming shear, as well as procedures enabling pilots to outfly or avoid it altogether. By the late 1990s, an FAA requirement had led to the installation of wind shear detection systems on all commercial aircraft.
Warbird Snafus
Although commercial and military aircraft share many of the same aeronautical technologies, military aircraft have their own suite of high-performance demands and potential issues. Such was the case for the U.S. Navy’s aircraft carrier-based F/A-18E/F Super Hornet fighter, versions of which had yet to be vetted for full-scale production.
During the winter of 1997-98, the Navy asked NASA to help resolve the problem of “wing drop,” an abrupt, un-commanded rolling motion that can occur during high-speed, high-g maneuvers, and prevent pilots from performing close-in tracking maneuvers on potential adversaries. Langley engineers devised a solution: a technology known as passive porosity. Applied to a small section of the upper surface of the Super Hornet wing at the point where the wing folds for carrier operations, the structural modification resolved the wing drop problem, enabling the Department of Defense to approve unrestricted production.
NASA also became involved with a vexing problem involving the F-22 Raptor fighter: breathing difficulties for pilots during high-gravity maneuvers that led to degraded motor skills, even loss of consciousness. Almost two dozen such incidents were noted, including one death, before the Raptors were temporarily grounded in 2011. Working with the U.S. Air Force and the U.S. Navy, a safety office housed at Langley – the NASA Engineering and Safety Center – identified several interlocking causes such as cockpit pressure changes, faulty oxygen-supply valves, an inadequately designed torso pressure vest, and lack of a robust oxygen backup system. The crisis concluded as redesigns and retrofits took hold in 2012.
Not all military craft are fast-fly fighters; there are those that can take off vertically and then hover over a given spot. But even for precisely positioned helicopters, danger can come quickly. Near-Earth maneuvers, especially those undertaken close to guy wires and telephone and electrical lines, can entangle rotors and cause loss of lift and crashes. The solution: a wire strike protection system, or WSPS, largely two blade-type devices made of hardened steel and attached to the top and bottom of the helicopter fuselage. During a wire strike, the cables slide either up or down the front of the helicopter, are caught, notched and then severed.
Pendulum swing tests conducted at Langley’s Impact Dynamics Research Facility in the late 1970s involving a U.S. Army a UH-1H helicopter fitted with the WSPS confirmed its effectiveness. Most military and some commercial helicopters have been outfitted with WSPS, dramatically reducing the threat from collision.
Shuttle Return to Flight
In the history of manned spaceflight, perhaps no missions were better known globally than those flown by NASA’s fleet of space shuttles. Between the first launch of Shuttle Columbia in April 1981, and the final landing of Shuttle Atlantis in July 2011, NASA’s shuttle fleet – Columbia, Challenger, Discovery, Atlantis and Endeavour flew 135 missions, helped construct the International Space Station, and inspired young and old alike as crews broadcast shuttle astronauts’ work and spacewalks from orbit.
Langley mourned with the nation and the world as Shuttle Challenger disintegrated during climb to orbit in January 1986. Once the shock had worn off, researchers set to work, helping a NASA team develop ways to improve shuttle components. In studying the four segments of the shuttle’s two solid-fuel boosters, Langley specialists devised a new joint design, intended to upgrade the original O-ring connectors. The failure of one of the thick rubber O-rings to properly seal led to Challenger’s destruction.
Eighty-eight missions and 15 years later tragedy struck once again with the loss of the orbiter Columbia in 2003. Langley researchers immediately lent their expertise to help NASA understand what happened and how to avoid a similar accident. Columbia broke apart during the heat of reentry because a piece of external tank foam that struck the orbiter during launch damaged its thermal protection system (TPS).
Langley focused its technical strengths on the TPS: its failure modes, how it could be inspected without physical damage, how to repair it on orbit, and when it was safe to fly a shuttle even with minor TPS damage. Following up such efforts, Langley researchers also conducted wind tunnel tests to ensure that minor damage and repairs to tiles or wing leading edges would not overheat the shuttle upon return to Earth. That work bore fruit; on July 26, 2005, ending a two-and-a-half-year shuttle-fleet hiatus, Space Shuttle Discovery flew to orbit, launching without incident from the Kennedy Space Center.
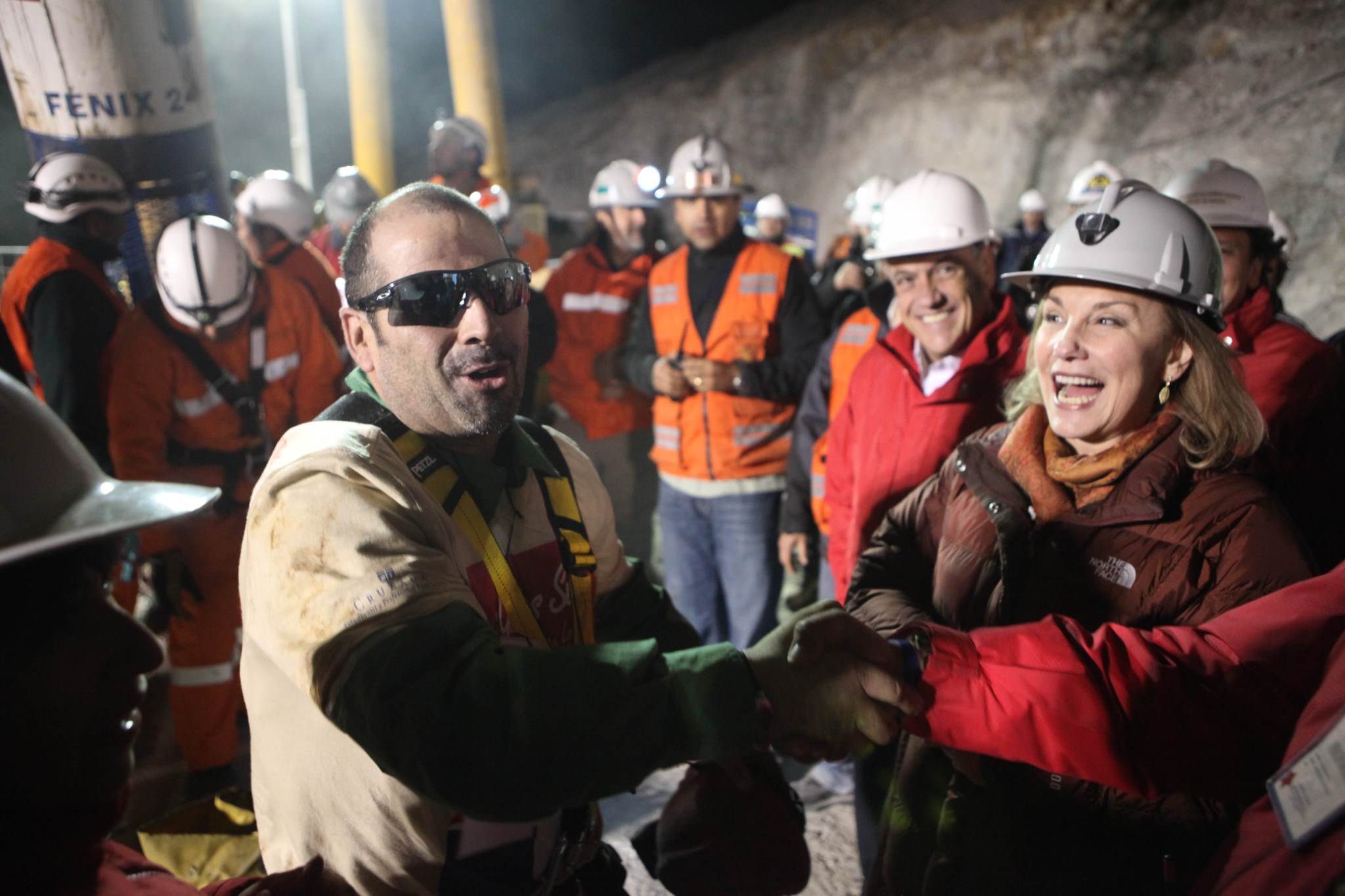
Help on the Ground
In 2004, Langley became the host of NASA’s Engineering and Safety Center (NESC), largely created in response to the Columbia accident investigation. Organized into technical discipline teams, the NESC pulls expertise from 10 NASA centers, and draws upon the knowledge of experts from academia, industry and other government agencies to make preventative and corrective recommendations.
The NESC played a major down-to-Earth role beginning August 5, 2010, upon the collapse of a copper mine in northern Chile that trapped 33 miners. After 17 days of intense digging and searching, all 33 were found alive, but rescue from a blocked tunnel proved a daunting challenge. The solution was design of a one-person, 13-foot-long, 926-pound capsule that a single miner could enter and secure without help.
The capsule featured exterior rollers and a trap door in the bottom. The rollers cushioned the ride up, reduced friction with tunnel walls, and lessened the possibility the capsule would get stuck midway, while the trap door allowed the rider an exit to repel back down in case it did stick. An oxygen tank provided an emergency air supply, there was an audio/video feed for communication with the rider during the transit, and medical probes like heart monitors were included so rescuers could check vital signs during the trip up.
Sixty-nine days later, on October 13, all 33 miners were above ground. None perished.
Sticky Accelerators
After a series of highly publicized accidents and deaths from sticking accelerator pedals on several Toyota car models, the National Highway Traffic Safety Administration (NHTSA) called upon the NESC in March 2010 to pinpoint the cause. Despite consumer claims that electronic and software systems were at fault, an exhaustive effort by NASA researchers found no evidence to support the assertions. The final NHTSA report identified two mechanical safety defects: design flaws that kept accelerator pedals depressed, or allowed the pedals to be trapped by floor mats.
Toyota recalled nearly 8 million vehicles in the United States for repair. In 2014, the company agreed to a $1.2 billion criminal penalty imposed by the U.S. Justice Department for concealing the defects from the general public. It was the largest federal settlement by a carmaker in American history.