Engine testing is firing forward for NASA’s new rocket, the Space Launch System, but it doesn’t stop on the test stand at the agency’s Stennis Space Center near Bay St. Louis, Mississippi.
Some 400 miles away at NASA’s Marshall Space Flight Center in Huntsville, Alabama, engineers are testing an additive manufacturing process — called selective laser melting. Selective laser melting is a 3-D printing process that can create complex rocket parts. The process is being used to make some of the parts more efficiently and affordably — without compromising performance and safety — for the engine and other components of the rocket.
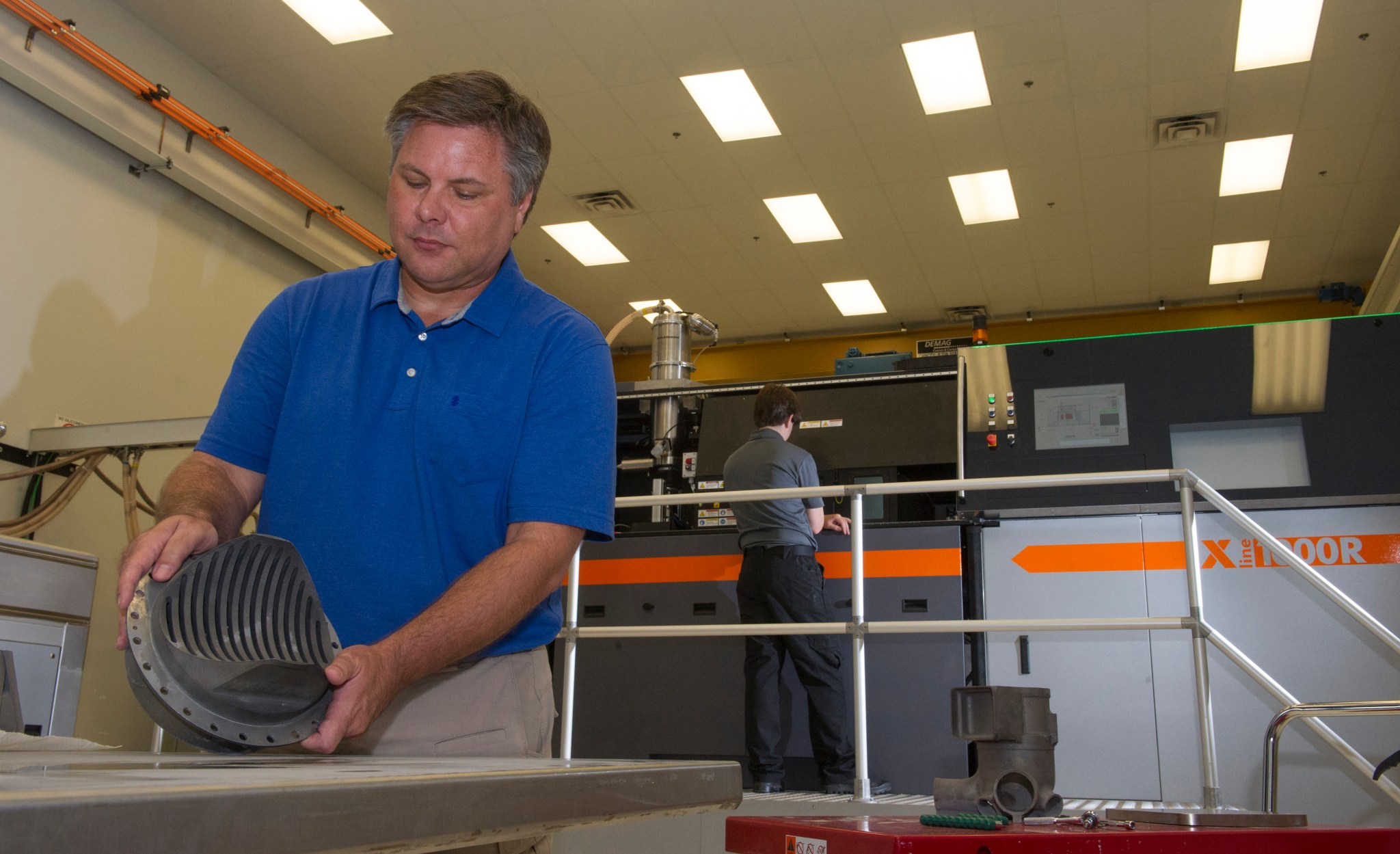
“The opportunity for affordability extends well beyond manufacturing because these technologies give us the ability to reduce the entire development life cycle from design to flight,” said Chris Singer, director of the Engineering Directorate at the Marshall Center, where the SLS Program is managed for the agency.
Four RS-25 engines, along with two five-segment solid rocket boosters, will power the core stage of the SLS, which will provide an entirely new capability for science and human exploration beyond Earth’s orbit, including deep-space destinations, like an asteroid and Mars. The core stage, towering more than 200 feet tall with a diameter of 27.6 feet, will store cryogenic liquid hydrogen and liquid oxygen that will fuel the vehicle’s RS-25 engines.
The process for selective laser melting begins with a three-dimensional design created by a computer that is transmitted to a machine, and inside the machine, a high-energy laser melts metal powder and fuses the powder layer by layer to build the desired component. The process drastically reduces or eliminates the need for multiple welds common to traditional manufacturing methods.
“Selective laser melting is changing the way we think and do things in the manufacturing world,” said Andy Hardin, a subsystems manager in Marshall’s Liquid Engines Office. “We have conducted a lot of studies to see which RS-25 parts would benefit most from the selective-laser-melting process. Our initial estimates show in some instances, this technology can reduce the RS-25 part cost by as much as 45 percent, and significantly shorten development and manufacturing time.”
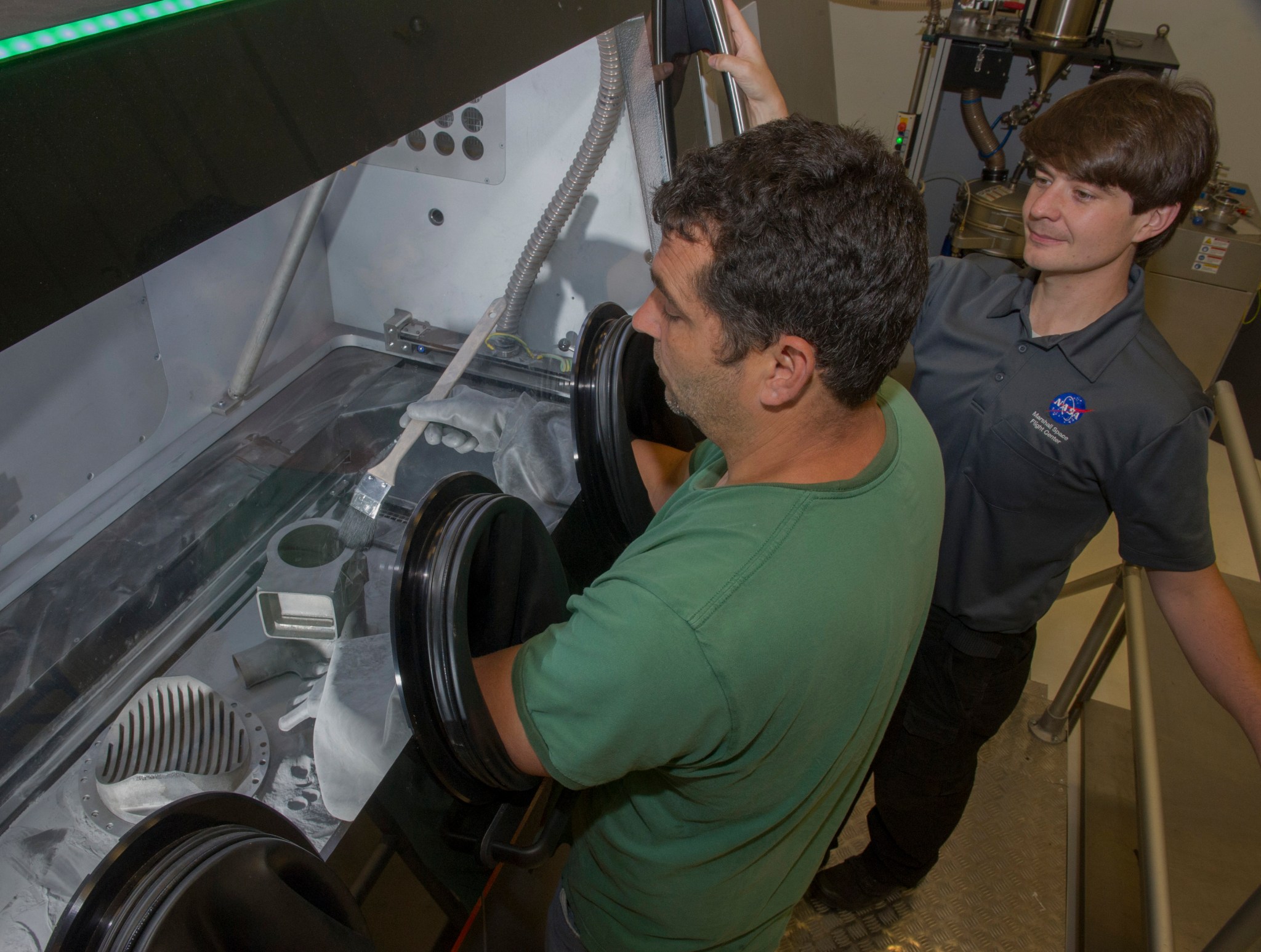
Additive manufacturing would make parts for the brand-new RS-25 engines that will be built for future SLS missions after the first four SLS flights. The program has 16 RS-25s in inventory from the Space Shuttle Program that provide affordable propulsion for the first four SLS missions.
The RS-25 is one of the most tested large rocket engines in history, with more than 3,000 starts and over a million seconds of total ground test and flight firing time over 135 space shuttle missions. The entire flight engine inventory will be upgraded with new state-of-the-art engine controllers, insulation and other details to meet SLS performance specifications.
Marshall has three selective-laser-melting machines, adding its latest one – the X line 1000R – in February to the Advanced Manufacturing Lab. The X line 1000R is the largest of the machines and increases build capacity by more than 400 percent. It can create parts up to 24 inches long, 16 inches wide and 19 inches high – comparable to a large microwave oven.
Selective laser melting is a specific example of how NASA is exploring the potential of additive manufacturing in high-technology production. NASA is on the cutting edge across this emerging field, from basic research into materials, to building whole rocket engines, to 3-D printing parts for use on the International Space Station. The goal of these investments is not only to reduce costs and manufacturing time, but also to explore the potential of 3-D printing to radically change the way space systems are designed, built and supported throughout their lifetime.
“A lot of foundational work is being done right now,” said Ken Cooper, advanced manufacturing team lead in Marshall’s Engineering Directorate. “We are making samples and testing them. We have to demonstrate first that we can build these parts, which isn’t a simple process. A lot of work goes into how a part is printed. You can’t just push a button and have an intricate rocket engine part come out a minute later. We have to do a lot of development work, including analyzing and testing the strength of a material being used, how it reacts to environmental factors and other conditions that may affect how the material performs.”
Some parts made by selective laser melting may be incorporated into development engines in the near future for RS-25 hot-fire testing at Stennis before being used for future SLS flights. Aerojet Rocketdyne, the prime contractor for the RS-25, has been working for the past five years to mature the selective laser melting processes sufficiently to feed their product needs, including the current opportunity to benefit SLS affordability.
NASA and Aerojet Rocketdyne are working closely together to ensure the appropriate level of process and component qualification are conducted to not only meet the new affordability targets, but also maintain the traditional reliability of the engine and safety associated with NASA’s human space flight programs.
The first flight test of the SLS will feature a configuration for a 70-metric-ton (77-ton) lift capacity and carry an uncrewed Orion spacecraft beyond low-Earth orbit to test the performance of the integrated system. As the SLS evolves, it will provide an unprecedented lift capability of 130 metric tons (143 tons) to enable missions even farther into our solar system to places like Mars.
For more information on SLS, visit:
Kim Henry
Marshall Space Flight Center, Huntsville, Alabama
256-544-0034
kimberly.m.henry@nasa.gov
Tracy McMahan
Marshall Space Flight Center, Huntsville, Alabama
256-544-0034
tracy.mcmahan@nasa.gov