Innovative Propulsion System Gets Ready to Help Study Moon Orbit for Artemis
by Abigail Tabor
In 2021, NASA’s Cislunar Autonomous Positioning System Technology Operations and Navigation Experiment, or CAPSTONE, CubeSat will launch to a never-before-used cislunar orbit near the Moon.
As a pathfinder for Gateway, a Moon-orbiting outpost that is part of NASA’s Artemis program, CAPSTONE will help reduce the risk for future spacecraft by verifying the dynamics of a unique halo-shaped orbit. The mission will also demonstrate innovative spacecraft-to-spacecraft navigation technology and communications capabilities with Earth.
CAPSTONE’s journey to the Moon will take about three months, starting with its launch to low-Earth orbit on a Rocket Lab Electron. Rocket Lab’s Photon spacecraft will take over next and conduct a series of orbit-raising maneuvers to prepare the CubeSat for its transfer path to the Moon. After separating from Photon, CAPSTONE will utilize an energy-efficient ballistic lunar transfer using its onboard propulsion system and enter into a near rectilinear halo orbit in the vicinity of and around the Moon. There, it will maintain the orbit to inform future spacecraft and demonstrate new technologies.
CAPSTONE’s propulsion system is designed and built by Stellar Exploration Inc. of San Luis Obispo, California. Initially funded by NASA’s Small Business Innovation Research program, the system is approximately 8-inches square by 4-inches deep. The system’s eight thrusters are fed hydrazine propellant from an unpressurized tank. CAPSTONE’s super small, high-performance thrusters integrate proven NASA technology with state-of-the-art industry fabrication techniques.
CAPSTONE is led by Advanced Space of Westminster, Colorado. Tyvak Nano-Satellite Systems of Irvine, California, is building the microwave oven-sized CubeSat platform. NASA’s Small Spacecraft Technology program within the agency’s Space Technology Mission Directorate funds the demonstration mission. The program is based at NASA’s Ames Research Center in California’s Silicon Valley. The Launch Services Program at NASA’s Kennedy Space Center in Florida manages the launch service.
NASA Tests Mixed Reality, Scientific Know-How, and Mission Operations for Exploration
by Frank Tavares
Mixed reality technologies, like virtual reality headsets or augmented reality apps, aren’t just for entertainment – they can also help make discoveries on other worlds like the Moon and Mars. By traveling on Earth to extreme environments – from Mars-like lava fields in Hawaii to underwater hydrothermal vents – similar to destinations on other worlds, NASA scientists have tested out technologies and tools to gain insight into how they can be used to make valuable contributions to science.
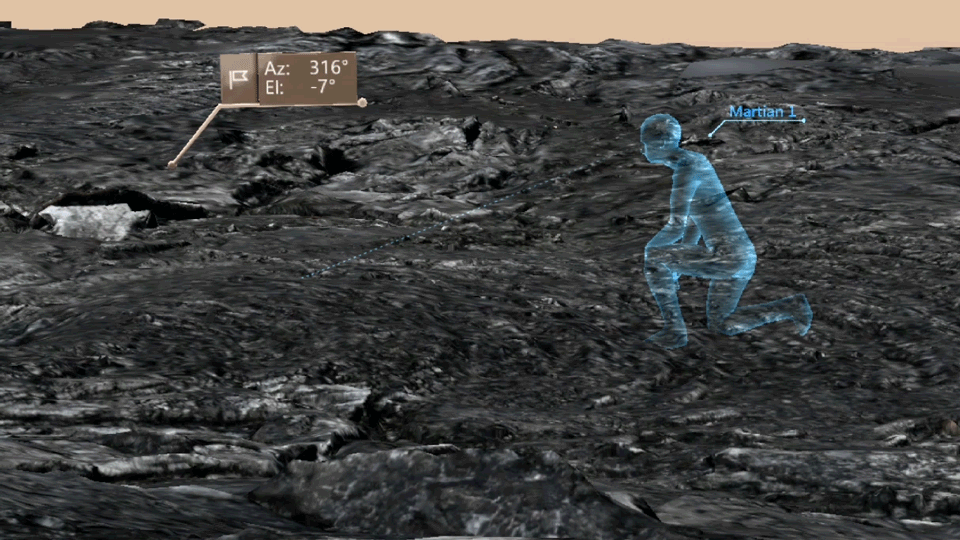
Three projects led by researchers at NASA’s Ames Research Center in California’s Silicon Valley presented their results in a special issue of Planetary and Space Science. Those results included new insights into how to study volcanic environments on other worlds, mission operation designs to manage conducting science in extreme environments, techniques to search for life, and more findings.
“This represents the culmination of years of work from missions all over the Earth, doing the work of figuring out how we can effectively conduct science on other worlds,” said Darlene Lim, the principal investigator of the Biologic Analog Science Associated with Lava Terrains, or BASALT, mission at Ames. “What we’ve done here is show how these missions to extreme environments on Earth can pave the way for our future exploration on other worlds.”
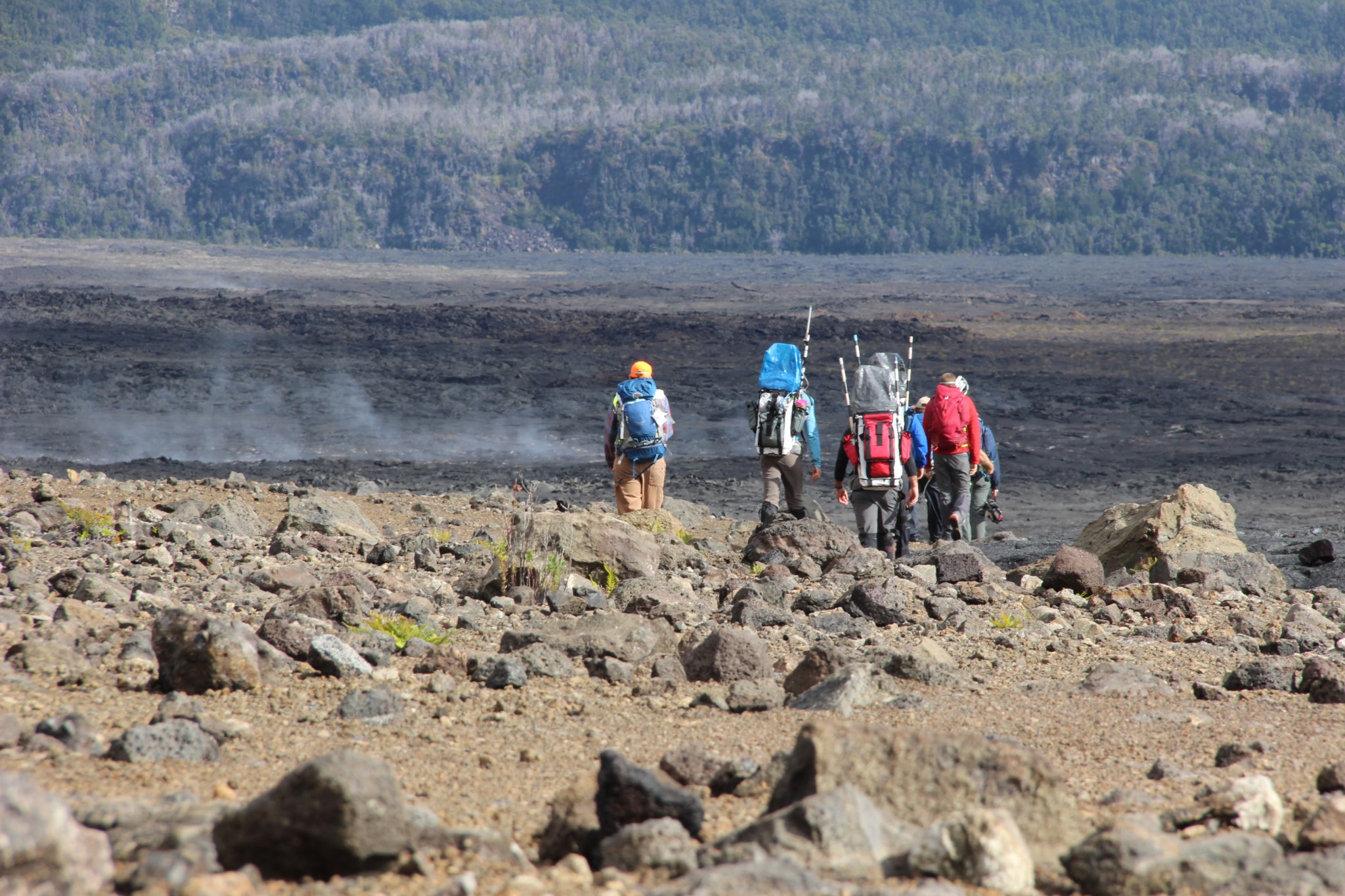
Augmented and Virtual Reality to Assist Future Explorers
The BASALT mission had three deployments, the third of which travelled to the Kilauea Caldera and Kilauea Iki regions of Hawaii in November 2017. In the environment of that scientific Mars analog, the team conducted 10 simulated extravehicular activity missions exploring the basaltic lava fields under many of the same operational constraints that future astronauts will experience on other worlds. One example of this is the significant time delay between communications that take place between the Earth and Mars, which were simulated in these missions. BASALT-3’s goals centered around conducting science relevant to Mars related to the biological, chemical, and geologic systems we expect to find there while incorporating novel technologies and operational techniques to make sure a mission can handle the constraints of operating on another world.
The BASALT-3 team found that virtual and augmented reality technologies allowed explorers in the field to send data visualizations back to a science team, which in turn could conduct complex analyses to inform where the field team would go next. Though similar technologies have been used before, this latest iteration had new capabilities for mapping data and terrain information over the real world. Scientists in the mission support center could use the augmented reality to explore the “Martian” environment as well.
“These technologies didn’t just provide a new tool,” said Kara Beaton, BASALT exploration research co-lead through Wyle Laboratories from Johnson Space Center in Houston. “They enabled real science to be achieved in extreme conditions. By collecting detailed imagery and data of basaltic environments and feeding only the most important aspects to the remote science team, data that could have been overwhelming and difficult to exchange became easily digestible. Ultimately, these technologies helped bring back the samples that made the discoveries detailed across this special issue possible.”
From BASALT’s deployments, those discoveries included a better understanding of how to look for microbial life on different kinds of basalts, presented in a paper in the special issue. Several other analog missions yielded results as well.
“These technologies didn’t just provide a new tool,” said Kara Beaton, BASALT exploration research co-lead through Wyle Laboratories from Johnson Space Center in Houston. “They enabled real science to be achieved in extreme conditions. By collecting detailed imagery and data of basaltic environments and feeding only the most important aspects to the remote science team, data that could have been overwhelming and difficult to exchange became easily digestible. Ultimately, these technologies helped bring back the samples that made the discoveries detailed across this special issue possible.”
From BASALT’s deployments, those discoveries included a better understanding of how to look for microbial life on different kinds of basalts, presented in a paper in the special issue. Several other analog missions yielded results as well.
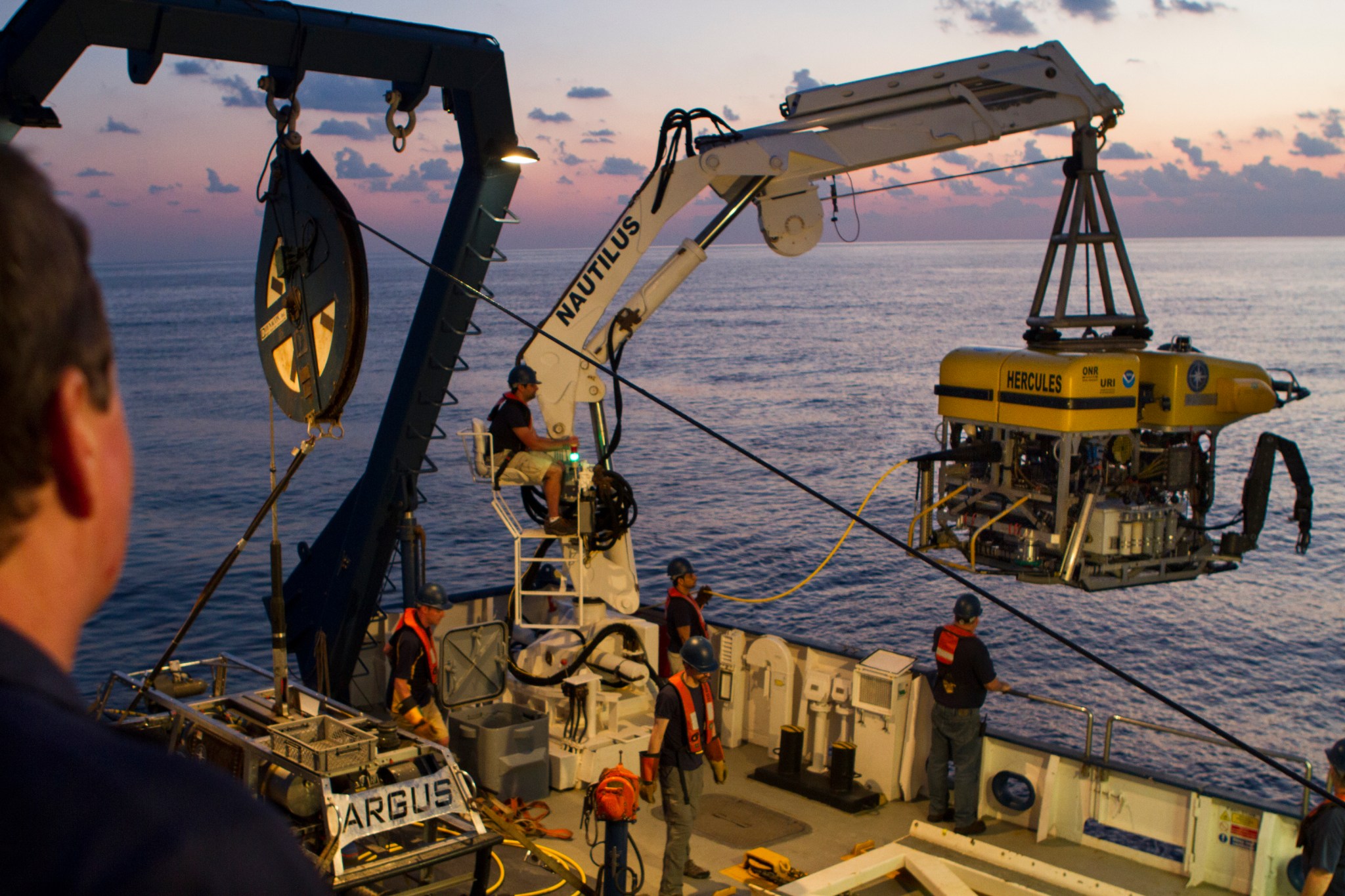
Taking to the Seas to Prepare for the Stars
The question of working through a time delay is one that becomes even more important as NASA conducts science further out in the solar system. Robotic missions to the icy moons of Saturn and Jupiter – places where life could potentially survive in oceans beneath their frozen surfaces – would face this challenge as well.
The Systematic Underwater Biogeochemical Science and Exploration Analog project, or SUBSEA, simulated such a journey in a deployment aboard the Exploration Vessel Nautilus to a hydrothermal vent site in the Pacific Ocean. Located at the northern edge of Gorda Ridge, the Sea Cliff site is an underwater volcanic zone about 75 miles off the coast where California and Oregon meet. One science team stayed ashore while another went out to sea, with their robotic explorers. The project developed techniques to maximize scientific return from exploration, using geochemical modeling to guide decision making. Rather than having to wait for data to travel back and forth from Earth to other worlds to make decisions, those choices can be made using real-time data – reducing what could take years to just hours.
From Volcanic Land Formations to Impact Craters
The third project, Field Investigations to Enable Solar System Science and Exploration, or FINESSE, traveled to Idaho to study volcanic land formation and to northern Canada to study impact craters. These earthly destinations help scientists learn more about and prepare to explore such environments on other worlds. Some science results presented in papers within the special issue included better understanding magma on the Moon, identifying more Earth analogs for volcanic features on the Moon and Mars, and continuing to develop a technique known as thermoluminescence, which heats up rock samples to learn about their history – and is already being used on Apollo lunar samples.
“All these projects require an interplay between technology development, complex logistics, and hard science that can only be tested out in the field,” said Jennifer Heldmann, principal investigator on FINESSE. “Ames’ interdisciplinary nature, where engineers and planetary scientists collaborate often, makes it uniquely suited to lead analog missions.”
By testing the technology, mission operations, and scientific know-how we’ll need to explore the Moon, Mars, and beyond here on Earth first, NASA plans to ensure when astronauts touch down on other worlds, they’ll be ready to make groundbreaking discoveries.
NASA Provides $45M Boost to US Small Businesses
Small businesses are vital to NASA’s mission, helping expand humanity’s presence in space and improve life on Earth. NASA has selected 365 U.S. small business proposals for initial funding from the agency’s Small Business Innovation Research (SBIR) and Small Business Technology Transfer (STTR) program, a total investment of more than $45 million.
“At NASA, we recognize that small businesses are facing unprecedented challenges due to the pandemic,” said Jim Reuter, associate administrator for the agency’s Space Technology Mission Directorate (STMD). “This year, to get funds into the hands of small businesses sooner, we accelerated the release of the 2021 SBIR/STTR Phase I solicitation by two months. We hope the expedited funding helps provide a near-term boost for future success.”
NASA selected 289 small businesses and 47 research institutions to receive Phase I funding this year. More than 30% of the awards will go to first-time NASA SBIR/STTR recipients. “We are excited to have a large cohort of new small businesses join the NASA family via the SBIR/STTR program,” Reuter said.
Through the program, NASA works with U.S. small businesses and research institutions to advance cutting-edge technologies. The agency provides up to $125,000 for companies to establish the merit and feasibility of their innovations. Phase I SBIR contracts are awarded to small businesses and last for six months, while Phase I STTR contracts are awarded to small businesses in partnership with a research institution and last for 13 months. Based on their progress during Phase I, companies may submit proposals to subsequent SBIR/STTR opportunities and receive additional funding.
NASA selected proposals to receive funding based on their technical merit and commercial potential. The selections span the breadth of NASA missions to empower the agency’s work in human exploration, space technology, science, and aeronautics. Some examples include:
- Syrnatec Inc., a woman-owned small business and first-time NASA SBIR awardee based in Middletown, Connecticut, will develop radiation tolerant, high-voltage, high-power diodes. This power management and distribution technology could enable the next generation of efficient high-power green technology in space and on Earth.
- Innoveering LLC, a Hispanic American-owned small business and first-time program awardee based in Ronkonkoma, New York, will use its SBIR award to develop a wind sensor to enable a flight path control system for high-altitude scientific balloon operations. Outside of NASA, this technology could aid in providing more accurate weather predictions.
- Under an STTR award, Qubitekk of Vista, California, will partner with the University of New Mexico, a Hispanic-Serving Institution. Together, they will develop a cheaper and more compact hardware package that provides a reliable calibration tool for detectors of quantum-sized information. This technology could be applied to secure satellite communication networks, deep-space laser communications, cybersecurity, and computing.
The small businesses and research institutions selected are as varied as the technologies they will develop. Hailing from 38 states, Washington, D.C., and Puerto Rico, they include women-owned, minority-owned, and veteran-owned small businesses, as well as Minority Serving Institutions (MSIs) and other types of research organizations.
The program is enhancing its efforts to further increase STTR participation by MSIs, including Historically Black Colleges and Universities, by launching two pilot initiatives. Under a cooperative agreement, NASA will work directly with MSI STEM Research and Development Consortium to increase its audience’s participation in STTR. Additionally, the program will collaborate with NASA’s Minority University Research and Education Project to offer research planning grants and incentivize partnerships between MSIs and small businesses. The grants will also let MSIs develop plans for proposing to an STTR solicitation subtopic.
“NASA SBIR/STTR interfaces with entrepreneurs pushing the boundaries of innovation,” said Program Executive Jason L. Kessler. “We’re proud to partner with a diverse group of innovators and expand the reach of NASA across the country.”
NASA’s SBIR/STTR program is part of STMD and managed by NASA’s Ames Research Center.
Comet Catalina Suggests Comets Delivered Carbon to Rocky Planets
by Alison Hawkes
In early 2016, an icy visitor from the edge of our solar system hurtled past Earth. It briefly became visible to stargazers as Comet Catalina before it slingshot past the Sun to disappear forevermore out of the solar system.
Among the many observatories that captured a view of this comet, which appeared near the Big Dipper, was the Stratospheric Observatory for Infrared Astronomy, NASA’s telescope on an airplane. Using one of its unique infrared instruments, SOFIA was able to pick out a familiar fingerprint within the dusty glow of the comet’s tail – carbon.
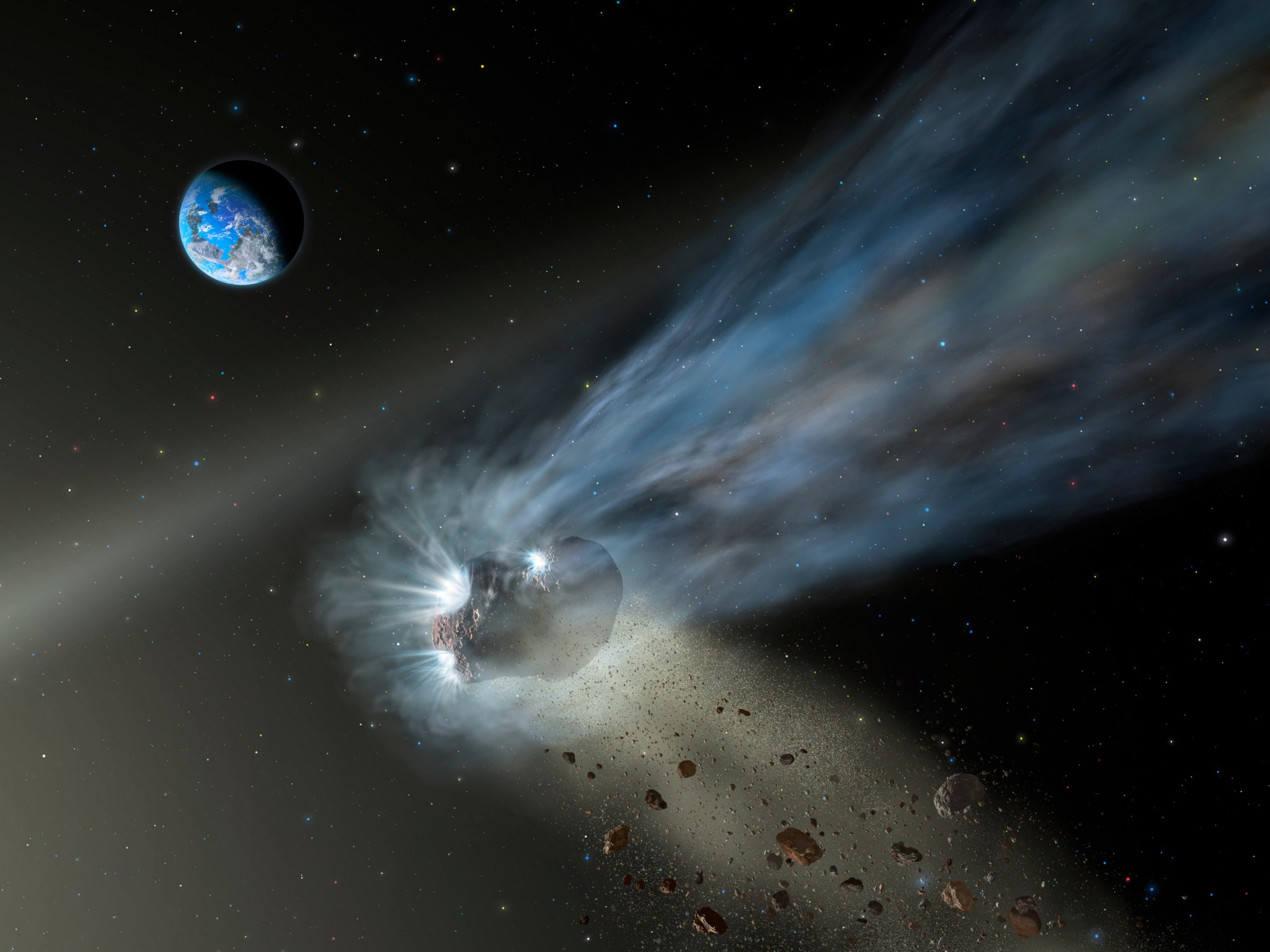
Now this one-time visitor to our inner solar system is helping explain more about our own origins as it becomes apparent that comets like Catalina could have been an essential source of carbon on planets like Earth and Mars during the early formation of the solar system. New results from SOFIA, a joint project of NASA and the German Aerospace Center, were published recently in the Planetary Science Journal.
“Carbon is key to learning about the origins of life,” said the paper’s lead author, Charles “Chick” Woodward, an astrophysicist and professor at the University of Minnesota’s Minnesota Institute of Astrophysics, in Minneapolis. “We’re still not sure if Earth could have trapped enough carbon on its own during its formation, so carbon-rich comets could have been an important source delivering this essential element that led to life as we know it.”
Frozen in Time
Originating from the Oort Cloud at the farthest reaches of our solar system, Comet Catalina and others of its type have such long orbits that they arrive on our celestial doorstep relatively unaltered. This makes them effectively frozen in time, offering researchers rare opportunities to learn about the early solar system from which they come.
SOFIA’s infrared observations were able to capture the composition of the dust and gas as it evaporated off the comet, forming its tail. The observations showed that Comet Catalina is carbon-rich, suggesting that it formed in the outer regions of the primordial solar system, which held a reservoir of carbon that could have been important for seeding life.
While carbon is a key ingredient of life, early Earth and other terrestrial planets of the inner solar system were so hot during their formation that elements like carbon were lost or depleted. While the cooler gas giants like Jupiter and Neptune could support carbon in the outer solar system, Jupiter’s jumbo size may have gravitationally blocked carbon from mixing back into the inner solar system. So how did the inner rocky planets evolve into the carbon-rich worlds that they are today?
Primordial Mixing
Researchers think that a slight change in Jupiter’s orbit allowed small, early precursors of comets to mix carbon from the outer regions into the inner regions, where it was incorporated into planets like Earth and Mars. Comet Catalina’s carbon-rich composition helps explain how planets that formed in the hot, carbon-poor regions of the early solar system evolved into planets with the life-supporting element.
“All terrestrial worlds are subject to impacts by comets and other small bodies, which carry carbon and other elements,” said Woodward. “We are getting closer to understanding exactly how these impacts on early planets may have catalyzed life.”
Observations of additional new comets are needed to learn if there are many other carbon-rich comets in the Oort Cloud, which would further support that comets delivered carbon and other life-supporting elements to the terrestrial planets.
SOFIA is a joint project of NASA and the German Aerospace Center. NASA’s Ames Research Center in California’s Silicon Valley manages the SOFIA program, science, and mission operations in cooperation with the Universities Space Research Association, headquartered in Columbia, Maryland, and the German SOFIA Institute at the University of Stuttgart. The aircraft is maintained and operated by NASA’s Armstrong Flight Research Center Building 703, in Palmdale, California.
Using NAS-Developed Tools to Quiet the Boom of Supersonic Flight
by Katharine Pitta
NASA’s Quiet SuperSonic Technology (QueSST) X‑59 is an advanced low-boom aircraft concept that will be used to emulate and test noise generated by future supersonic over-land transport designs. As part of this project, researchers in the Computational Aerosciences Branch in the NASA Advanced Supercomputing, or NAS, Division are using agency-developed tools to run simulations of various design iterations of the aircraft and verify its supersonic performance.
Developed in partnership with Lockheed Martin, the X‑59 will be NASA’s first piloted experimental aircraft in decades, and will feature innovative technology to reduce loud sonic booms to a quiet thump. The problem of sonic booms has been the primary barrier to commercial faster-than-sound aircraft over land; the iconic Concorde was limited to transatlantic flights, and was retired in 2003 due to high maintenance costs and low passenger numbers. Using advanced shaping and other new techniques, the X‑59 is being designed to produce a lower sound signature that will not significantly disturb people on the ground, in addition to improving flight speed, efficiency, and affordability.
However, designing and testing new aircraft concepts is expensive, both in time and costs, so QueSST project engineers have been working with computational fluid dynamics, CFD, experts at NAS to develop and validate designs using complex computer models. While performance optimization of traditional aircraft primarily focuses on maximizing the lift-to-drag ratio, designing the X‑59 also requires the prediction of sonic boom noise. To achieve this, thousands of CFD simulations using NAS’s in-house-developed Launch Ascent and Vehicle Aerodynamics, or LAVA, and Cart3D tools were performed for mission planning and rapid-testing of design modifications on the Pleiades, Electra, and Endeavour supercomputers at the NAS facility, located at NASA Ames.
Modeling Sound
Predicting ground noise is challenging, and with no experimental data for the X‑59—which is currently under assembly at Lockheed Martin’s Skunk Works factory in Palmdale, California—it is crucial to verify the CFD solutions across as many solvers as possible in order to build confidence in the predictions. Teams at NASA’s Ames and Langley Research Centers worked together to ensure that the various CFD codes used across the project predicted similar loudness values. At NAS, the team compared the results from the two solvers, Cart3D and LAVA.
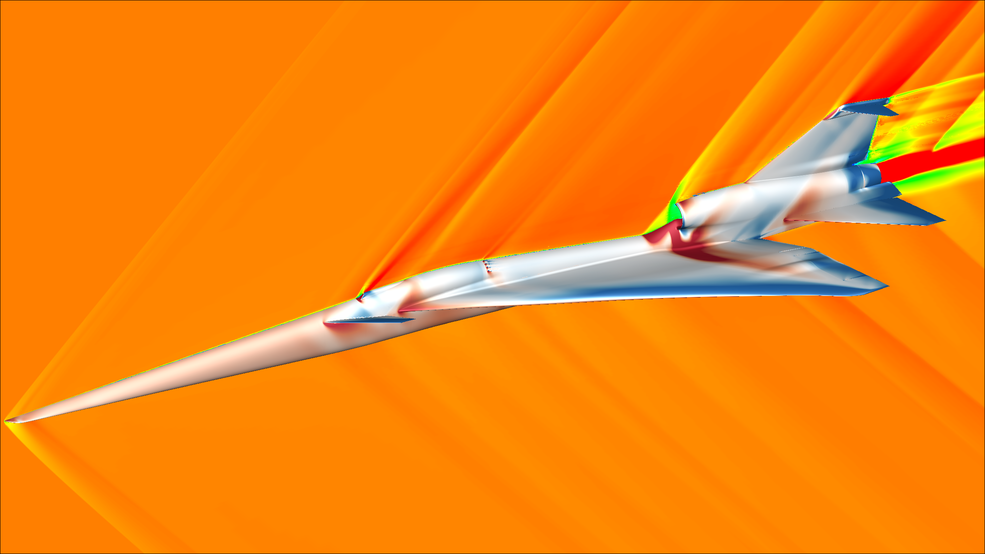
In a typical Cart3D simulation—which solves Euler equations on a Cartesian mesh and requires about six hours when using one node of either Electra or Pleiades—a nearfield pressure signature is extracted from the simulated flowfield around the X‑59. To estimate the boom noise at ground level, the pressure signature is propagated from a flight altitude of 55,000 feet to the ground using an atmospheric propagation solver. Additional tools are used to provide uncertainty estimates of the pressure signatures and loudness, validation that is needed due to the varied operating conditions and vehicle configurations being tested over the course of the project.
“The large capacities of Pleiades and Electra are critical for handling the thousands of cases required for aerodynamic performance databases, shape optimization, and uncertainty quantification of the X‑plane,” said Marian Nemec, an aerospace engineer within NAS’s Computational Aerosciences Branch and the primary developer of Cart3D’s adjoint-based mesh refinement module and shape optimization framework. “We use the Electra system for most production runs, where we can predict the entire boom footprint of the aircraft overnight when using several hundred cores. Our shape optimization cases run on the shared-memory Endeavour system, where complex optimizations require several days on 512 cores.”
These simulations contributed to numerous design improvements throughout the QueSST project, such as reducing the noise generated by the nose of the aircraft, instrumentation probes, and secondary-air-systems inlets. Cart3D also was used by the team at NAS to support the agency’s supersonic wind-tunnel tests, including using CFD simulations to verify the design of a new wind-tunnel strut that holds the scale X‑59 aircraft model in position, ensuring it does not interfere with pressure signatures during testing.
The ground level noise predictions from Cart3D simulations compare very well with those produced for the X‑59 using LAVA, which solves steady Reynolds-Averaged Navier-Stokes, or RANS, equations on a polyhedral mesh. Recent improvements to the LAVA solver have significantly decreased turnaround time, with a typical X‑59 simulation running on 1,500 cores of the Pleiades supercomputer completing in only an hour or two, leading the QueSST team to choose LAVA as the main code to be used to develop a large supersonic performance database. The database will be used to feed a flight planning tool that will train pilots how to fly the X‑59 and hit target noise levels during flight tests. It will need to cover all possible combinations of control surface settings and flight conditions that might be encountered during the test campaign—a massive undertaking for the team at NAS.
“Without high-performance parallel computing, supersonic database generation for the X‑59 would not be possible,” said James Jensen, one of the NAS aeronautics engineers working on the QueSST project. “The thousands of LAVA and Cart3D simulations required to perform mission planning for the X‑59 make high-performance computing an indispensable part of this program.”
The supersonic performance data for pilot training will also be used by the flight test program to provide a variety of high-quality data for the Federal Aviation Administration, or FAA, and the International Civil Aviation Organization, or ICAO, to help determine the future of civilian supersonic flight.
The Future of Supersonic Flight
At the end of 2020, the construction of the X‑59 reached its halfway point, with final assembly scheduled for 2021. The aircraft will then undergo a multitude of tests to ensure the integrity of its structure and that all of its components all work correctly. Data from CFD simulations will be used during this period to help predict flight performance, as well as to develop training for pilots.
Community response testing, which is set to begin in 2024, will include flights over a wide variety of environments and locations to build up a database of noise levels and acceptability metrics. This database will be used by the FAA and ICAO to set noise level requirements for supersonic over land flight, replacing the blanket ban that is currently in effect. While the X‑59 itself won’t carry passengers at supersonic speeds, it is the first great leap toward developing standards that will lead to faster, efficient air travel around the world.
NASA Practices VIPER Moon Rover Assembly in New Clean Room
by Abigail Tabor and Alison Hawkes
NASA’s water-hunting lunar robot now has a workspace prepped and ready at the agency’s Johnson Space Center in Houston, where it will be built for its upcoming mission to the Moon. The Volatiles Investigating Polar Exploration Rover, or VIPER, has a new 1,000-plus square-foot clean room, called the Surface Segment Integration and Test Facility, where engineers will assemble and outfit the rover.
Located in a corner of the center’s Space Vehicle Mock Up Facility, the VIPER team recently launched the assembly of a full-scale replica of the rover. The “assembly pathfinder” activity will last roughly three months and serve as a dress rehearsal for the flight version.
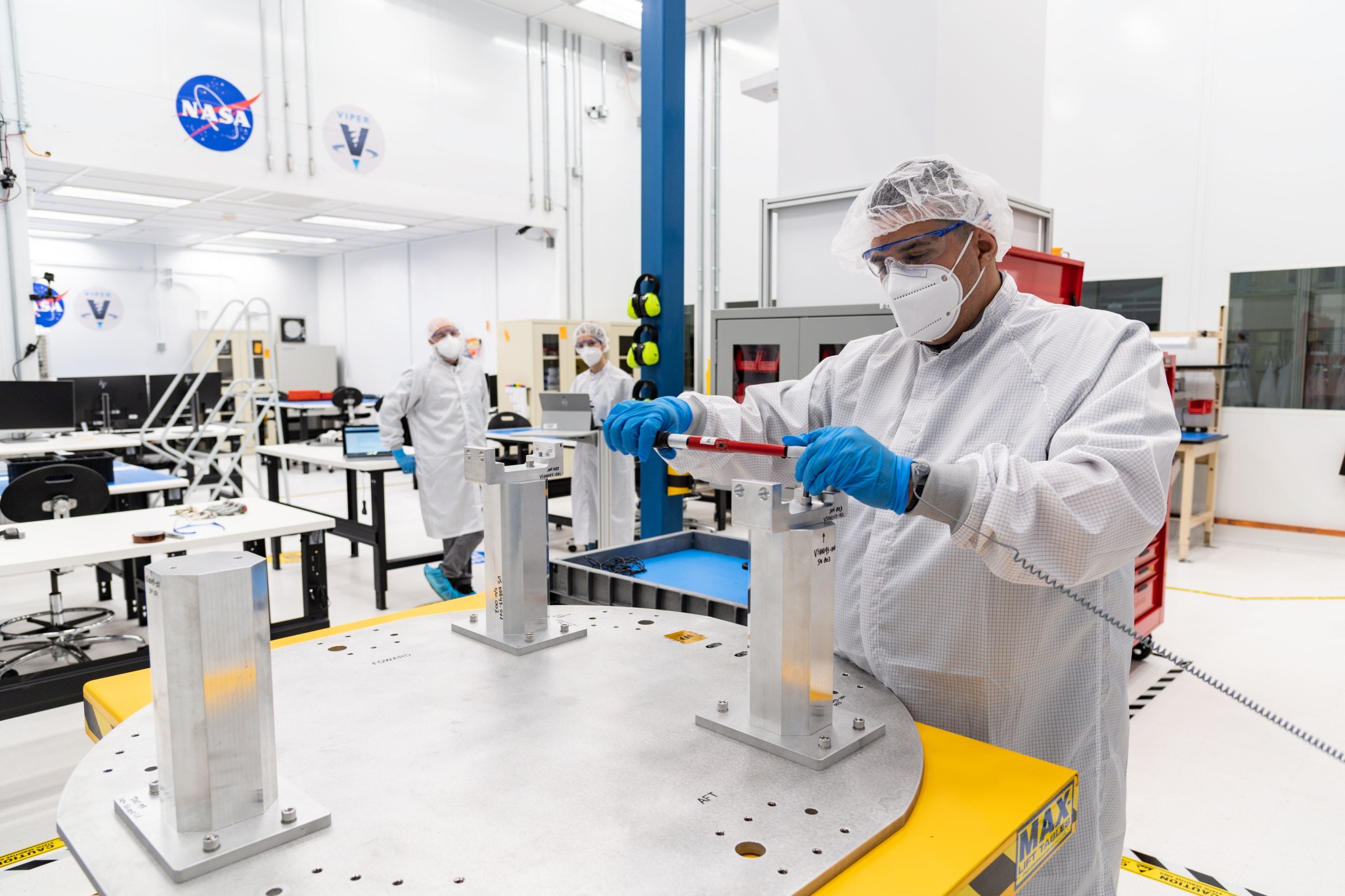
Faced with a pile of mock components and a heap of requirements for cleanliness and safety, documentation and protocols, the team is blazing a trail toward a rover that’s ready for launch. This way, NASA will be as efficient as possible when the real flight equipment arrives – and avoid any unwanted surprises.
“We need to work out the bugs now,” said David Petri, VIPER’s system integration and test lead at Johnson. “That could mean a lot of things, from discovering there isn’t enough clearance in one corner of the rover to turn a wrench, to realizing team members need additional training to get the job done. These are the kind of unforeseen challenges that could slow development down.”
NASA’s VIPER will be built in the summer of 2022, bound for the lunar South Pole in 2023, where it will search for ice in deep, dark craters and other places to create the first water resource maps of the Moon for future space exploration. This work will help advance the Artemis program to establish a sustainable human presence on the Moon.
All About Assembly
Since this work is focused on assembly, not a functioning rover, there are no moving parts. Instead, the parts are precision-made from VIPER’s designs – mostly 3D-printed, and some made out of sheet metal. The real test comes when determining the order in which the parts are put together. Should they screw part A to part B, then bolt that to part C – or join B and C, first? That’s the kind of detail to know before getting too far into assembling a bookshelf, much less a spacecraft.
If there’s no easy solution for the assembly team, they may ask the rover’s designers for small but essential changes. The current test will make that kind of adjustment possible.
VIPER’s New Clean Room
The year leading up to this dry run of VIPER’s assembly was spent turning an ordinary workspace into a controlled workspace, or clean room. New air filtration units and particle counters help keep the space extremely clean. This was necessary to prevent any debris or contamination from getting into the spacecraft, where it could potentially interfere with the scientific instruments’ measurements or make the solar arrays or radiator work less efficiently, for instance. A highly sensitive video fire-detection system keeps the hardware safe from flames. And everything inside the room has mitigations against creating sparks, which could damage circuit boards in the rover’s sensitive electronics.
There are so many things to think of when building something to meet NASA’s rigorous requirements for spaceflight. How will you keep the parts super clean on their way to the workspace? Are the wrenches calibrated? Do you have every necessary nut and bolt? Has someone scheduled the quality inspectors? And so on. The assembly team works long hours to make sure all the bases are covered, but it’s worth it.
“You get to work on something that’s going to the Moon, and you’re doing it with people who will do whatever it takes to be successful,” said Petri. “You don’t want to let them or the mission down. And it’s mutual. So, that makes it exciting!”
VIPER is a collaboration within and beyond the agency. VIPER is part of the Lunar Discovery and Exploration Program and is managed by the Planetary Science Division of NASA’s Science Mission Directorate at NASA Headquarters in Washington. NASA’s Ames Research Center in California’s Silicon Valley is managing the project, leading the mission’s science, systems engineering, real-time rover surface operations and flight software. The hardware for the rover is being designed and built by NASA’s Johnson Space Center in Houston, while the instruments are provided by Ames, NASA’s Kennedy Space Center in Florida, and commercial partner Honeybee Robotics in Altadena, California. The spacecraft, lander and launch vehicle that will deliver VIPER to the surface of the Moon will be provided by Astrobotic in Pittsburgh, Pennsylvania, who was selected through NASA’s Commercial Lunar Payload Services, or CLPS initiative, delivering science and technology payloads to and near the Moon.