The successful March 11 test of a solid rocket motor for NASA’s new deep space exploration rocket, the Space Launch System, lasted only two minutes, but its success was the culmination of months of intense investigation to solve a puzzling problem.
Finding unexpected and unwelcome air bubbles in the solid rocket propellant and between the propellant and insulation kicked off a months-long journey for the booster team. Such challenges are typical in the spaceflight business. After the first booster qualification test, it looks like the talented Orbital ATK and NASA booster team have likely found an engineering solution.
Overcoming gravity requires a lot of energy. Putting a payload in orbit demands pushing the limits of physics while balancing the needs of both safety and performance. For rocket scientists – who are engineers, actually – it means controlling enormous masses, pressures, temperatures, speeds, and other factors far beyond the demands of the average family car or commercial airliner.
That’s why spaceflight hardware, particularly human spaceflight hardware like SLS, is designed and inspected in great detail, and tested thoroughly to ensure safe flight.
Developing the SLS Boosters
The solid rocket motor is the largest component of the SLS booster. SLS uses a pair of boosters in addition to its liquid propellant engines. The performance demands of the booster drive the design limits by maximizing energetic materials — like propellant — and minimizing non-energetic materials, including the motor case and insulation. As a result, about 90 percent of the booster weight consists of the propellant in the motor. In one rocket booster, all of that propellant is burned in about two minutes, producing the 3.6 million pounds of thrust needed to propel the SLS rocket into space.
This propellant starts out as a thick, doughy mixture that cures inside the motor case to have a consistency roughly like that of a pencil eraser. The propellant is poured into the motor cases and molded into a specific shape to provide the required performance. Because the motor is so long, it is built of five separate segments, each holding approximately 300,000 pounds of this propellant. The center of each segment is hollow. Once lit, the propellant burns outward rapidly from this center hole toward the metal case.
When the motor is ignited, the internal temperature reaches about 5,600 degrees Fahrenheit, and the pressure jumps to around 900 pounds per square inch. The motor generates more thrust than 14 four-engine jumbo jets as the exhaust leaves the nozzle at three times the speed of sound. The five-segment motor has to contain that pressure and must be insulated against heat that could literally melt the metal cases.
To keep the metal case to a relatively cool 200 degrees Fahrenheit, sheets of rubber insulation are vulcanized to the metal case segments before the propellant is poured into the cases to harden.
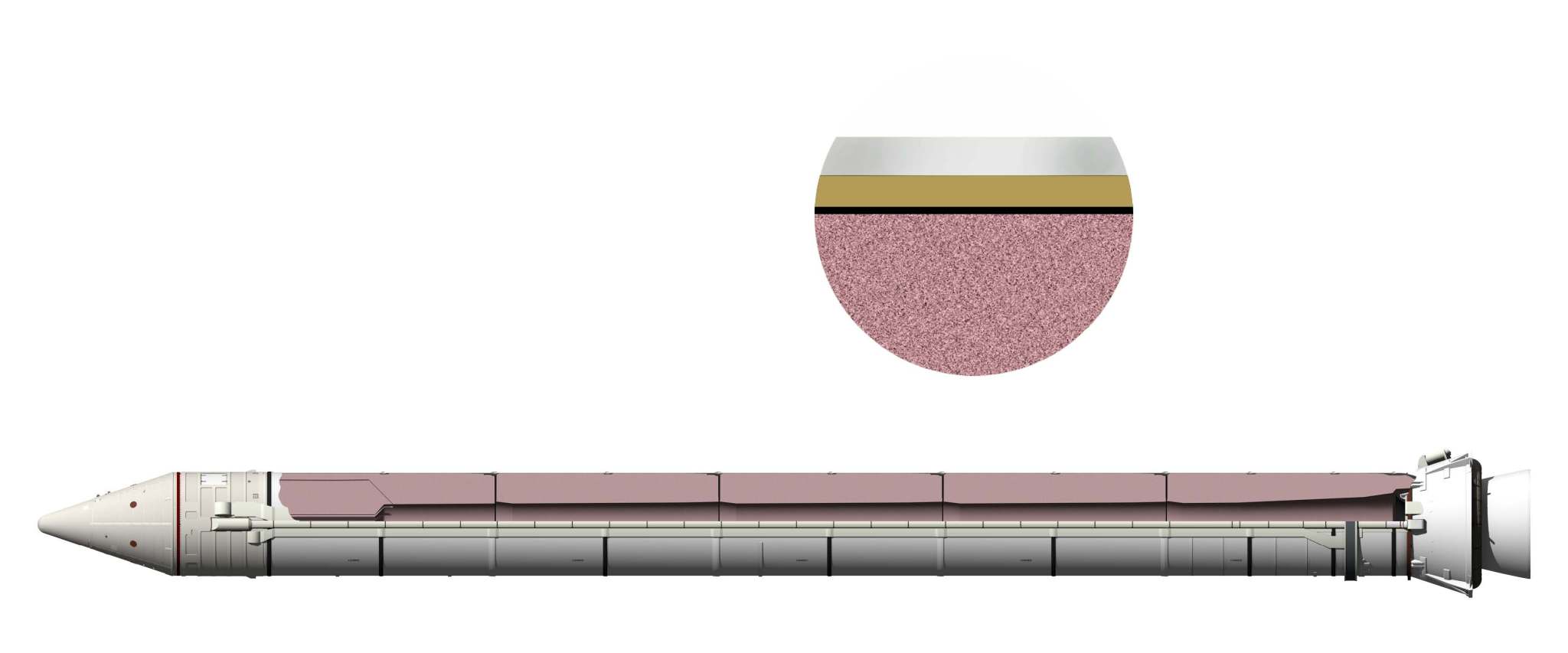
It is important that the insulation sticks to the metal cases and that the propellant sticks to the insulation with no significant ‘voids’ (bubbles in the propellant) or ‘unbonds’ (places where the propellant doesn’t stick to the insulation).
A few small bubbles in certain locations was considered normal during the Space Shuttle Program, but SLS and Orbital ATK engineers discovered unacceptable voids and unbonds in the insulation and propellant of the aft motor segments cast for the first qualification test motor. These voids were found during X-ray inspection of the segments. What followed was long months of analysis, testing, and developing process and inspection techniques that didn’t exist in the shuttle era. This extensive effort was required to understand and mitigate the problem.
“We ran thousands of tests from the smallest material property test to five full-scale engineering and process simulation articles,” said Alex Priskos, manager of the SLS Boosters Office at NASA’s Marshall Space Flight Center in Huntsville, Alabama, where the SLS Program is managed for the agency. “There were a lot of nights and weekends involved. It was an intensive investigation.”
The issue was traced to the new asbestos-free insulation, selected to comply with environmental regulations. In fact, it was lighter and had better thermal performance properties than what was used for the space shuttle boosters. But after the insulation was cured in the motor case segments, it emitted gas bubbles when the segments were filled with warm propellant. The release of gas bubbles created unbonds at the interface between the propellant and insulation, as well as voids in the propellant. Engineers looked at everything involving the material and the manufacturing processes.
Finding a Solution
Finally, one sample emerged from testing with no bubbles. It turned out that the adhesive used between the metal case and the adjacent insulation was impervious to the levels of outgassing observed by the engineers. The adhesive successfully blocked gas from the insulation from reaching the solid propellant. This was an extremely thin layer of adhesive, so engineers added an additional thin sheet of rubber insulation on top of the adhesive layer to add structural strength to the barrier.
A new aft segment was manufactured with this new barrier system, as well as several other process improvements and enhanced inspection techniques. For example, application of the rubber sheets to the motor case walls was modified to significantly reduce the amount of air trapped during the process. The problem was attacked on two fronts — reduce the sources of gas and create a barrier to stop what was left. The segment built with these new designs turned out to be the most defect-free aft segment ever produced.
“It’s been a tough road, but we’ve come through this with new processes, new repair techniques, and new inspection techniques that help ensure this is the safest booster ever built,” Priskos said. “The team did an amazing job. We will continue to gain additional data about this insulator because we want to make sure that we can reproduce this success time and time again. We face that challenge with every booster we make.”
With the insulation design changes, process improvements and new inspection techniques in place, engineers will gain more confidence with the second qualification test planned for early 2016. That next qualification motor is already in production. Together, these two tests will support qualification of the booster design for first flight.
For the SLS team, it’s another challenge overcome on the road to first flight in 2018.
The first flight test of SLS will feature a configuration for a 70-metric-ton (77-ton) lift capacity and carry an uncrewed Orion spacecraft beyond low-Earth orbit to test the performance of the integrated system. As the SLS evolves, it will provide an unprecedented lift capability of 130 metric tons (143 tons) to enable missions even farther into our solar system.
For more information on SLS, visit: