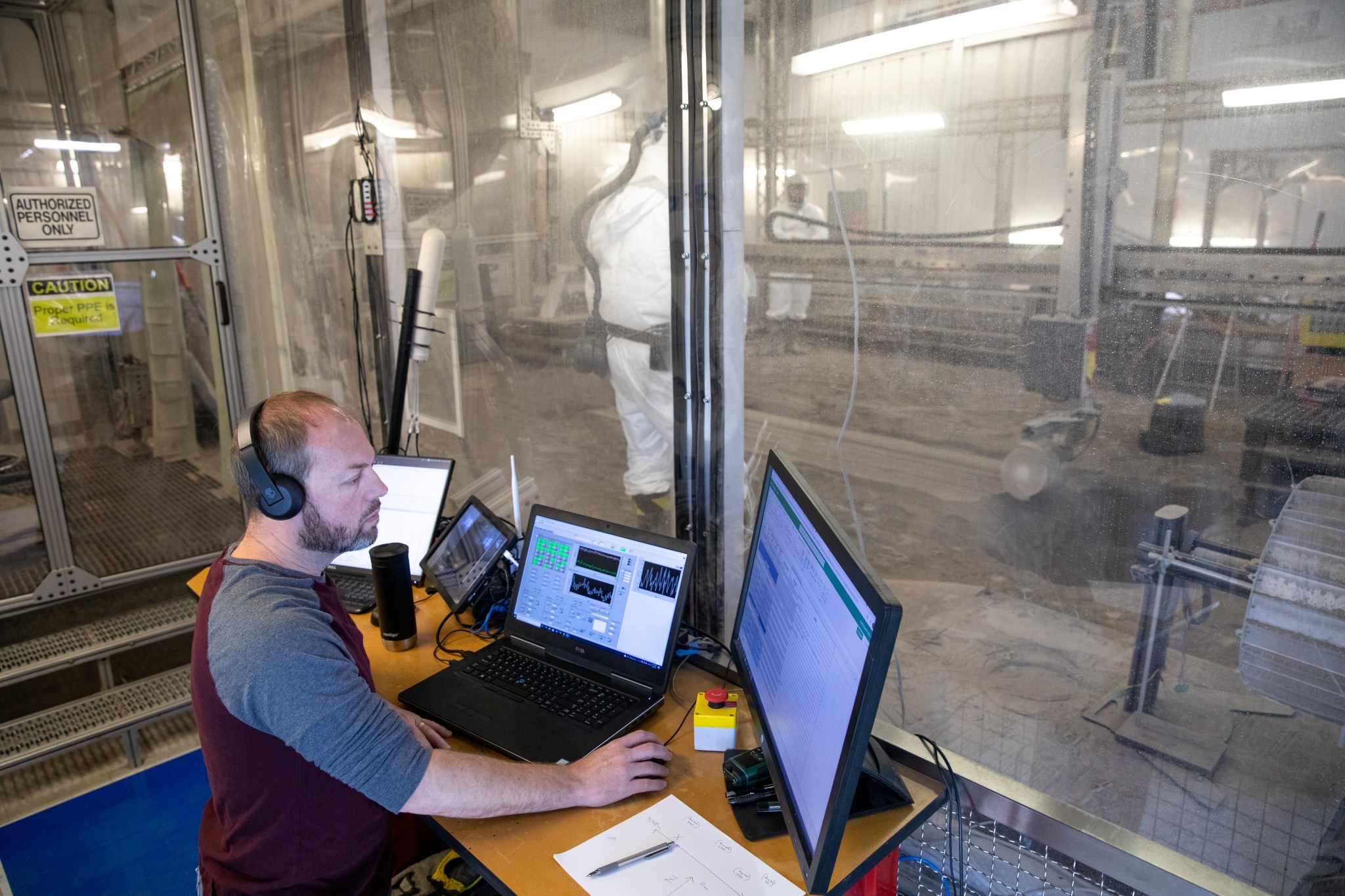
By Jim Cawley
NASA’s Kennedy Space Center
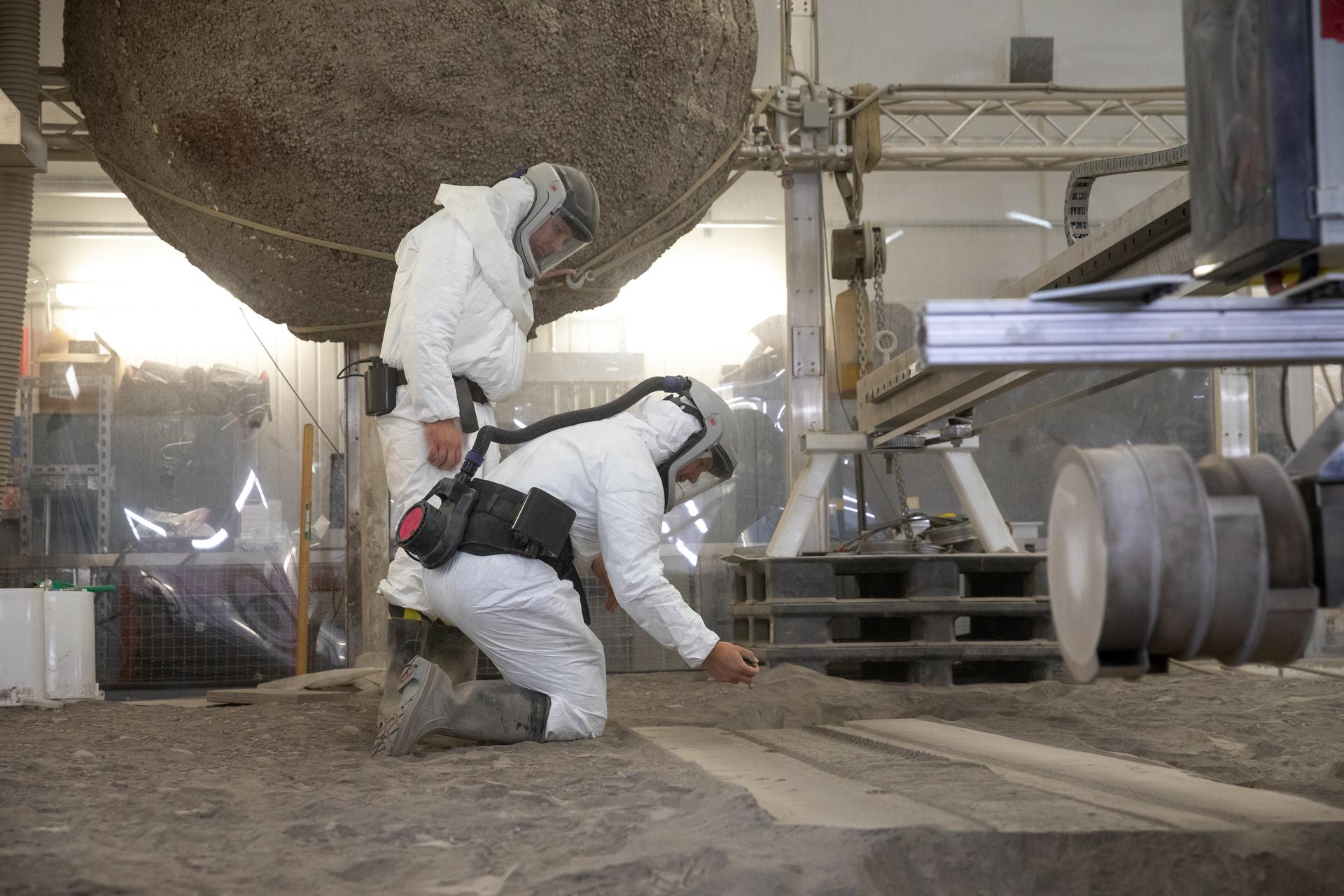
A team at NASA’s Kennedy Space Center is utilizing a new 3D software tool that benefits Artemis, the agency’s campaign to establish the first long-term human presence on the Moon in preparation for crewed missions to Mars.
Kurt Leucht, a software engineer at the Florida spaceport, was creating online tutorials for NASA’s Break the Ice Lunar Challenge, an event aimed at encouraging the public to develop technologies for a sustained human presence on the Moon. While using actual lunar elevation data captured by NASA spacecraft for developing the simulation environment for the contestants’ robots, he was struck with an idea.
“Once I saw the 3D robot driving around on the 3D lunar surface, it occurred to me that I could add more detail and make it more realistic,” Leucht said. “It got me thinking, ‘I support other projects at Kennedy that could really use a tool like this.’”
The software tool is officially called Immersive Surface Operations Lunar Visualization Environment, or I-SOLVE. But internally, Leucht and the simulation’s users have started calling it by the nickname “Moon Tycoon.”
The Moon Tycoon software is playing an important role in developing the In-Situ Resource Utilization (ISRU) Pilot Excavator, a project headed by Kennedy Robotics Engineer Jason Schuler, and funded by NASA’s Game Changing Development Program.
The robot excavator, targeted to fly aboard a Commercial Lunar Payload Services (CLPS) flight in the next several years, will demonstrate excavation of up to 10 metric tons of regolith on the Moon. The ability to excavate regolith in such high quantities is a critical part of NASA’s plan to create sustainable infrastructure on the Moon.
“This will be the first time excavating for mining operations, or in other words, where the intent is to actually use the resources, Schuler said.
Schuler reached out to Leucht to learn how the simulator could be used in testing his team’s “robotic construction worker.” The robot’s demonstration will take place near the South Pole region of the Moon – an area with significant lighting and shadow concerns. While finalizing layout of the robot, Schuler and his team had questions about camera placement.
“With this software, we can simulate cameras in any position we want on the robot, and we can simulate putting different lenses on the camera, so we get multiple fields of view and viewing angles,” Schuler said. “We can look through them in the simulation and get the perspective that the robot will have.”
Leucht collaborated with NASA’s Jet Propulsion Laboratory (JPL) in California to enhance the simulation and create accurate topography to a more desirable resolution. This helped account for the expected number and sizes of rocks and craters, as well as the undulating terrain the robot – about the size of two carry-on suitcases – will encounter during excavation.
Leucht has focused on making I-SOLVE as accessible and easy to use as possible. Everyone on the Pilot Excavator project team from the Granular Mechanics and Regolith Operations (GMRO) Lab, the Swamp Works team, as well as engineers at other centers, can use the software at their desktop. It works on a standard computer screen or in virtual reality, and upgrades can be applied in minutes.
“It allows us to very quickly iterate the robot design and the tool as the robot design changes,” Leucht said. “It’s really a valuable tool that we didn’t even realize we needed until we had it.”
Leucht’s program may soon have other uses. A project involving 3D printing of structures on the Moon, such as garages to house rovers and equipment, is in the research and development phase at Kennedy. Researchers expressed the desire to visualize how their equipment will operate on the Moon and how robots will interface with it. Leucht was able to quickly add photo-realistic 3D models of the proposed 3D printed lunar structures to the simulation, allowing the team to visualize and interact with them in virtual reality.
In the meantime, the Moon Tycoon will continue to help provide more detailed and accurate testing on the ISRU Pilot Excavator, as it prepares for the CLPS launch.
“We can excavate the regolith and use it as construction material,” Schuler said. “We can build landing pads, leveling areas for site preparation, build berms, and compact pathways all in simulation. All of these capabilities are important for enabling a sustainable human presence on the Moon.”
Click here to learn more about NASA’s Moon to Mars missions.